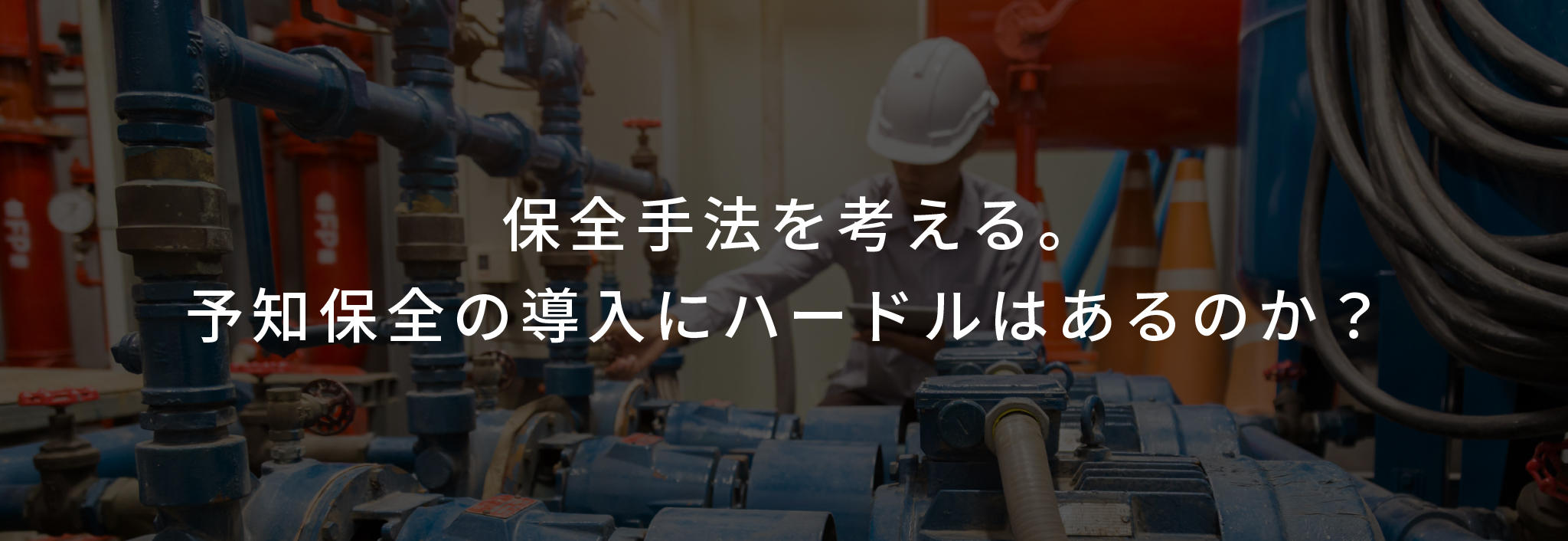
工場DXの一環として予知保全が注目されていますが、DXを推進する方にはさまざまな不安もあるのではないでしょうか。例えば「現在の保全手法から切り替えるほど、本当に効果があるのだろうか」「設備の故障をどこまで正確に予知できるのかがわからない」「データ収集が大変で、かえって手間がかかるのではないか」といった声を聞きます。
そうした疑問をお持ちの方に向けて、ここでは、設備保全の代表的な手法と課題、予知保全のメリットを紹介。また予知保全の導入ハードルについて考察していきます。
設備保全における3つの手法
製造業における設備保全の手法は、一般的に以下の3種類があります。
・事後保全(BM:Breakdown Maintenance)
・定期保全(TBM:Time Based Maintenance)
・予知保全(CBM:Condition Based Maintenance)
それぞれ、次のような特徴があります。
事後保全(BM:Breakdown Maintenance)
・設備の不具合が起きた後に、メンテンナンスを実施する方法です。
・設備の復旧までに計画外のダウンタイムが発生します。
・生産効率の低下、機会損失、ダウンタイムの長期化など、多くのデメリットが指摘されています。
