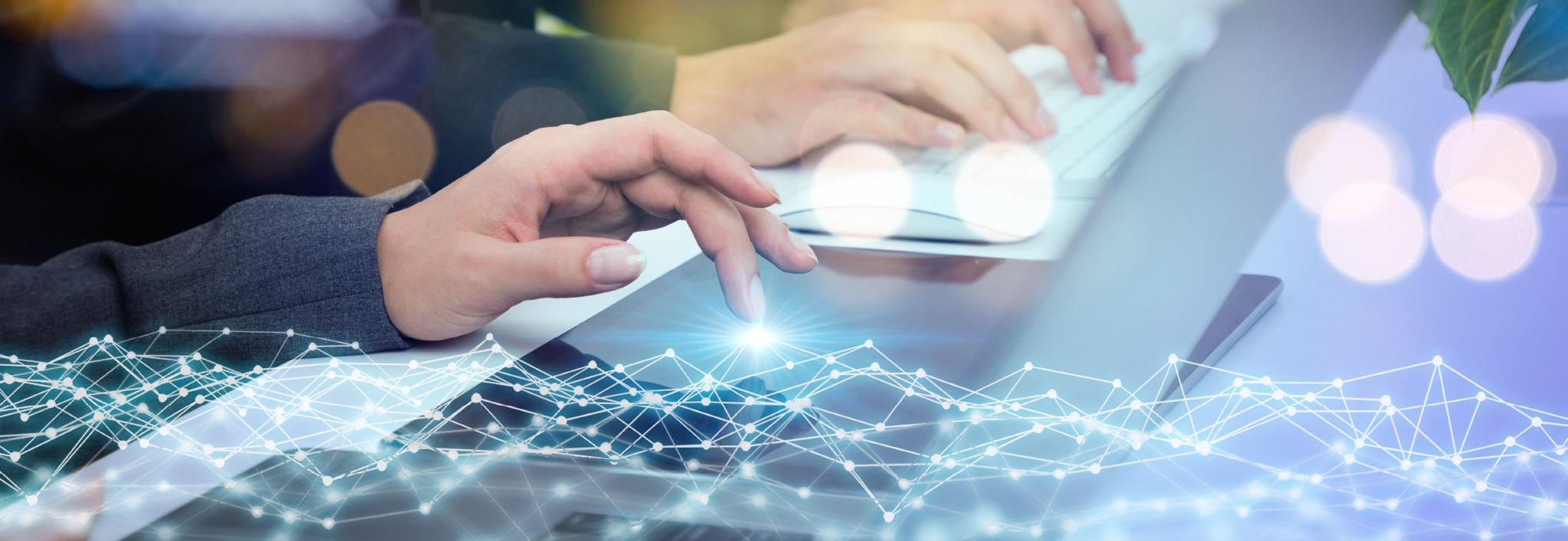
Supporting the dramatic changes in the automotive parts industry through production simulation
"Plant Simulation" contributes to on-site improvements and improved quality of new process designs
──Tanaka Precision Industry Co., Ltd.
Tanaka Seimitsu Kogyo Co., Ltd., which manufactures core parts for automobile engines, is accelerating its efforts to create a new environment, different from the precision manufacturing processes that the company has traditionally specialized in, amid the rapid change in the shift to EVs. To achieve this, the company introduced "Plant Simulation," a production simulation software that can digitally reproduce and verify everything related to the manufacturing process, as an essential system for process design and improvements to existing lines. We asked them about the details of how they came to adopt it.
Participating members of this project
Tanaka Precision Industry Co., Ltd.
- Masaki Takai, General Manager of the Sales and Technology Department, Parts Manufacturing Division
- Ryota Yokokawa, DX Promotion Section, DX Promotion Division, Business Process Reform Department
- Mr. Kenji Kuze, Manager of the Equipment Design Department, Tanaka Engineering Co., Ltd.
