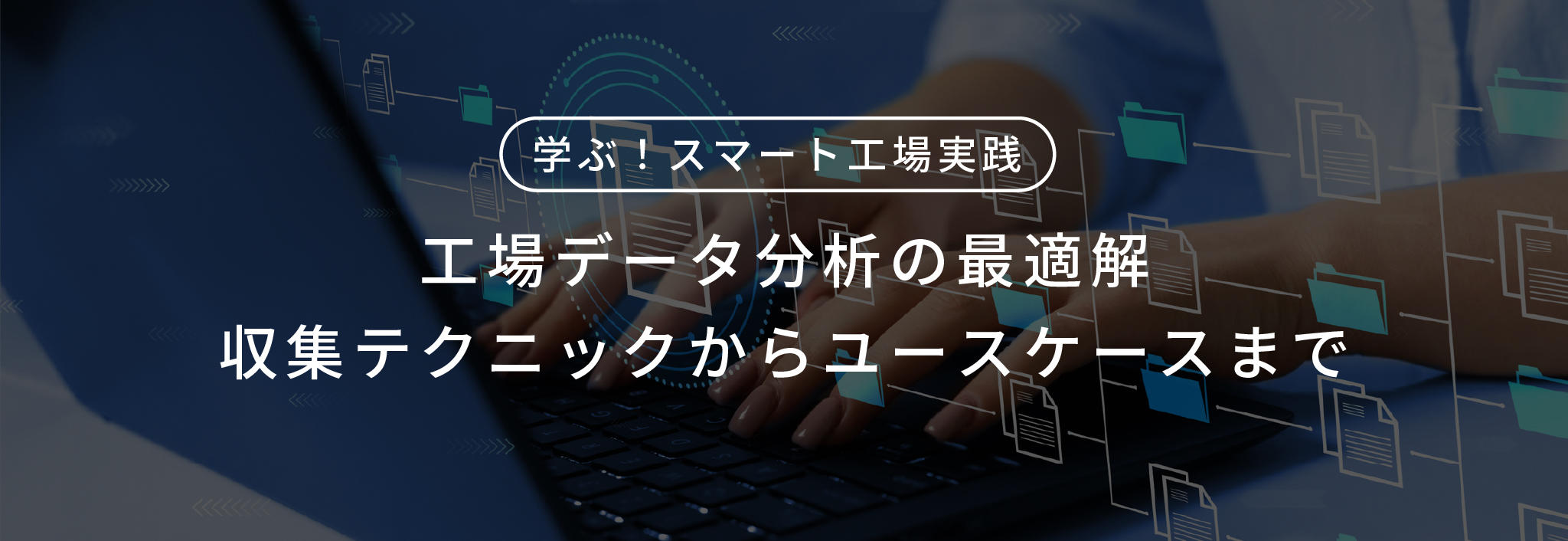
1. What you need to know before collecting data
When collecting factory data, it is important to first clarify the theme and issues of how you want to use the factory data before collecting the data.When smart factories and IoT first started to attract attention, the conventional approach at manufacturing sites was to "just collect data and then think about what the issues are based on the collected data."
