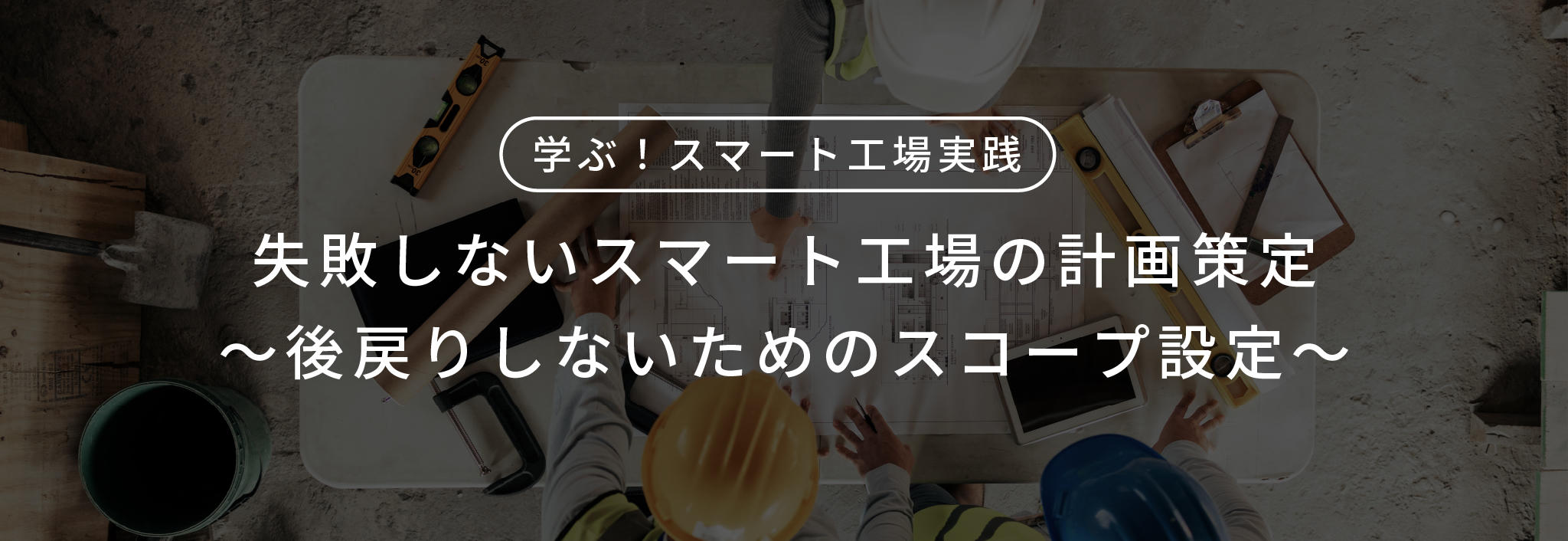
1. Barriers you encounter when you take a step
The production sites that manufacture a wide variety of products have a wide variety of processes and equipment, and the amount of production site data generated from them is enormous, making it difficult to formulate plans for smart factories. If you are involved in the production department, you might wonder, ``How valuable would it be if we could manage a unified system through standardization and improve productivity and reduce costs based on accumulated data?'' I think so.
However, such initiatives tend to create a gap between the highly abstract vision and the concrete issues on the ground, and it is also necessary to involve multiple departments to promote the project, so many people are having difficulty realizing it. It is also true that there are many.
In the end, planning for a smart factory is all about thinking from the why (business issue), specifying the what (work to be done using data from the manufacturing site), and how (what kind of system to use and how to collect data). Therefore, we will consider whether to use it as a resource or not.
