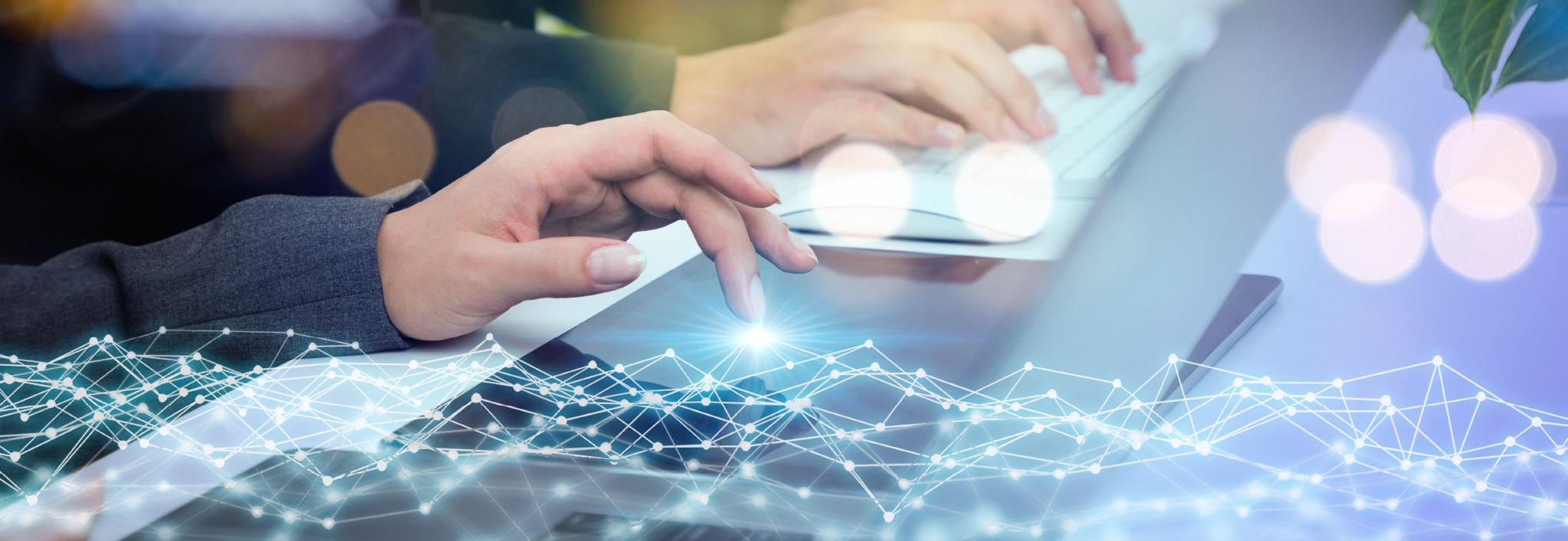
自動車部品業界の劇的な環境変化を生産シミュレーションで支援
現場改善と新たな工程設計の品質向上に貢献する「Plant Simulation」
──田中精密工業株式会社様
自動車エンジンのコア部品を手掛けている田中精密工業株式会社では、EV化の急激な変化のなかで、従来得意としてきた精密加工による製造プロセスとは異なる、新たな環境づくりへの取り組みを加速させています。そのための工程設計や既存ラインの改善に欠かせない仕組みとして導入したのが、製造工程に関するあらゆることをデジタル上に再現して検証できる生産シミュレーションソフトウェア「Plant Simulation」です。その経緯について詳しく伺いました。
本プロジェクトの参加メンバー
田中精密工業株式会社の方々
- 部品製造事業部 営業技術部 部長 高井 正樹様
- 業務プロセス改革部 DX推進課 DX推進係 横川 良太様
- 株式会社タナカエンジニアリング 設備設計課 課長 久世 健二様
株式会社マクニカ
- デジタルインダストリー事業部プロフェッショナルサービス第2部第1課 鈴木亜衣
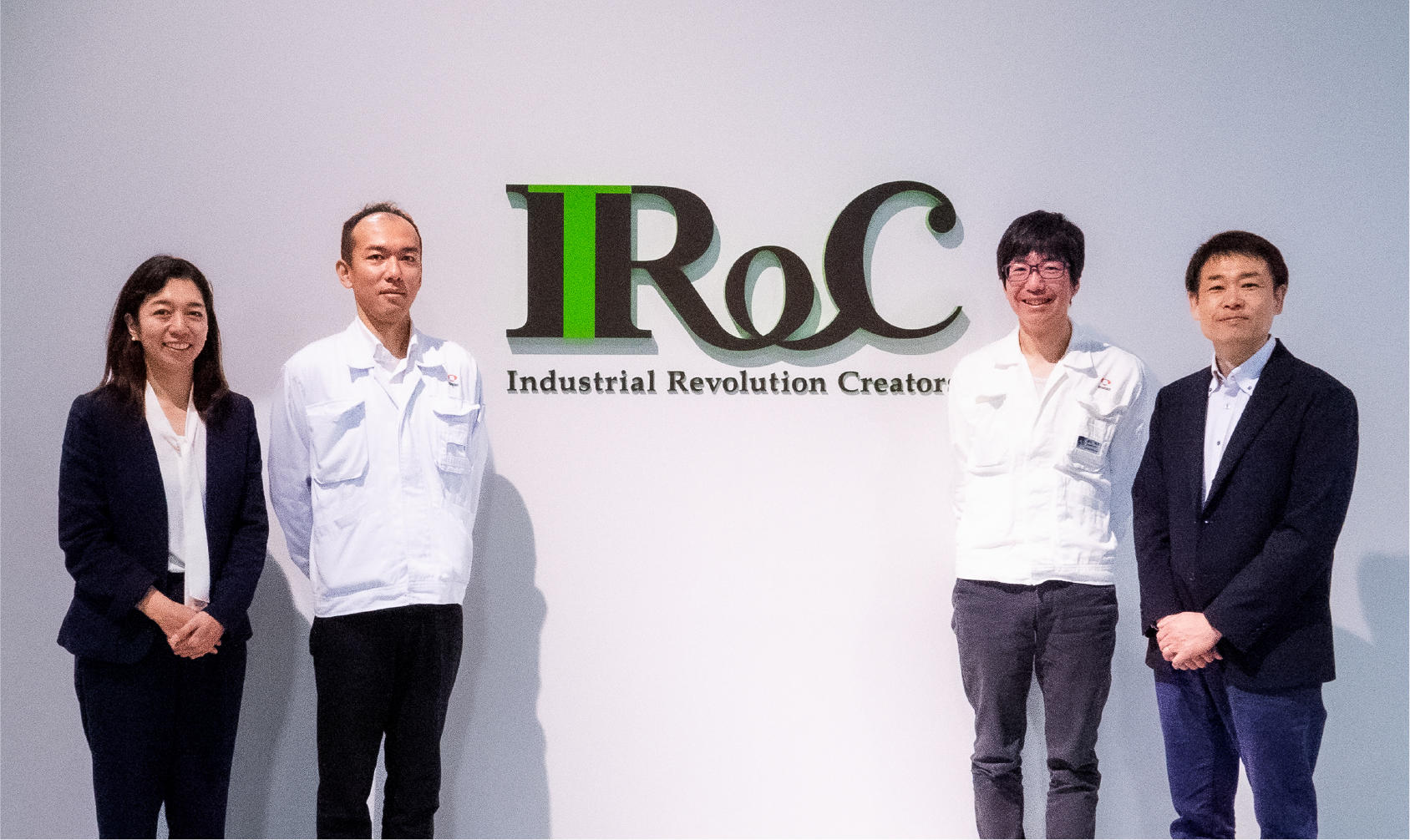
- 課題
-
- EV化による製品需要変化に伴う製造プロセスの大幅な改革
- Excelシミュレーションによる試行錯誤の限界
- 複雑な一貫製造プロセスによる計算困難
- 目的
-
- 工程設計と現場改善のシミュレーション支援
- 製造プロセスの見える化と最適化
- シミュレーションを内製化し自由度を確保
- 効果
-
- 数値評価の容易化と効率的な検証
- 動的評価による生産プロセスの効率向上
- 競争力向上と現場改善の迅速化
シミュレーション環境が必要だった背景
自動車部品業界の環境変化に製造工程の変革が必要に
高井様:私たちはシリンダーヘッド内に取り付けるロッカーアームという、ガソリンエンジンの心臓部に当たる部品を手掛けている自動車部品メーカーです。高精度かつ高性能な製品を造る高い技術力とともに、塑形加工から施削・切削、熱処理、仕上、部品組立・検査までの一貫加工体制が大きな強みとなっており、大手自動車メーカーを中心とした顧客から厚い支持をいただいています。現在は、2030年ビジョンとして「Change the future」を掲げており、これまで培ってきた技術力と創造力を駆使し、航空宇宙産業への参入からモーター製造技術の提供、工場自動化装置の開発など、さまざまな領域に事業を展開しています。
