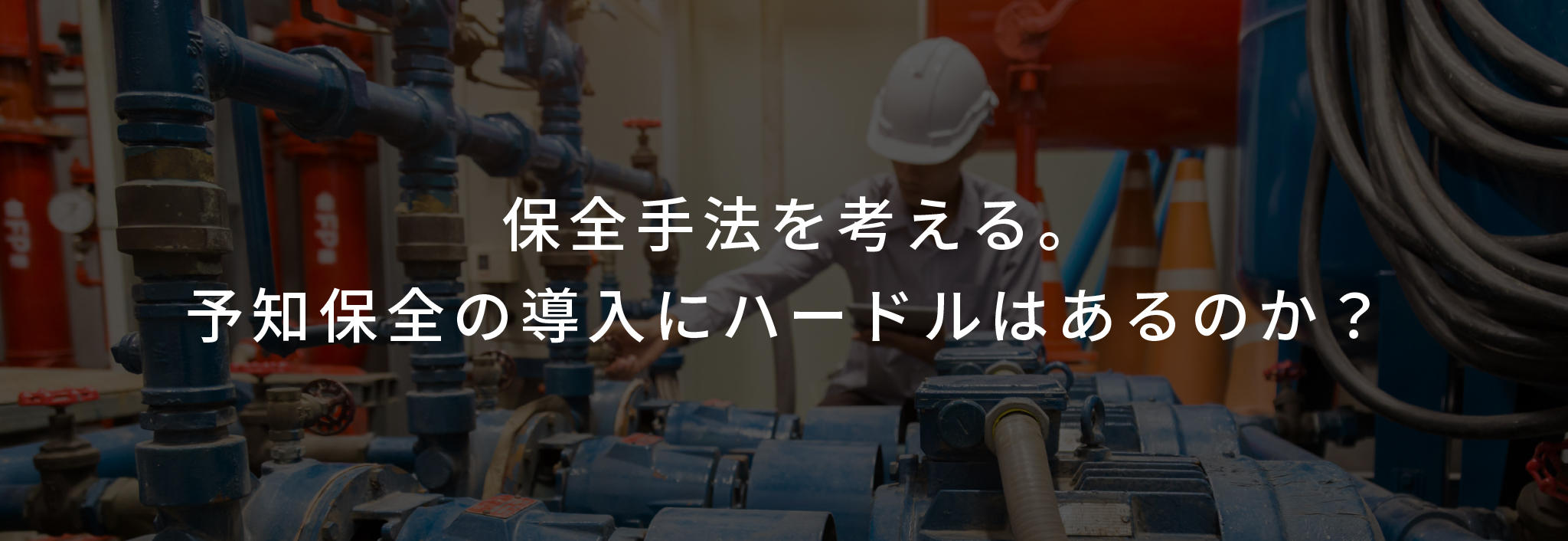
Predictive maintenance has been attracting attention as a part of factory digital transformation, but those promoting digital transformation may have various concerns. For example, we hear voices such as "Will it really be effective enough to justify switching from current maintenance methods?", "We don't know how accurately equipment failures can be predicted," and "Collecting data is difficult, so won't it just be more work than it actually is."
For those of you with such questions, we will introduce the typical methods and challenges of facility maintenance, the benefits of predictive maintenance, and discuss the hurdles to implementing predictive maintenance.
Three methods for equipment maintenance
There are generally three types of equipment maintenance methods used in the manufacturing industry:
・ Breakdown Maintenance (BM)
・Periodic maintenance (TBM: Time Based Maintenance)
・Predictive Maintenance (CBM: Condition Based Maintenance)
Each has the following characteristics:
Breakdown Maintenance (BM)
-This is a method of carrying out maintenance after an equipment malfunction has occurred.
・Unplanned downtime will occur until equipment is restored.
- Many disadvantages have been pointed out, including reduced production efficiency, lost opportunities, and extended downtime.
Regular maintenance (TBM: Time Based Maintenance)
-This is a method of determining the maintenance cycle for equipment and carrying out maintenance on a regular basis.
・Maintenance will be carried out regardless of whether there is a malfunction or not.
- Reduces unplanned downtime compared to corrective maintenance.
Predictive Maintenance (CBM: Condition Based Maintenance)
- This method allows maintenance to be carried out at the optimal timing depending on the condition of the equipment.
- Sensors are attached to the equipment to monitor it, and if signs of malfunction are detected, maintenance is performed.
・It is expected to be an efficient conservation method that utilizes DX.