定期保全(TBM:Time Based Maintenance)
・設備の保全周期を決め、定期的にメンテナンスを実施する方法です。
・不具合の有無にかかわらず、メンテナンスを行います。
・事後保全に比べて、計画外のダウンタイムを減らすことができます。
予知保全(CBM:Condition Based Maintenance)
・設備の状態に応じて、最適なタイミングでメンテナンスを実施する方法です。
・設備にセンサーを取り付けてモニタリングを行い、不具合の予兆を検知したら、メンテナンスを行います。
・DXを活用した効率的な保全方法として期待されています。
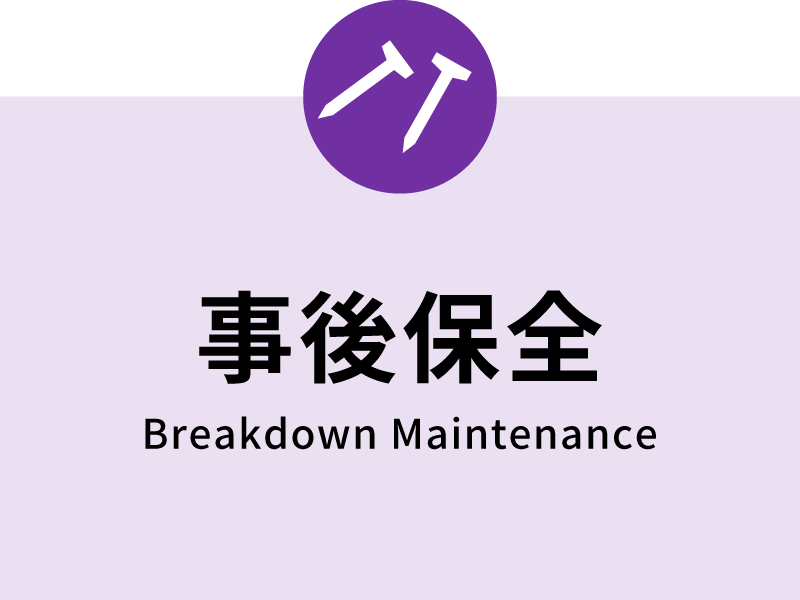
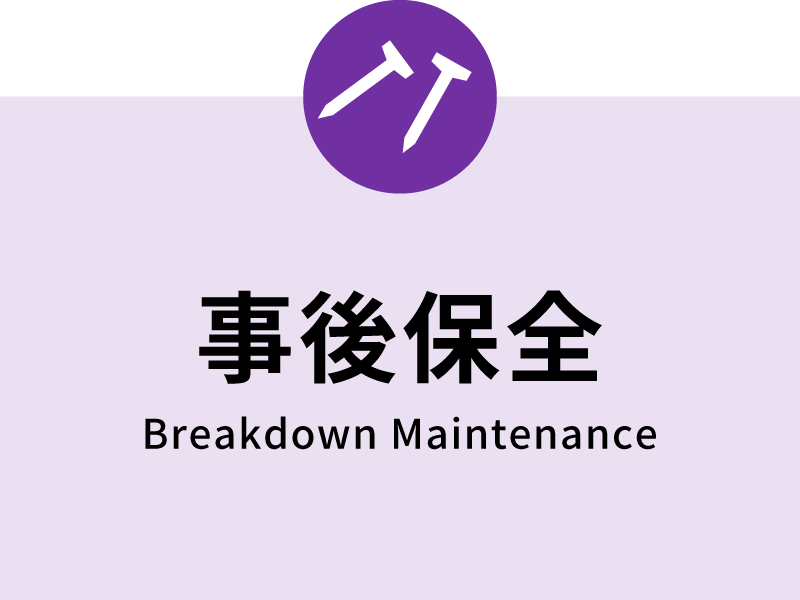
設備故障後にメンテンナンス実施
・保全が事後になるため、ダウンタイムの発生におけるマイナスの発生や復旧までに時間が掛かる傾向がある
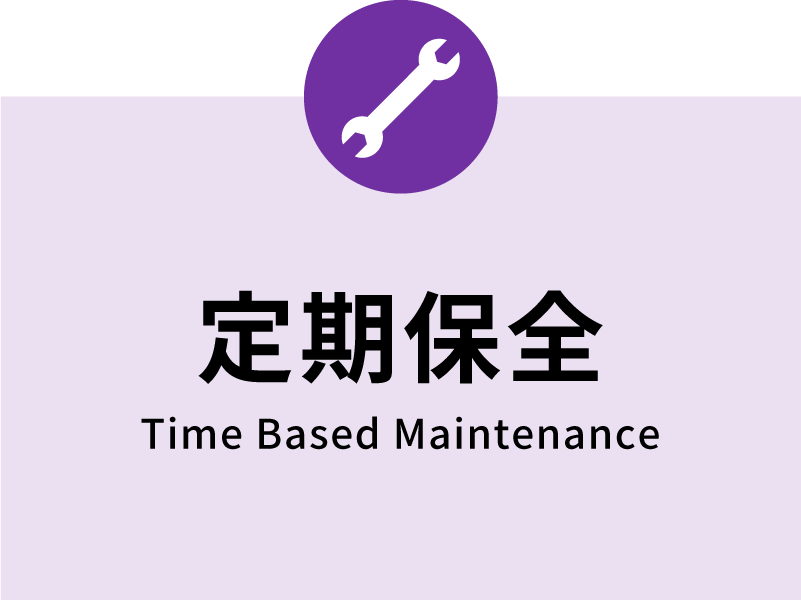
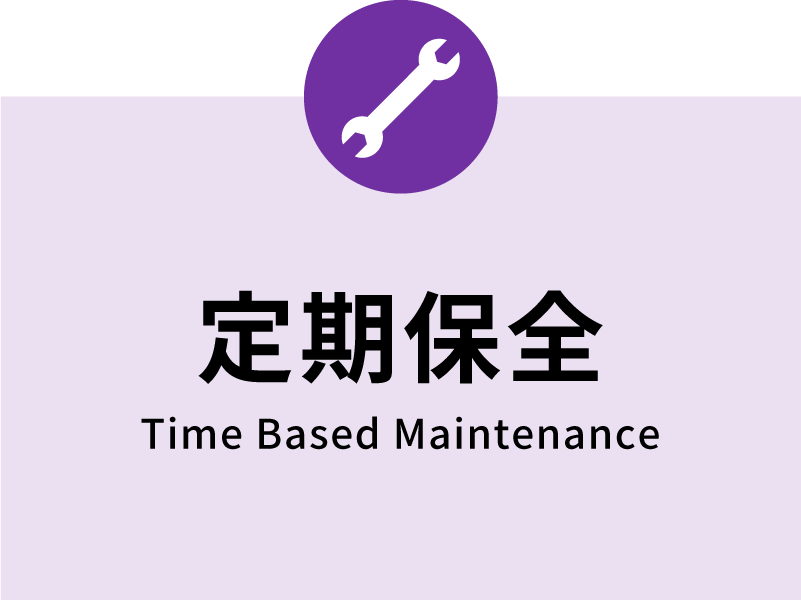
周期:設備の保全サイクルでメンテナンス実施