昨今は市場の変化に伴って、内燃機関用部品からHEVやBEV部品への移行が求められており、中期経営計画のなかでもEV系の部品に切り替えていくことが基本方針として掲げられています。もともとは手のひらサイズの精密加工を得意としており、高精度で小さな部品を大量生産するケースが多かったのですが、EV系の部品は大型の部品が多く、運搬容器1箱に数百の部品が詰まっているようなものとは違い、極端に言えば1つの箱に1部品というサイズのものもあります。部品の運搬方法や保管、製造工程やロットの考え方など、これまで我々が手掛けてきたモノづくりとは大きく違うアプローチが求められています。
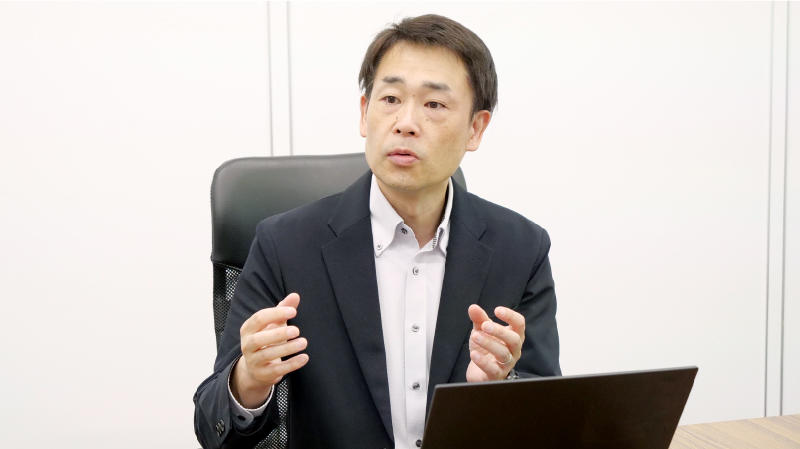
課題
Excelでの計算に限界、一貫した生産プロセスを持つが故の課題
横川様:市場の変化に対応すべく、我々としてもExcelなどを駆使してシミュレーションなど粗いながらも計算できることはいろいろトライしてきましたが、さすがにやり切れない部分もありました。Excelでのシミュレーションは途方もない工数がかかり、できたとしても数パターンのシミュレーションが限界で、設備の場所や作業動線等を変更したらどうなるかといった試行錯誤が難しい状況でした。しかも、モノが動くなかで保管スペースがどう変化するのかといった許容量の動的な検証は、ExcelやCADでは正直難しいのが現実です。
久世様:我々は素材の調達から組み立て加工までを全て自社で行っているため、完成までの工程が多岐にわたっています。そのため、変数が非常に多く、計算自体も想像以上に複雑です。例えば組み立てだけを行う企業であれば、Excelでも何とかやりようがありますが、我々にとっては道のりが長い作業が発生してしまいます。EV系の商材への転換を考えた場合、モノづくりの現場としての課題が顕在化していたのです。
「Plant Simulation」選択の理由
工場を丸ごと最適化するためのシミュレーションを実現したい
高井様:生産シミュレーター導入のきっかけは、現場において課題が顕在化していたことだけでなく、社長からのトップダウンでした。ある動画から有効なソリューションであることを知り、我々に対して検討しているかどうかの確認があったのです。我々としても製造プロセスの見える化や新たな工程設置に向けてシミュレーションできる環境を求めていたこともあり、すぐに検討することにしました。
久世様:実は2017年ごろに、IoT/AIの取り組みのなかで生産シミュレーターを検討したことがありましたが、当時は費用対効果が明確に示せなかったこともあり、導入自体は断念した経緯があります。その時に検討していたものの1つが「Plant Simulation」で、今回新たに検討するきっかけとなった社長の話のなかでも、具体的に「Plant Simulation」の名前が出ていたほどでした。