Macnica
- Ai Suzuki, Digital Industry Business Division, Professional Services Division 2, 1st Section
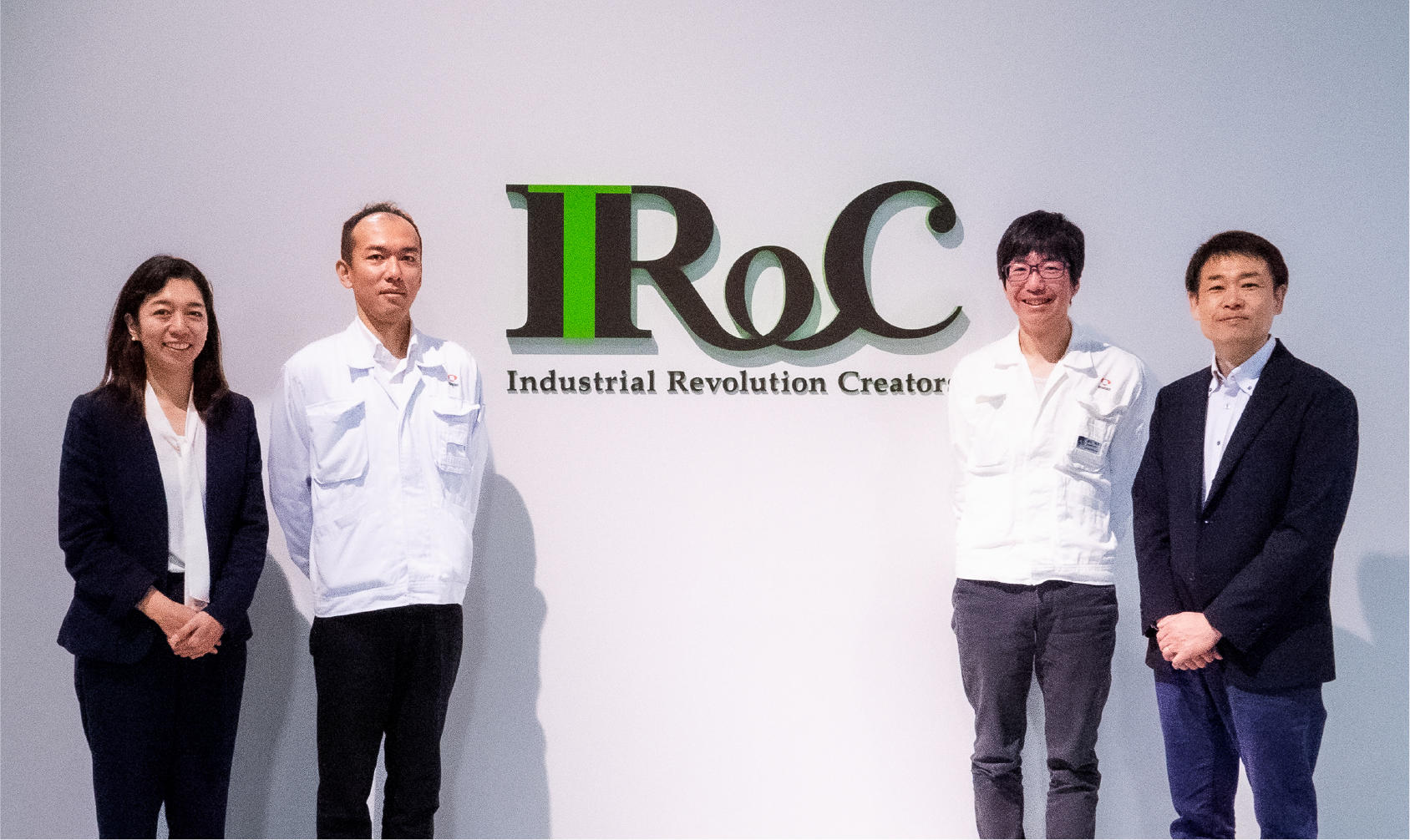
- Task
-
- Major reforms to manufacturing processes in response to changes in product demand due to the shift to EVs
- Limitations of trial and error using Excel simulation
- Difficult to calculate due to complex integrated manufacturing process
- Purpose
-
- Simulation support for process design and on-site improvements
- Visualization and optimization of manufacturing processes
- In-house simulation ensures flexibility
- effect
-
- Easier numerical evaluation and more efficient verification
- Dynamic evaluation for improved efficiency of production processes
- Improved competitiveness and faster on-site improvements
Background of the need for a simulation environment
Changes in the automotive parts industry require transformation of manufacturing processes
Takai-san: We are an automotive parts manufacturer that handles rocker arms, which are installed inside the cylinder head and are the heart of a gasoline engine. In addition to our high technical capabilities to manufacture high-precision, high-performance products, our major strength is our integrated processing system, which covers everything from plastic processing to lathing, cutting, heat treatment, finishing, and part assembly and inspection. This has earned us strong support from customers, mainly major automotive manufacturers. Currently, our 2030 vision is "Change the future," and we are utilizing the technical capabilities and creativity we have cultivated to expand our business into various fields, from entering the aerospace industry to providing motor manufacturing technology and developing factory automation equipment.
