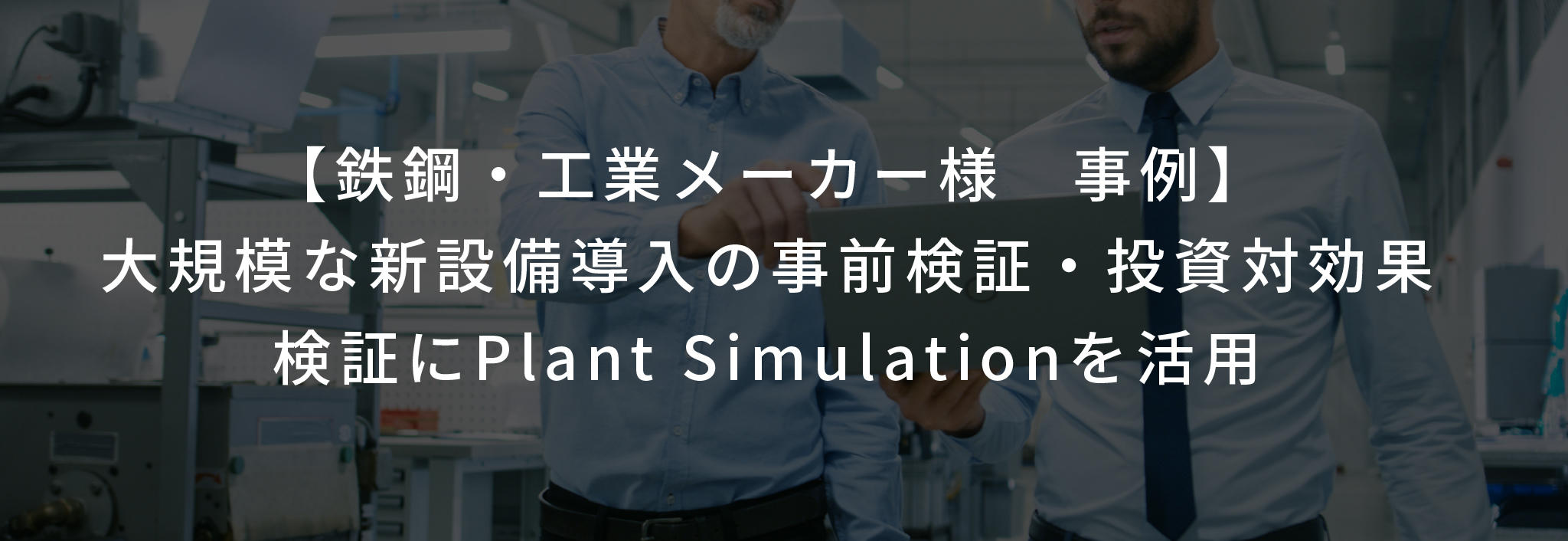
DX推進の背景
目的
-
大規模な設備投資を行うにあたり、
-
期待する生産量の増加が実際に見込めるかどうかの検証
-
投資対効果の検証
課題
-
設備導入にかかる費用に対し、期待する投資対効果が得られるのか不明
結果
-
期待する効果が得られないということが判明
-
不要なコストをかける前に、計画を変更することに成功
1. 背景
当時、使用しているほとんどの設備が既に20年、30年経っており、老朽化が課題となっていたため、新規設備への更新を検討していました。
また、作業員が行う工程も多くある中で、大口受注の話も出てきていたため、設備を自動化し、作業員を増やすことなく生産効率を上げるための検討をすることになりました。
検討を始めた当初は自社内で設備の仕様検討のための調査をし、ロボットベンダーや加工機械メーカーとともに機械の仕様やオプションについて話を進めていました。
2. 課題
しかし、1年ほど検討を進めていく中で、設備導入にかかる費用がもともとの予算を大幅に超えてしまう計画になっていました。その投資額に対して本当に期待している効果が得られるのか、疑問に感じていました。
そんな時Plant Simulationのことを知り、シミュレーションを行えば、設備導入による工数の削減や、生産量の増加など設備導入による費用対効果を事前に検証できると知り導入を決定しました。
3. 導入
まずは実際の図面をもとに、大まかな結果が見られるようなサンプルモデルを作成するところから開始しました。その後、導入を検討している設備の組み合わせや台数、レイアウトなどを変えて複数のシミュレーションモデルを作成し、それぞれの各設備の稼働率や一日の生産量を比較しました。
おおよそ三カ月程度で複数のシミュレーションモデルを作成し検討を行った結果、多額の投資をして設備導入を行っても目標としていた生産量に到達しないことが分かりました。
