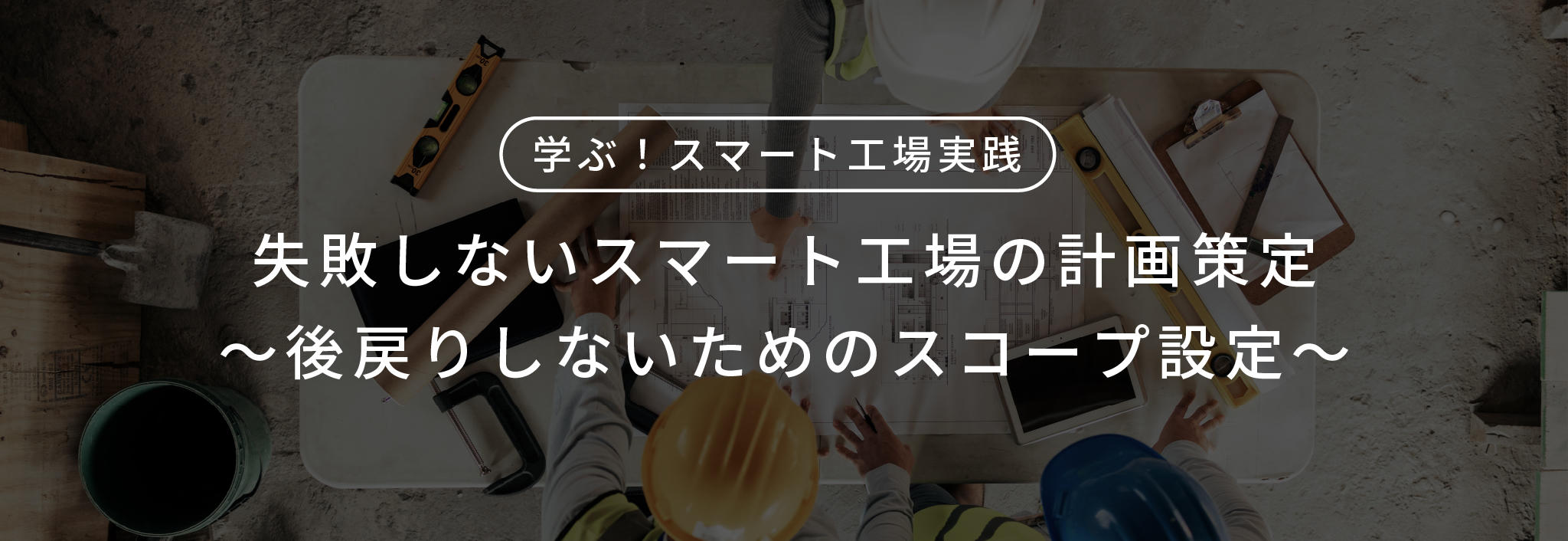
1.一歩踏み出すとぶつかる障壁
多種多様な製品を製造する生産現場の工程や設備は多岐にわたり、そこから生み出される生産現場データの点数は膨大であるため、スマート工場の計画策定は容易ではありません。「標準化をしながら統一されたシステムを管理し、蓄積データをもとに生産性向上や原価低減を実現できたら、どれだけ価値があるだろうか?」と、生産部門に携わる方であれば考えるのではないでしょうか。
しかし、そういった取り組みでは抽象度の高いビジョンと現場の具体的な課題の間にギャップが生まれやすいうえに、複数の部門を巻き込んでプロジェクト推進を行う必要もあることから、実現に苦労されている方が多いのも事実です。
スマート工場の計画策定は結局のところ、Why(事業課題)から考え、What(製造現場のデータを活用して行う業務)を具体化し、How(どのようなシステムで、どのようにデータを収集して活用するか?)を検討することにつきます。
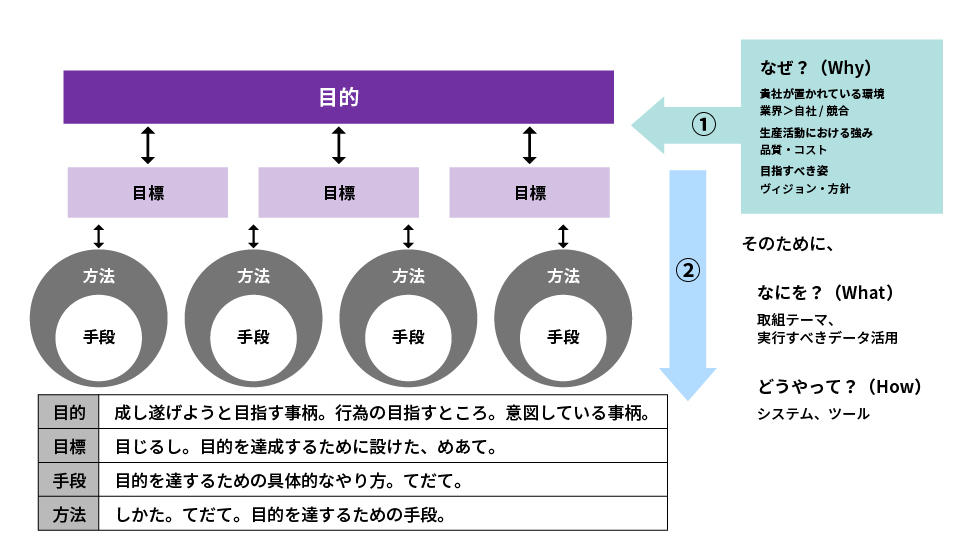
マクニカでは、多種多様な業界のお客様のスマート工場推進プロジェクトをご支援しております。上図のような過程では、特にデータやシステムの要素が強くなる「What」や「How」の段階において、生産部門の方にとって非専門分野であることから心理的な障壁を感じてしまう方も少なくないように思います。
その背景には「過去に会社の中でさまざまなデータ活用に取り組んだものの、製造部門向けに作ったシステムが使われなかった」「特定の工程やテーマに対してPoC的に取り組んだが他工程やテーマに拡張できなかった」といった、苦い経験もあるように感じます。
