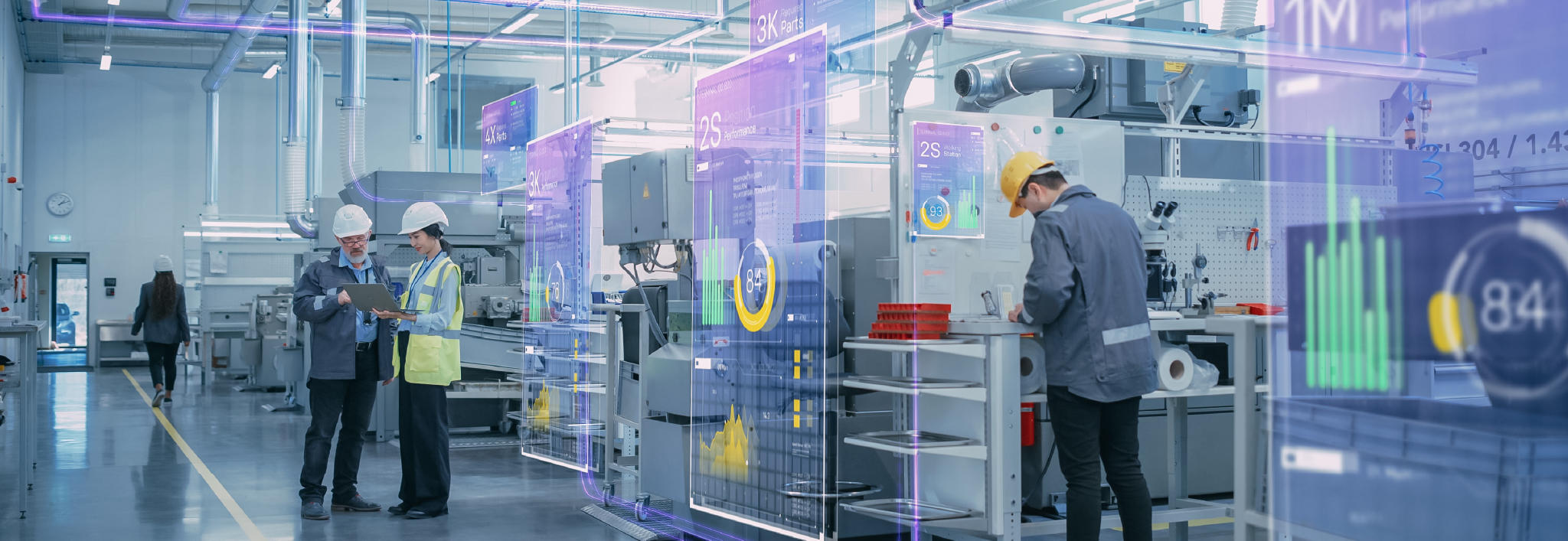
内製の力で現場の可視化がさらに加速!
製造現場の監視&実績分析を実現する「DSF Cyclone」
──DIC株式会社様
基礎素材である有機顔料と合成樹脂をベースに、パッケージング&グラフィック、カラー&ディスプレイ、ファンクショナルプロダクツの3つの事業部門を展開しているDIC株式会社では、現在全社的にDXを推進しています。そうした取り組みの中で館林工場では、現場データの可視化による遠隔監視および実績分析の仕組みづくりやデジタル人材の育成に向けた環境整備に、マクニカの「DSF Cyclone」を活用しています。その経緯について伺いました。
本プロジェクトの参加メンバー
DIC株式会社の方々
- 生産技術部生産技術開発グループ製造3グループ駐在 マネージャー 吉井 貴則様
- 生産技術部生産技術開発グループ 入倉 幸一様
- 館林工場製造グループ マネージャー 中村 真弓様
- 館林工場製造グループ機能性コンパウンド製造課 湯川 大輝様
- 館林工場の皆さま
株式会社マクニカ
- デジタルインダストリー事業部技術部第3課 櫻 俊介
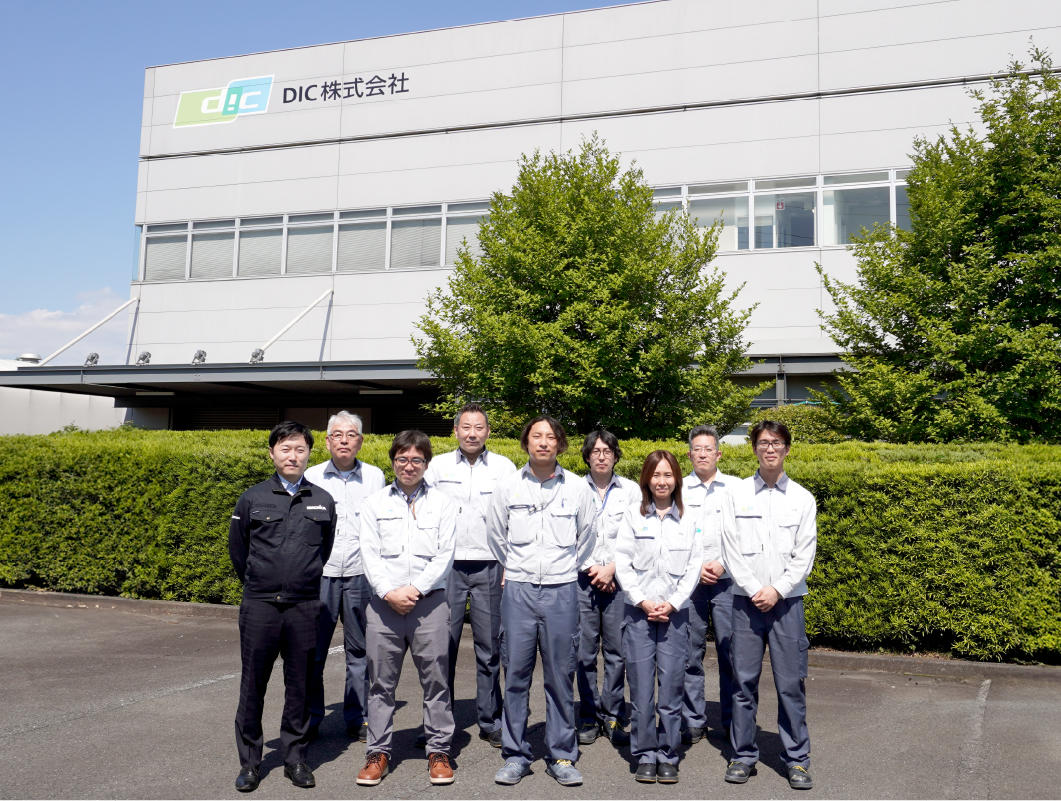
- 課題
-
- 状況確認のために作業員が何度も現場を訪問
- 時間を要する過去データの扱い
- 要件変更ごとにコストがかかる可視化システム
- 目的
-
- 設備の稼働状況を遠隔監視できる環境整備
- 限られた人的リソースでの内製化
- 取得データの利活用促進
- 効果
-
- 専用画面作成による状況確認の効率化
- データ収集でトラブル原因を明確に
- 原料補充タイミング予測などで事前計画を実現
新たなプロジェクトのはじまり
中村様:印刷インキの製造と販売で創業し、世界62の国と地域に180社を超えるグループ会社を展開しています。印刷インキ、有機顔料、PPSコンパウンドで世界トップシェアを誇っており、基礎素材である有機顔料、合成樹脂をベースとして事業領域を拡大中です。さらに現在は包装用接着剤や多層フィルムなどのパッケージ材料、ディスプレイ用顔料、化粧品用顔料、半導体・モビリティ分野向け高機能樹脂製品、工業用テープ、中空糸膜モジュール、ヘルスケア食品などさまざまな分野に事業を展開しています。