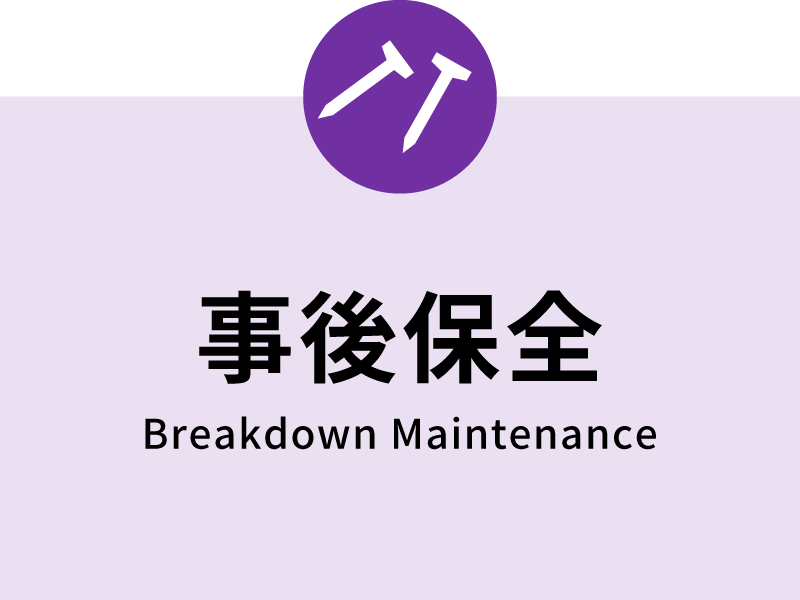
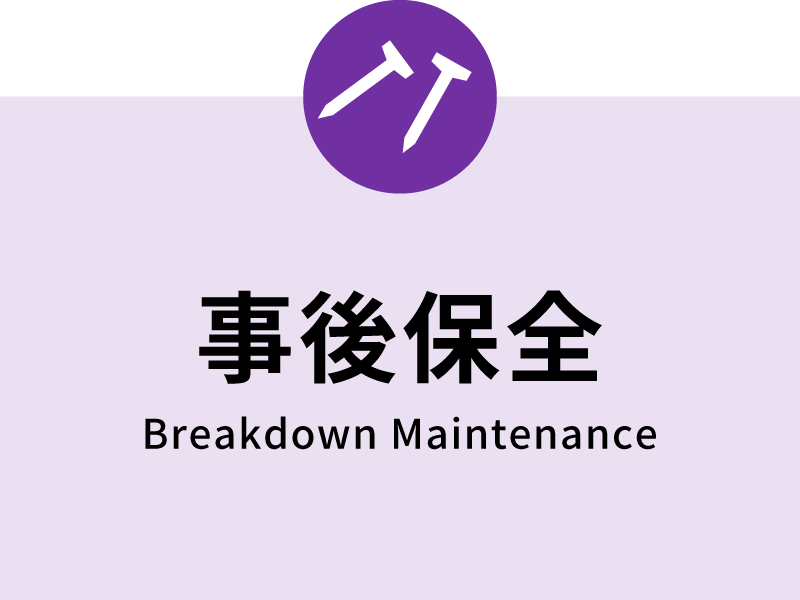
Maintenance carried out after equipment failure
・Since maintenance is carried out after the fact, there are negative consequences when downtime occurs and it tends to take a long time to recover.
