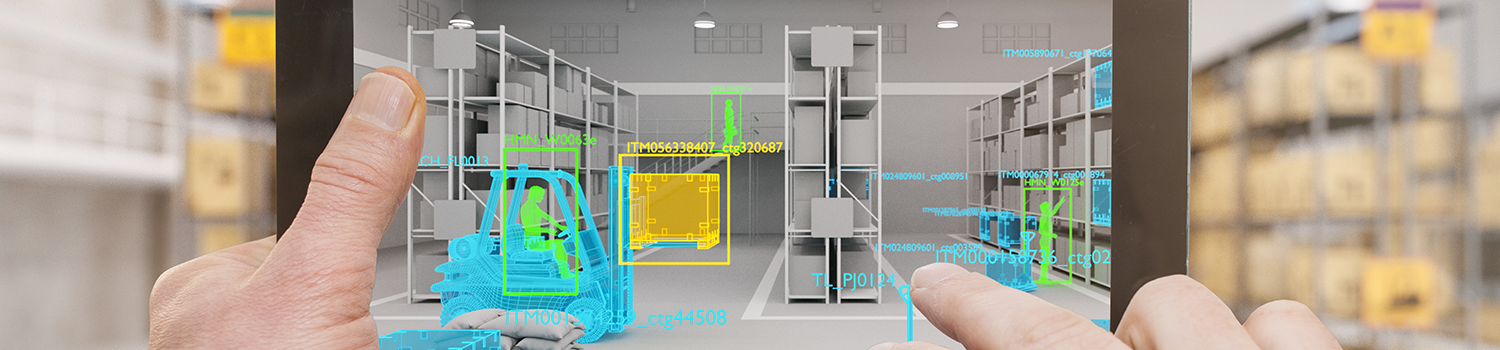
デジタルツイン工程最適化サービス
工場を仮想空間上に再現することで、現実の工場で改善を実施する前にデジタル上でさまざまな製造パフォーマンスの検証が可能です。これは4Mにおけるボトルネック分析にも有効です。また、生産量や納期などのKPIを達成するための仮説検証を何度でも何パターンでも繰り返すことが可能です。
デジタルツイン*によって実工場をデジタル上に再現することで、工程を最適化し生産のスループット向上を実現できます。
マクニカではデジタルツインをより早く、簡単に、定着してご活用いただくためのサービスを提案しており、お客様のDXの取り組みを加速させるサポートをしています。
*デジタルツインとは仮想空間で現実空間を再現する技術であり、現実空間では不可能な『時間を操る』ことで様々な事象や現象を予測することが可能となる技術です。
ホワイトペーパー
デジタルツインとは何か、活用方法や事例・導入効果の詳細をまとめました。
デジタルツインのはじめの一歩として、ぜひご覧ください!
※閲覧・ダウンロードにはお申し込みが必要です
INDEX
-
デジタルツインについて動画で詳しく知りたい! ※動画の概要・視聴申し込みのページが開きます
デジタルツインによる3つのメリット
●現在の工場の見える化
4M情報を収集しシミュレーション上で可視化することで現状の把握ができます。
ボトルネックの発見や改善案の立案に役立ちます。
●改善案の仮説検証
シミュレーション上であれば何度でも何パターンでも改善案を検討することができます。
実際の工場へより確実な改善手法を反映させることができるため、無駄な投資や工数を削減します。
●関係者とのコミュニケーションツールに
シミュレーションデータを活用することによって関係者間で情報共有をすることができます。
複雑かつ複数部署をまたがるDXの取り組みに関しても関係部署で情報交換が活発になり、経営層への説得材料に。
課題解決の一例
工場で発生している、以下のような4Mにおける課題の解決に役立ちます!