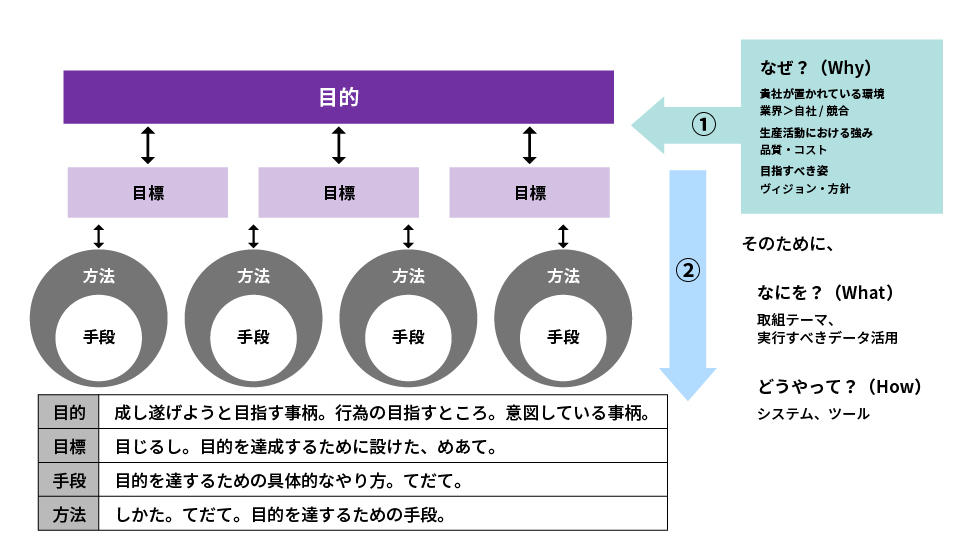
Macnica supports smart factory promotion projects of customers in a wide variety of industries. In the process shown in the diagram above, especially in the "what" and "how" stages where data and system elements are strong, there are some people in the production department who feel psychological barriers because it is a non-specialized field. I think there are quite a few.
The reasons behind this were: ``In the past, we worked on various data utilization within the company, but the system created for the manufacturing department was not used.'' ``We worked on a PoC for a specific process or theme, but other processes and I feel like I have had some bitter experiences, such as not being able to expand on the theme.
As a result, don't you worry that the system will become unused again?Won't it be wasted because it cannot be expanded laterally?
Below, we will introduce Macnica 's scope setting process, which is the `` what'' that minimizes the risk of relapse, for such people.
*The full content of this article is also available in the white paper.
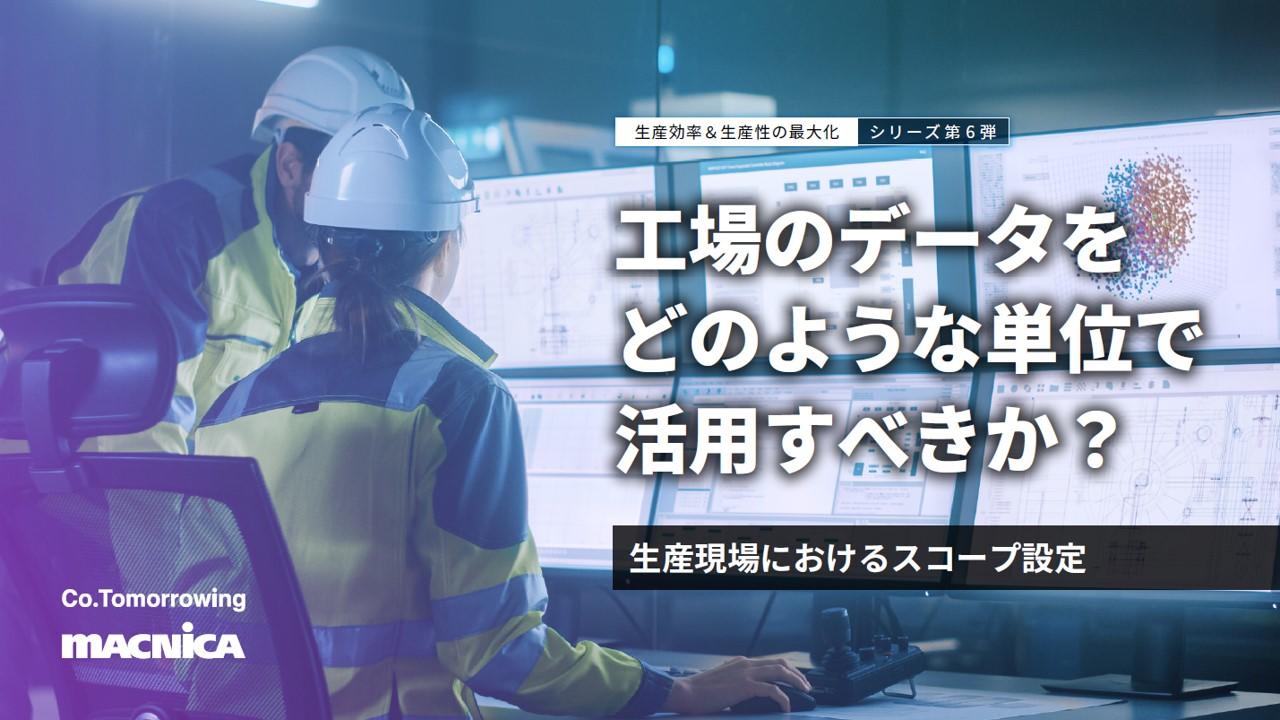
[Recommended white papers]
As the importance of IoT and DX grows in recent years, there is a greater need to utilize data from production sites.
