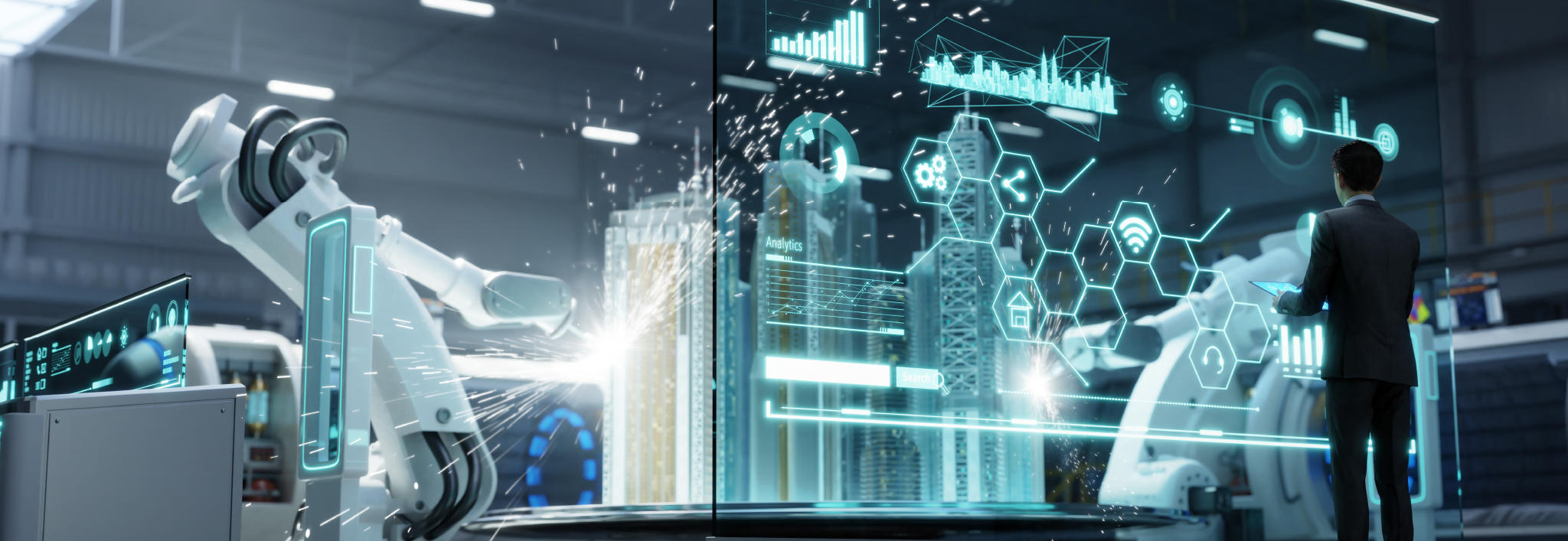
データ駆動型経営の実現に向けたCPS施策を加速
環境変化に対応可能な工場の工程づくりに役立つ「Plant Simulation」
──株式会社ソミック石川様
車の足回り部品として欠かせないボールジョイントを中心とした自動車部品メーカーである株式会社ソミック石川では、持続可能な経営基盤の確立と環境変化に柔軟に対応可能なデータ駆動型経営を目指し、サイバーフィジカルシステム(Cyber Physical Systems:CPS)への取り組みを加速しており、その一環としてスマートファクトリー化につながるシミュレーション環境としてPlant Simulationを導入しています。その経緯について伺いました。
本プロジェクトの参加メンバー
株式会社ソミック石川の方々
- 生技開発部CPS推進室 室長 鈴木 良則様
- 生技開発部CPS推進室 主務 磯部 充孝様
- 生技開発部CPS推進室 主任 小林 友紀様
- 生技開発部CPS推進室 飯田 雪月様
株式会社マクニカ
- デジタルインダストリー事業部技術部 部長 町田 悦一
- デジタルインダストリー事業部技術部第1課 課長 稲垣 智和
- デジタルインダストリー事業部プロフェッショナルサービス第2部第1課 鈴木 亜衣
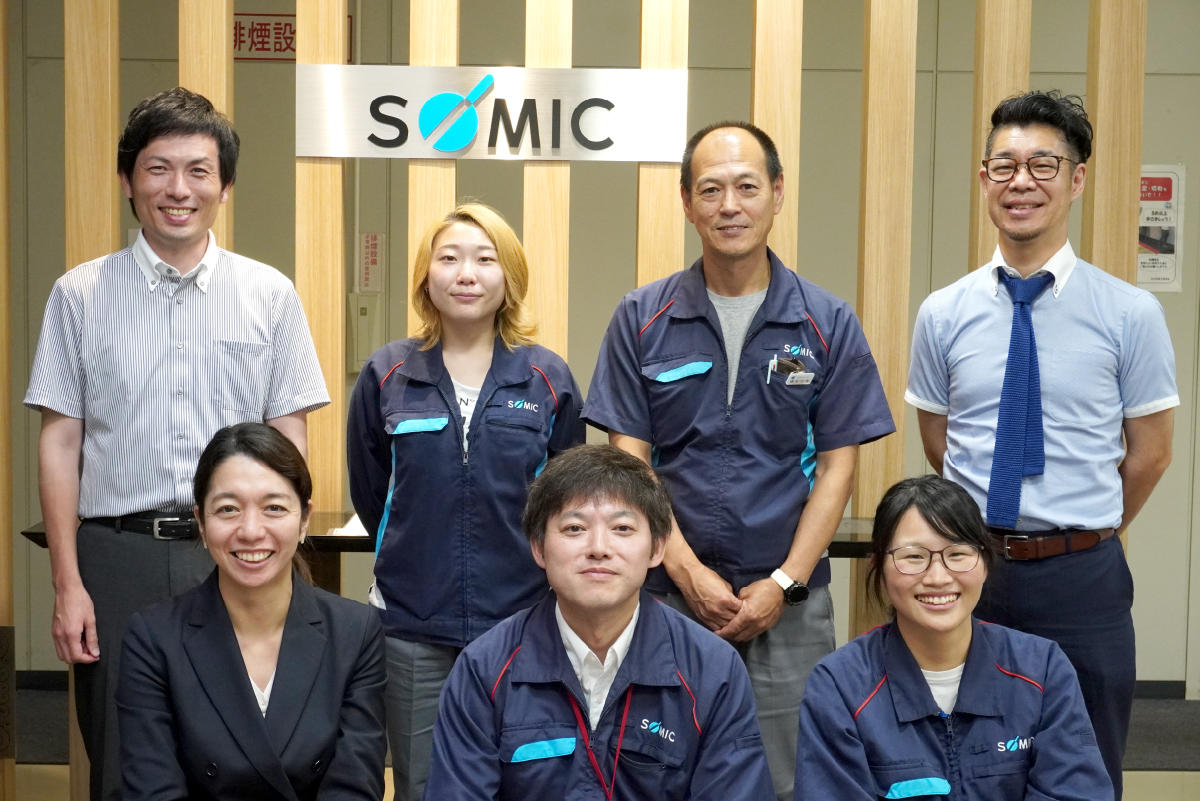
- 課題
-
- 3Dモデルでの再現性の高さが現場に必要
- 現場が活用するためのローコード仕様
- 習熟度を高めるための伴走支援が必須
- 目的
-
- 持続可能な経営基盤の確立
- データ駆動型経営を目指すためのCPS推進
- ツール活用でのDX人材の育成
- 効果
-
- 新たな工程プロセス検討や既存ラインの改善に貢献
- 生産シミュレーターによってDX人材の育成に貢献
- 社内外でのコミュニケーションツールとしても活躍
新たなプロジェクトのはじまり
社会の実験場として社会課題を解決していく企業
鈴木様:我々は、ソミックグループにおいて、ボールジョイントをはじめとした自動車部品の開発から設計、製造、販売までを手掛けている株式会社ソミック石川に所属しています。単なるモノづくりだけでなく、モノづくりを変革しながら自ら「社会の実験場」として社会課題を解決していき、地域社会に貢献していくために次世代社会としてのSOMIC SOCIETYを掲げています。世界規模で事業を展開しており、米国やフランス、中国など6か国に10工場を展開しており、ボールジョイントの国内シェア50%超、世界シェアでも20%ほどとなっています。