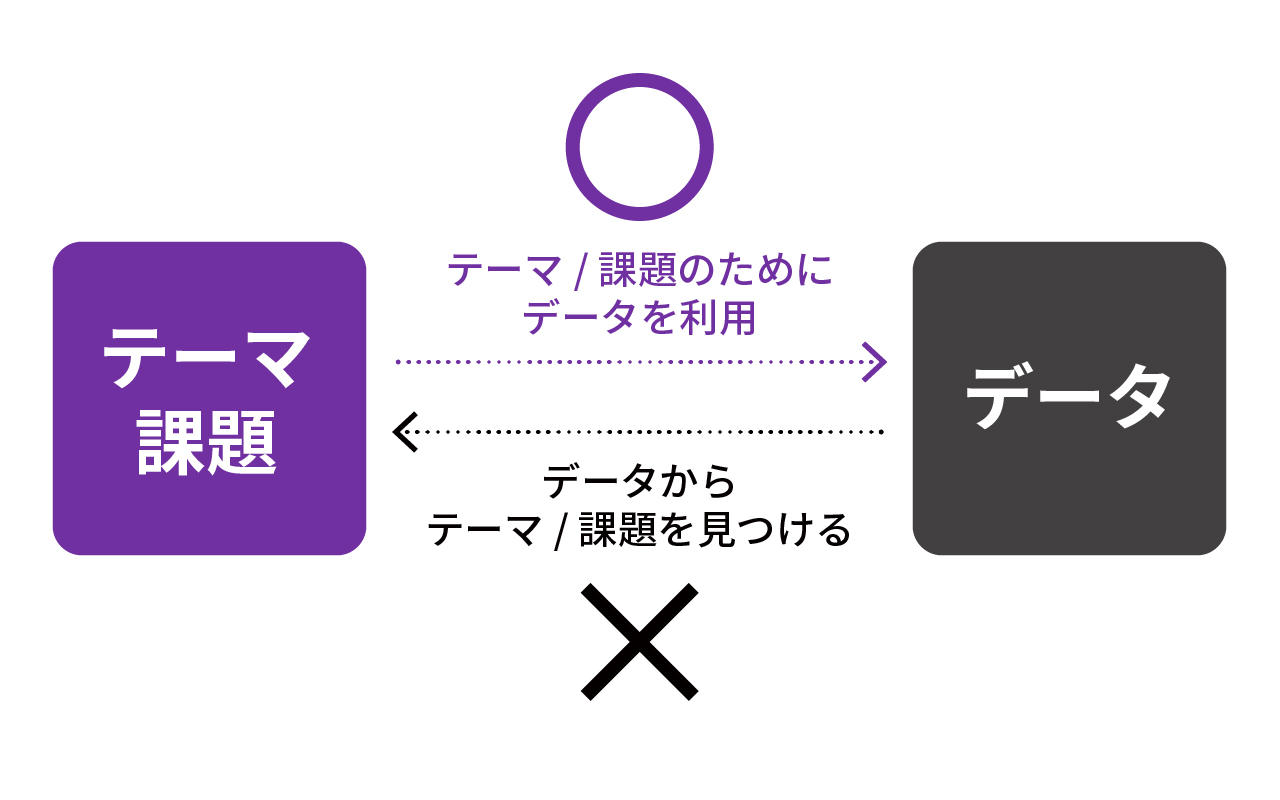
Figure: The importance of approaching data from a theme or issue perspective
The main purpose of a factory is to "continue to be a profitable factory" as a manufacturing process for a business company. To achieve this, the top priority is to reduce costs, shorten production lead times, and improve capital turnover through improvement activities that continuously eliminate losses by making them apparent. Specifically, losses in manufacturing processes are advocated by the Japan Plant Maintenance Association, a public interest incorporated association.