・設備が壊れていない場合でもメンテナンスを行う為、オーバーメンテナンスになる可能性が高い
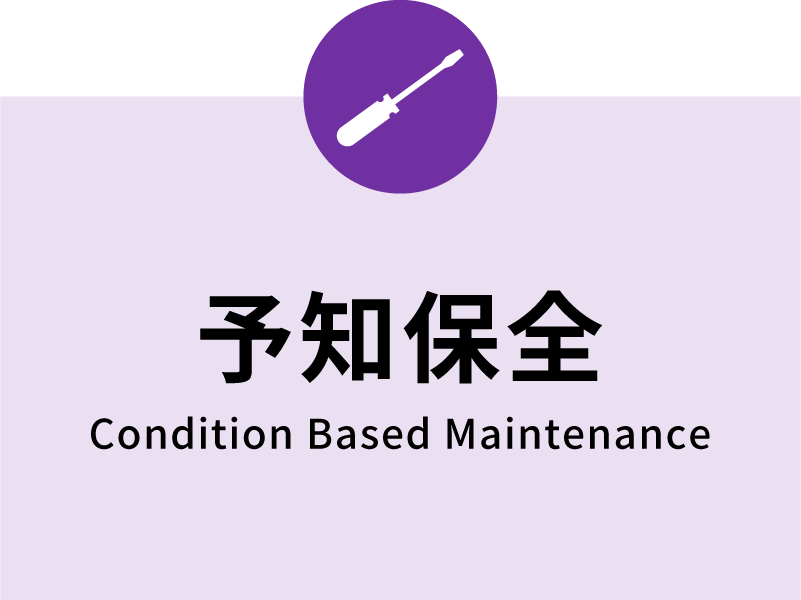
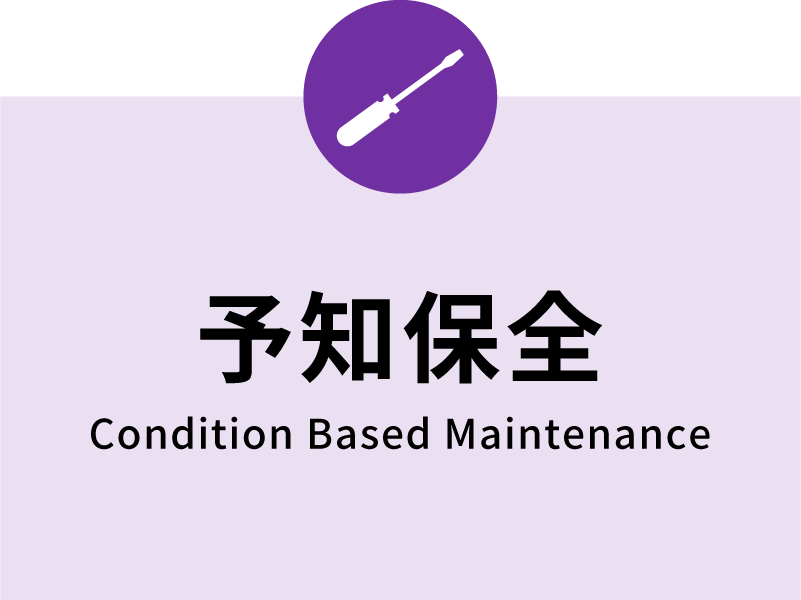
状態:設備の状態に応じて適切なタイミングでメンテナンス実施
・効率的なメンテナンスが可能だが、一般的にはデータ収集や分析の専門性が求められる
この中で、最も一般的に行われているのが定期保全です。事後保全に比べてダウンタイムを削減できるメリットがありますが、デメリットや課題も存在しています。そこで、定期保全のデメリットを紹介します。
定期保全の課題と予知保全のメリット
定期保全にはどのようなデメリットがあるのでしょうか。主な課題を以下にまとめます。
●オーバーメンテナンス
不具合がなくてもメンテナンスを行うため、例えばまだ使用可能な部品を早めに交換してしまい、オーバーメンテナンスになる恐れがあります。オーバーメンテナンスとは、点検や部品交換が過剰に行われることで、コストの増大要因となります。一方、オーバーメンテナンスを避けるために保全周期を長くすると、突発的な不具合のリスクが高まってしまいます。
●保全要員の不足