自動車業界は、カーボンニュートラルやEVへのシフトなどさまざまな課題があるものの、社会課題と複雑に関係していることが多く、持続可能な社会づくりに我々としても積極的に関わっています。大きな変革期にある社会だけに予測困難な時代ではありますが、既存事業の変革と新規事業の創出を実現することで持続可能な経営基盤の確立を進める必要があります。その1つのアプローチとして取り組んでいるのが、環境変化に柔軟に対応可能なデータ駆動型経営の実現であり、CPSに関する取り組みです。具体的にはAIによる外観検査をはじめ、簡単に電力などのエネルギー量の収集を可能にするIoTシステムの開発といった、カーボンニュートラル関連の取り組みがその代表的な施策の一例です。
生産シミュレーターが果たす役割とDX人材育成への取り組み
鈴木様:実際には、以前からスマートファクトリー化に向けたデジタル推進の一環として、IoTによる生産稼働状況の可視化を進めてきましたが、取得した情報を活用し、デジタル空間に工場そのものを作り上げるデジタルツイン実現に向けて、生産シミュレーターを活用しようという流れがありました。要は、生産シミュレーターにて生産数を予測し、工場というフィジカルな場の自動化や効率化に役立つ環境づくりを進めるプロジェクトです。そんなデジタル化に向けたさまざまな取り組みを融合させていくのが、我々が所属するCPS推進室が取り組んでいることです。
また、デジタルに長けたDX人材の育成については、本来的には人事部門の所掌範囲となるものの、導入したCPSの仕組みを現場で使いこなしていける人材配置は当然進めていく必要があります。当然社内だけでは人材を賄いきれない部分もあるため、外部の協力も視野に入れながら、社内でDX人材をどう育てていくべきなのか、人事部門と一緒に進めている側面もあります。CPSの活動そのものが社内のDXをリードしているという観点からも、人材育成につながっていくことになるのは間違いありません。
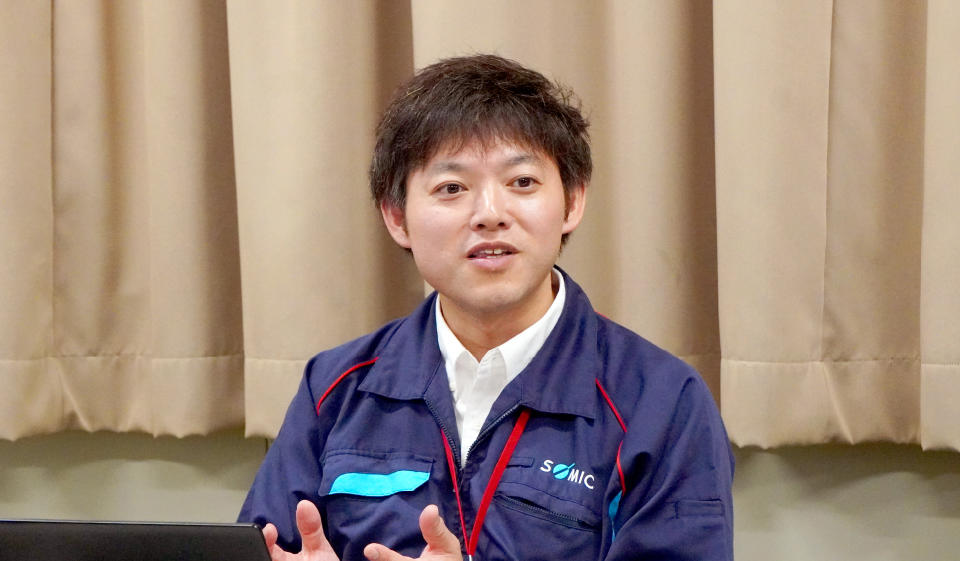
再現性の高さとローコード開発できる点を評価
以前から関心を持っていた生産シミュレーター、経営層からの後押しで実現