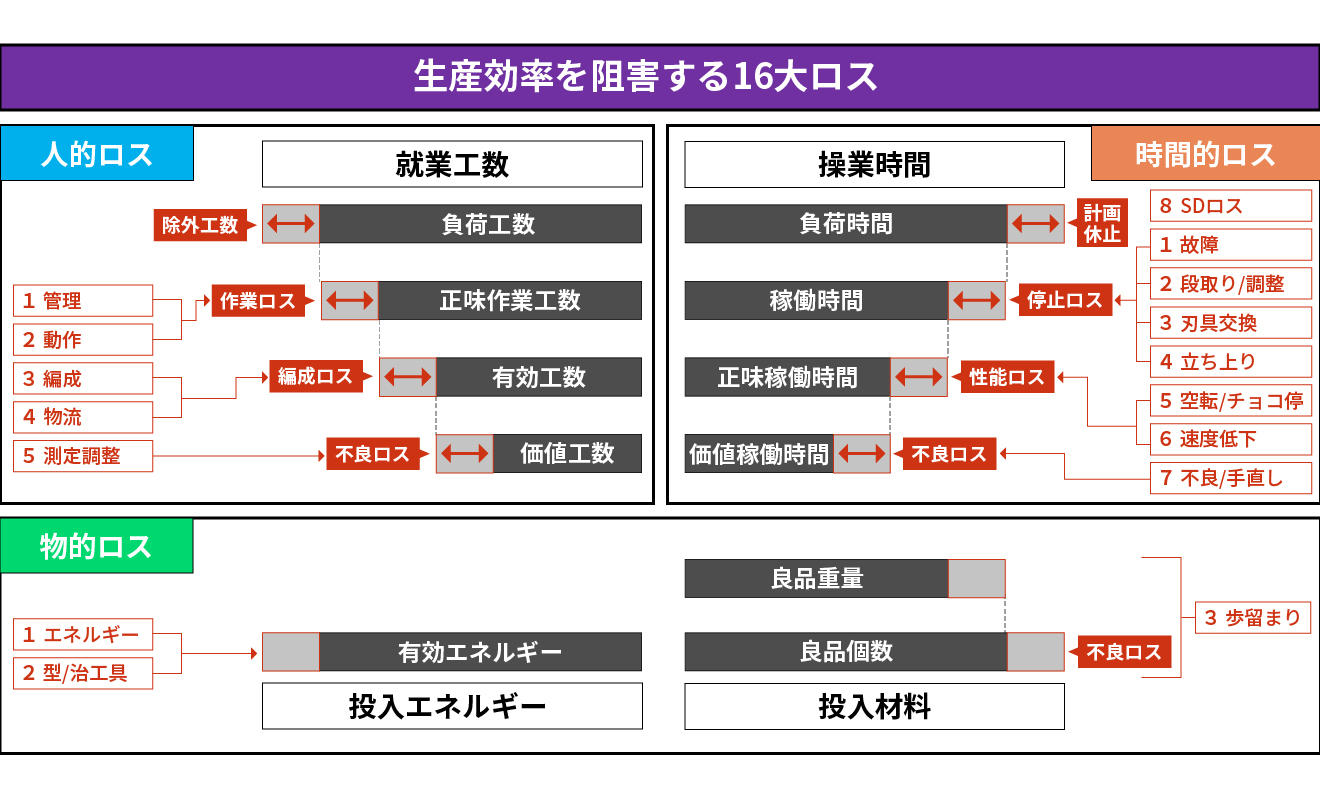
Figure: 16 major losses proposed by the Japan Institute of Plant Maintenance
2. Difficulties in utilizing factory data – Diversity of manufacturing sites
However, even so, collecting and utilizing factory data is difficult.
Since the German government proposed Industry 4.0 in 2011, data collection has become more active at production sites across a wide range of companies, but many people have probably had some trouble getting it to work.
The difficulty lies in the diversity of manufacturing sites. Products, equipment, and data items are diverse, occur asynchronously, and change due to equipment maintenance, etc.