新たな環境づくりでは、工程設計のシミュレーションが可能なもので、最終的には工場丸ごと最適化の検証ができるものを求めていました。具体的には、複数の製造ラインを兼任させた要員負荷やスキル別での成立性検証、製品運搬やルート作成、原価償却を想定した設備費の入力、付帯作業である書き物や寸法検査系作業の費用計算、工程間在庫の適正化および妥当性検証といった、自分たちでシミュレーションしたいことができるかどうかがポイントです。どちらかといえば、シミュレーションの正確性というよりも、アイデアをそれなりに表現できる自由度の高さを求めていました。
自由度や再現性の高さが最適、内製化に向けた伴走支援サービスを重視
久世様:実際には自分たちでシミュレーションモデルを内製化したいという思惑もあり、最初からモデリングをお願いするつもりはありませんでした。ただし、誰でも簡単に扱える代物でないことは試した段階で感じた部分もあります。Industrial Engineering(IE)の知識は必須ですし、コードの自作作業や3Dモデルの作成といった高度な知識を有する人材が必要だと考えていました。実際に複数の生産シミュレーターを検討したのですが、3D描写がきれいな、見栄えのいいツールも存在していましたが、結局は具体的な変数をしっかり登録してシミュレーションできるものとしては、「Plant Simulation」一択だったのです。自分たちで内製化していける、そして自由度が高いという観点では、他のツールは弱い印象でした。
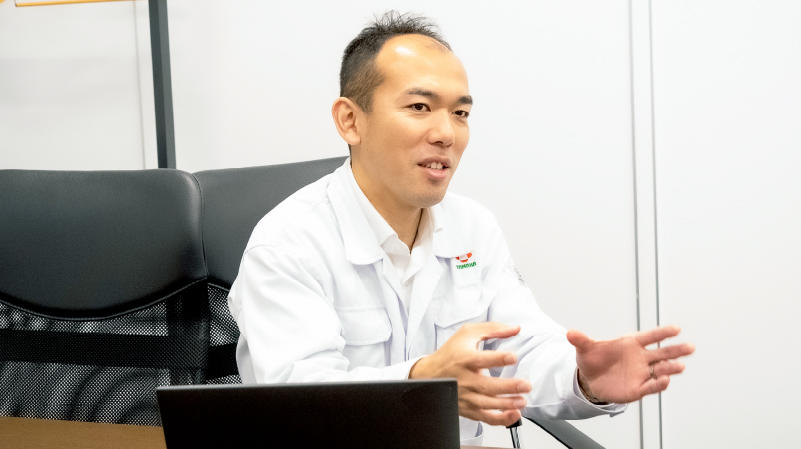
久世様:自由度という意味では、例えば10個部品が入る箱に、製造された最後に端数が3つほど残った場合もその箱に入れる必要があり、その場合は10個の箱と同じだけの検査が必要です。当然ながら割高な状態になりますので、具体的な現場のシーンを想定したものまでシミュレーションできるかどうかといったことが一例になります。そういったカスタム要素が入ると、他のツールではかなり難しい処理が必要で、結局外部にお願いせざるを得ないという状況が生まれてしまいます。内製化の文化がある我々にとって、「Plant Simulation」では内部でも進めていけるのではと考えたのです。