鈴木様:2025年にデータ駆動型経営を目指すという経営判断から、それをリードするCPSという位置づけでさまざまな取り組みを進めていますが、そもそも生産シミュレーター活用については、経営陣から具体的に言及される前から検討していた経緯があります。生産シミュレーターによって工場の生産効率や新たな設備投資に向けた試算が可能になるだけでなく、DX人材の育成にも貢献するため、いずれ現場で使っていけるような環境を整備したいと考えていました。かつては説明のためにPPTで壮大なアニメーションを作成したこともありますが、これを工場全体でやっていきたいという想いがありました。そんな生産シミュレーターについての想いを秘めていたところ、経営層から生産シミュレーターの話題が出たことで、うまく予算化していける段取りができたのです。
再現性の高い「Plant Simulation」
鈴木様:生産シミュレーター選びについては、大前提として3Dモデルでシミュレーションできることを大前提に考えており、その時点で大きく2つのソリューションに絞り込まれました。そこで注目したのが、マクニカが提供する「Plant Simulation」でした。特に製造業においてはインダストリー4.0と呼ばれる製造業の革新的な考え方がドイツから生まれたことからも、ドイツのメーカーで自らPLC含めたFAを進めているシーメンスが開発した「Plant Simulation」のほうが感覚的に進んでいる印象があり、工場をターゲットにしたモデルづくりを多く手掛けている点も評価しています。
磯部様:従来型のシミュレーションのモデルと使ってみると、どうしても現場からはピンとこないという感覚を持たれてしまいます。設備も多種多様にあるため、自動機1つをとっても、現状の工場に近い形で持っていけるような再現性の高い生産シミュレーターを期待していました。他のソリューションに比べて、詳細まで作り込みできる点から再現性の高さは「Plant Simulation」に分があった気がします。
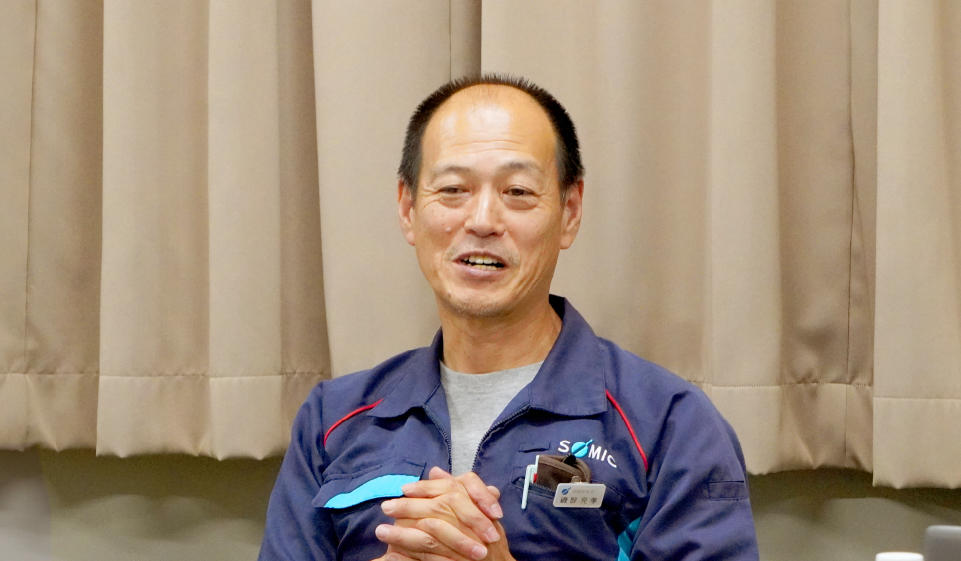
現場に使ってもらうために求めたローコード仕様
鈴木様:現場で利用できるようにするためには、できる限りコードを書かないローコード仕様の仕組みが必要でした。実際に検討した他のソリューションの場合、多少はコードを書く必要がありました。私自身は社内のAI開発にかかわっていたこともあり、Pythonも多少使えますが、多くのメンバーがコードを扱えるわけではありません。ある程度までコードに頼らずともモデルづくりが進められるのが「Plant Simulation」だったのです。
伴走型支援の内容が充実していたマクニカに軍配