With recent changes in the market, there is a demand to shift from internal combustion engine parts to HEV and BEV parts, and the basic policy in the mid-term management plan is to switch to EV parts. Originally, we specialized in palm-sized precision machining, and in many cases we mass-produced small parts with high precision, but EV parts tend to be large, and unlike a shipping container packed with hundreds of parts, there are some that are one part per box, to put it in extreme terms. We are being asked to take a very different approach to the manufacturing we have been involved in up until now, in terms of parts transportation and storage, manufacturing processes, and lot thinking.
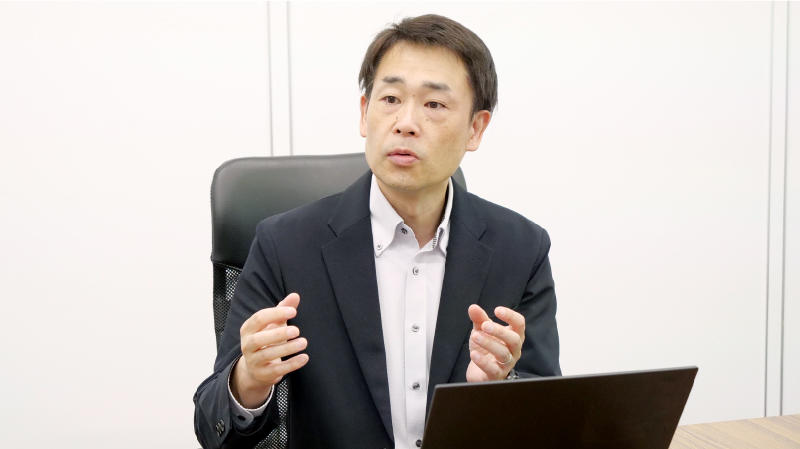
Task
Limitations of Excel calculations, challenges of having a consistent production process
Yokokawa: In order to respond to changes in the market, we have tried various things that we can calculate, even if it is rough, using simulations such as Excel, but there were some parts that were beyond our ability. Simulations using Excel require an enormous amount of man-hours, and even if they were possible, we could only simulate a few patterns at most, so it was difficult to do trial and error to see what would happen if we changed the location of the equipment or the work flow. Moreover, the reality is that it is honestly difficult to dynamically verify the capacity, such as how the storage space changes as things move, using Excel or CAD.
Mr. Kuze: We do everything from sourcing materials to assembling and processing in-house, so the process from start to finish is very diverse. Therefore, there are a lot of variables, and the calculations themselves are more complicated than you might imagine. For example, if a company only does assembly, they could do it somehow with Excel, but for us, it would be a long process. When we thought about switching to EV-related products, the issues of the manufacturing site became apparent.
Reasons for choosing "Plant Simulation"
We want to realize simulations to optimize the entire factory.
Mr. Takai: The reason we decided to introduce a production simulator was not only because problems had become evident on-site, but also because the president had made a top-down decision. He learned from a video that it was an effective solution and asked us if we were considering it. We were also looking for an environment where we could visualize our manufacturing process and perform simulations to set up new processes, so we decided to consider it right away.
Kuze: Actually, around 2017, we considered using a production simulator as part of our IoT/AI efforts, but we gave up on the idea because we couldn't clearly show the cost-effectiveness at the time. One of the things we were considering at the time was "Plant Simulation," and the president even mentioned "Plant Simulation" in his talk, which prompted us to start considering it again this time.
In creating a new environment, they wanted something that would enable them to simulate process design and ultimately verify the optimization of the entire factory. Specifically, the key point was whether they could do the simulations they wanted to do themselves, such as verifying the feasibility of staff loads and skills for multiple manufacturing lines, product transportation and route creation, inputting equipment costs assuming depreciation, calculating costs for incidental tasks such as writing and dimensional inspection work, and optimizing and validating inventory between processes. Rather than focusing on the accuracy of the simulation, they wanted a high degree of freedom to express their ideas to a certain extent.