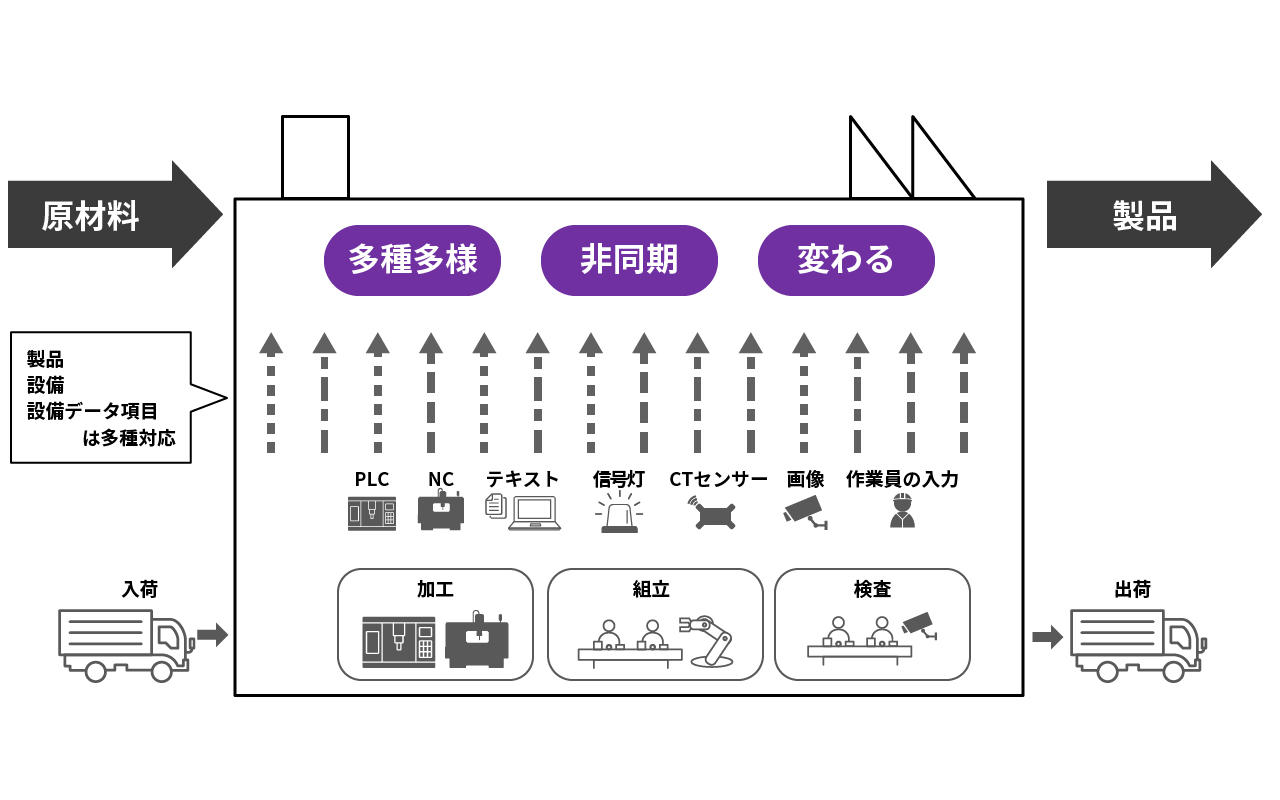
Diagram: Diversity of manufacturing sites
Many people have actually collected data from equipment such as PLCs and signal lights in order to utilize data on the manufacturing site. Also, the processes where data can be collected from such equipment are relatively easy and many people are working on it, but collecting data from other processes is difficult and difficult.
3. Classification of factory data
At Macnica, we use factory data from a variety of industries and processes to capture such a wide variety of production sites, and we believe it is important to establish a common way of thinking and collect data according to that standard, even when the manufacturing entities (equipment / workers) and the types of equipment (new / old) are different. Then, by using that data as input and standardizing and accumulating it, it becomes possible to use the data for highly accurate analysis and predictions that take a bird's-eye view of the entire factory.
From here, I would like to classify the factory data according to its characteristics. As mentioned above, we can classify the production lines into those mainly based on equipment and those mainly based on workers.
In the case of facilities
For new equipment, data can be collected from PLCs and signal lights, but for older equipment (equipment that is difficult to collect data from, such as equipment that does not support Ethernet communication), it is possible to collect machine signals by modifying the equipment or to collect data by attaching retrofit sensors. It is more difficult to collect data from older equipment.
In the case of worker-centered
Since there is no data source to begin with, workers will need to do something, such as inputting the situation, which increases the burden on the manufacturing site for collecting data.