横川様:正直に言えば、最初に「Plant Simulation」を開発しているシーメンスにお願いして1か月ほど触らせてもらったのですが、自分で一から作るのは難しいと考えていました。開発経験がない私にとって、一緒に伴走してもらえる支援がないと形にするまでには至らないという懸念もあります。そこで、シーメンスから紹介を受けたのがマクニカで、そこに伴走支援のサービスがあったことは大きいと感じました。モデル作成サービスではなく、伴走していただけるというのが何よりもありがたかったのです。おそらく伴走支援がなければ、投げ出したい気持ちになっていたかもしれません。
高井様:金額的に見ても、他社と比べても十分許容範囲の金額だったこともあり、とりあえず1年は使ってみようというチャレンジの思いで導入を決断しました。買い切りと違い、いわゆるサブスクリプションで契約できるため、難しいようであれば継続しないという判断もしやすかったのです。
現状の運用
既存工場をデジタル空間に再現することに成功
横川様:実際には検討指示から年内に判断をするべく検証を進め、導入後は私のほうで半年間の間に操作を習得するという計画で進めていきました。そのなかでは、既存工場をデジタル空間に再現するためのモデル作成を実施し、製造プロセスの改善に至る使い方検証まで推進しました。工場稼働の前提条件を想定して「Plant Simulation」で改善案も提示できる形までもっていきましたが、実際に現場の工程レイアウトを改善案に沿った形で変更するところまでには至っていません。まさに、これから実現場へシミュレーションの結果を生かしていくことになります。
私以外にも、2名のプラントエンジニアのメンバーが習得をしており、工場の現場側のメンバーと技術側のメンバーそれぞれの立場で工程設計などのシミュレーションを行いながら、いろいろなパターン出しを行っています。習熟度の難易度もあるため、今のメンバーがしっかり使っていけるようにしていきながら、いずれはもっと多くの人が触っていけるような環境でシミュレーションを業務に組み込んでいけるような体制にしていきたいです。
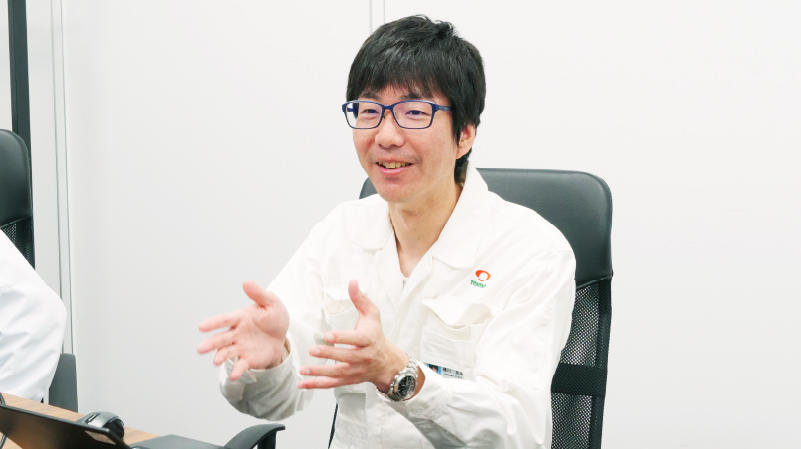
久世様:シミュレーションに用いているパラメーターといえば、特に設備稼働率に起因するところで、非常に多くの要因を考える必要があります。今はAGVの必要台数や充電状況、スペース、ルートなど、周辺設備も含め非常に多岐にわたっています。もちろん、ラインそのものの能力である1時間あたりに加工できる数や運搬能力なども加味しており、それぞれパラメーターを変更することで新たなシミュレーションが可能です。この辺りは、まさにIEの知識や経験が必要で、新たにラインを立ち上げる仕事を長年やってきている横川だからこそ、「Plant Simulation」でのモデル作りが実現できました。