鈴木様:「Plant Simulation」をイメージするには、マクニカがネット上で公開している動画もわかりやすく、「Plant Simulation」でのモデルづくりがITに詳しくないメンバーにも伝わりやすかった点が好評でした。周りに見せれば、具体的なモデルづくりが説明しやすいものとなっています。また、導入してすぐに使えるわけではなく、当然ながら習熟する期間が必要です。そのため、伴走いただけるサービスや教育機会の提供など、どこまで支援いただけるのかも検討しました。「Plant Simulation」を提供している他のインテグレーターとも比べた結果、マクニカが一番伴走型支援の内容が充実しており、コストパフォーマンスも優れていました。
「Plant Simulation」導入後の現在
将来構想に向けたプロセス検討や既存ラインの改善活動に役立てる
鈴木様:現在は、CPS推進室にて「Plant Simulation」の習熟を進めており、2ライセンスでモデルづくりを進めています。実際にトライアル期間を経て導入し、1年ほど伴走支援のサービスで「Plant Simulation」でのモデルづくりを通じて習熟度を高めてきました。具体的な使い方としては、今後主流になる若い工場に関しては、将来的な構想があるため、全体的な工場のプロセス検討に向けてモデルづくりを進めています。また、既存の生産ラインについての改善を進めるべく、さまざまなシミュレーションによって生産効率を高める検討を進めています。
小林様:既存ラインの改善に向けたモデルでは、自動化設備のデータを使ってモデルを作成し、働く作業者のシフトも加味しながら現場の動きを見ていくようなシミュレーションを行っています。IoTを駆使して必要なデータを取得するだけでなく、人の動きはカメラで動画を撮影して作業者の動きをデータとして投入しています。
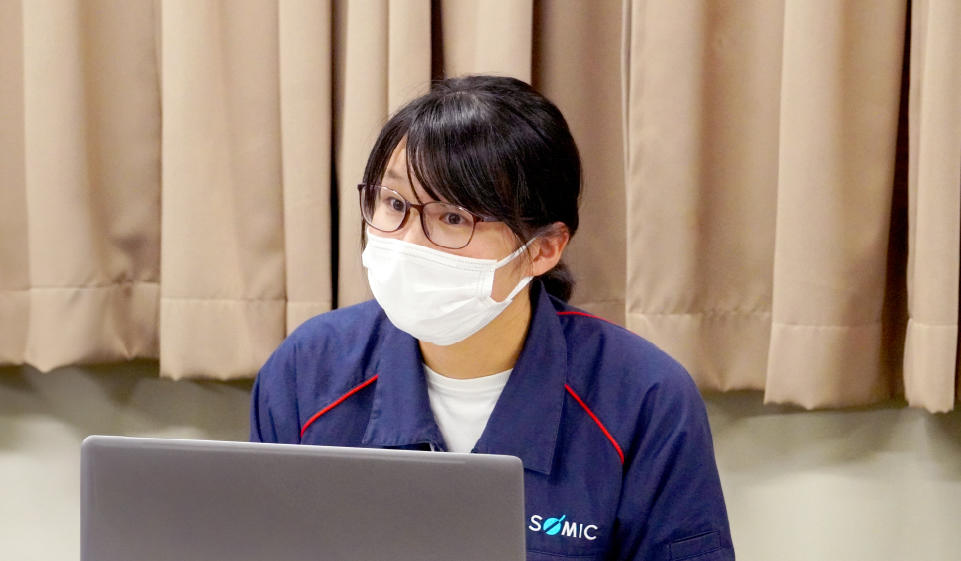
磯部様:設備の情報は3D CADのデータそのものだとデータサイズが大きいため、ある程度削って「Plant Simulation」に取り込んでいます。作業者の人数でどのような動きになるのかを見ながら、人が減った場合のシミュレーションなどを行っており、現場には実際に動きを見てもらうといった使い方です。仕掛量も変化しますので、現場から情報をいただきながらシミュレーションに活かしています。現場としては、最終的に人的リソースを最適な形に持っていきたいという想いがあります。
ITスキルよりもモノづくりの現場を知るメンバーを重視