This document is based on the actual experience of project promotion between customers and Macnica.
We will introduce the important points to consider when setting goals and approaches to avoid having to go back and do things again.
2. Smart factory scoping
First, take inventory of the data sources that generate the data you want to use. After working with a variety of customers, we have found that most data sources are concentrated into three sources.
The first is the "production equipment" itself. Specifically, it refers to the operational performance data of each production equipment, which is carried out by multiple processes, lines, and equipment within a factory.
The second is the auxiliary equipment necessary to operate production equipment, or "utility." In order to operate production equipment, electricity and gas are the power sources, and water, steam, air, etc. are used for operation.
The third is "recording". At production sites, the day's work is thoroughly recorded in forms such as daily reports and inspection forms for performance management. Information written on paper contains information about the actual situation at the site that cannot be read from equipment data, so it is one of the data sources that you want to utilize.
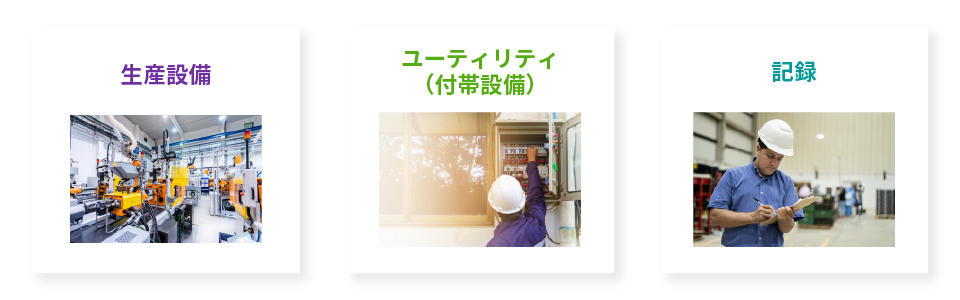
Next, let's organize the data types in the data source. What is important here is to think in terms of the granularity of the type of data item, rather than the item name of each data item (error signal name, temperature, vibration). This is because if you start thinking about the details, the number will reach into the thousands or tens of thousands, and you will not be able to consider them all.
Once the organization is complete, think about how to divide it into scopes. Scope classification is a unit used for data utilization at production sites. Group which data sources and data types are required for specific matters that you want to tackle using data.
For example, ``When promoting environmental measures, we need values collected from utilities and electric motor values of production equipment.'' ``We need to use the operation / stop signals of production equipment and equipment stop error signals that are the reason. "We want to digitize management, but we also need defect counter values and defect error codes that provide production counter values and defect information."
Here, we will introduce an example from Macnica.
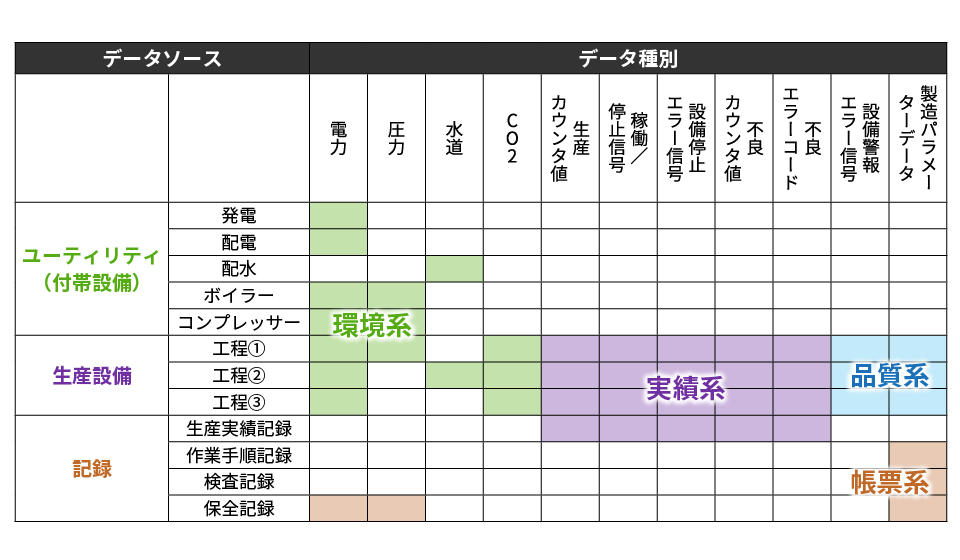
In this example, we have categorized the items we want to work on into the following four categories.
