Manufacturing process innovation starting with digitization
Digitizing the manufacturing process will help you visualize the results, such as improving processes that tend to be bottlenecks, reducing costs by improving the productivity of the entire factory, and maintaining the stability of product quality. be connected.
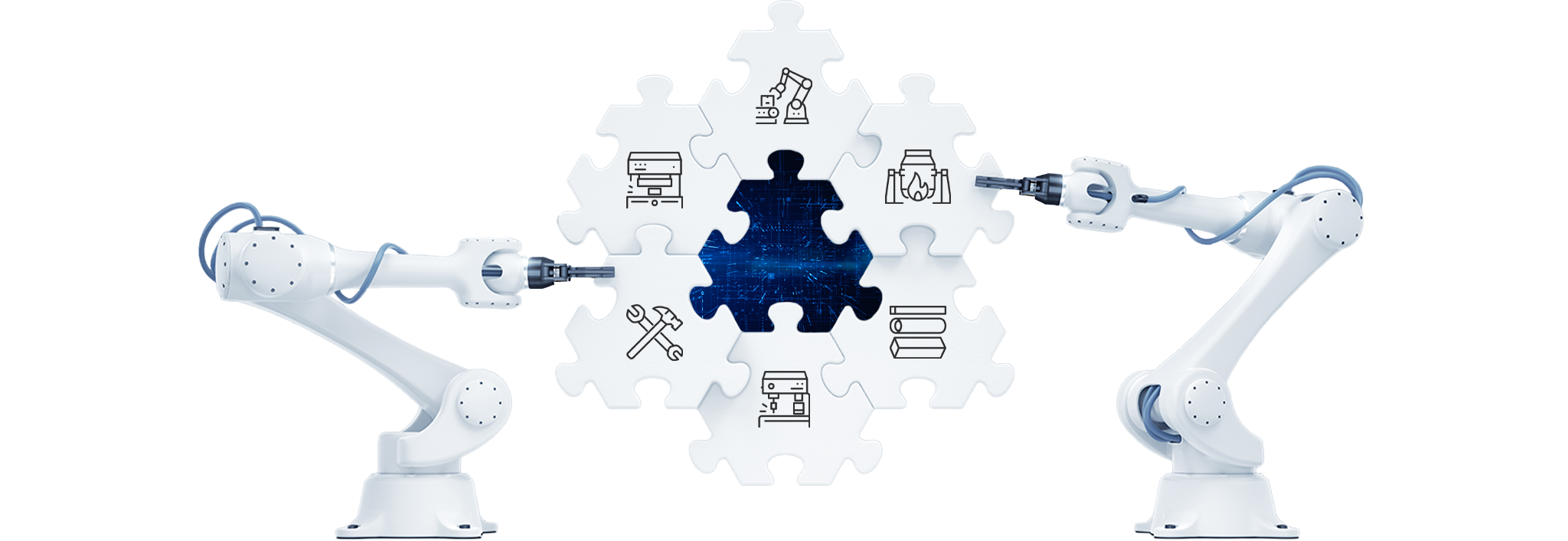
Manufacturing process reforms for DX of manufacturing as a whole
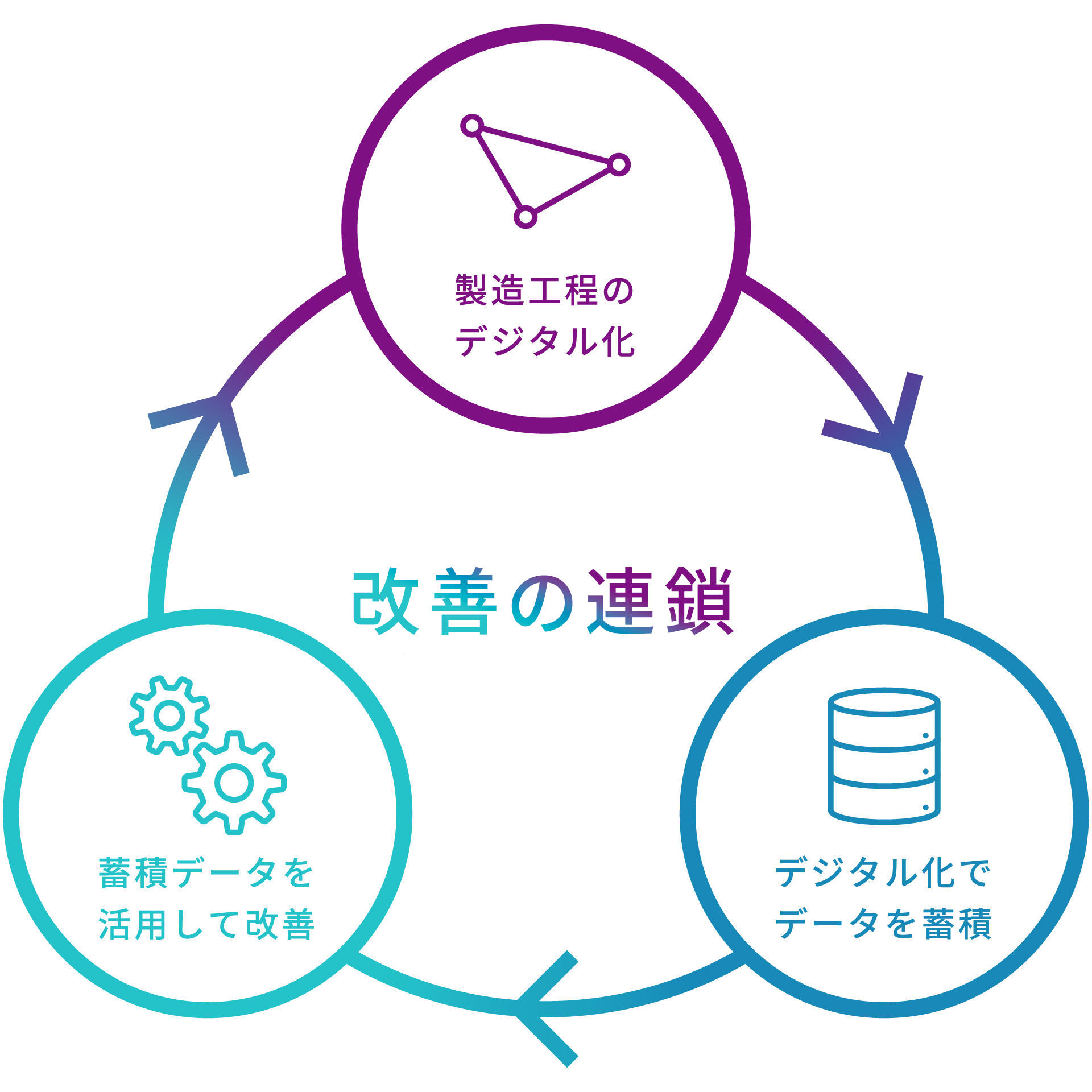
What is digitalization that leads to the next step that does not end with individual correspondence?
Digitizing manufacturing processes
- Improvement of processes that tend to become bottlenecks