1993年に操業を開始した館林工場では、樹脂着色剤事業のマザープラントとして、主に樹脂を混錬・賦形する設備を使い、生産を行っています。現在では機能性コンパウンドと呼ばれる、樹脂に高付加価値な機能を持たせる素材を中心にモノづくりを行っています。
DXの足がかりとして作業効率の向上に資する遠隔監視の仕組みを模索
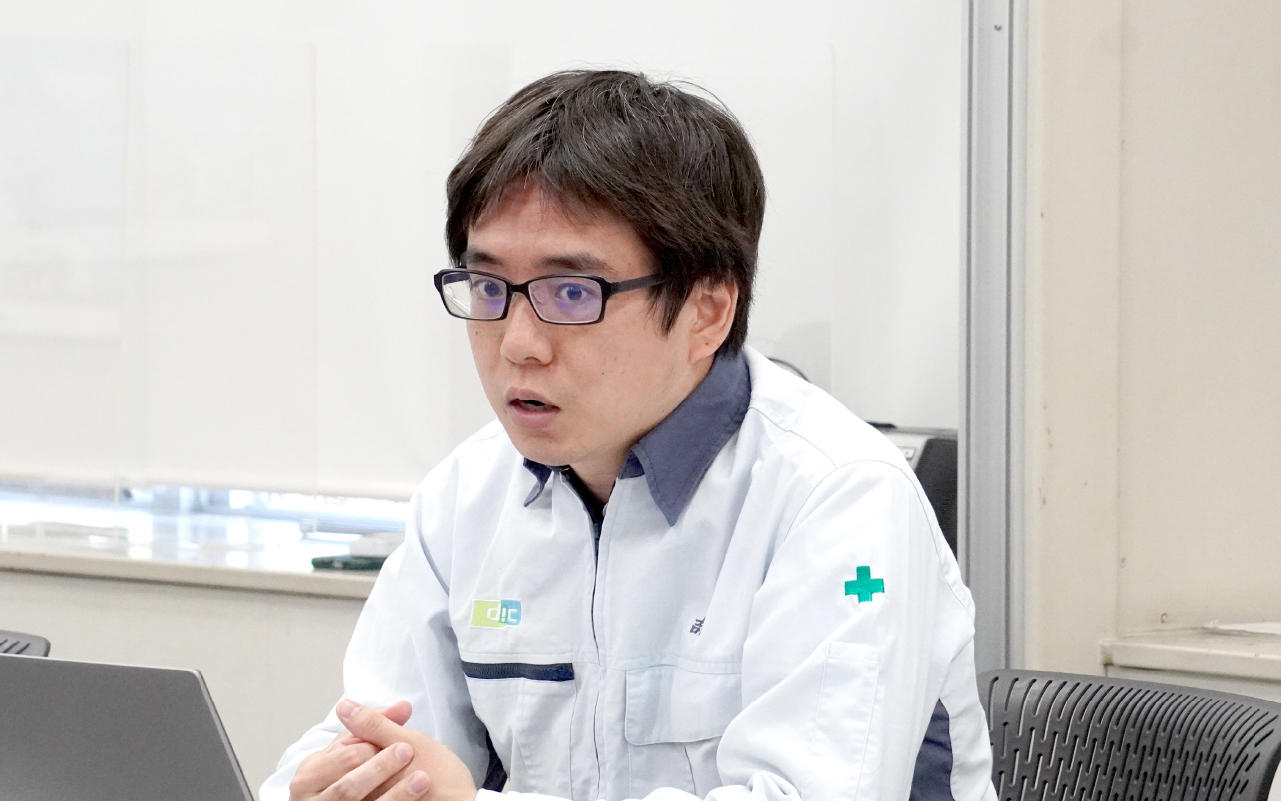
吉井様:もともと全社的なDX推進は2019年ごろから始まっていますが、2017年ごろから館林工場では生産部門を中心にデジタル化を進めており、スマート工場化に向けてさまざまな取り組みを進めてきました。老朽化への対処や継続的なメンテナンスが必要な生産設備を維持・継続していくなかで、全社的にはデータ活用につながるログ収集基盤の整備が求められたのです。実際には本格的なDX化が始まる前からログ収集の基盤をスポット的に導入していましたが、将来を見据えたこれからの時代に必要な環境づくりの一環として、改めて見直していこうという機運が高まっていました。
中村様:デジタル化の推進によって少しでも作業効率を高めていこうという動きは、以前から現場改善を進めていくための施策の延長として進めてきた経緯があります。特に館林工場は、大きく4つに現場が分かれており、各現場でログを収集して設備状態の可視化や履歴確認などに役立てていました。
今回の新たな取り組みでは、設備の稼働状況やトレンド情報を遠隔監視できる環境を整備し、その場に駆けつけなくともスマートフォンなどから迅速に状況把握できる環境づくりを目指しました。過去のログ収集基盤では、確かにデータは取得可能ですが、機側以外で可視化する仕組みとはなっていなかったため、今回の目的に合致した新たな環境整備を進めることにしたのです。
構造上現場に階段を使って駆けつけざるを得ない、ロスも発生しやすい
吉井様:遠隔監視が可能な仕組みが構築できれば、設備からアラートが発せられた際にもその都度現場に赴かなくとも状況が把握できますし、早期に設備状況が判断できれば対処も迅速になり、結果として生産効率が向上します。ちょうど同じメンバーで従来よりも広範囲な現場を担当せざるを得なくなるといった業務範囲の変更の影響で、現場に人を派遣して状況を把握するというアプローチから脱却する必要もあったのです。