そのため、「また使われないシステムになってしまわないか?」「また横展開できずに無駄になってしまわないか?」と心配になるのではないでしょうか?
以降はそういった方に向け、マクニカが考える、後戻りのリスクを最小化した「What」にあたるスコープ設定の流れをご紹介します。
※本記事の全容はホワイトペーパーでもご紹介しております。
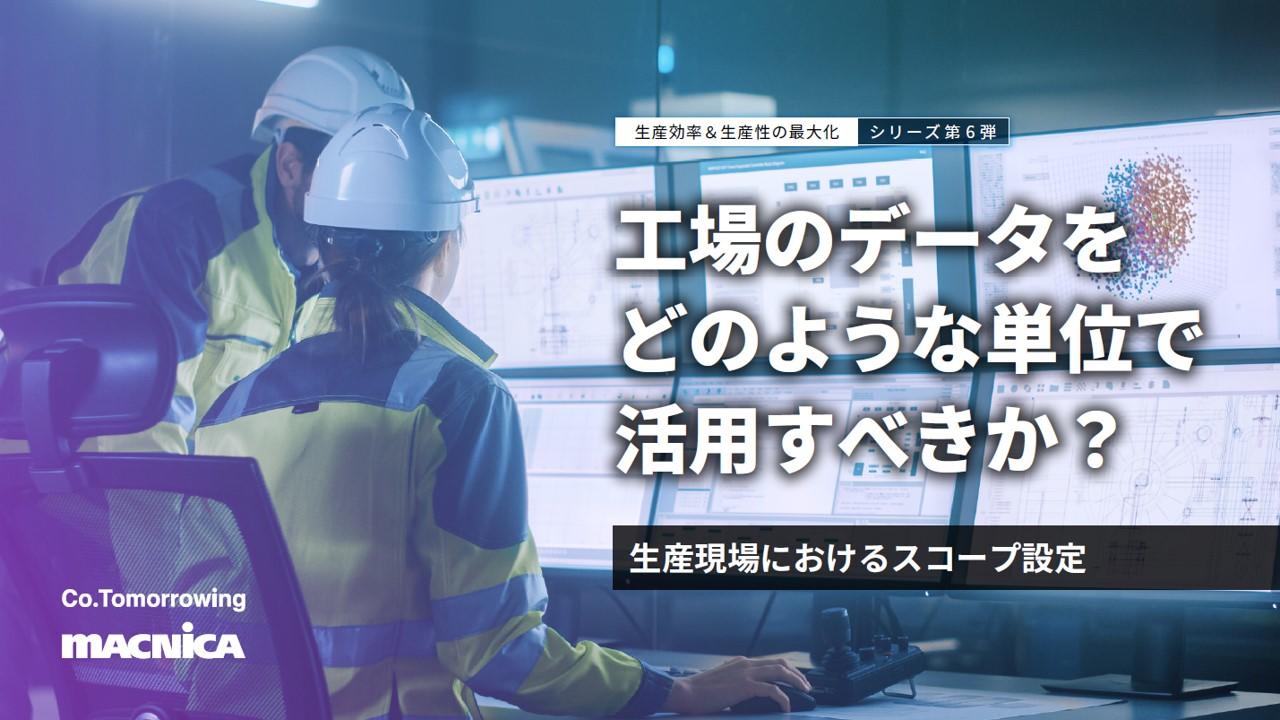
【おすすめホワイトペーパーのご案内】
IoTやDXの重要性が高まる近年では、生産現場のデータ活用がより求められています。
本資料では、お客様とマクニカによるプロジェクト推進の実体験をベースとした、
重要な目的設定のポイントや、手戻りを発生させないためのアプローチをご紹介します。
2.スマート工場のスコープ設定
まず、活用したいデータが生じるデータソースを棚卸してみます。さまざまなお客様と取り組みさせていただいたなかでは、ほとんどのデータソースは3つに集約されることが明らかになっています。
1つ目は、「生産設備」そのものです。具体的には、工場内で複数の工程・ライン・設備によって行われている、各生産設備の稼働実績データを指します。
2つ目は、生産設備を動かすために必要な付帯設備、つまり「ユーティリティ」です。生産設備を動かすためには動力源となる電力やガス、稼働するために活用する水や蒸気やエアなどが該当します。
3つ目は、「記録」です。生産現場では、実績管理のために日報や点検票といった帳票にその日の作業を記録することが徹底されています。紙に記載された情報には設備データからは読み取れない現場の実態も記されているため、活用したいデータソースの1つになります。
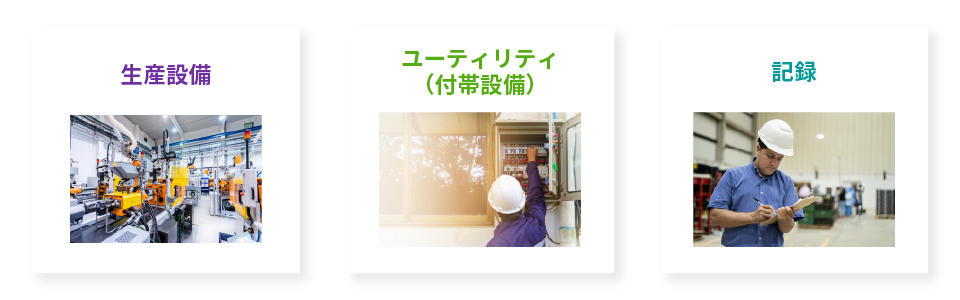