- Reduce costs by improving productivity throughout the factory
- Maintaining product quality safety
など、"成果の見える化"につながります。
Approach to digitization that will change the future
Improving production efficiency with digital twins
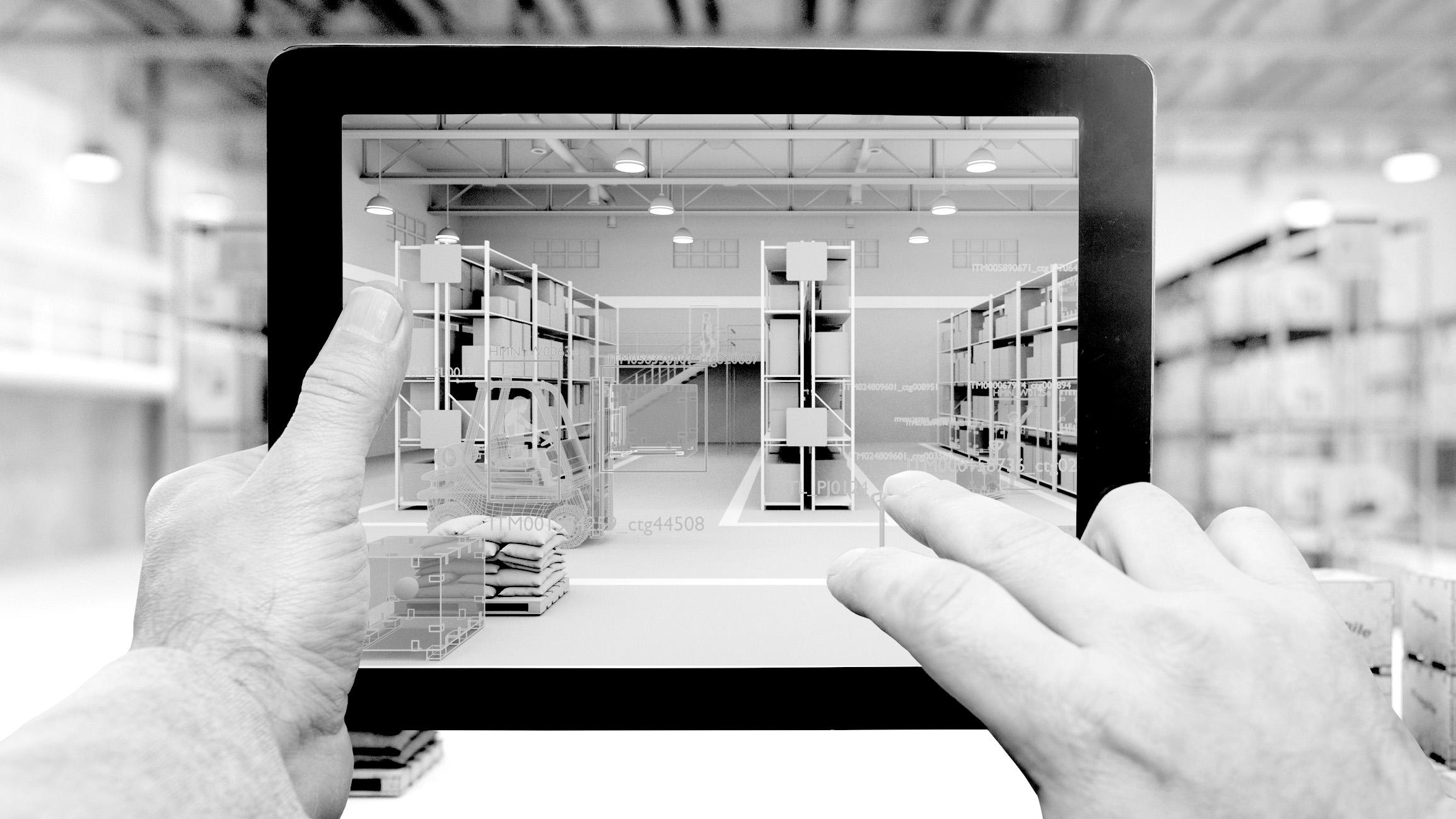
Simulation that changes jobs
Reproduce the factory in a virtual space, compare the current and