定期保全では頻繁にメンテナンスが実施されるため、事後保全よりも多くの要員が必要になります。保全要員には、専門的な知識や技術が求められます。昨今は人手不足が深刻化しており、適切な要員をスケジュールどおりに確保できない場合があります。
●診断のばらつき
従来の設備保全では、音やにおいなど人間の五感に頼る診断が行われており、担当者の技能によって精度にばらつきが生じることがあります。技能の伝承も難しいため、経験豊富な技術者が定年退職を迎える中、信頼性の確保が課題となっています。
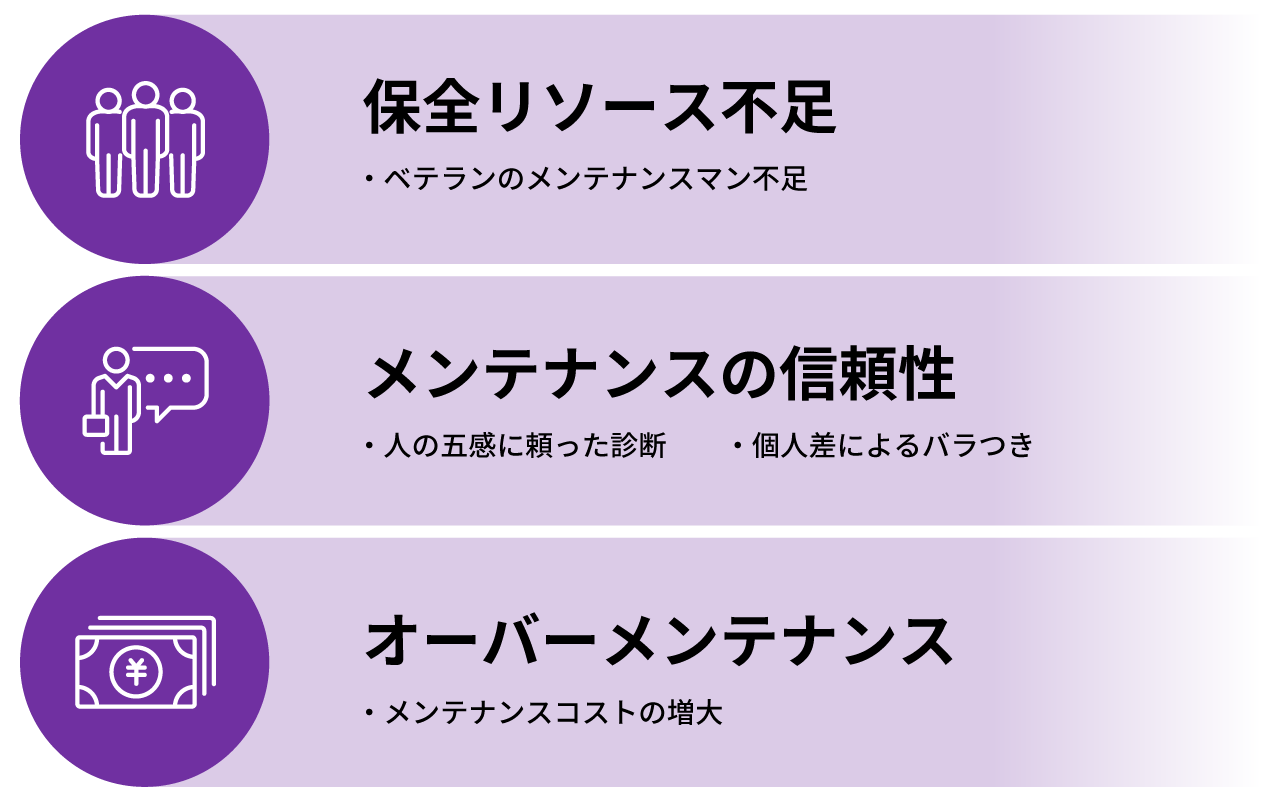
定期保全には課題が多い。予知保全のメリット
予知保全のメリットとは
こうした課題の解決に向けて期待されているのが、DXを活用した予知保全です。予知保全では設備の状態を監視し、不具合の予兆を捉えてメンテナンスが行われます。そのため、以下のようなメリットが得られます。
●オーバーメンテナンスを防ぎ、無駄なコストを削減できる
●メンテナンス回数を最適化し、保全要員を効率的に活用できる
●データに基づく診断を実現し、担当者による精度のばらつきを解消できる
人手不足や設備の老朽化に悩まされている製造業において、設備保全を効率化できる予知保全は、ぜひ取り組むべき施策だといえるでしょう。
予知保全の知っておくべき導入ハードル
