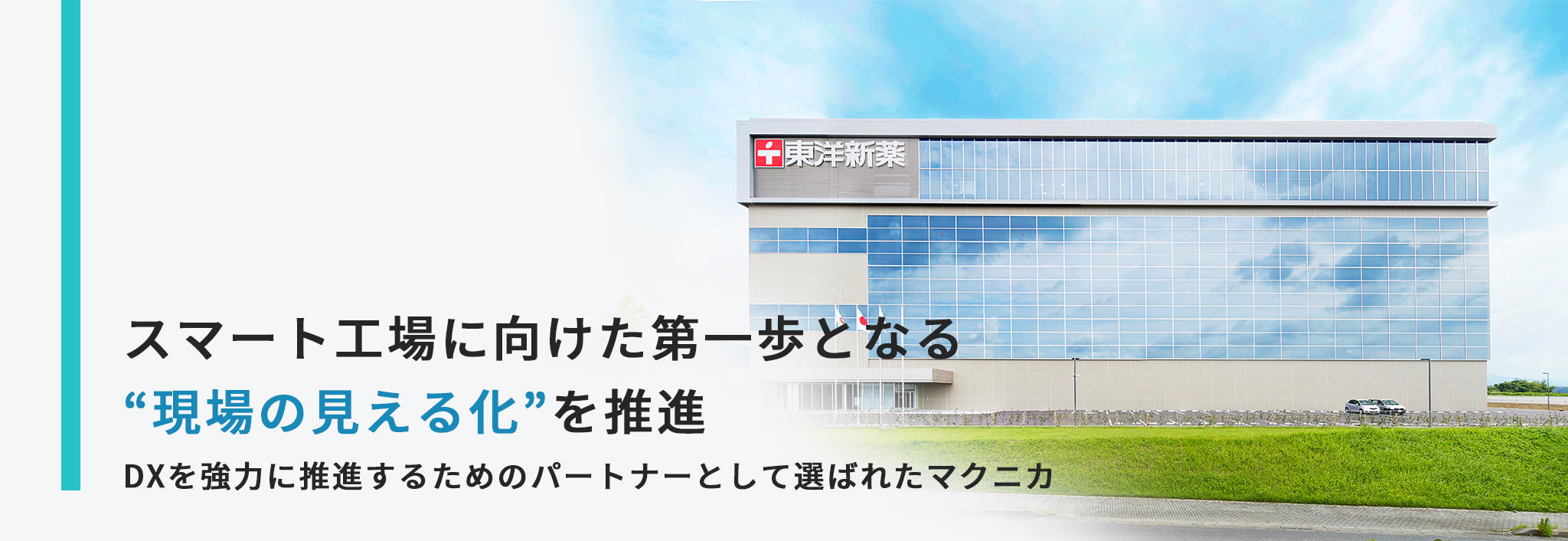
株式会社東洋新薬様事例
ODEMという新たなビジネスモデルで健康と美をサポート
1993年に化粧品卸販売業として創業し、1997年に株式会社セブンシーズ内の健康食品部門が独立して設立された株式会社東洋新薬。
「健康食品」「化粧品」の両方をワンストップで製造できる総合受託メーカーとして、高度な製造管理、品質管理体制を整えており、健康食品によって身体の内側から、そして化粧品によって身体の外側の両面から「健康」と「美」をサポートしている。
商品企画から処方設計、製造、販売促進支援までトータルサポートを行っており、委託者のブランドで製品を設計・生産するODM(Original Design Manufacturing)にて培われた研究・開発力、知財、生産能力を生かし、委託者のブランドで製品を生産するOEM(Original Equipment Manufacturing)にも注力。
同社ならではのビジネスモデルであるODMとOEMの両輪による“ODEM(オデム)”を武器に、エビデンスに基づいた付加価値の高い製品づくりによって世界中の人々の健康と美へ貢献する事業を推進している。
USER PROFILE
■企業情報:株式会社東洋新薬
■事業内容:
健康食品・化粧品のODM・OEMメーカーとして第一線を行く株式会社東洋新薬。
「HIGH-END VALUE」の企業理念のもと、「研究開発力」「品質管理体制」「国際基準をクリアした工場設備」を強みに、世界の人々の「健康」と「美」への期待に『価値』で応え、顧客と消費者に最も支持される会社を目指している。
サマリー
背景
-
“ODEM(ODM & OEM)”という新たなビジネスモデルで健康と美をサポート
-
設備稼働率の最大化と業務シンプル化
-
全社的DXを推進し全情報の連携を目指す
課題
-
製造ラインの進捗状況の見える化
-
リアルタイムな稼働状況の把握
-
営業から製造までデータの一気通貫
選定
-
ITとOTの両方に精通
-
現実を見据えた将来構想を一緒に描ける
-
経営が意識するKPI管理
取り組み
-