future sites, verify the movement of people and their efficiency, predict and manage intermediate inventory
Realizing data-driven manufacturing
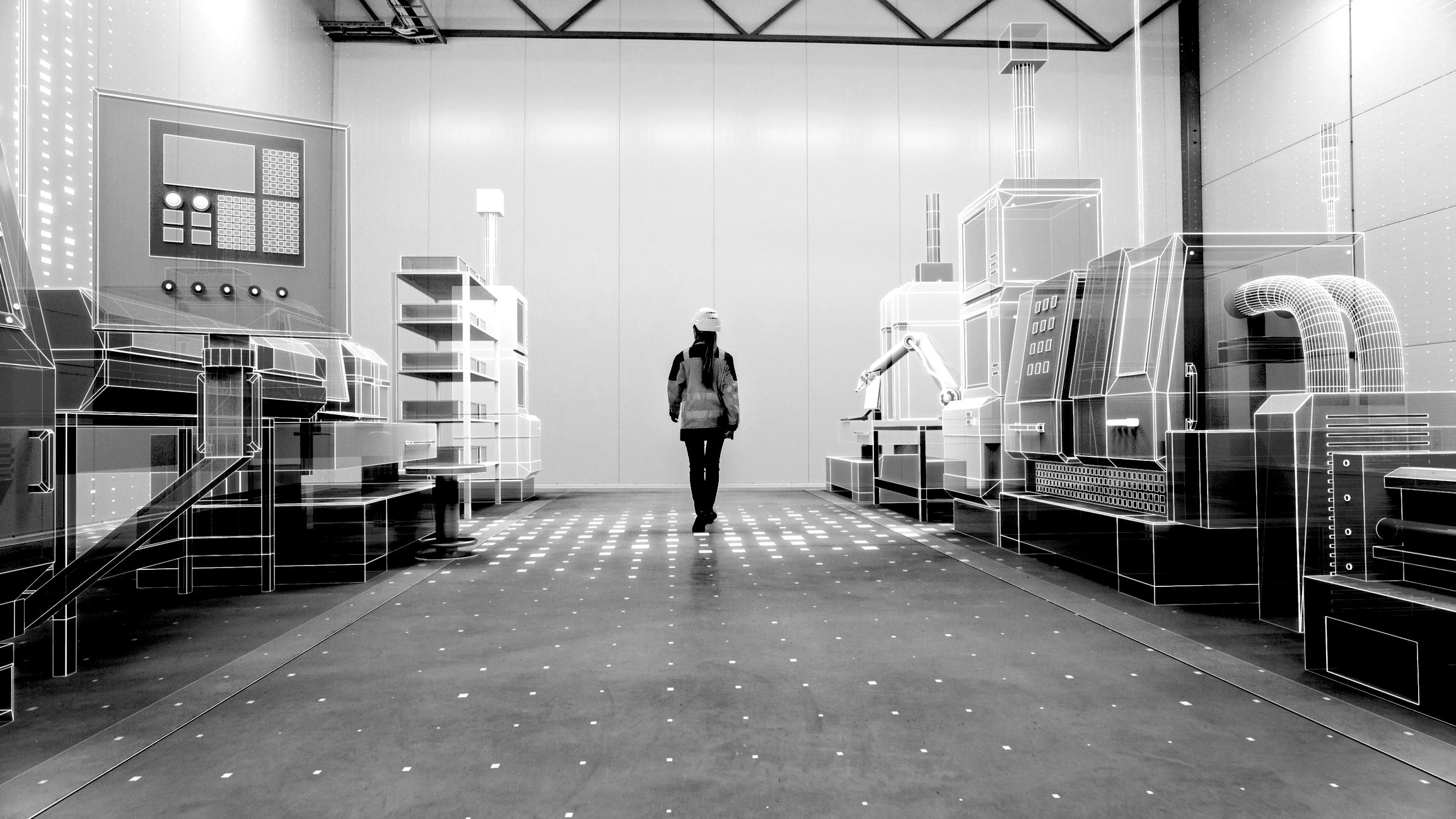
Experience MES (Manufacturing Execution System)
Build infrastructure that serves as the “foundation for Digital Manufacturing” such as business reform/improvement and automation (MES)