モデルは1度の制作で終わらない、常に運用していくことが必要な業界
横川様:現状は小型の部品を製造する工場のモデルをAs Isとして作り、これから大きな部品を作るラインを増設していくような理想的なTo Beモデルを考えています。これまでは、300個製造すれば1回持っていけば終わるところ、「EV関連の大型部品の場合は、何回運んでいくのか」といったことから、運搬回数の増加により「すべてをフォークリフトで運べない大型の部品はAGVを動かしてどう運ぶのか」といったことなども検討が求められます。部品の保管も1段ずつ積んでいった場合、段積みした場合などそれぞれのプランで何名ぐらいが必要なのか、製品ををどのように運び、保管スペースはどう確保するのかといったことを対比させながら、数値化していくような使い方ができます。今まで感覚で出していたアイデアが、充電タイミングなども加味しながらAGVの必要台数を割り出すなど、「Plant Simulation」によって具体的な数値まで落とし判断できるようになっています。
久世様:シミュレーションができたら実際にそのまま製造ラインを作ればいいと考える方もいますが、我々からすればその案件が失注してしまう恐れもあります。特に自動車部品の世界では、年間10万台分の部品を作っていたのが、来年から20万台に増えるかもしれないという状況が常に起こり得ます。「Plant Simulation」でモデル化した方向性で実施するのは絶対よいことは分かっているのですが、常にそのリスクも考慮しながら進めていく必要があります。ラインを立ち上げるプロジェクトは、環境変化が激しく五月雨式に動いていくため、常にシミュレーションを回していくようなイメージが必要です。
「Plant Simulation」導入での変化
動的検証が難しいExcel、単位時間あたりのアウトプット量が劇的に変わる
高井様:「Plant Simulation」を導入したことで、基本のモデルさえ作成すれば、例えばスペース効率やリードタイム、中間在庫などさまざまな目的に応じてパターンごとの数値が導き出せるなど、数値評価がしやすくなる点は大きな魅力です。また、先進的な取り組みとして社外に向けて情報発信したいという役員の声があり、資料を出すことは多々あります。工場見学などで外部の方が訪問した際にも同様に、「Plant Simulation」の資料を出していますね。