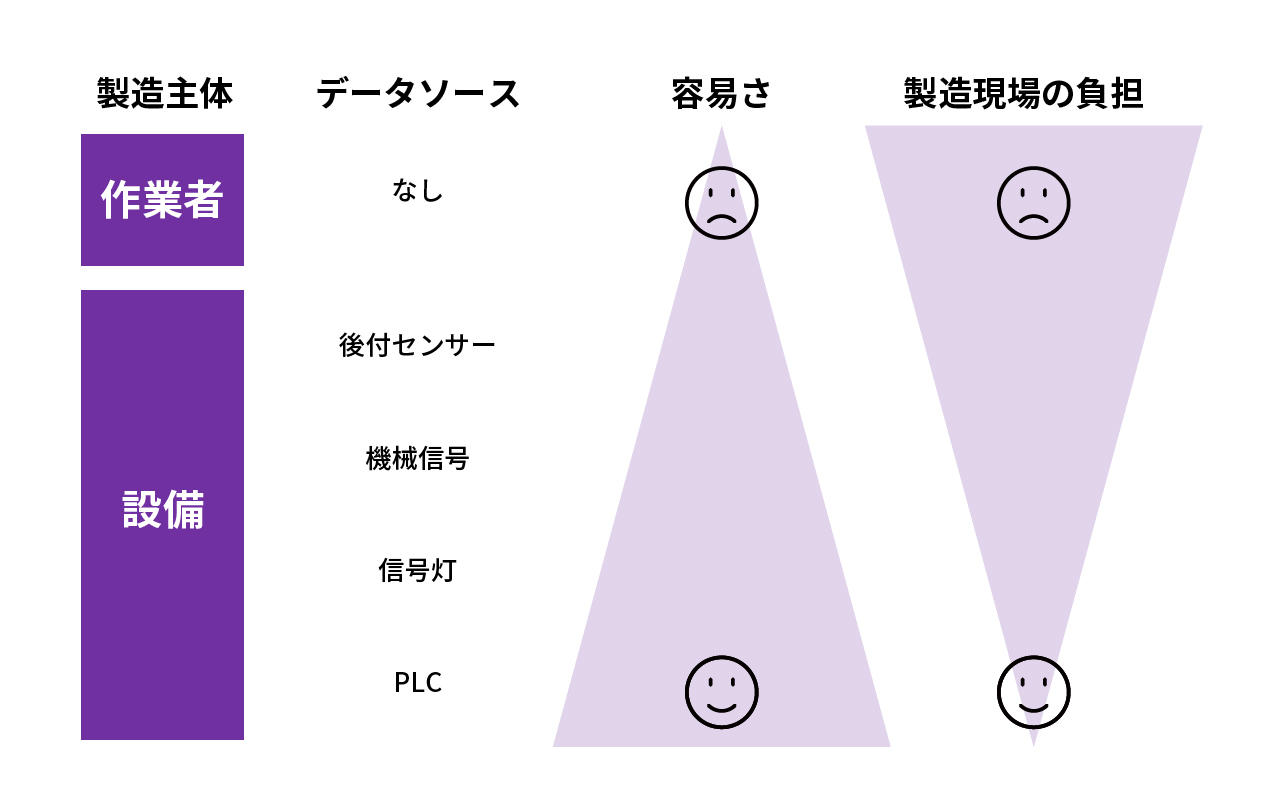
Figure: Relationship between ease of collecting factory data and on-site burden
In recent years, there have been cases where automation using robots and conveyors has been considered for worker-centered manufacturing lines. However, in a world where there is a need to respond to a wide variety of consumer demands, maintaining a flexible worker-centered line is one of the strengths of the manufacturing industry, and the current situation is that equipment installation is not progressing easily.
4. Approach to collecting factory data
What should we keep in mind when collecting data from production sites like this?
We will introduce the approaches that Macnica has taken so far.
For new equipment
Collection of equipment data from PLCs, signal lights, and other equipment can be achieved for multiple production lines for a few hundred thousand yen by using tools such as a master PLC, logger, and IoT gateway.