鈴木様:生産シミュレーターに関してはモデルづくりもそうですが、そもそもどういったデータセットを用意するかが大変です。人の動きなどデータ化されていない部分は、現場に赴いてモノづくりの流れを見る必要があります。ITスキルを持った人は現場のモノづくりの流れを知らないので、どのデータを取得すればシミュレーションに活かせるのかがわかりません。一方で生産現場のメンバーは、ITのスキルがないのでどうやってシミュレーションに落としていけばいいのかがわかりません。この場合、モノづくりの現場を経験するほうがおそらく大変な労力が伴うため、シミュレーションに関してはIT系の人材よりは現場の人間を成長させていくアプローチを選択しています。
小林様:既存ラインにおけるモデル化は、伴走支援のサービスを経験したうえで、おそらく1か月ほどで作成できています。現在もモデルの改善は続けていますが、最初はIT用語が全く分からず、少しずつ自分で学習機会を作っていきました。プログラム自体はExcelに近い感覚があり、もともと表づくりなどが好きだったこともあり、何とか作っていくことができました。
もちろん、2週間に1回伴走支援のサービスを受けることができたことは大きかったです。その都度作りたいモデルについて相談して手伝ってもらいながら、不明点があれば適宜質問するような形で進めていくことができました。
飯田様:私自身は、最近新たに「Plant Simulation」を触り始めました。伴走支援の際にマクニカから提供された教育資料などをもとに、操作方法やプログラム作成の方法などを学んでおり、YouTubeで「Plant Simulation」のモデル作成の方法なども参考にしています。「Plant Simulation」にて用意されているサンプルや小林が伴走支援の時に作成したモデルを見て、自分なりに作っています。何かあれば小林のほうに聞きながら習熟度を高めています。
「Plant Simulation」がもたらした効能
改善活動はもちろん、社内外でのコミュニケーションツールとしても役立つ
鈴木様:実際にはこれから現場の改善に利用していきますが、すでに工場からはいくつかのシミュレーションに対する期待の声が寄せられており、改善に役立つ意味でも生産シミュレーターに対する関心は高い状況です。やはり従来と違って試行錯誤できる点で、いろいろな案が出てくることになるでしょう。また、これまでは4人を3人に減らした場合にどうなるかという検討が難しいところでしたが、シミュレーションできるようになったのは何よりです。
取引先である自動車メーカーの調達部門にシミュレーションのモデルを見てもらうと、改善プロセスなどを理解してもらいやすくなり、相手とビジョン共有できるようになったのは非常に大きいです。また、外部のパートナーにシミュレーションを見てもらうことで、我々がイメージしたラインが共有でき、システムのつなぎ込みなどシステムの改善などの意図が伝わりやすくなったという効果もあります。生産シミュレーターがコミュニケーションツールとして有効に機能しています。