Equipment maintenance shifts from “prevention” to “prediction”
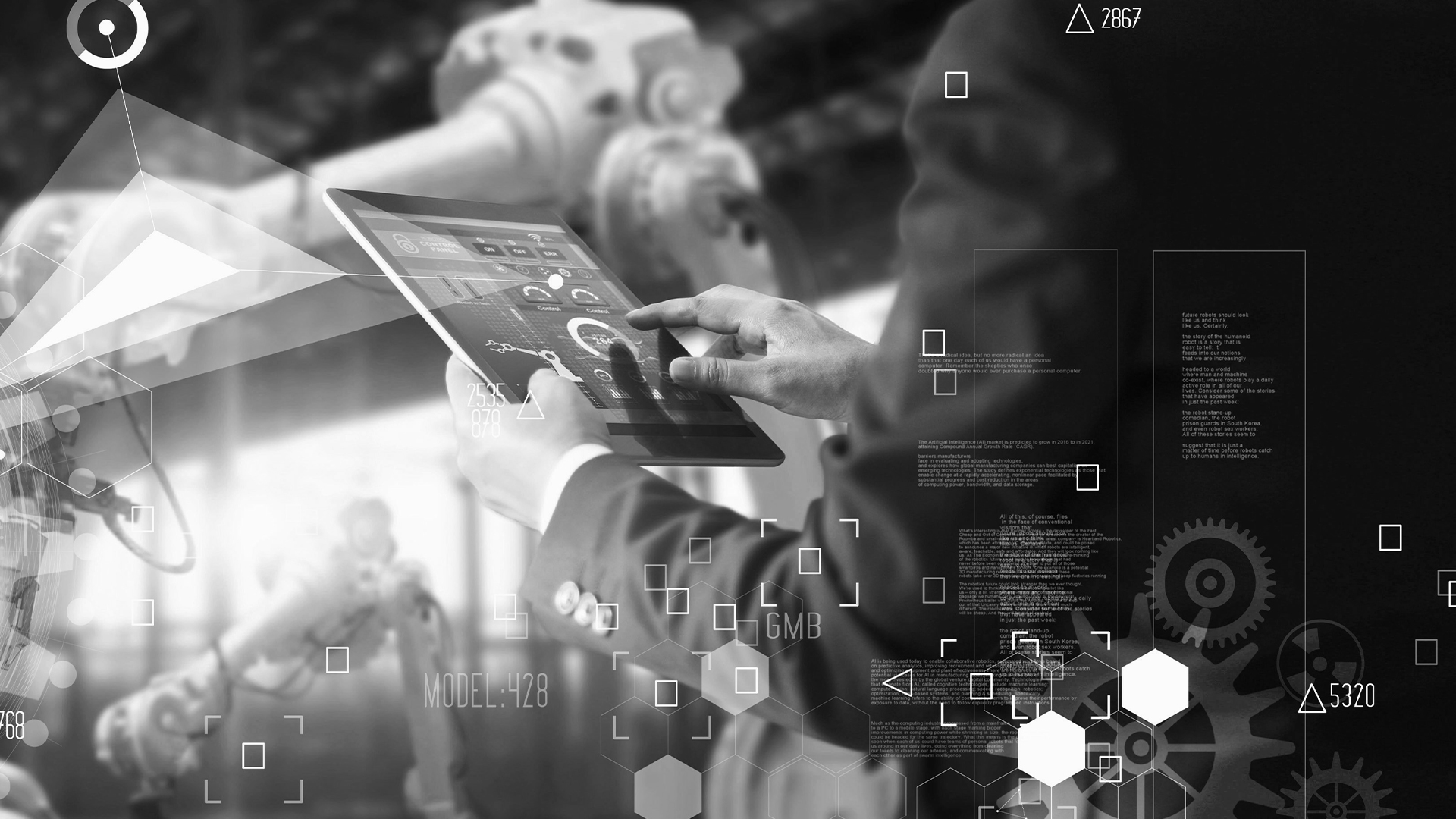
Predict equipment failure from sensing data
Abnormality detection/predictive maintenance (CBM) that enables everything from equipment maintenance to productivity improvement
From personalization to automation of appearance inspection process