Old equipment and worker-centered
・Remodeling equipment and collecting analog signal data from old machines
・Install new sensors and collect measurement data
- Switches and cards are placed at the production site and data is collected by workers operating them.
・Collect data entered into an application on a tablet (such as electronic form software)
・Workers collect data based on voice registration using IT equipment
・Workers are given wearable devices or beacons (communication terminals) to collect data on their work status based on their location information.
・Work movements are recorded with a camera, and the video is analyzed by AI to collect data on the work situation.
When implementing these approaches, it is important to choose the most appropriate method based on the specific circumstances, needs and constraints at the site.
5. Important points to keep in mind when collecting factory data
So, with so many different approaches available, how do you choose the best one?
The key points to keep in mind are "reliable data" and "the cost of collecting the data."
Reliable data
High-precision analysis requires reliable input data. Relatively new equipment data is data on the production machines themselves, so it is less likely to contain false data and is therefore highly reliable.
On the other hand, data collection on old equipment or worker-driven production lines requires ingenuity. As a result, data often becomes unreliable based on unreasonably set criteria, and there is no point in collecting such data.
Collecting reliable data is something you should keep in mind when you start collecting data.
Cost of data collection
Next, there is the issue of the cost of collecting data. In many cases, when a large budget is approved for collecting data, it is during the testing phase, which also serves as an investigation into the latest technology. Once the testing passes, and the system is introduced to the entire factory to collect factory data, a return on investment is required. Investments of more than several hundred thousand yen per line are often unacceptable, and this is where things often stop, so it is important to be aware of the need to proceed with a realistic sense of cost.
When considering collecting factory data, it is important to proceed realistically while keeping in mind the reliability and cost of the data.
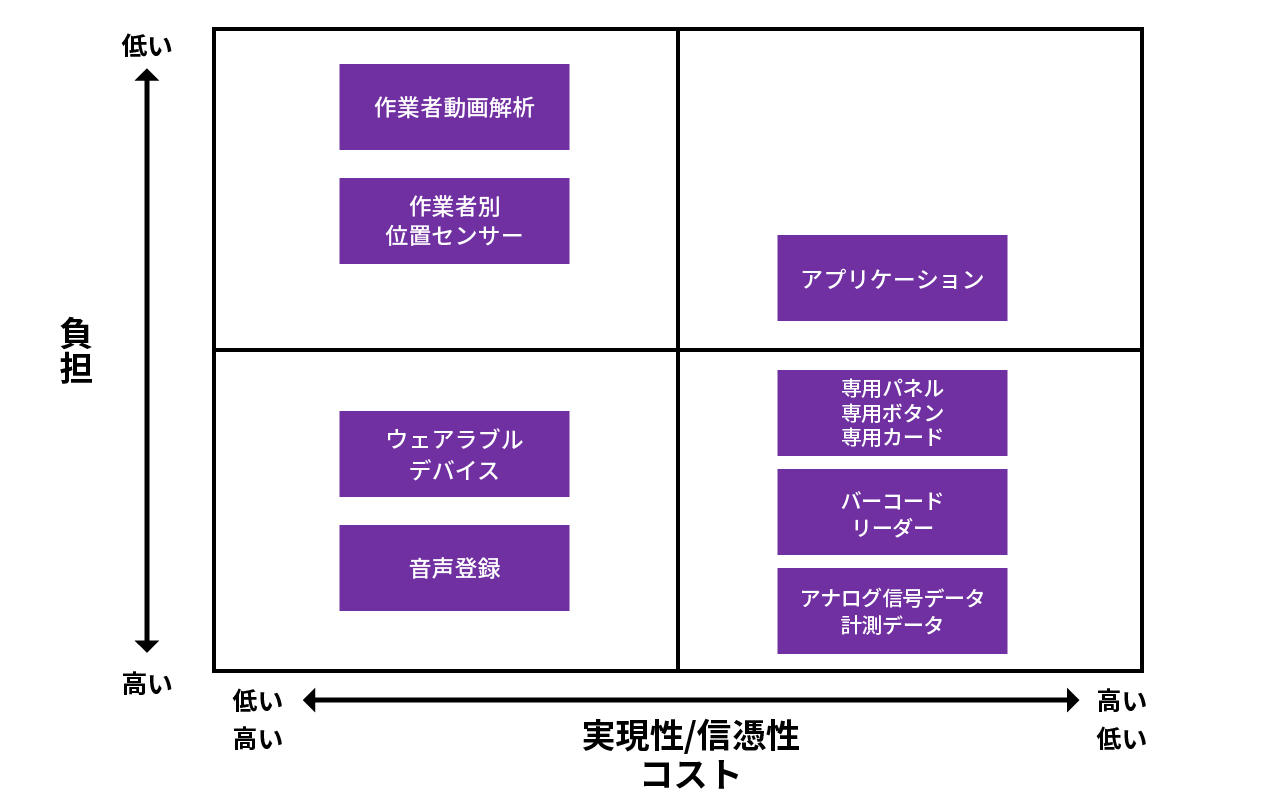
Figure: Example of factory data collection using old equipment and workers
6. Use cases for factory data analysis
As such, while capturing a wide variety of production sites, it is important to establish a common approach and collect data in accordance with that standard, even if the manufacturing actors (equipment / workers) and the type of equipment (new / old) are different. However, data collection itself is only a means, and it is more important than anything else to be able to utilize factory data. In this chapter, we will look at use cases for data utilization analysis.