データ駆動型経営に向けて生産シミュレーターがデータ活用を加速させる
磯部様:データ駆動型経営を目指すという方針に沿った形で、データを有効活用できるようになっています。現場では、ガントチャートなどで動きが見たいという声も挙がっており、オプションを利用するのかスクラッチで作りこむのか選択肢があるかと思いますが、もっと現場に分かりやすい形で提供できるとさらに活用の幅が広がると考えています。
小林様:事前のトライアルではゲーム感覚でいろいろお試しできましたし、伴走支援サービスでも具体的なモデルづくりの疑問に対する的確な回答でとてもお世話になりました。メールでの問い合わせもモデルのサンプルを作成してお送りいただくなど、参考になる情報を多くいただくなど、親身な対応に感謝しています。前職の工作機械メーカーでは、いろいろ試そうとすると本番の機械に影響が出てしまうため、なかなか自分のやってみたいことができませんでした。生産シミュレーターのおかげでいろいろお試しできるため、アイデアが広がる環境として理想的です。
飯田様:まだ経験が浅いものの、自分の作りたいものが形になるのは気持ちがいいし、とてもうれしく思います。分からないことも、ヘルプで検索するなど調べていける環境があることもありがたかったです。英語ながらYouTubeで「Plant Simulation」でモデルづくりしている人もいるなど、参考になる情報もあることはとても助かっています。データのインポートで困ったことがあったとき、マクニカに問い合わせをした際にはいくつか提案をいただき、無事に解決につながったこともあり、手厚い支援に感謝しています。
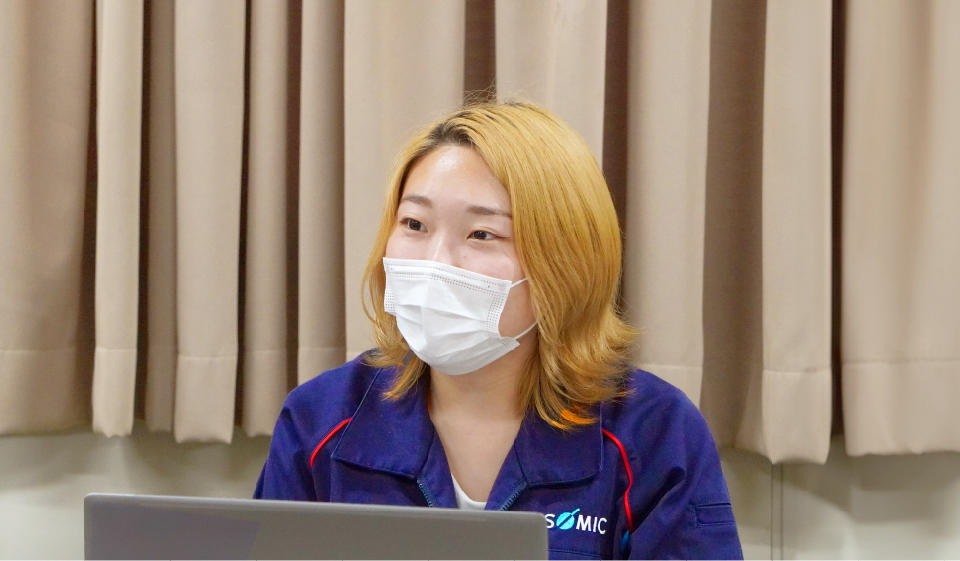
「Plant Simulation」で描く未来像
各工場への展開を進め、日常の業務プロセスのなかに組み込んでいく
鈴木様:現在はCPS推進室での利用ですが、いずれは各工場でそれぞれ改善活動に「Plant Simulation」が生かせる環境づくりを進めていきたいです。できれば、IoTで取得できるデータをリアルタイムで見ながら、次はこうなるだろうという未来予測につながるようなリアルタイムシミューレーションができれば理想的ですね。昨日の状況からシミュレーションで課題を抽出し、すぐに改善などの打ち手につなげていくような使い方ができればと考えています。