High degree of freedom and reproducibility are optimal, and emphasis is placed on support services for in-house production
Mr. Kuze: Actually, we wanted to develop our own simulation model in-house, so we didn't intend to ask someone to do the modeling from the beginning. However, we felt that it was not something that anyone could use easily when we tried it. Knowledge of Industrial Engineering (IE) is essential, and we thought that we needed people with advanced knowledge of writing our own code and creating 3D models. We actually considered several production simulators, and although there were some that had beautiful 3D depictions and looked good, in the end, the only choice for a tool that could properly register specific variables and perform a simulation was "Plant Simulation." In terms of being able to develop it in-house and having a high degree of freedom, the other tools seemed weak.
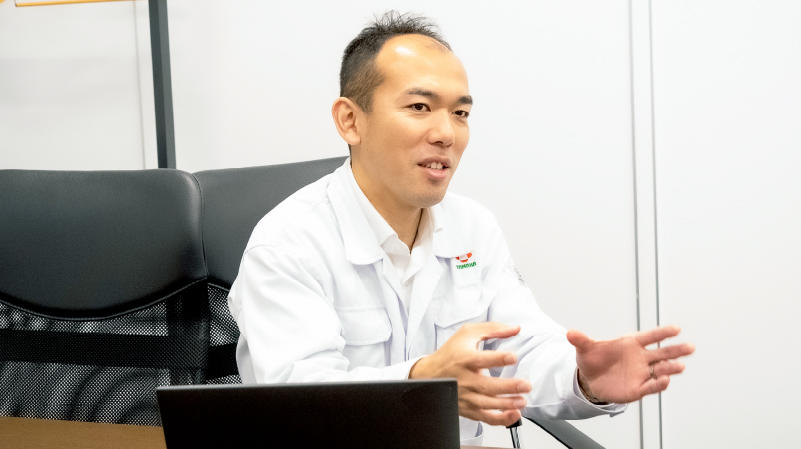
Kuze: In terms of flexibility, for example, if a box contains 10 parts, and at the end of production, about 3 parts remain, they still need to be put into the box, and in that case, the same amount of inspection as for 10 boxes is required. Naturally, this will be expensive, so one example is whether it is possible to simulate specific on-site scenes. When such custom elements are included, other tools require very difficult processing, and in the end, we end up in a situation where we have no choice but to ask an outside party. Since we have a culture of in-house production, we thought that we could proceed internally with "Plant Simulation".
Yokokawa: To be honest, I first asked Siemens, the developer of "Plant Simulation," to let me use it for about a month, but I thought it would be difficult to create it from scratch on my own. As someone with no development experience, I was concerned that I would not be able to put it into shape without support from someone who could accompany me. That's when Siemens introduced me to Macnica, and I felt that it was a big help that they offered a support service. I was most grateful that they could accompany me, rather than providing a model creation service. Without the support, I probably would have felt like giving up.
Takai-san: In terms of cost, it was within the acceptable range compared to other companies, so I decided to try it out for a year. Unlike a one-time purchase, it is a subscription contract, so it was easy to decide not to continue if it was difficult.
Current operation
Successfully recreated an existing factory in a digital space
Yokokawa: In reality, we proceeded with the verification so that we could make a decision by the end of the year, after the instructions were given, and then after the introduction, I planned to learn how to operate it within six months. During that time, we created a model to reproduce the existing factory in a digital space, and promoted usage verification leading to improvements in the manufacturing process. We were even able to present improvement proposals using "Plant Simulation" based on the assumptions for factory operation, but we have not yet reached the point where we can actually change the process layout on site in line with the improvement proposals. From now on, we will put the results of the simulation to use in the real world.
Besides me, two other plant engineers have also learned the technology, and they are coming up with various patterns while conducting simulations of process design from the perspectives of both the factory staff and the technical staff. Because it requires a certain level of proficiency, I would like to make sure that the current members are able to use it properly, and eventually create a system in which simulations can be incorporated into work in an environment where more people can use it.