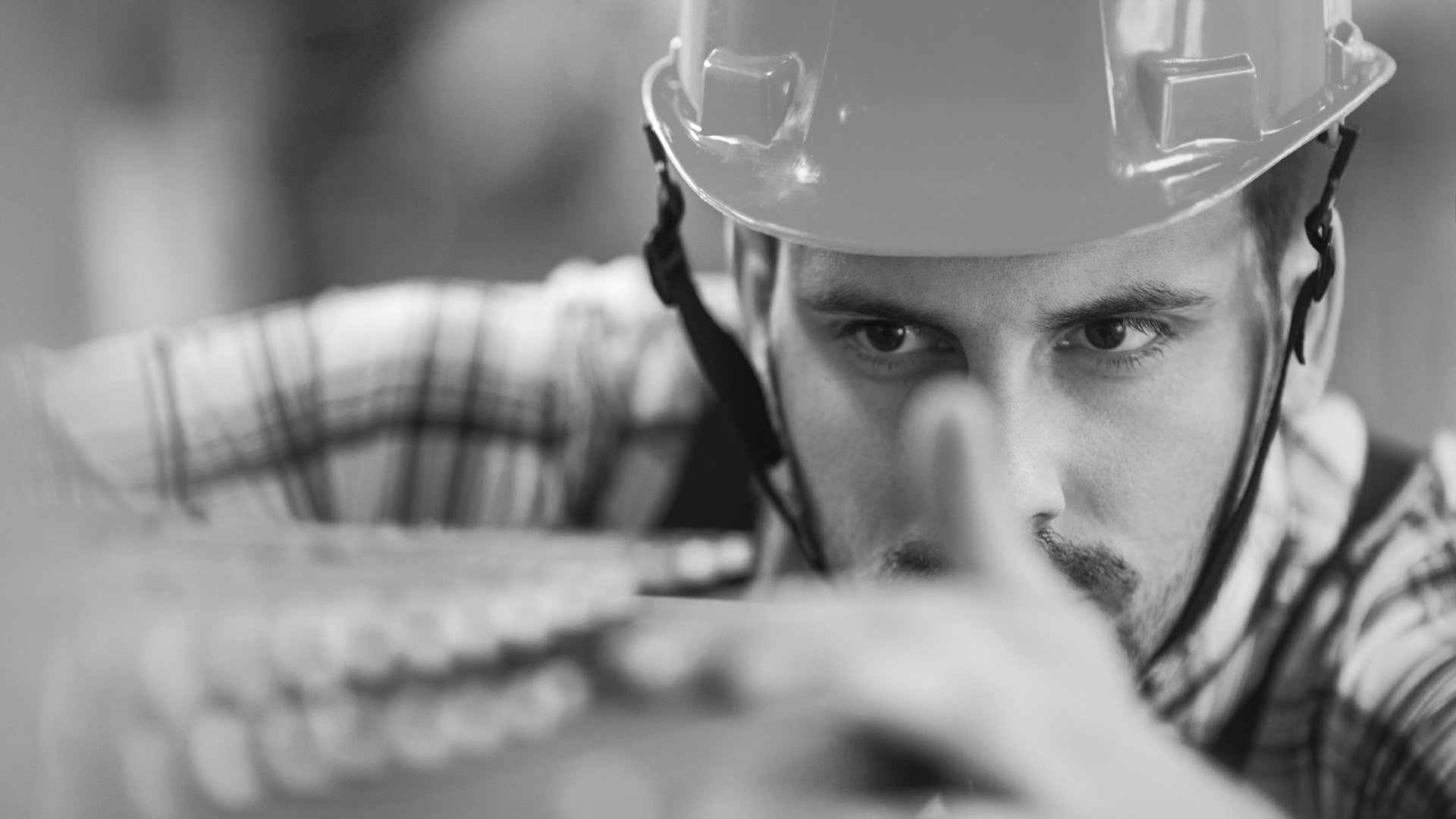
Passing craftsmanship to the next generation with AI
Achieving Visual inspection automation with "operable AI" created with a group of experts
Casting slag removal from personalization to automation
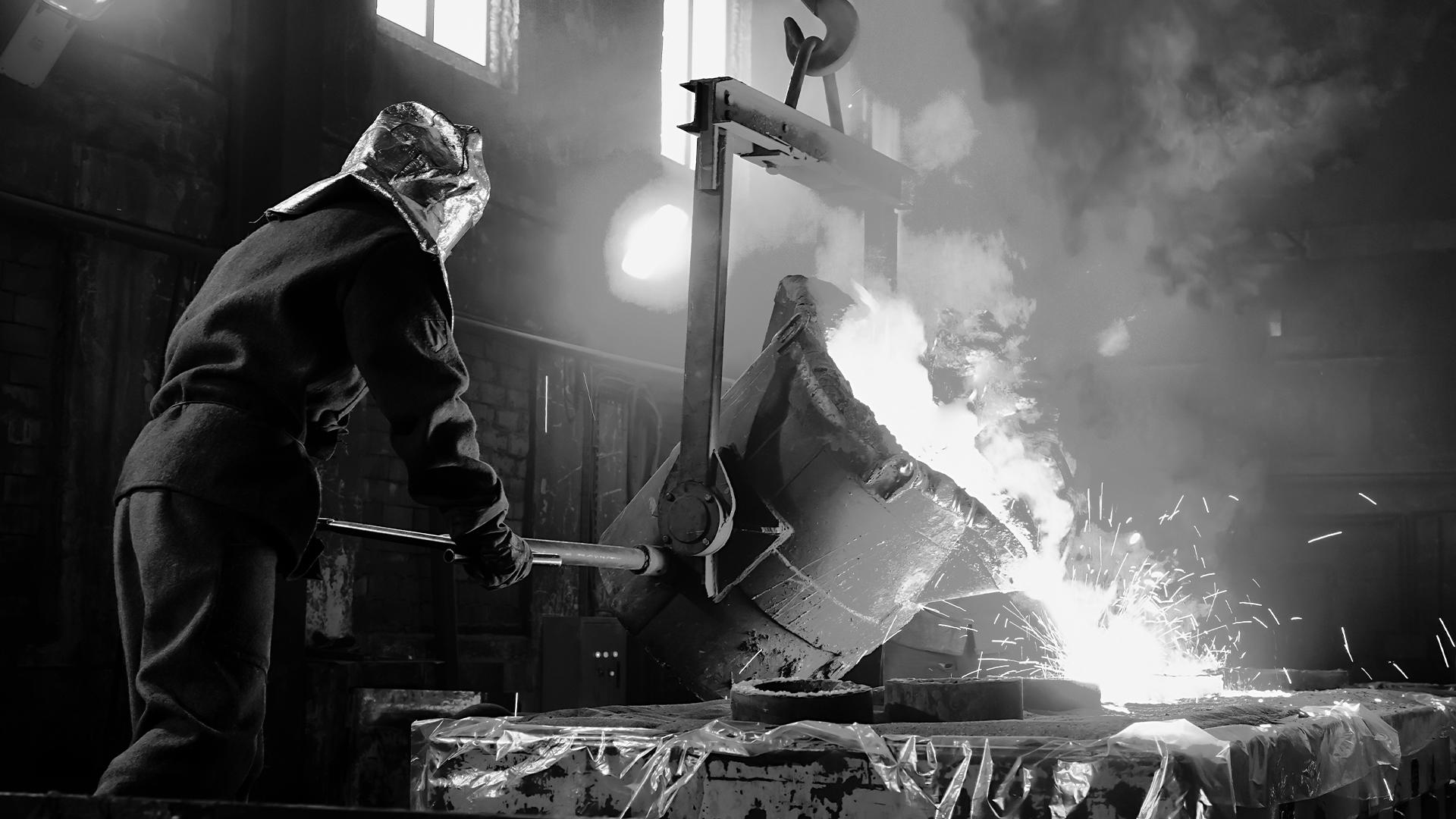
Aiming to create a comfortable working environment