久世様:工程としてAGVがどう動けば効率的なのか、最小限の台数で済むのかといったことの検討は、やはりExcelでは難しいです。設備がメンテナンスやトラブルなどで一定の割合で停止することは致し方ありませんが、Excelの場合は1日平均1時間停止するといった稼働率をベースに計算せざるを得ません。「Plant Simulation」であればきちんと正規分布に従って停止を計算してくれるなど、クリティカルな部分がきちんと見えてきます。その意味でも、やっぱりシミュレーターはいいものだと感じています。Excelでは難しい動的な評価ができることが大きいですね。ざっくりとした方向の検討はExcelで可能でも、ダイナミックに変化する事象をとらえたい場合は、どうしてもExcelだけでは難しいところです。
横川様:シミュレーションの状況を見せることですごいという声は聞かれますが、それをどう使うのかはこれからです。今は製造側のメンバーに「Plant Simulation」を教えていますが、そのメンバー目線だと製品の配置などの視点が違うなど、現場ならではの目線が垣間見えます。そんな共通の会話ができるだけでも大きな効果で、今後期待を寄せています。シミュレーションによって最適化を進めていくことで、最終的には他社との競争力に効いてくるはずです。
久世様:実際には設備レイアウト変更にExcelを使ってどの程度時間をかけていたのかを洗い出しており、例えば過去2年間で3259時間をかけていましたが、工数は同じでもよりクオリティを高めた検討が進められるという視点で効果を見ています。変数もその都度変えていくことで、さらに効率よくシミュレーションが可能なはずで、単位時間あたりのアウトプット量が大きく変わることが評価の1つとなってきます。
マクニカがもたらした変化
プロジェクト遂行になくてはならない伴走型支援
横川様:私自身プログラムなどの経験がなく、当初は本当に何もわからないところからのスタートで不安がなかったといえば嘘になります。マクニカの伴走型の支援があったことで、色々キャッチボールしながらなんとか進めていけました。マクニカのエンジニアからは「3ヶ月ぐらいすれば雲が晴れる」と励ましてもらいましたが、本当に雲が晴れたのです。そこからは色々なことがシステム的に考えられるようになりました。
伴走支援については、月2回でそれぞれ1時間ずつ定例会の時間を確保いただき、webミーティングでこちらのわからないことを教えてもらっていました。日常的な学習は、マクニカが作成した「Plant Simulation」のマニュアルをベースに学んでいきました。最初に見た時は何が書いてあるのかさっぱりでしたが、今となってはとても分かりやすいマニュアルだと実感しています。伴走支援サービスですが、毎月打ち合わせしながら学習できる環境としても、だいぶコストパフォーマンスがいい印象です。
