Operations and Quality Chosen by Customers
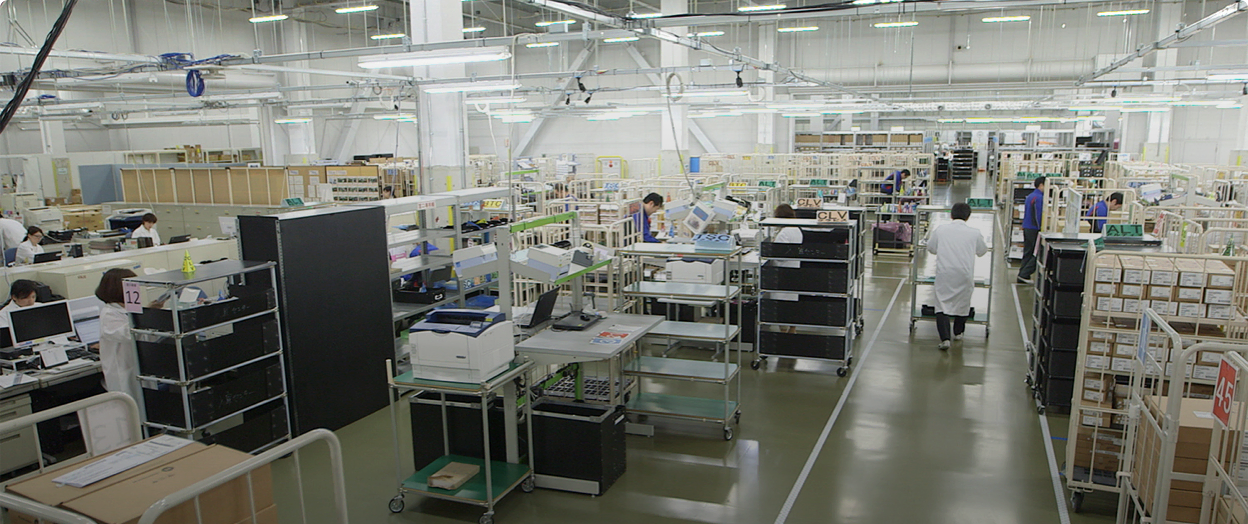
Logistics Operation
There is "Quality That Supports the Customer's Business"
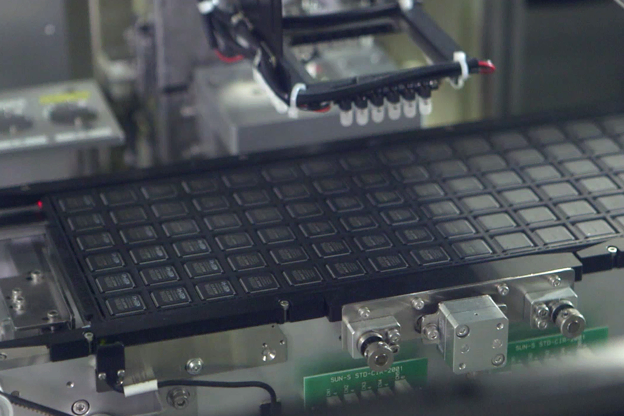
Semiconductors and other electronic components are used in all kinds of electronic products in the world, and there are a huge number of types. Since products of the same type have different functions and performance, shipping errors can have a major impact not only on the production site, but also on the operation of the final product. Therefore, the logistics of semiconductor products can be said to be the key to supporting the business of our customers.
Therefore, in addition to pursuing scale and productivity, Macnica is working hard every day to create a system that increases security and trust, taking into account the special characteristics of electronic components.
High Quality & Efficient Logistics
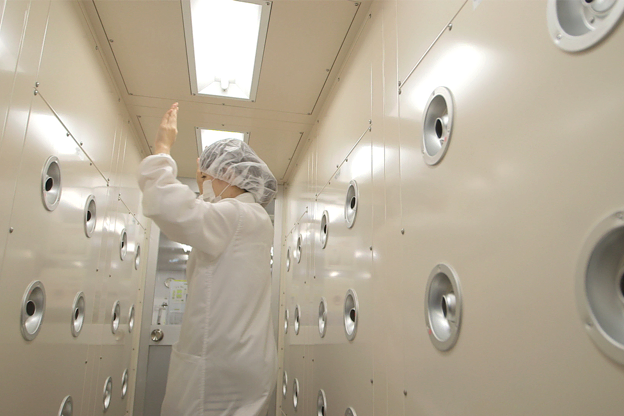
Yokohama Shinkoyasu. The logistics center, which has good access to the expressway and is ideally located as a distribution base, has a space of more than 6,000 tsubo and manages more than 500,000 boxes of inventory at any given time. In addition, we have Asia's largest writing center capable of producing more than 2 million PLDs (*1) per month, as well as a class 9 (*2) clean room.