次に、データソースにおけるデータ種別を整理してみましょう。ここで大切なのは、データ1点1点の項目名(エラー信号名や温度・振動)ではなく、そのデータ項目の種別の粒度で考えてみることが大切です。詳細まで考え始めた場合、その数は数千・数万にものぼり、検討しきれないためです。
整理が完了したら、どのようにスコープとして区分するかを考えます。スコープ区分とは、生産現場のデータ活用で用いる単位です。具体的にデータを活用して取り組みたい事項に対し、どのデータソースの、どのデータ種別が必要になるかをグルーピングします。
たとえば、「環境対策を推進する際にはユーティリティから収集される値や生産設備の電力モーター値が必要」「生産設備の稼働/停止信号や、その理由となる設備停止エラー信号を活用して実績管理をデジタル化したいが、生産カウンタ値や不良情報となる不良カウンタ値と不良エラーコードも必要」といった具合です。
ここで、マクニカによる実例をご紹介します。
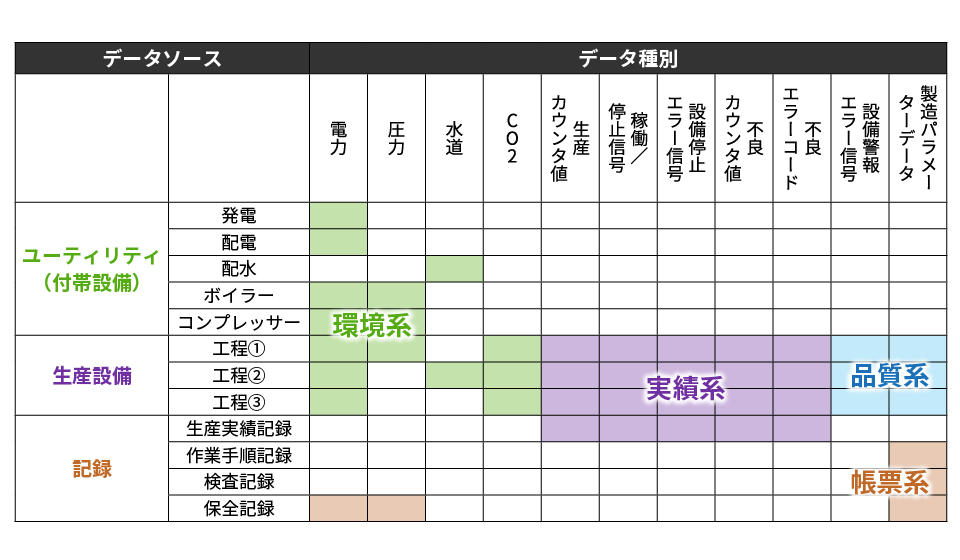
この例では、取り組みたい事項を下記の4つに分類しています。
①環境系:環境対策の推進のために生産現場データを活用し、省エネ対策をしたい
②実績系:生産現場データを活用して現場の効率改善を推進したい
③品質系:製造の際に計測された製造条件に関するデータを活用して品質改善を推進したい
④帳票系:製造現場で作業者が書いている記録をデジタル化することで作業負荷軽減とデータ参照の活性化を推進したい
上の表からは4つのスコープそれぞれで、どのデータソースの、どのデータ種別が必要かが分かるかと思います。
スコープ区分ができたら、取り組みたい事項の優先順位からどのスコープをどのライン(エリア)にシステム実装を行っていくかを検討していくことになります。ここで大切なのは、下記の2点です。