湯川様:今回ターゲットとなったラインは、4階建ての建屋の複数フロアにまたがって工程が作られていますが、設備の状態確認や異常解消の際は階段で現地へ出向き対応しています。また、現場メンバーは各自それぞれの場所で作業していることが多く、対応タイミングをメンバー間で把握しあうことも困難なため、同じ対応目的で別メンバーと現地で出くわすなどの無駄な移動が発生していました。さらに、どこの設備からアラートが発生しているかを一度現場管理室へ出向き、確認してからでないと対象設備と状態の把握が出来なかったため、作業場所から直接現地へ移動できない非効率な状況となっていました。
吉井様:大きくは設備系メーカーのソリューションと、ITベンダーやSIerが出しているソリューションを中心に比較検討しました。我々の他工場でやり取りした実績があり、そこでぜひお話を伺ってみようというのが、マクニカを知ったきっかけでした。
今回の目的は遠隔監視ではありますが、当然取得したデータの利活用を促進させたいという想いがありました。そのあたりも含めていろいろな経験や知見を有しており、データ連携も含めて実績を持つマクニカに注目したのです。以前のログ収集については、設備系メーカーが提供している仕組みで、データは取れるものの利活用についてはあまり経験がありませんでした。設備系のメーカーにお願いしてしまうと、発展させていくための対応が難しいのではというのも、判断のポイントです。
また、あまり複雑なものだと現場の運用が回りません。「DSF Cyclone」に関しては、当初データ取得の部分は構築してもらったうえで、「MotionBoard」という汎用的なソリューションでデータ活用できるという構成を高く評価しました。
選ばれた「DSF Cyclone」とマクニカ
必ず出てくる変更要求、望んだ内製化
吉井様:現場が4箇所あり、トータルで20以上のラインが稼働しているため、全てのラインを一気に遠隔監視の対象に含めるわけにはいかず、まずはテストラインを定めたうえで、他のラインに展開していく想定で考えました。そのため、都度外部にお願いして展開するのではなく、できるだけライン拡張を内製化できるような仕組みを念頭にシステム設計を実施しました。