1 PLD: Programmable Logic Device. An IC that can be freely programmed by the user.
2 Class 9: A grade representing the cleanliness of clean rooms stipulated by ISO14644-1.
Macnica has built its own WMS (warehouse management system) based on the know-how of a semiconductor trading company. In addition to the usual WMS features of receipt/shipment management, inventory management, and stocktaking management, it accurately manages manufacturing lot information that differs depending on product characteristics and uses, strengthening traceability. It also responds to individual customer needs by affixing identification labels to be used at delivery destinations such as production plants. In terms of improving efficiency, it outsources some operations to 3PL partner companies that have strengths in logistics operations themselves in pursuit of improving productivity and reducing costs.
Through these efforts, we have been able to reduce our rate of misshipments to 0.0015%, and maintain the highest level of quality in the industry. In addition, we provide our customers with peace of mind and trust through the use of facilities equipped with vibration control devices in preparation for earthquakes, and through the use of 20 ESD coordinators who are specialists in the risk of electrostatic breakdown.
Operational Capabilities Enhanced by Teamwork
Coordinators who support operations manage more than 1,000 orders backlog per person in an environment where the order situation changes every moment. Mainly, we are responding to timely delivery to customers and adjusting supply and demand to suppliers. To achieve this, we need to accumulate knowledge and quickly share information so that we can quickly respond to every case.
By constantly maintaining and updating manuals for each customer, we are working to strengthen the overall strength of the team while eliminating individual dependence. In addition, in preparation for the risk of a decline in service levels due to a shortage of operating personnel, we have set the goal of optimizing the work-life balance and have introduced telework ahead of the industry so that even women who are raising children can work.

In addition, coordinators with a wealth of business experience are involved in RPA development based on their own know-how, realizing the automation of many simple tasks. Productivity improved by RPA promotes work style reform, and the time saved is used to strengthen customer service and add further value.
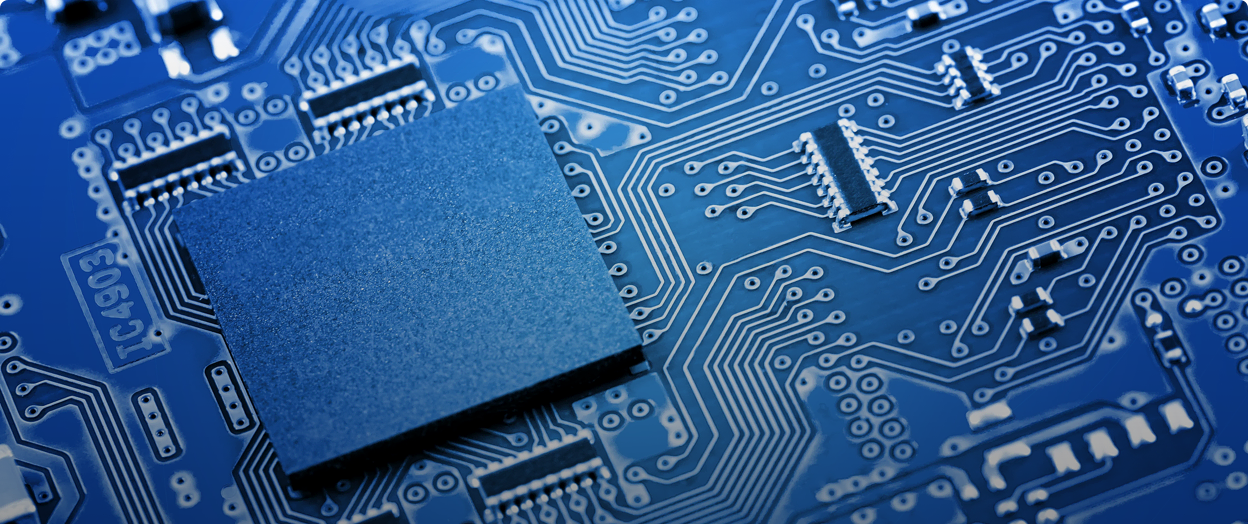
Semiconductor Product Quality
Commitment to Quality
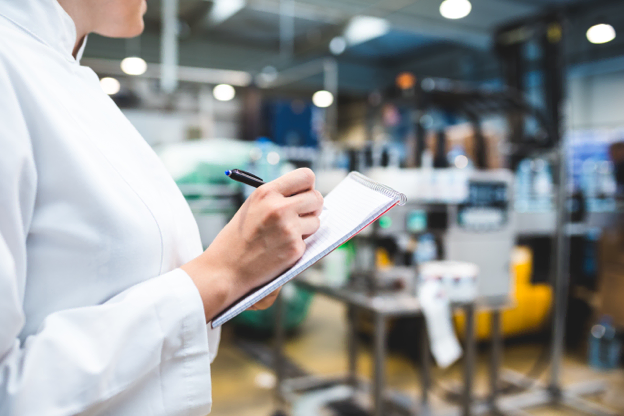
Semiconductors are used in every product around us. They range from the size of a grain of rice to the size of a child's palm. Various items such as shape, electrical, mechanical, and functional are stipulated in detail.