1.スコープ区分した範囲より小さなシステム実装はしないこと
取り組みたい事項から、必要なデータソースとデータ種別を基にグルーピングしたのがスコープ区分です。スコープ区分された範囲は、合わせて活用したい範囲であることは明確です。この範囲より小さなシステム実装をしてしまうと、必然的にエリア/機能拡張が生じた際に、「このデータも必要だったのに……」と後戻りすることになります。
2.複数のスコープをまたがるシステム検討をしないこと
理屈上は、取り組みたい事項からデータソースとデータ種別を選んでいるため、他のデータソースやデータ種別が必要になることはありません。逆に、取り組みたい事項に不要なデータを収集することは、時間の浪費になります。
下図は、マクニカが4つのスコープ区分を踏まえ、最適なシステム(ソリューション)の選定・実装の検討を行った際の全体像を示しています。このケースでは実績系と品質系をそれぞれ別に考慮しましたが、同一のシステム(ソリューション)が2つのスコープに最適という結果でした。
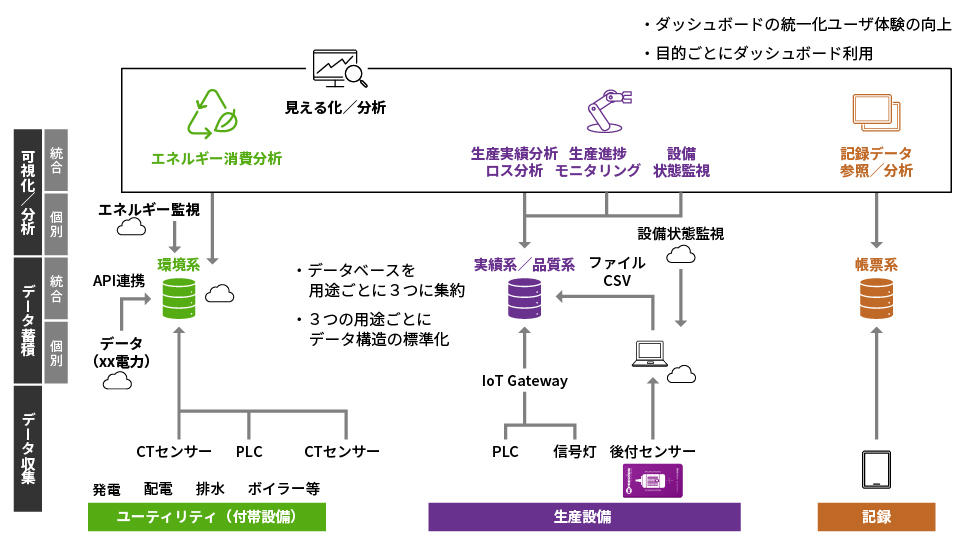
3.スマート工場の着実な一歩を!
今回はスマート工場の計画策定におけるスコープ設定の流れをご紹介しましたが、いかがでしたか?
本記事が、後戻りのリスクをできるだけ軽減したいという方に少しでも寄与し、また貴社のプロジェクト推進のお役に立てば幸いです。
なお、本コラムでご紹介させていただいたスマート工場におけるスコープ設定の全容はホワイトペーパーにまとめております。
スマート工場推進の具体的な流れにご興味のある方向けに、ウェビナー動画もご用意しております。
いずれも下記リンクからダウンロードいただけます。
※ダウンロードにはお申し込みが必要です