①Environmental: We want to use production site data to promote environmental measures and implement energy-saving measures.
② Performance-based: Want to use production site data to promote efficiency improvements at the site
③ Quality system: We want to promote quality improvement by utilizing data related to manufacturing conditions measured during manufacturing.
④ Form system: By digitizing the records written by workers at the manufacturing site, we would like to reduce the workload and activate data reference.
From the table above, you can see which data sources and data types are required for each of the four scopes.
Once you have determined the scope, you will need to consider which scope and line (area) to implement the system based on the priority of the items you want to tackle. The following two points are important here.
1. Do not implement a system that is smaller than the scope.
Scope classification is a grouping of items based on the required data sources and data types. It is clear that the scoped ranges are the ranges that you want to utilize together. If you implement a system smaller than this range, you will end up going back and thinking, "I needed this data, too..." when the area / function expansion inevitably occurs.
2. Do not consider systems that span multiple scopes.
In theory, you choose data sources and data types based on what you want to work on, so you don't need other data sources or data types. On the other hand, collecting data that is not necessary for what you want to work on is a waste of time.
The diagram below shows the overall picture when Macnica considered the selection and implementation of the optimal system (solution) based on four scope classifications. In this case, the performance system and the quality system were considered separately, but the same system (solution) was found to be optimal for both scopes.
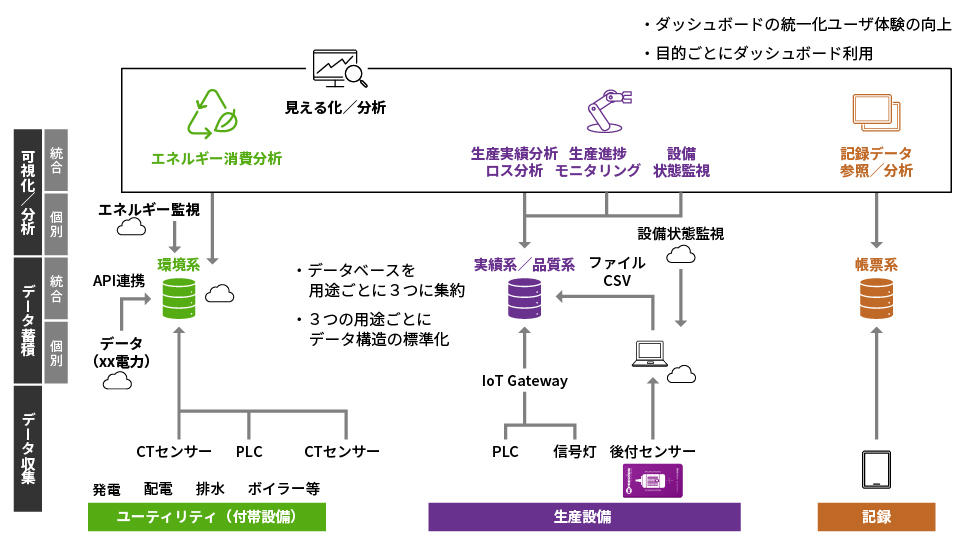
3. A steady step towards a smart factory!
This time, I introduced the flow of scope setting in planning a smart factory.What did you think?
We hope that this article will be of some help to those who want to reduce the risk of relapse as much as possible, and that it will also be useful in promoting your company's projects.
The complete details of the scope setting in smart factories introduced in this column are summarized in the white paper.
We also have webinar videos available for those interested in the specific process of promoting smart factories.
Both can be downloaded from the links below.
*Application is required to download