ケース1:在庫調整
-
必要部品数の算出
-
仕掛品在庫の調整
-
部品/仕掛品/完成品の置き場検討
『いつ』、『どこに』、『どれだけ』の部品、仕掛品が発生するかをシミュレーションによって可視化・分析し、在庫過多を削減
ケース2:設備利用
-
新規生産ラインの設計
-
設備の増設/縮小の判断
-
自動化の検討
新設/既設の生産ラインにおけるボトルネックをシミュレーションで事前に分析することで合理的な設備投資を判断
ケース3:人員配置
-
人員の配置(資格、技能)
-
省人化
-
動線の最適化
『スキル』、『役割』、『動線』を考慮した様々な人員配置をシミュレーションで検証し、人員リソースと配置を最適化
ケース4:プロセス調整
-
生産スケジュールの計画
-
生産ロットサイズの決定
-
原価計算
納期、スループット、コストなど様々な条件に対する最適な投入順序、ロットサイズを自動最適化機能(GA)で計画
事例
製造シミュレーションを利用して、電子機器の組立製造を最適化
■ 電子機器メーカー組立工場
納期、工程、設備の使用順序、設備能力、作業者の能力などをシミュレーションソフトウェア上に再現し、日々の生産効率の最適化を実現
■ 課題
・ | エクセルでの工程計画を行っているが勘と経験に頼っており、時間がかかってしまっている | |
・ | 人、AGVの動きを最適化したい | |
・ | 生産工程のどこにボトルネックがあるか調べたい |
■ 成果
✓ | 事前に生産ラインのシミュレーションを実施することで既存設備の動きを最適化でき、誰が見てもわかるように |
✓ | 飛び込み受注などの急な対応に対してもシミュレーション上で最適な計画を立ててから生産が開始できる |
✓ | 作業員の動きを最適化 |
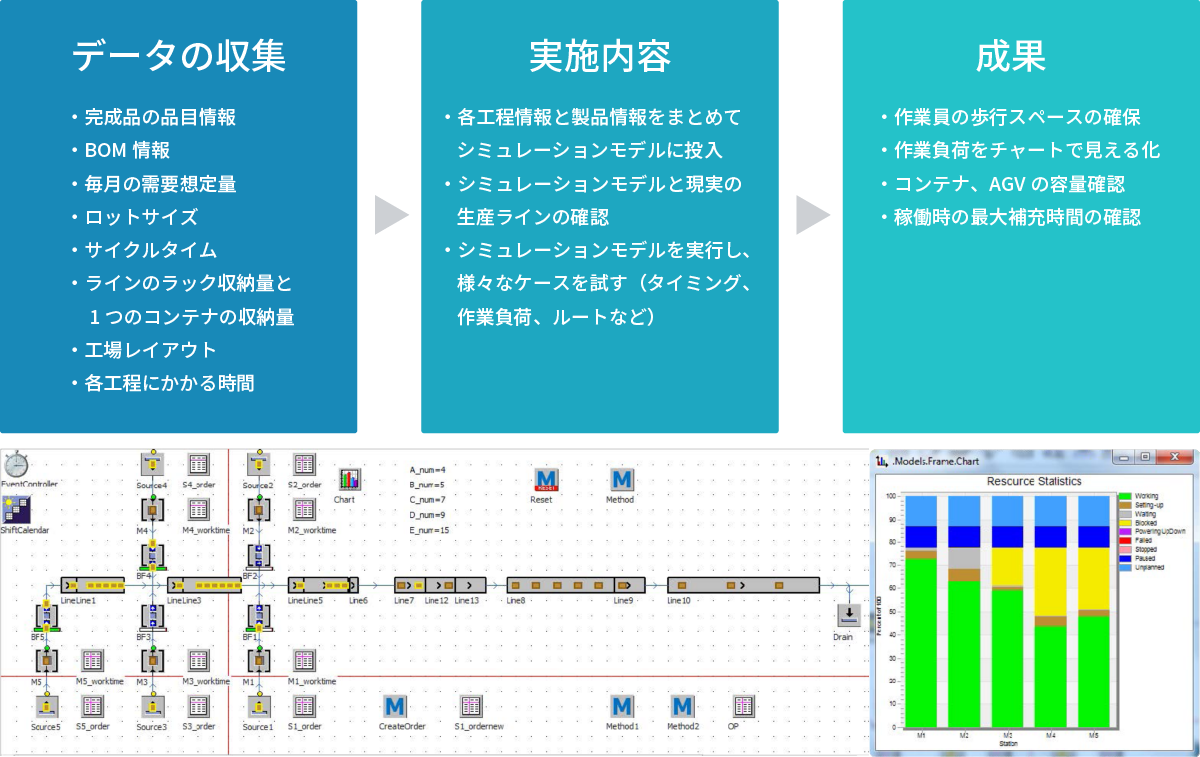
導入フローの例
プロジェクトの進め方 |
サービス |
|
- Phase 1 - |
現状課題の把握/シミュレーションの効果検討 / オプションサービスの選定 / 費用見積もり |
コンサルティング |
▼ | ||
- Phase 2 - |
工程情報(フロー、レイアウト等)/ 設備情報(加工時間、段取り時間等)/ 作業者情報(人数、役割等) |
コンサルティング |
▼ | ||
- Phase 3 - |
目的設定 / 機能設計 / モデル設計 / レビュー |
|
▼ | ||
- Phase 4 - |
用途に沿ったシミュレーションソフトウェアライセンスを選定 |
|
▼ | ||
- Phase 5 - |
使用方法トレーニング / モデル設計方法トレーニング |
トレーニング |
▼ | ||
- Phase 6 - |
テクニカルFAQ / 定例会 / モデル精度向上 / モデル範囲拡張 |
有償サポート |
デジタルツイン紹介動画集
全6回のデジタルツイン紹介動画をご覧いただけるページをご用意いたしました。
デジタルツインについてもっと知りたい方、ソフトウェア「Plant Simulation」でのシミュレーションの様子をご覧になりたい方、ぜひご覧ください!
※動画の視聴にはお申し込みが必要です