In order for customers to be able to use these semiconductor products with peace of mind, Macnica not only provides a stable supply of products through logistics, but also provides documents that customers need regarding quality, reliability, laws and regulations, etc. We create information, manage changes, and provide notifications.
Support Quality, Underpin Value
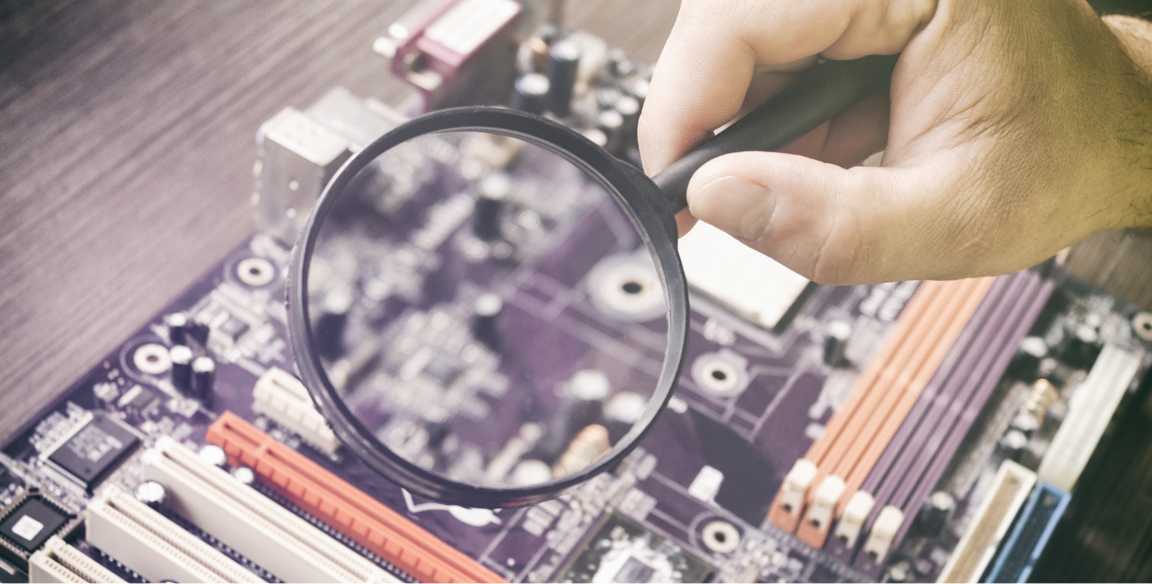
Delivery Specification
We understand the needs and issues from the stage when customers consider adopting semiconductor products, and stipulate the performance, characteristics, reliability, range of usage conditions, etc. of semiconductor products to be used before mass production of final products. We exchange delivery specifications. Depending on the product, there may be hundreds of pages, but this clarifies the common understanding of semiconductor product performance, quality, standardization, and safety.
PCN (notification of manufacturing process, material change, etc.)
As a continuous support after the start of mass production, if PCN is received, we check the impact on quality and reliability, notify the customer and obtain approval, so that we can make a prompt switchover. By coordinating with the logistics department, we reliably control the distribution of products before and after changes.
Trouble Shooting
In the unlikely event that a malfunction occurs, Macnica 's engineers (CQE/FAE) with specialized knowledge will promptly confirm the phenomenon, perform initial analysis, take countermeasures, and investigate the cause. 。
Responding to Environmental Surveys
In recent years, with the aim of reducing the burden on ecosystems and the global environment, laws and regulations on chemical substances used in each country and product have been strengthened. We confirm whether our products are in conflict with laws and regulations, and provide the information to our customers as appropriate.
Macnica Company Information
Also check this