項目を追加したい、画面を変更したいという要望は必ず出てくることが想定されていたので、自分たちで修正できるものが望まれていました。実は以前導入した可視化の仕組みは、完全に外部に開発をお願いして運用していましたが、やはり現場の要望で変更するたびにコストが発生してしまっていました。人的リソースが限られるなかでも、自分たちで内製化できるものを見据えてシステムを選ぼうと考えたのです。
中村様:実際にはいくつかの企業を比較検討させていただきましたが、プロジェクトメンバーそれぞれがIT領域に精通したメンバーではないため、しっかり提案およびサポートいただけること、そして一緒に作りこんでいただけるような伴走支援が可能かどうかは重視しました。単なる物売りでは困るので、将来的な内製化も含めてスキルトランスファーいただけるかどうかが大きなポイントでした。
データ活用の負担を可能な限り減らす仕組みを希望
入倉様:私自身は入社したばかりで、工場のことがまだ十分に理解できていない状況でした。ただ、当時はいくつかの現場でCSVを取得して日付と突合しながらつなぎ合わせるといった作業が行われており、過去のデータを使う際には非常に手間がかかっていました。グラフを作るにも時間がかかり、データが満足いく形で使える状態ではありませんでした。そのため、プロジェクトに入った段階で少しでもデータが簡単に扱えるようにしたいという想いがあり、使いやすさはもちろん、データが扱い易いソリューションを期待していました。
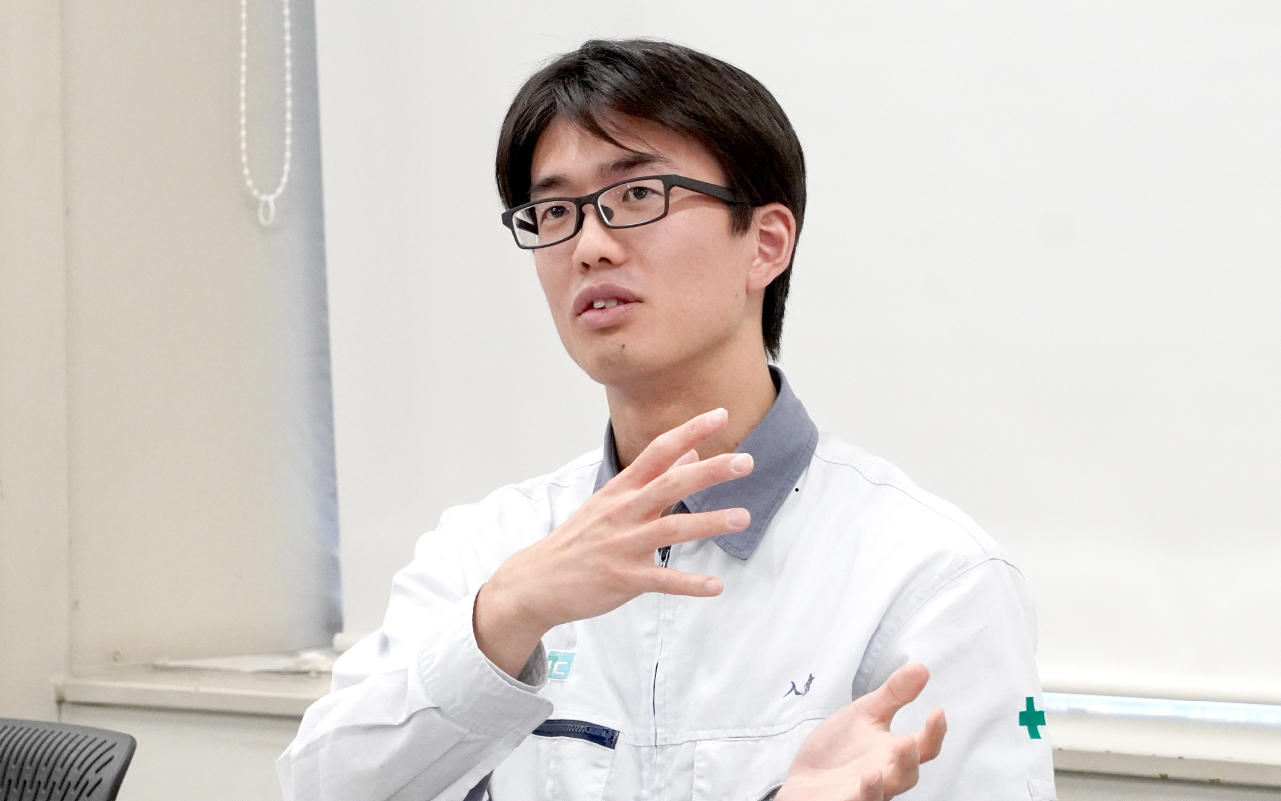
可視化の進む現在の運用
2つのラインに「DSF Cyclone」を展開、現場の可視化を実現
湯川様:今回は、「DSF Cyclone」を1機目のラインに導入したうえで、そこから拡張してもう1つのラインに展開しています。厳密には違いがありますが、ほぼ同じ機械からそれぞれのラインでデータを取得しています。ただし、ラインによって欲しい情報が異なることから、2機目のラインはガラッと内容が変わっています。1機目のラインは至ってシンプルですが、2機目は構造がかなり複雑で、取得するチェックポイントが多くありました。
押出機そのものからとれる情報が違うだけでなく、樹脂の種類や配合品それぞれのラインで異なっており、温度や圧力の情報もそれぞれ欲しいものが異なっています。当然取得する場所も異なってくるため、データ取得の数だけでも、1機目のラインが200ほどで、2機目のラインがその倍近くの情報を取得しています。5秒に1回データ更新を行っているので、ほぼリアルタイムな状況把握が可能です。