Ensuring worker safety by determining casting slag with AI and automating removal work
Learning from videos, reforms by issue
Explore other approaches
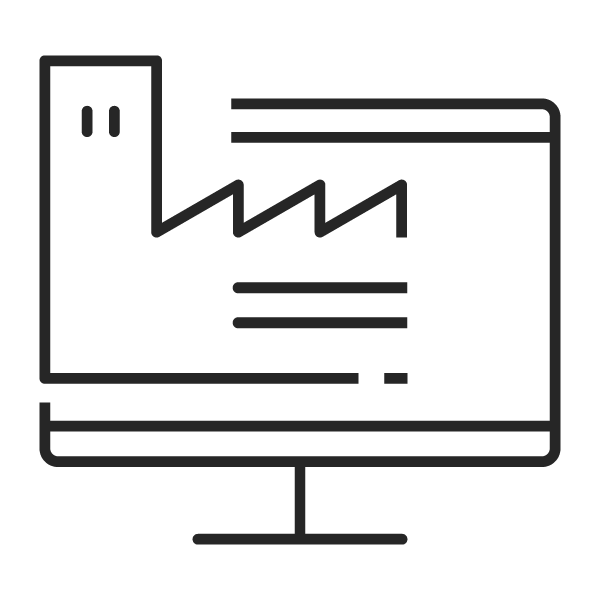
Digital twin that creates "three movements"
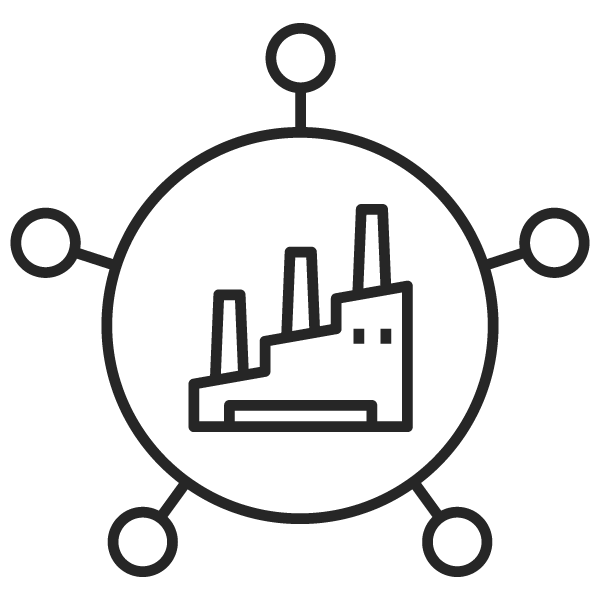
Digital Manufacturing starting from health checkup