At first glance, there may seem to be many different types of factory data analysis, but in reality there are only a few types. Historical Data Based on this, we analyze the actual situation and pursue the causes, real time Based on the factory data collected by the system, the system detects the current situation and takes appropriate action. 2 It's just a variety.
※Related materials※
[White Paper] Please see here for 9 types of data utilization use cases that further divide these two types.
theme | Outline | Operator | leader | Maintenance/Inspection | Industrial science | Production Management |
---|---|---|---|---|---|---|
Historical | Quantitatively grasp daily line performance values | - | 〇 | - | 〇 | - |
Set the loss (factor) that reduces the aptitude value | 〇 | 〇 | - | 〇 | - | |
Identify the causes (factors) that lead to these factors | 〇 | 〇 | - | 〇 | - | |
Refer to daily reports, inspection records, etc. when an abnormality occurs | 〇 | 〇 | 〇 | 〇 | - | |
Understand the actual results when a certain product is manufactured on a certain line | - | 〇 | - | 〇 | 〇 | |
real time | Shows how much equipment is producing and how much it is operating | 〇 | - | 〇 | - | 〇 |
Displays the current progress of production against production instructions | - | △ (If the manufacturing area is large) | - | - | 〇 | |
Display of equipment outage information/outage duration | △ (If the manufacturing area is separated) |
△ (If the manufacturing area is large) |
〇 | - | - | |
Display of equipment information and factors that cause quality abnormalities (production values/inspection values) | △ (If the manufacturing area is separated) |
△ (If the manufacturing area is large) |
- | 〇 | - | |
Staff availability | Shows maintenance and inspection staff availability | 〇 | - | - | - | - |
Figure: Use cases for data utilization at production sites
7. Conclusion
The most important thing about using factory data is to promote improvement activities toward a better state through collecting and using this data.
This blog summarizes Macnica 's experiences for manufacturers who are facing challenges with data collection.
Related Videos
We propose optimal data collection methods for a wide variety of production sites.
We also have a reference video that is about 10 minutes long, so please take a look.
"How to collect data for a wide variety of production sites!"
<Watch the video (no registration required)>
"DSF Cyclone" is a manufacturing performance system that connects manufacturing performance and production plans with structured data to realize "highly productive factories." If you are interested, please refer to this as well.