入倉様:具体的には、樹脂や顔料などの原料が蓄えられたタンクにどの程度の原料が残されているのか、そして原料タンクや計量器、押出機、充填梱包など各装置においてどんなエラーが出たのかといった情報を把握することです。原料タンクの中身が減れば補充する必要がありますが、以前は設備の近くまでいって画面を確認するなど、現場を何度も訪れる必要がありました。今はスマートフォンで原料タンクの状況を可視化したことで、どこにいても補充すべきタイミングが適切に判断できるようになっています。
アラームが鳴れば1階に駆けつけることでおおよその状況が把握できますが、確認後に各階の現場に向かうといった動きが発生します。スマートフォンによる可視化は、どこにトラブルがあるのかをその場で確認し、直接必要な階に出向いて確認できるというメリットも生み出しました。
「DSF Cyclone」で用意しているダッシュボードは、機械の運転停止などの状況が分かる設備の稼働状態とともに、温度や圧力などのトレンドグラフ、アラート情報に基づいたトラブル一覧画面などがあります。
スマートフォンで現場の状況把握が可能に
湯川様:私のほうは、「MotionBoard」を活用してスマートフォンで分かりやすく状況把握できる画面を最優先に作りました。3交代制の現場で、システム専用スマートフォンで何かあれば確認できるようになっています。今は必要な環境があれば誰でも稼働状況が把握できますが、結局複数のメンバーが現場に向かってしまうケースもあるので、いずれは誰が行くのかの登録をダッシュボード画面から実施できるようにしたいです。現状は誰が行くのかを事前に決めて運用しています。
入倉様:設備から取得できない生産計画などの情報はCSVで投入することもありますが、ラインの設備が止まった場合は自動的に記録されます。場合によっては原因の登録を「DSF Cyclone」に直接行い、日時やロットで検索してトラブル発生時のデータにさかのぼって確認することもあります。データを収集しておくことで原因が明確になり、改善につなげていくといったことにも役立っています。