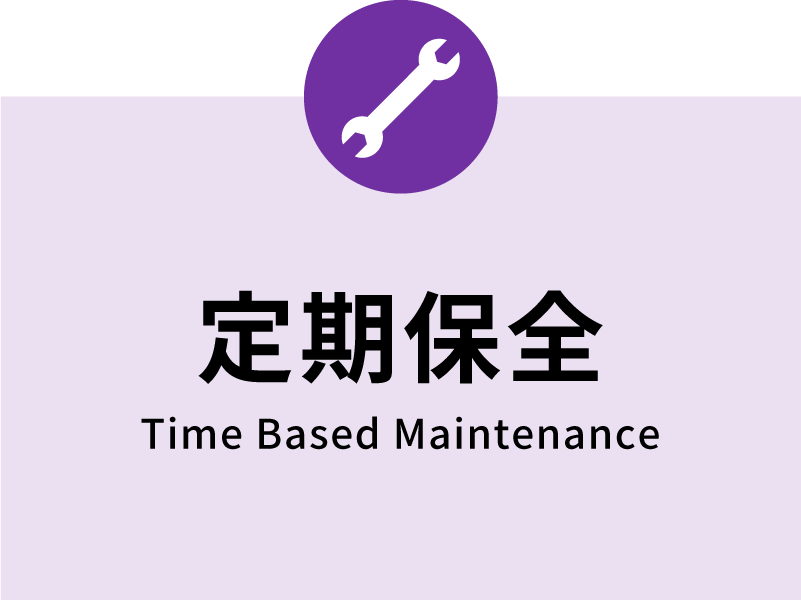
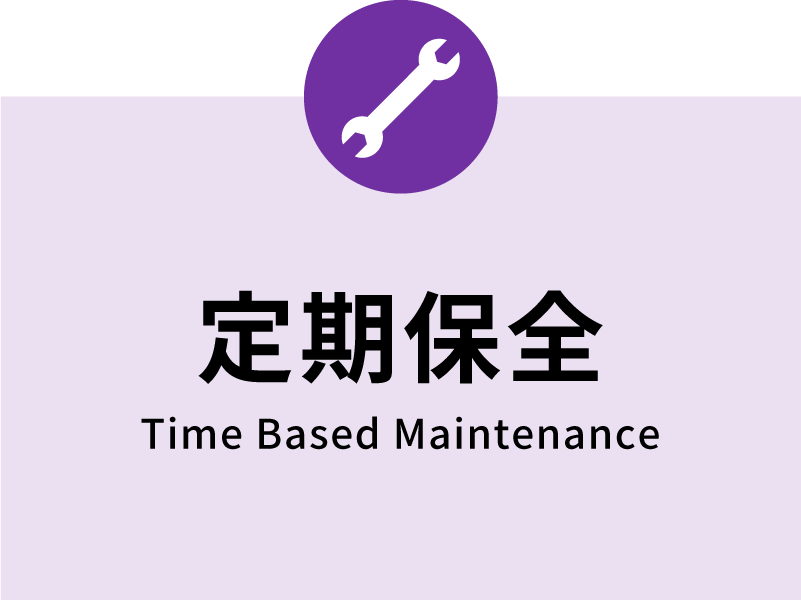
Period: Maintenance is performed according to the equipment maintenance cycle
・Even if the equipment is not broken, maintenance is performed, so there is a high possibility of over-maintenance.
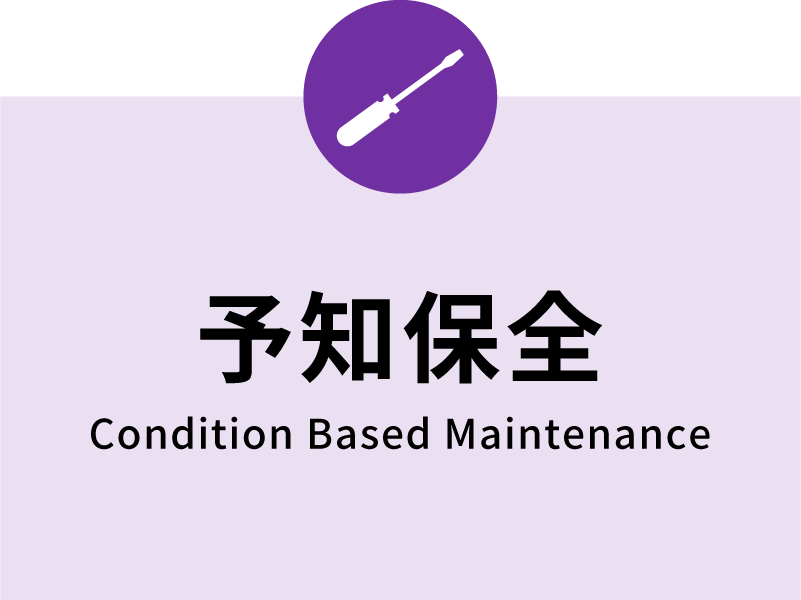
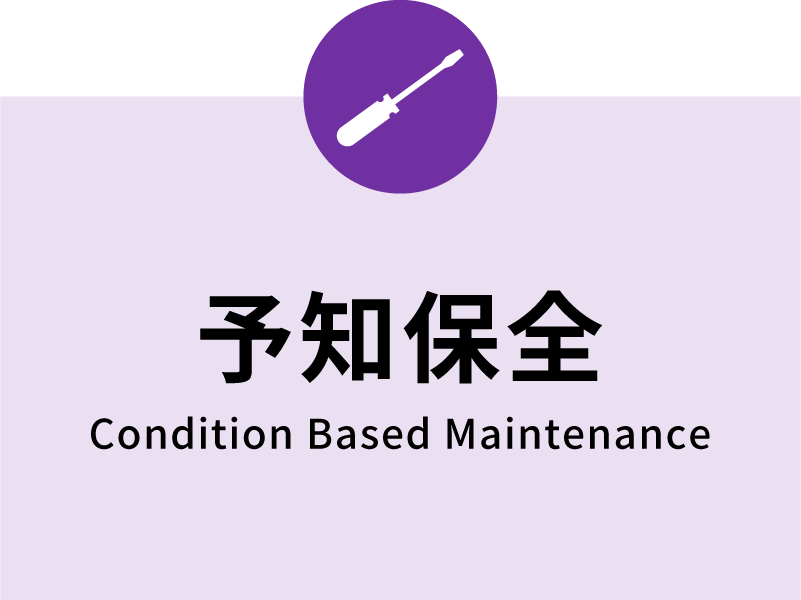
Condition: Carry out maintenance at the appropriate time according to the condition of the equipment
・Efficient maintenance is possible, but expertise in data collection and analysis is generally required
Of these, scheduled maintenance is the most common. Compared to corrective maintenance, it has the advantage of reducing downtime, but it also has disadvantages and issues. Here, we will introduce the disadvantages of scheduled maintenance.
Issues with routine maintenance and the benefits of predictive maintenance
What are the disadvantages of regular maintenance? The main issues are summarized below.
●Over-maintenance
Because maintenance is performed even when there are no malfunctions, there is a risk that, for example, parts that are still usable may be replaced prematurely, resulting in over-maintenance. Over-maintenance is the excessive inspection and part replacement that causes costs to increase. On the other hand, if the maintenance cycle is extended to avoid over-maintenance, the risk of sudden malfunctions increases.
● Shortage of maintenance personnel
Regular maintenance requires more personnel than corrective maintenance because it is performed frequently. Maintenance personnel are required to have specialized knowledge and skills. Labor shortages have become more serious in recent years, and it may not be possible to secure the appropriate personnel according to schedule.
Diagnostic variability
Conventional facility maintenance relies on the five human senses for diagnosis, such as sound and smell, and accuracy can vary depending on the skills of the person in charge. As it is difficult to pass on skills, ensuring reliability has become an issue as experienced engineers reach retirement age.