特定ラインで、取得した機器情報をリアルタイムにデータ処理し可視化
-
見える化した情報は検査や充填の実績 / アラーム / 歩留まり数 / 目標達成率など
-
使用方法の事前トレーニング
今後
-
基幹システムとの連携で、営業から物流まで全情報の一気通貫を目指す
-
予防保全や動線解析による標準工数の算出など、新たな考え方も取り入れスマート工場に向かう
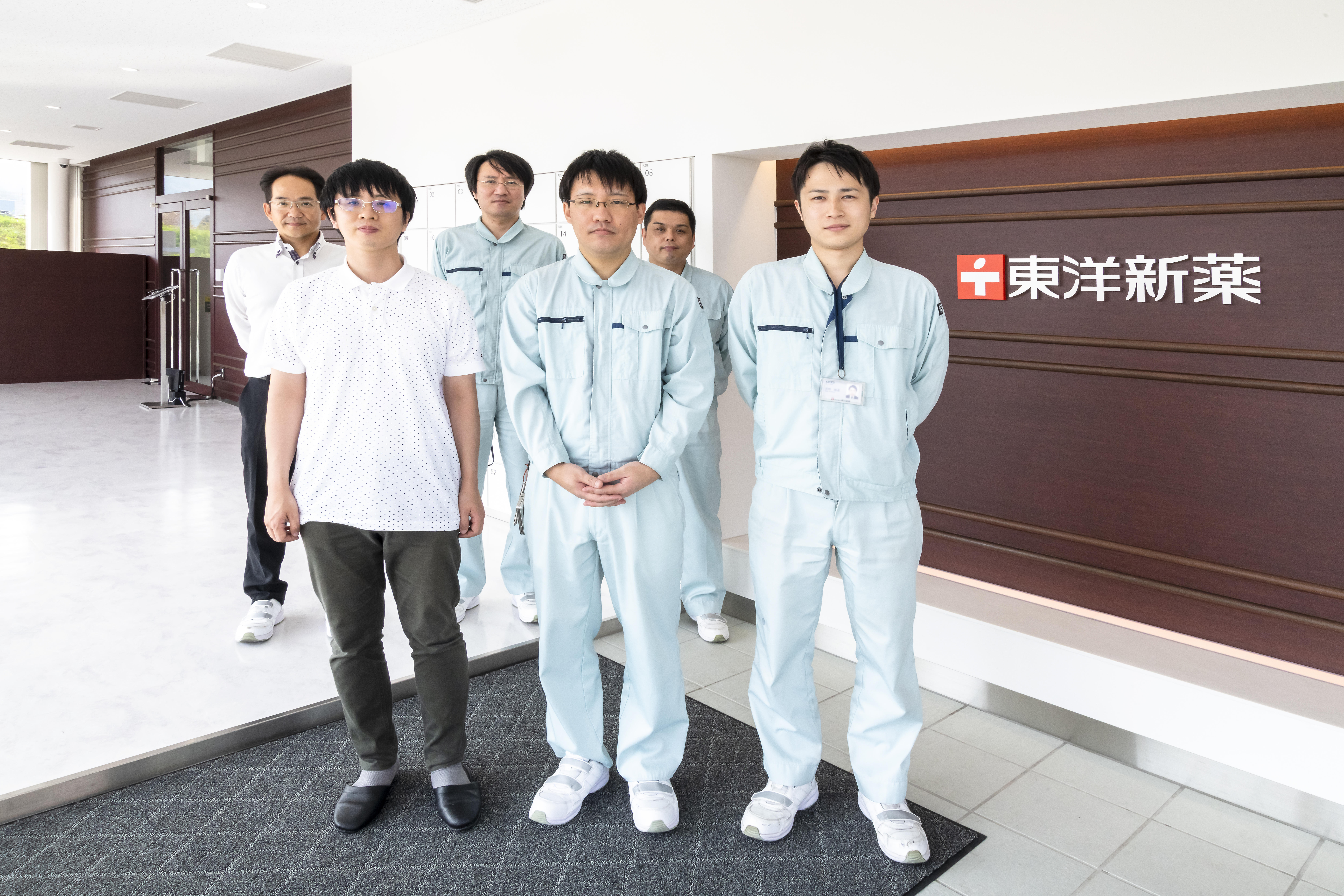
<奥左から>
製造本部 設計技術部 部長 小関善史 氏
製造本部 設計技術部 設備技術課 次長 豊田崇 氏
IP工場 副工場長 森山久雄 氏
<手前左から>
システム開発部 伊藤大輔 氏
製造本部 設計技術部 設備技術課 阪田憲明 氏
製造本部 設計技術部 設備技術課 長野樹道 氏
背景
高い品質の商品を生み出す同社の工場を支える製造本部では、業務フローの見直しや人材育成を積極的に実施している。
ー 森山氏
2019年には次世代型の製造拠点として新たにインテリジェンスパーク(IP)工場を設置し、お客様のご要望にあわせて設備を導入できるようフレキシブルな建屋として設計されています。最新鋭の設備によって、機能性表示食品をはじめとした高付加価値の健康食品を製造しています。
このIP工場では、5Sの徹底をはじめ、設備稼働率を最大化するためのノンストップ工場の実現、そして前段取りのしっかり徹底することで業務のシンプル化を図るフロントローディングの実践という3つを掲げているという。
また、右肩上がりの成長を続けている同社では、営業部門をはじめ、品質保証や研究開発分野において単機能でのシステム構築を行ってきたが、今後のさらなる成長を見据えるなかで生産管理システムも含めた基盤全体の刷新を進めている。
ー 藤村氏
成長を続けるなかで会社として転換期を迎えており、システムの刷新によって新たな戦略ツールとして機能させていくことを目指しています。
現在は、現場から得られた情報は主にExcelを中心に手作業で分析しているが、全社的なDXを強力に推進することで、製造現場から営業部門まで全ての情報を連携させていく未来を描いている。
課題
慢性的な課題となっていた、情報活用によるリアルタイムな現場の見える化を目指す