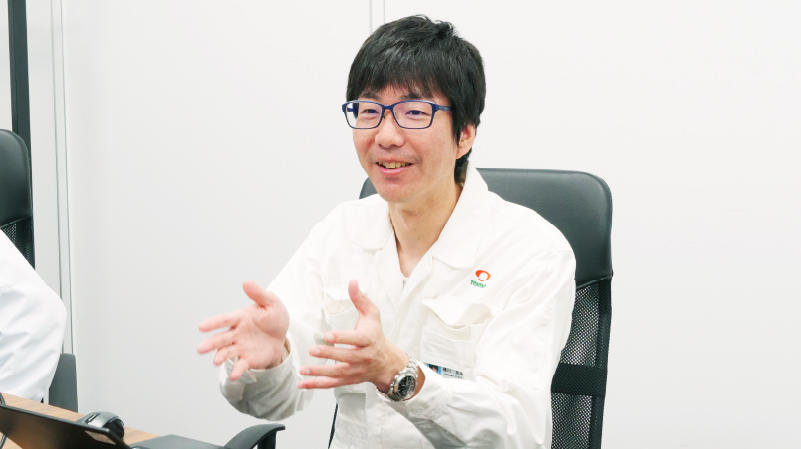
Kuze: Speaking of parameters used in simulations, there are many factors that need to be considered, especially those related to equipment operation rates. Currently, there are a wide range of factors, including the number of AGVs required, charging status, space, routes, and peripheral equipment. Of course, the capacity of the line itself, such as the number of products that can be processed per hour and transport capacity, is also taken into account, and new simulations can be made by changing each parameter. This is where IE knowledge and experience are required, and Yokogawa, with its many years of experience in setting up new lines, was able to create a model using "Plant Simulation."
Models are not created once and then finished; they need to be constantly managed in this industry.
Yokokawa: At present, we are creating a model of a factory that manufactures small parts as an As Is, and we are considering an ideal To Be model in which we will add a line to manufacture larger parts in the future. Until now, we could manufacture 300 pieces and take them once, but with the increase in the number of transports, we need to consider things like "how many times do we transport large EV-related parts?" and "how do we move AGVs to transport large parts that cannot all be transported by forklift?". It can also be used to quantify things like how many people are needed for each plan, such as when storing parts one layer at a time or when stacking them, how to transport the products, and how to secure storage space. Ideas that were previously based on intuition can now be reduced to concrete numbers with "Plant Simulation," such as calculating the number of AGVs needed while taking into account charging timing.
Mr. Kuze: Some people think that once the simulation is done, we should just build an actual production line, but from our perspective, there is a risk that the project will be lost. Especially in the world of automotive parts, a situation can occur where the production volume of parts for 100,000 vehicles a year may increase to 200,000 vehicles next year. We know that it is definitely good to proceed in the direction modeled with "Plant Simulation," but we need to always consider the risks as we proceed. Projects to launch production lines move in a haphazard manner due to rapid changes in the environment, so we need to imagine that we are constantly running simulations.
Changes with the introduction of "Plant Simulation"
Dynamic verification is difficult in Excel, and the amount of output per unit time changes dramatically.
Takai: The biggest attraction of introducing "Plant Simulation" is that it makes it easier to perform numerical evaluations, for example, by creating a basic model and deriving values for each pattern according to various purposes such as space efficiency, lead time, and intermediate inventory. In addition, there were voices from Member of the Board who wanted to disseminate information outside the company as an advanced initiative, so we often provide documents. Similarly, when outside visitors come for factory tours, we provide documents from "Plant Simulation".
Kuze: It is difficult to use Excel to consider how to operate AGVs efficiently as a process, or how to minimize the number of units. It is inevitable that equipment will stop for a certain percentage of the time due to maintenance or problems, but in Excel, you have to calculate based on the operating rate, such as an average of one hour of stoppage per day. With "Plant Simulation," it calculates stoppages according to normal distribution, so you can clearly see the critical parts. In that sense, I think simulators are good after all. It is great that it can perform dynamic evaluations that are difficult to do in Excel. Although it is possible to consider rough directions in Excel, if you want to capture dynamically changing phenomena, it is difficult to do so with Excel alone.
Yokokawa: We hear people say that it's great to show the simulation results, but we're yet to see how to use them. We're currently teaching "Plant Simulation" to members of the manufacturing side, and from their point of view, we can get a glimpse of the unique perspective of the field, such as a different perspective on product placement. Just being able to have such shared conversations is a big effect, and we have high hopes for the future. By advancing optimization through simulation, we're sure it will ultimately have an impact on our competitiveness against other companies.
Kuze: We actually used Excel to determine how much time it took to change the equipment layout. For example, it took 3,259 hours over the past two years, but we see the effect from the perspective that we can conduct higher quality studies with the same number of man-hours. By changing the variables each time, we should be able to perform simulations more efficiently, and the large change in the amount of output per unit time is one of the evaluation points.
