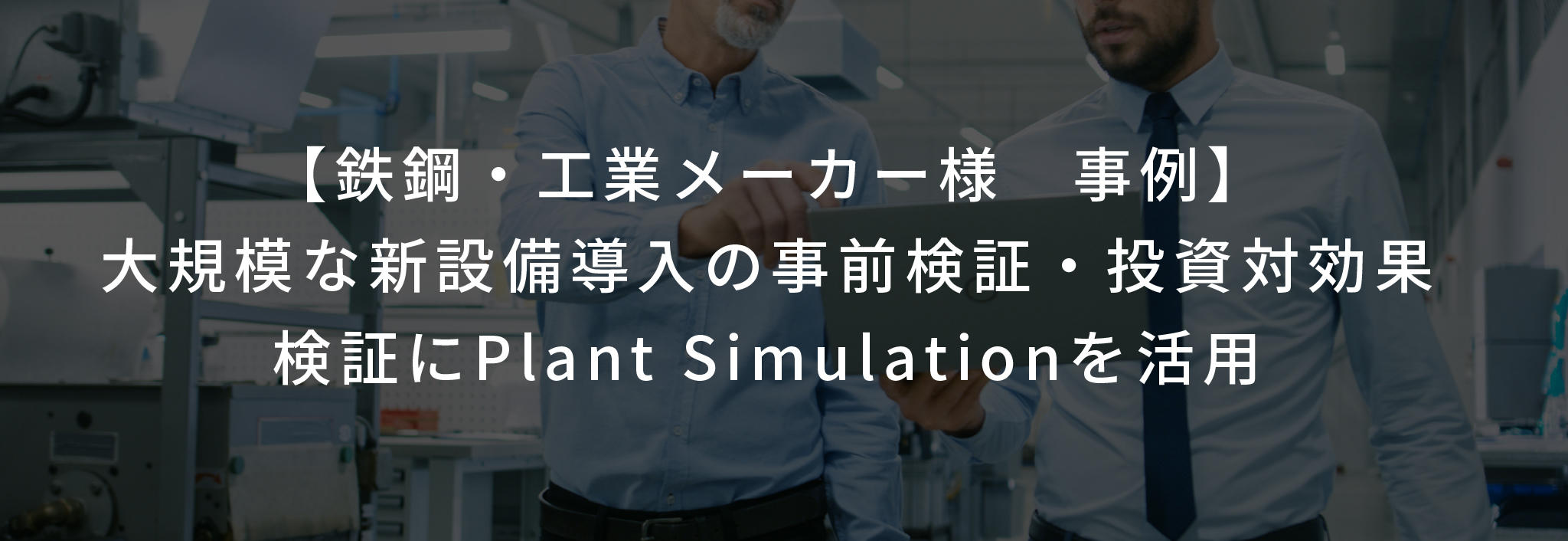
Background of DX promotion
Purpose
-
In making a large-scale capital investment,
-
Verification of whether the expected increase in production volume can actually be expected
-
Verification of return on investment
Task
-
It is unclear whether the expected return on investment can be obtained for the cost of installing equipment
result
-
It turns out that the expected effect is not obtained
-
Succeeded in changing plans before incurring unnecessary costs
1. Background
At that time, most of the equipment in use was already 20 to 30 years old, and aging was a problem, so we were considering updating to new equipment.
In addition, since many processes are performed by workers, there was talk of large orders, so we decided to consider automating the equipment and improving production efficiency without increasing the number of workers.
At the beginning of the study, we conducted an in-house survey to study the specifications of the equipment, and discussed machine specifications and options with robot vendors and processing machine manufacturers.
2. Issues
However, as we proceeded with the study for about a year, it was decided that the cost of installing the equipment would greatly exceed the original budget. I was wondering if I could really get the expected effect for the amount of investment.
At that time, I learned about Plant Simulation, and I decided to introduce it because I knew that if I did a simulation, I could reduce the man-hours and increase the production volume, etc.
3. Introduction
First, we started by creating a sample model based on the actual drawing so that we could see the rough results. After that, we created multiple simulation models by changing the combination, number, layout, etc. of the equipment we were considering introducing, and compared the operation rate and daily production volume of each equipment.
As a result of creating and examining multiple simulation models in about three months, we found that we could not reach the target production volume even if we invested a large amount of money to introduce equipment.
Also, before using Plant Simulation, I used to calculate the production volume on Excel. It turned out that things were accumulating more than expected in various places inside, and the result was that the operating rate was remarkably low. Plant simulation can simulate the entire flow in a state close to reality, so it has become possible to calculate detailed points that cannot be calculated with Excel.
Based on the results, it was decided to temporarily suspend the large-scale equipment installation plan and reconsider the plan.
Utilizing Plant Simulation to verify equipment availability
4. Results
Originally, the plan was to make a large-scale capital investment to improve the production volume, but after conducting a preliminary verification using plant simulation, it was found that the expected return on investment could not be obtained.
Through simulation, we also learned that there is a problem of reduced equipment operating efficiency due to stagnation of intermediate inventory, which adversely affects production capacity, such as inefficient use of work space and an increase in unproductive operations such as management. .
Based on the results, we decided to use Plant Simulation to study the optimal production plan and production line that can minimize the stagnation of intermediate inventory.
Related product
Click here for more information!
movie
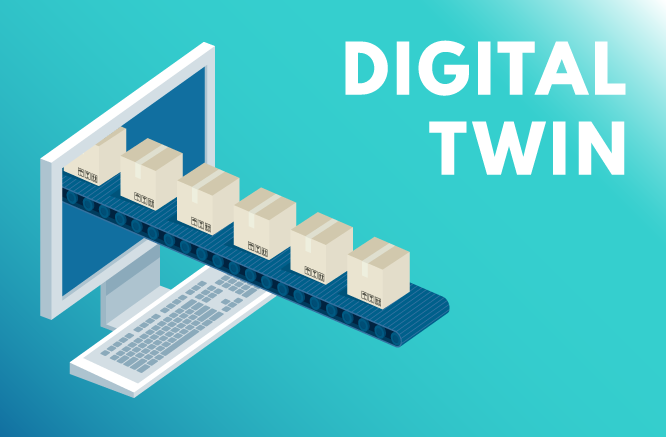
Digital twin introductory video collection
Let's start with the digitalization of the production process! Introducing everything from the basics of digital twins to how to use them in each industry. *Application is required for viewing.
white paper
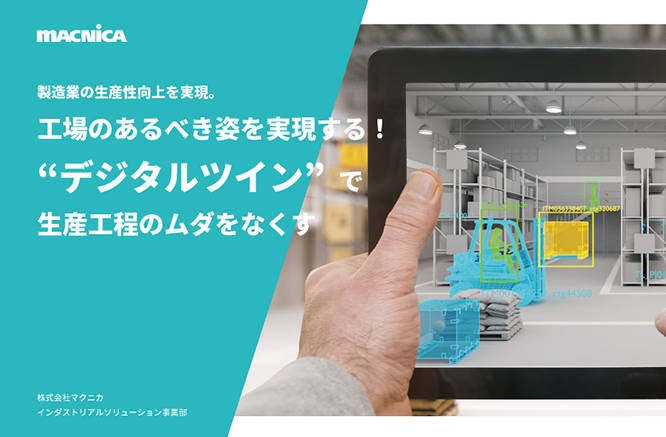
Achieving the Ideal Factory! Eliminate waste in the production process with a “digital twin”
An easy-to-understand explanation of the value of digital twins and how to proceed with their introduction along with case studies. *Application is required to download.