マクニカ自身も、製造業の現場をよく理解しており、打てば響いてくれます。製品運搬の市場トレンドもよく知っていますし、経験から出てくる新しいアイデアなどをいただくこともあります。今まで考えていなかったような評価方法まで教えていただけて、とても勉強になりました。
久世様:当初は、工場のモデルをマクニカ側で作成する前提で、それを1年の研修を通じて一緒に作成していくという提案でした。我々にとって“何でも聞ける先生”になって欲しいという要望にも、柔軟に対応していただけました。かなり無茶なお願いもありましたが、我々の希望に沿う形で支援体制を整備していただけて感謝しています。
定例会についても、こんなことがしたい、こういうやり方が分からないといったことをその場でぶつけるのではなく、自分なりに考えた部分とわからないことを事前に連絡し、その回答を定例会の前にいただいたうえで当日にそこを解消していくというやり方で進められ、限られた時間を効率よく活用できました。
「Plant Simulation」の習熟度を高めながら未来へ繋げる工場実現に向けた環境整備を続けたい
高井様:これからですが、基本的には技術部門と製造部門それぞれ1名が「Plant Simulation」の習熟度を高めるべく継続して触れており、製造部門は既存ラインの現場改善に、技術部門は新たに立ち上げるラインに対して数値評価しながら工程を決めていくといった使い方になっていくことでしょう。
横川様:まずは「Plant Simulation」をしっかり実装段階に移していくことが重要で、製造実行システムなど他システムとの連携はこれから検討する可能性はあります。最終的には“未来へ繋げる工場”へ進化させていきたいため、マクニカが持っている他のソリューションも含めて、役立つものがあれば提案いただき、うまく活用していきたいと思います。
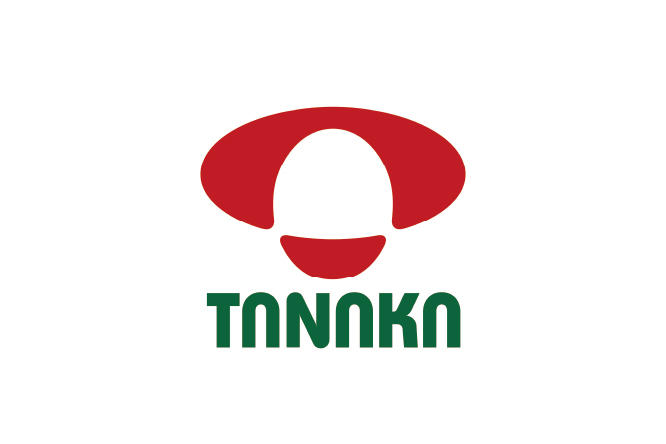
田中精密工業株式会社
- 事業内容
- 自動車部品、オートバイ部品、汎用部品、その他製造販売
- 創立
- 1948年
- 従業員数
- 連結 1,242名 単独 391名 (2023年3月31日現在)
- ウェブサイト
- https://www.tanasei.co.jp/
PRODUCT/SERVICE
本事例の関連製品・サービスはこちらから
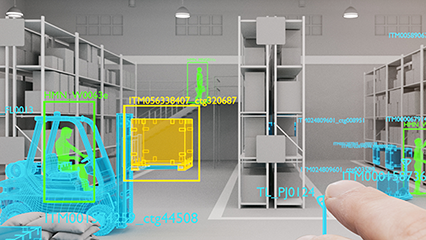
シーメンス Plant Simulation 「Tecnomatix」
Digital Twin 生産シミュレーションソフトウェア
CONTACT
本事例、製品の導入に関するご相談など、お気軽にお問合せください。