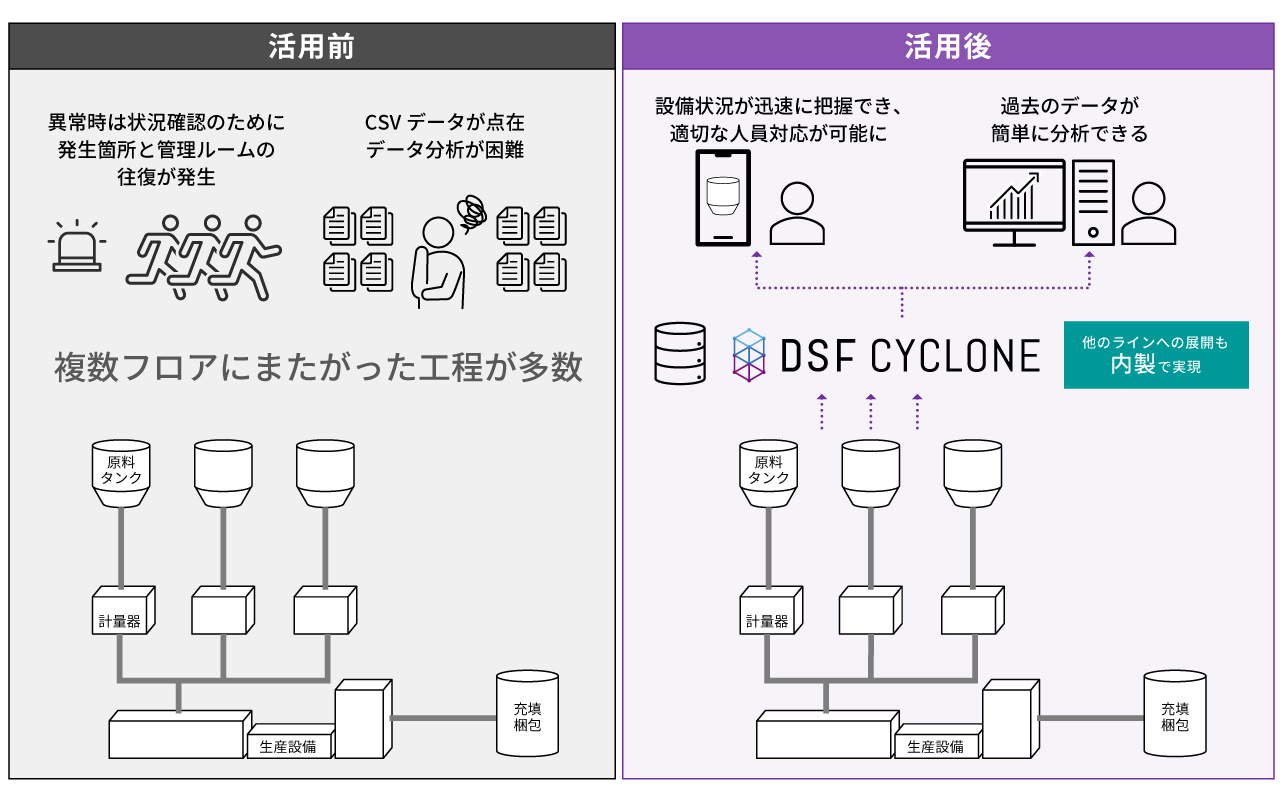
「DSF Cyclone」導入による効能
中村様:我々のなかでは、改善したものを定量的に評価して金額換算する合理化予算というものを持っており、この情報も「DSF Cyclone」に実績として入れています。また、月々実施されている改善活動報告会を工場全体で開催していますが、平均時給をベースに時間的ロスの削減がどの程度進んだのかを湯川のチームから報告を受けています。
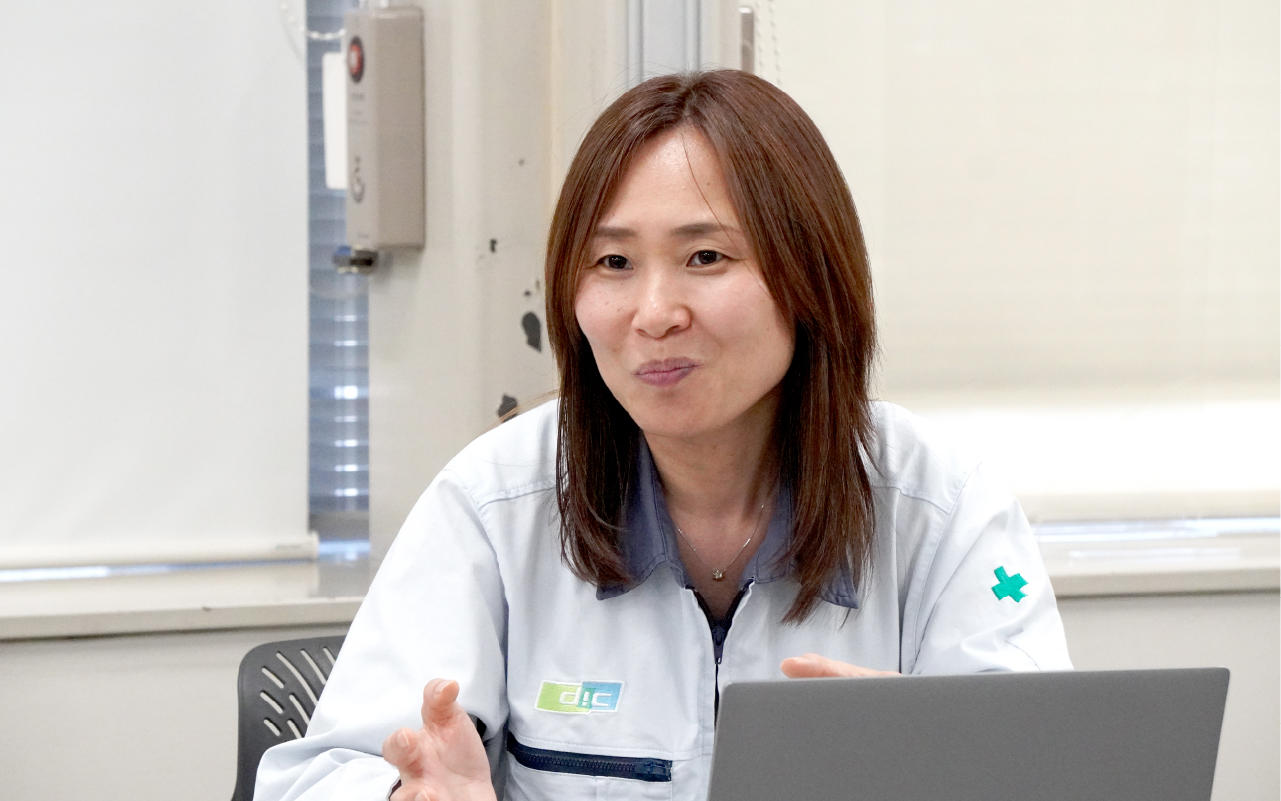
湯川様:計算ベースですが、「DSF Cyclone」によって現場が可視化できるようになったことで、機械がフル稼働した場合に削減できる時間は1日あたり260分という試算が出てきています。とにかく現場を確認しに行く手間を大きく削減できることは間違いありません。特に原料の補充など仕込む時間が予測できるようになり、仕事の計画がきちんと事前にたてられるようになったことは大きいですね。
内製化によってデジタルに明るいDX人材の育成に貢献
中村様:「DSF Cyclone」を内製化して運用できるようにしたことで、デジタルに明るいDX人材を社内で育てることには間違いなく貢献していると考えています。全社的にDX人材の姿を明確に定義しているわけではなく、それぞれの拠点や工場であるべき姿を考えながら取り組んでいますが、少なくとも館林工場においては、今回の施策で「DSF Cyclone」を活用したことで人材育成に寄与している部分はあります。
入倉様:当初から念頭に置いていた内製化によって、現場の可視化が実現できたのは「DSF Cyclone」があったからこそですし、その点を高く評価しています。当然、可視化は現場がどう見たいのかが重要になってくるため、私自身が獲得できた知見を活かしてもらいながら、現場主導で進めていただくことができました。
初めての環境整備、構築の苦労も
入倉様:今回はデータ収集とBIツールによる可視化がその中心ですが、データ収集については初めての経験で正直簡単ではありませんでした。たくさんデータを取得しようとすればその分作業量は増えますし、取得し過ぎても整理できなくなってしまうなど、いろいろ苦労した部分もあります。ただ、その都度マクニカに教えを乞うことで、何とか作り上げることができました。