また、Plant Simulationを使用する前はExcel上で生産量の計算をしていたのですが、算出していた導入予定の設備の稼働率は80%を超えていたのに対し、Plant Simulationでは工程内のあらゆるところで予想以上にモノが滞留することが分かり、稼働率が著しく低くなってしまうという結果が出ました。Plant simulationは現実に近い状態で全体の流れをシミュレーションできるため、Excelでは計算しきれない細かい箇所の計算が可能になったのです。
その結果をもとに、大規模な設備導入計画を一度中断し、計画を再検討することになりました。
Plant Simulationを活用して設備の稼働率を検証
4. 結果
もともとは大規模な設備投資を行って生産量を向上させる計画でしたが、Plant Simulationで事前に検証したところ、期待する投資対効果が得られないということが分かりました。
中間在庫の滞留による設備稼働効率の低下に問題があり、作業スペースが有効活用されなかったり、管理などの非生産的な業務の増大など、生産能力に悪影響を与えるということもシミュレーションにより分かりました。
その結果を受け、まずは中間在庫の滞留をミニマイズできる最適な生産計画や生産ラインの検討をPlant Simulationを活用しながら実施していくこととなりました。
関連製品
もっと詳しく知りたい方はこちら!
動画
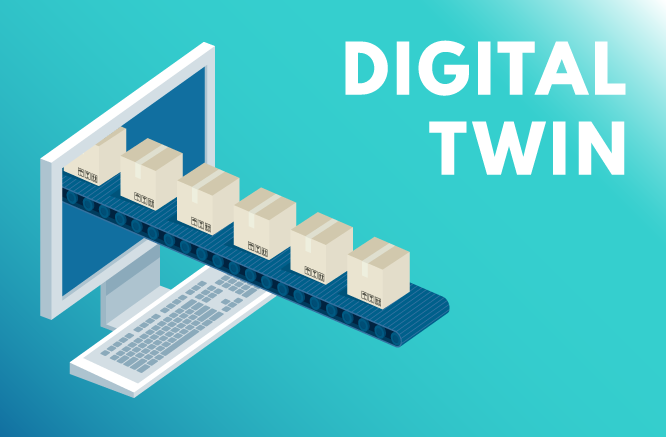
デジタルツイン紹介動画集
生産工程のデジタル化から始めよう!デジタルツインの基礎から各業界ごとの活用方法までを一挙ご紹介。※視聴にはお申し込みが必要です。
ホワイトペーパー
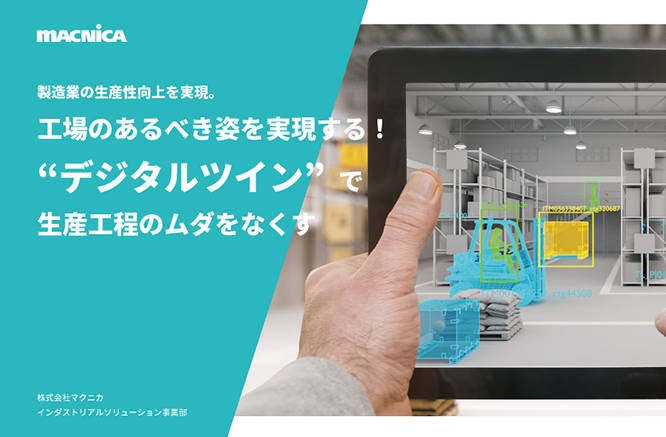
工場のあるべき姿を実現する!“デジタルツイン”で生産工程のムダをなくす
活用事例とともにデジタルツインの価値と導入の進め方をわかりやすく解説。※ダウンロードにはお申し込みが必要です。