一方、予知保全の導入にはいくつかのハードルがあります。以下は、予知保全の導入にあたり、企業が直面する一般的な課題です。
【データ収集】設備ごとにセンサーを選定
設備の状態を把握するために、センサーを取り付けてデータを収集します。設備ごとに適切なセンサーを選定し、最適な取り付け位置を判断することは容易ではありません。
【計測頻度】必要十分なタイミングを判断
データの計測頻度やタイミングを検討します。センサーの消費電力なども考慮して、必要十分な計測タイミングを決定しなくてはなりません。
【閾値設定】正常と異常の基準を決定
収集したデータについて、正常と異常を区別するための閾値を決定します。正常値の範囲内での変動なのか、異常値なのか、その線引きには非常に難しい判断が求められます。
【データ分析】膨大なデータから情報を抽出
センサーのデータを分析して、有用な情報を抽出します。膨大な生データの分析作業には、高度な専門知識が求められます。
【診断】異常箇所や劣化程度も特定
データ分析の結果をもとに、設備の状態を診断します。異常の有無だけでなく、発生箇所や劣化程度まで特定することは、設備診断の専門家でなければ困難です。
このように、予知保全にはデータ活用にともなう課題があります。特に難しいのは、異常の初期兆候を正確に判断することです。設備が正常に稼働している間は、異常時のデータが得られません。一度設備が故障するまでは、閾値設定や異常診断のためのデータが不足します。
多くの場合、予知保全を導入してから実運用をスタートするまでに、多大な時間とコストがかかります。しかし、DX活用を急ぐ企業としては、手間やコストをあまりかけずに、できるだけ早く効果を実感したいのが本音でしょう。
予知保全には多くの導入ハードルがあることから、近年は一度予知保全に取り組んだものの、なかなか成果が得られず、挫折する企業も出てきています。
導入の敷居をなくす「Mpression® Smart Motor Sensor」
実は、こうした課題を解決できる予知保全ソリューションとして、スマート・モーター・センサー「Mpression® Smart Motor Sensor」(以下、スマート・モーター・センサー)があります。その主な特長は、以下のとおりです。
【データ収集】所定の場所にセンサーを設置
バッテリー駆動のセンサーモジュールを、所定の位置に取り付けるだけで、モーターの状態を把握できます。
【計測頻度】適切なタイミングで自動計測
スマートフォンのアプリから初期設定を行うと、適切な計測頻度が自動設定され、データ収集がスタートします。
【閾値設定】学習済みのAIが自動判定