プログラミングの知識がなくとも、ここまでのものができるのは、ツールとしての「DSF Cyclone」とマクニカの支援があったからこそです。ライン追加の際には、データベースを直接触れずとも「DSF Cyclone」のGUI上で実施できますし、IDSを触ることで新たなデータ取得も内製化できます。
湯川様:私は可視化のツールとしての「MotionBoard」を中心に触っていました。そもそもはExcel程度しか触ることができない人間ですが、それでも何となく触れながら作っていくことができたという印象です。入倉が1機目のラインの時にしっかり作りこんだ経験があったため、その知見を参考にさせていただきながら、うまく可視化していくことができました。
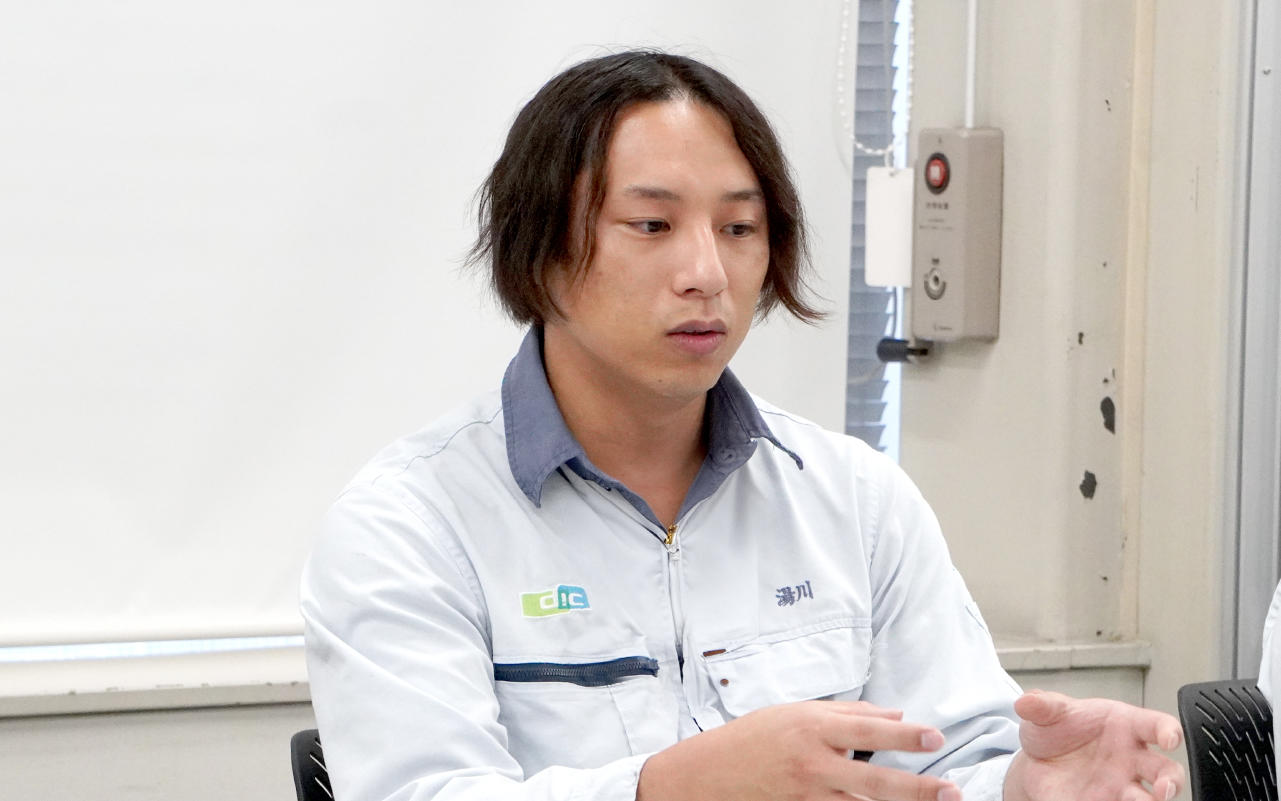
2週間の手厚い支援で内製化に向けて弾みをつける
入倉様:2機目のラインへ展開する前に、1機目のテストラインで一部仕様変更が発生し、IDSの変更を実施する必要がありました。その際に、仕様変更の手順について教わったり、スケジュール管理をしてもらったりとマクニカには2週間ほど手厚く支援いただけました。1機目のラインはマクニカにお願いしていたこともあり、実は「DSF Cyclone」が習熟できていたというわけではありませんでした。かなりスパルタでしたが、この2週間があったからこそ、自分でしっかり触れるようになったと感謝しています。
湯川様:可視化の領域で使う「MotionBoard」については、いったん触れたものの、かなり自由度が高いこともあって、なかなか思うようなものが作れませんでした。ただ、汎用的なツールだけにYouTubeなどにも多くの動画が投稿されており、自分で調べながらベンダーの講習会に参加して学びを深めていくことで、思ったものが作成できました。
これからの展開
DX人材としての知見を業務に生かしていきたい
中村様:今回のプロジェクトは、導入ツールの実使用においては、普段の業務に忙しい現場からすればとても負担が大きかったと思っています。それでも現場内で議論を重ねながらデジタル技術を駆使した可視化を実現することができ、プロジェクトメンバーと現場メンバーには大変感謝しています。今後については、工場の将来性も含めて考えていく必要があり、現在のところは未知数です。状況は不確定ですが、いずれ推進における目的を改めて考えつつ、これからも工場の効率化や生産性向上につながる活動を積極的に展開していきたいですね。