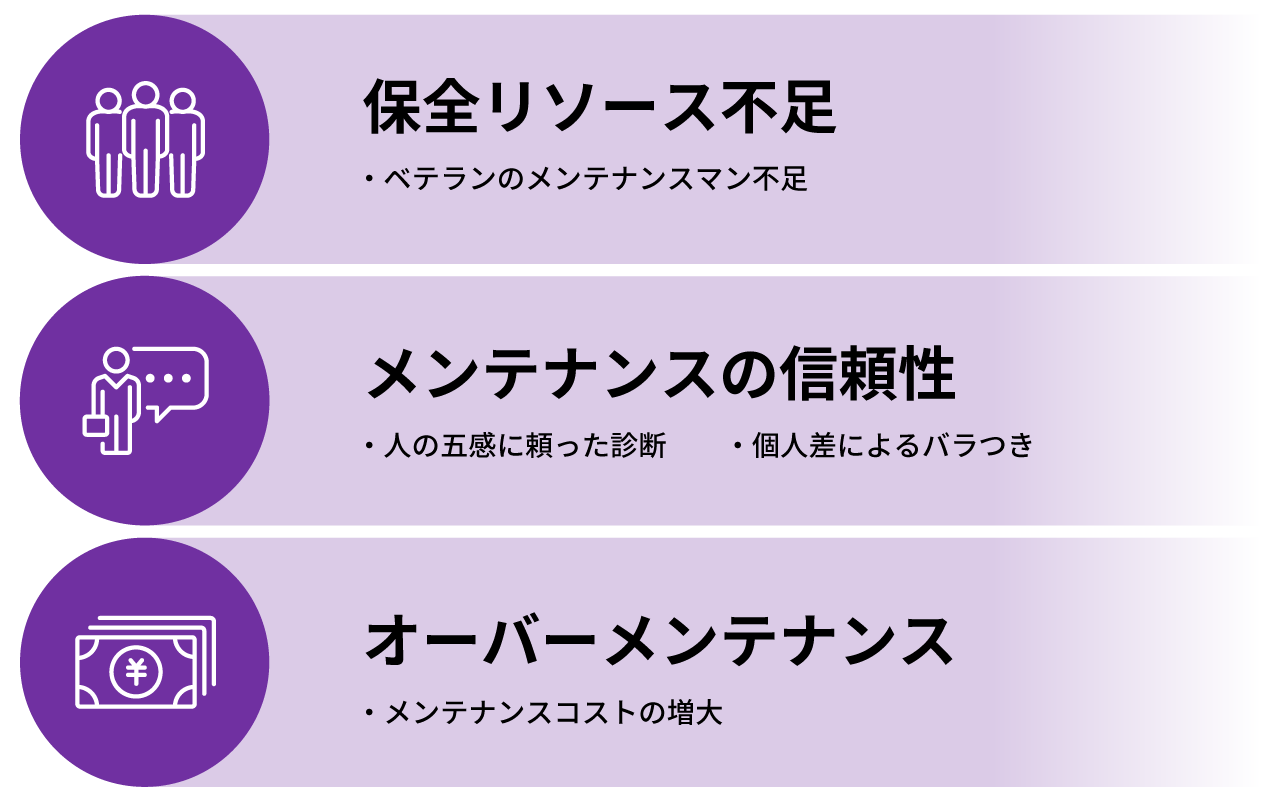
Regular maintenance has many challenges. The benefits of predictive maintenance
What are the benefits of predictive maintenance?
Predictive maintenance using digital transformation is expected to help resolve these issues. Predictive maintenance monitors the condition of equipment, detects signs of malfunction, and performs maintenance accordingly. This provides the following benefits:
●Prevents over-maintenance and reduces unnecessary costs
● Optimize maintenance frequency and utilize maintenance personnel efficiently
● It enables data-based diagnosis and eliminates the variation in accuracy between staff members.
In the manufacturing industry, which is plagued by labor shortages and aging equipment, predictive maintenance, which can make equipment maintenance more efficient, is a measure that should definitely be undertaken.
Hurdles to be aware of when implementing predictive maintenance
However, there are some hurdles to overcome before you can implement predictive maintenance. Below are some common challenges that companies face when implementing predictive maintenance:
[Data collection] Select sensors for each facility
To understand the condition of equipment, sensors are installed to collect data. However, it is not easy to select the appropriate sensor for each piece of equipment and determine the optimal installation location.
[Measurement frequency] Determine the necessary and sufficient timing
Consider the frequency and timing of data measurement. You must determine the necessary and sufficient measurement timing, taking into account factors such as the power consumption of the sensor.
[Threshold setting] Determine the criteria for normality and abnormality
We determine the threshold for distinguishing between normal and abnormal data. It is very difficult to determine the line between a fluctuation within the normal range and an abnormal value.
[Data analysis] Extracting information from huge amounts of data
Sensor data is analyzed to extract useful information. Analyzing huge amounts of raw data requires advanced expertise.