新たな工場で活用する場合は、どんな設備を導入してどんなラインを作っていくのかという生産準備の段階で「Plant Simulation」を活かしていくことを考えています。いずれにせよ、「Plant Simulation」を使える組織をどんどん増やし、日常の業務プロセスのなかにシステマチックに入っていけるような環境を作り上げていきたいと考えています。
「Plant Simulation」以外の領域でいえば、PLMをはじめ我々に足りていないシステムなどはマクニカと一緒に作っていけることは期待していますし、現場の困りごとをDXで変えていくような大きな話についても、いろいろ継続して相談していければと思っています。
海外拠点への展開も含め、現場の可視化をさらに加速させたい
磯部様:現場に使いやすい環境づくりへの改善はもちろんですが、現在は国内の工場に展開している「Plant Simulation」を、いずれは海外拠点にも展開しながら、活用のシーンを広げていかなければいけないと考えています。
欲を言えば、自社が取り扱う製品が全て「Plant Simulation」に取り込めれば、どこに仕掛かりがあるかや、現時点での生産量なども全て可視化できます。全てがデジタルに落とし込めれば、管理する面からも大きなメリットがあります。
小林様:現在のラインに合わせてモデルを構築していますが、現場の意見を常にヒアリングしながら、ニーズにマッチしたモデルを作り上げ、最終的な改善活動に活かしてもらえるようにしていきたいです。また、いずれは看板方式なども「Plant Simulation」を通じてモデル化し、最適なシミュレーションに活かしていきたいと思います。
飯田様:今は小林がモデルづくりをリードしていますが、少しでも「Plant Simulation」を扱えるようになって、今以上のモデルづくりができるように精進していきたいです。
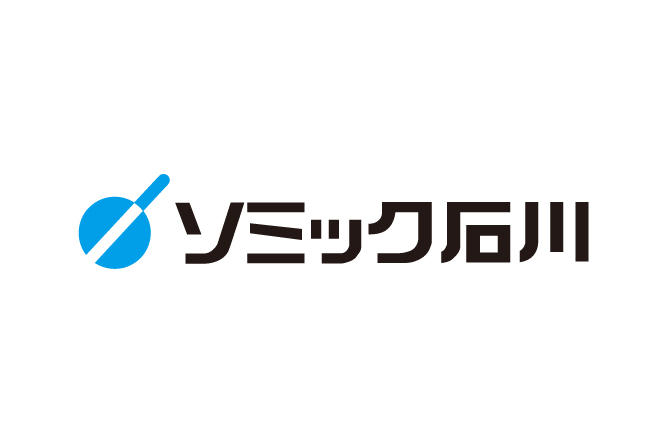
株式会社ソミック石川様
- 事業内容
- 自動車部品(ボールジョイント)の開発・設計・製造・販売
- 創立
- 1916年
- 従業員数
- 1,805名(2023年4月現在)
- ウェブサイト
- https://www.somic.co.jp/
PRODUCT/SERVICE
本事例の関連製品・サービスはこちらから
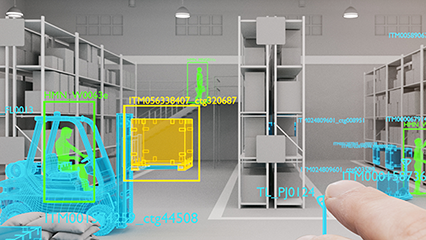
シーメンス Plant Simulation 「Tecnomatix」
Digital Twin 生産シミュレーションソフトウェア
CONTACT
本事例、製品の導入に関するご相談など、お気軽にお問合せください。