Changes brought about by Macnica
Accompanying support is essential for project execution
Yokokawa-san: I myself had no experience with programming, so I would be lying if I said I wasn't anxious at the beginning, as I really didn't know anything. With Macnica 's support, we were able to move forward somehow, with a lot of back and forth. A Macnica engineer encouraged me, saying, "The clouds will clear in about three months," and the clouds really did clear. From then on, I was able to think about various things from a system perspective.
As for the accompanying support, we had regular meetings twice a month, one hour each, where they helped us with anything we didn't understand through web meetings. For daily learning, we used the "Plant Simulation" manual created by Macnica as the basis for our learning. When I first saw it, I had no idea what it said, but now I realize that it is a very easy-to-understand manual. Although it is an accompanying support service, it seems to be very cost-effective as an environment where we can learn while having monthly meetings.
Macnica itself has a good understanding of the manufacturing industry, and they respond well when you give them advice. They are also well aware of the market trends for product transportation, and sometimes give us new ideas based on their experience. They even taught me evaluation methods that I had never thought of before, which was very educational.
Kuze: Initially, the factory model was created by Macnica, and the proposal was that we would work together to create it over a one-year training period. They were also flexible in responding to our request to be a "teacher we could ask anything to." It was a pretty unreasonable request, but we are grateful that they were able to put together a support system that met our wishes.
Regarding regular meetings, rather than just blurting out what I wanted to do or how I didn't know how to do it, I communicated my own thoughts and the things I didn't understand in advance, received answers before the meeting, and was able to resolve any issues on the day, which allowed us to use the limited time efficiently.
I want to continue improving my proficiency in "Plant Simulation" while working to create an environment that will connect to the future of factories.
Takai-san: From now on, one person from each of the technical and manufacturing departments will be continuously using "Plant Simulation" to improve their proficiency. The manufacturing department will be using it to make on-site improvements to existing lines, while the technical department will be using it to determine processes while performing numerical evaluations for new lines that are being launched.
Yokokawa: First of all, it is important to move "Plant Simulation" firmly to the implementation stage, and there is a possibility that we will consider linking it with other systems such as manufacturing execution systems in the future. Ultimately, we want to evolve it into a "factory that connects to the future," so if there are any useful solutions, including other solutions that Macnica has, please suggest them and we will make good use of them.
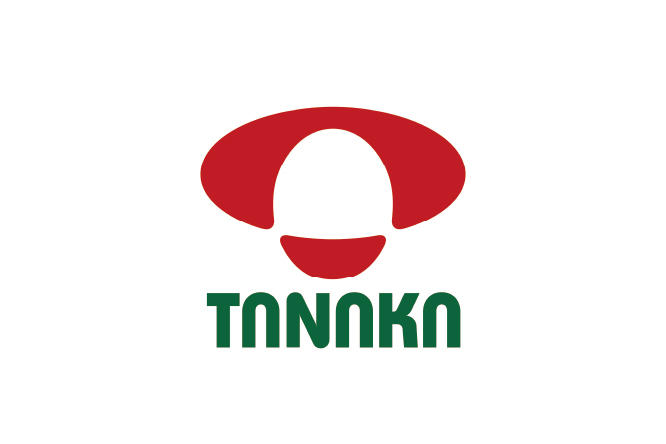
Tanaka Precision Industry Co., Ltd.
- Business
- Automobile parts, motorcycle parts, general-purpose parts, and other manufacturing and sales
- founding
- 1948
- Number of Employees
- Consolidated: 1,242 people Non-consolidated: 391 people (as of March 31, 2023)
- website
- https://www.tanasei.co.jp/
PRODUCT/SERVICE
Click here for products and services related to this case study
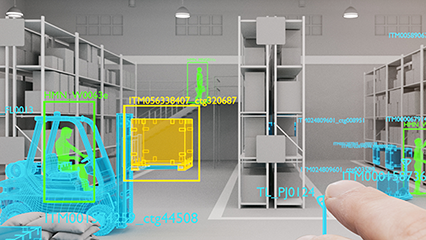
Siemens Plant Simulation "Tecnomatix"
Digital Twin production simulation software
CONTACT
Please feel free to contact us with any inquiries regarding this case study or product implementation.