[Diagnosis] Identify abnormalities and the degree of deterioration
The condition of the equipment is diagnosed based on the results of the data analysis. It is difficult for anyone other than an equipment diagnosis expert to not only determine whether there is an abnormality, but also to pinpoint the location of the abnormality and the degree of deterioration.
As such, predictive maintenance poses challenges when using data. Particularly difficult is accurately identifying early signs of abnormalities. While equipment is operating normally, data on abnormalities cannot be obtained. Until an equipment failure occurs, there is insufficient data for setting thresholds and diagnosing abnormalities.
In many cases, it takes a lot of time and money to introduce predictive maintenance and start actual operation. However, companies that are rushing to utilize DX would probably like to realize the effects as quickly as possible without spending too much time and money.
Because there are many hurdles to overcome in implementing predictive maintenance, some companies have tried it in recent years but have been unable to see results and have given up.
"Mpression® Smart Motor Sensor" removes the barrier to implementation
In fact, there is a predictive maintenance solution that can solve these issues: the smart motor sensor "Mpression® Smart Motor Sensor" (hereinafter referred to as the "Smart Motor Sensor"). Its main features are as follows:
[Data collection] Install sensors in designated locations
By simply installing the battery-powered sensor module in the designated location, you can monitor the condition of the motor.
[Measurement frequency] Automatic measurement at appropriate times
Once you perform the initial settings using the smartphone app, the appropriate measurement frequency will be automatically set and data collection will begin.
[Threshold setting] Trained AI automatically determines
AI learns from a huge amount of data on motor behavior in advance, and the optimal threshold is automatically set based on the algorithm.