AIが、モーターの挙動に関する膨大なデータを事前に学習。アルゴリズムに基づいて、最適な閾値が自動で設定されます。
【データ分析】振動・温度・磁界データを自動分析
センサーが振動・温度・磁界のデータを収集し、Wi-Fi経由でクラウドに送信。AIが自動で分析します。分析結果は随時ダッシュボードで確認できます。
【診断】AIが異常箇所まで自動診断
AIが異常を検出すると、すぐに通知を行います。異常箇所や対処方法まで自動的に診断できます。
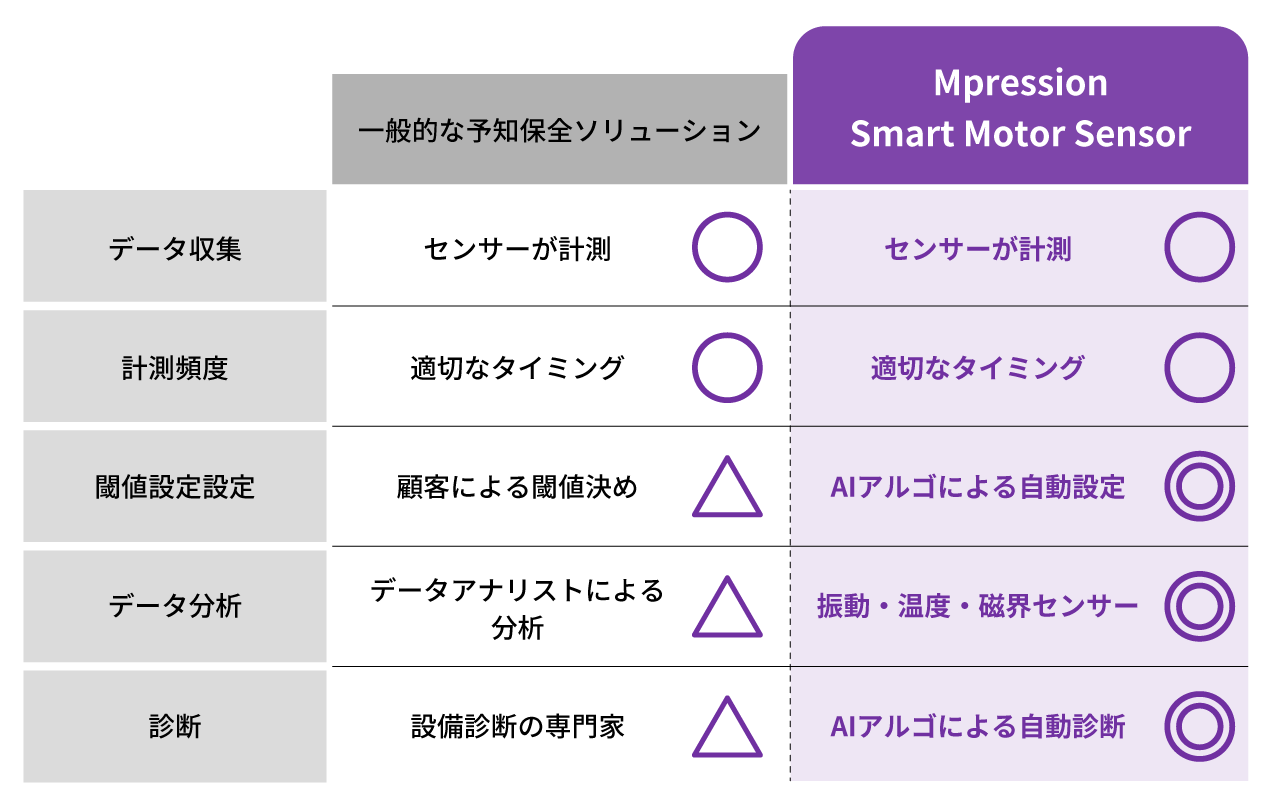
予知保全(CBM)にも課題はある。低圧三相モーターならSMSがすべて解決
スマート・モーター・センサーは、予知保全の導入にともなう一般的な課題をすべてクリアしています。手軽に導入し、すぐに効果を実感することが可能です。
スマート・モーター・センサーは低圧三相かご型誘導モーターに特化したサービスです。低圧三相かご型誘導モーターであれば、データ収集から異常診断まで、予知保全をセンサー1台で実現できます。もし該当するモーターをお持ちであれば、この機会に予知保全を試してみてはいかがでしょうか。
ご興味のある方はこちらもご参照ください。
お問い合わせ
本記事についてご質問がありましたら、以下よりお問い合わせください。