吉井様:本システムを他工場においても展開することができれば、獲得したスキルや知見を更に活かすことができるはずです。目的の設定やシステムの統一、そしてリソースの各本土をしっかり計画的に進めていければ、もっと広がっていく可能性を秘めています。
入倉様:内製化で「DSF Cyclone」はもちろん、設備の中身もいろいろ触ることで、システムの導入や運用はなんとなくイメージできたところです。「DSF Cyclone」に限らず、今後自分がDXのような領域に関わる場面では今回の経験が活かせるはずです。
湯川様:製造現場の人間として関わることができたのは、貴重な経験であることは間違いありません。今後もDX推進に関われるかどうかわかりませんが、自身のスキルアップにつながったことも含めて、貢献できることがあればお手伝いしていきたいですね。
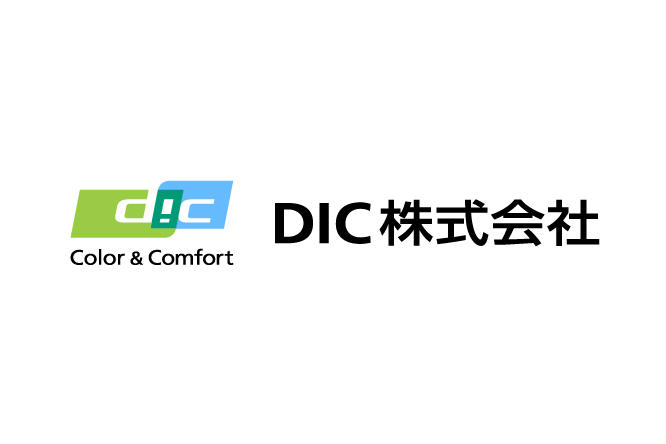
DIC株式会社様
- 事業内容
- 印刷インキ、有機顔料、合成樹脂等の製造・販売
- 創立
- 1908年
- 従業員数
- 連結 22,255名 単体 3,973名 (2023年12月31日現在)
- ウェブサイト
- https://www.dic-global.com/ja/
PRODUCT/SERVICE
本事例の関連製品・サービスはこちらから
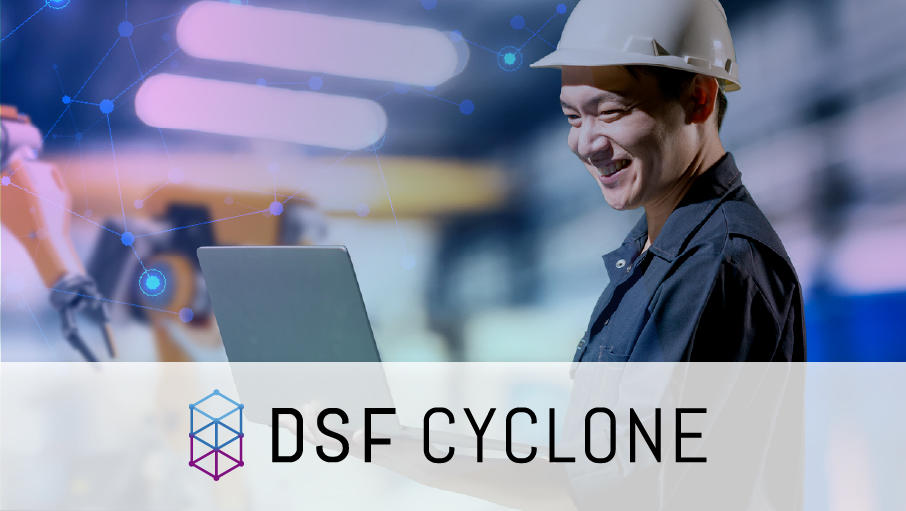
生産効率向上 × 現場起点の製造DX 「DSF Cyclone」
製造実績と生産計画を構造化されたデータでつなぎ「生産性の高い工場」を実現するサービスソリューション
DOCUMENT
本事例を読んだ方におすすめの資料はこちら
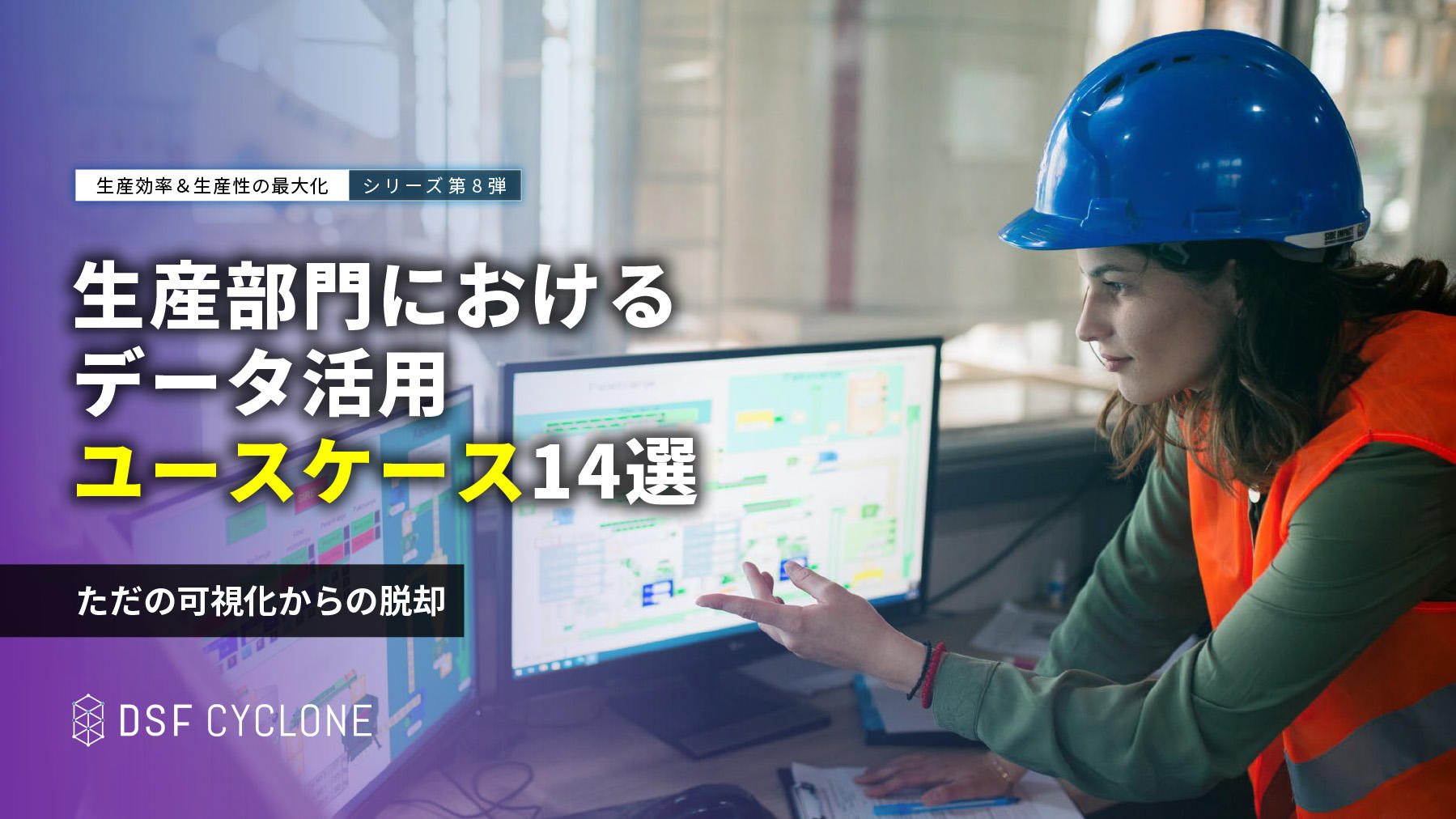
生産部門におけるデータ活用ユースケース14選
ただの可視化からの脱却
製造現場におけるデータ活用のフレームワークとユースケースをご紹介します。
※ダウンロードにはお申し込みが必要です。
CONTACT
本事例、製品の導入に関するご相談など、お気軽にお問合せください。