[Data analysis] Automatic analysis of vibration, temperature, and magnetic field data
The sensor collects vibration, temperature, and magnetic field data and sends it to the cloud via Wi-Fi. AI automatically analyzes the data. The analysis results can be viewed on the dashboard at any time.
[Diagnosis] AI automatically diagnoses abnormalities
When AI detects an abnormality, it will notify you immediately. It can automatically diagnose the abnormality and provide a solution.
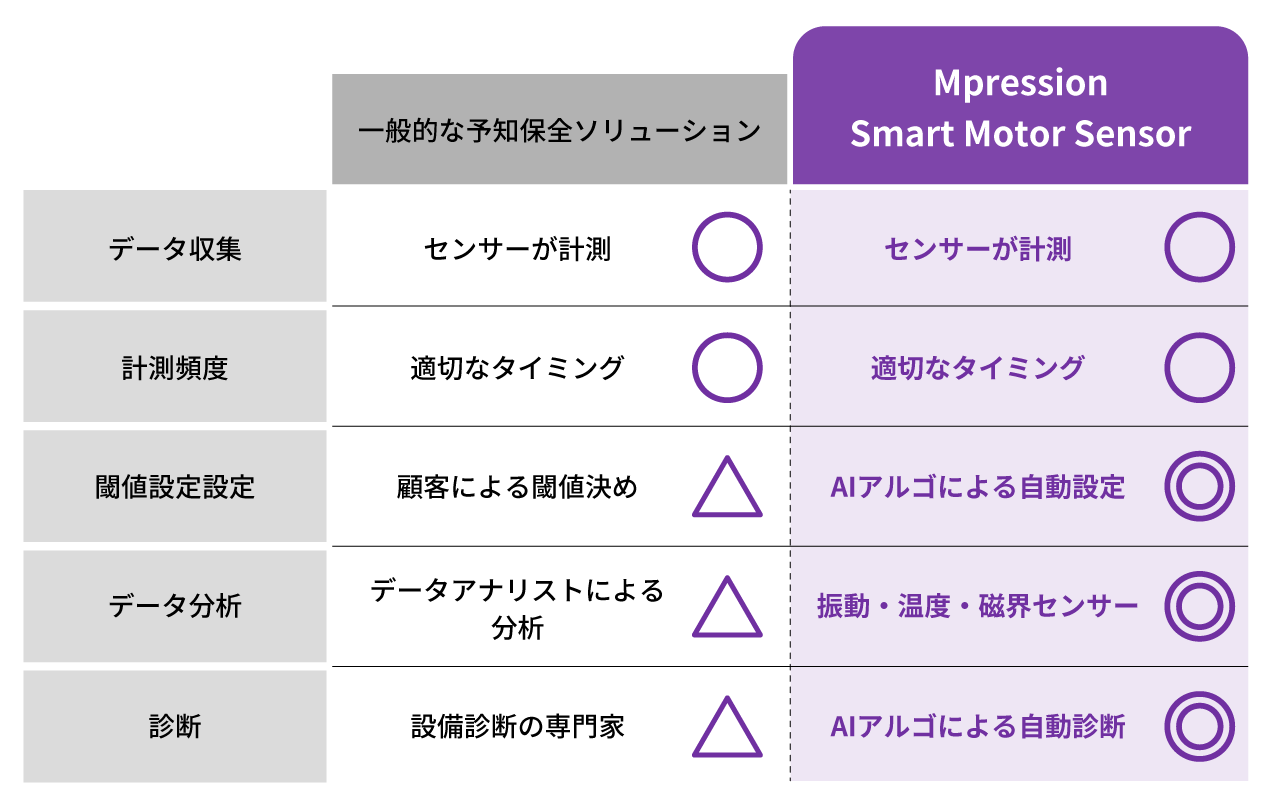
Predictive maintenance (CBM) also has its challenges. With low-voltage three-phase motors, SMS solves all of these issues
The Smart Motor Sensor overcomes all of the common hurdles associated with implementing predictive maintenance, making it easy to implement and allowing you to see immediate benefits.
Smart Motor Sensor is a service specialized for low-voltage three-phase squirrel-cage induction motors. For low-voltage three-phase squirrel-cage induction motors, predictive maintenance can be achieved with just one sensor, from data collection to anomaly diagnosis. If you have a motor that meets this requirement, why not take this opportunity to try out predictive maintenance?
If you are interested, please refer here.
Inquiry
If you have any questions about this article, please contact us using the form below.