そんなDXを全社的に推し進めるなか、新たに竣工したIP工場が掲げているテーマの1つである“設備稼働率を最大化する”ための施策として、スマート工場への取り組みを検討することになったという。
ー 小関氏
新たな工場では、製造ラインの進捗状況が十分に見える化できていないことが課題として顕在化していました。
以前からの慢性的な課題ではありますが、現場だけでなく管理部門にまで情報共有が進むことで、最適な製造計画が立案できるなど、モノづくりのデータが各部門に対して情報が提供できるようにしたいと考えたのです。
と当時を振り返る。
実際には、新たに導入した設備の稼働率を向上させるべく、当時製造部門に所属していた小関氏などが現場に張りつきながら改善を続けることで、稼働率を相当レベルにまで高めることができたものの、
ー 豊田氏
これから事業が拡大してライン数が増えていくことが明確に見えていたなかで、このやり方ではすぐに破綻してしまう。そんな思いが大きな原動力となったのです。
と説明する。
製造現場でも同様の課題が顕在化していた。
ー 佐々木氏
確かにExcelなどによる管理は行ってきましたが、こちらから見に行く必要があり、自分たちで収集、分析する必要がありました。リアルタイムで適切に稼働状況が把握できれば、ロスを減らすことにもつながります。常時数字で現場の状況が把握できる環境が望まれていたのです。
また工場全体の作業指示を行う製造統括部門に関してはデータ自体が見えておらず、現場から距離が離れてしまうほど状況把握が困難な環境だった。
ー 藤村氏
本来であれば、製造の出来高に応じて、検査部門や物流部門に至る後工程への連携が必要ですが、それも十分ではありませんでした。受注生産となるODEMを中心にビジネスを推進している我々にとって、営業から製造まで一気通貫でデータが流れていかないと会社自体が機能しないため、将来的には、営業にまで出来高が迅速に共有できる環境が望まれています。
その手始めとして、ITを活用することで現場の見える化を実施し、後工程にもつなげていくことを目指したのです。
:
続きをご覧になられたい方は
こちらよりPDF資料をダウンロードしてください