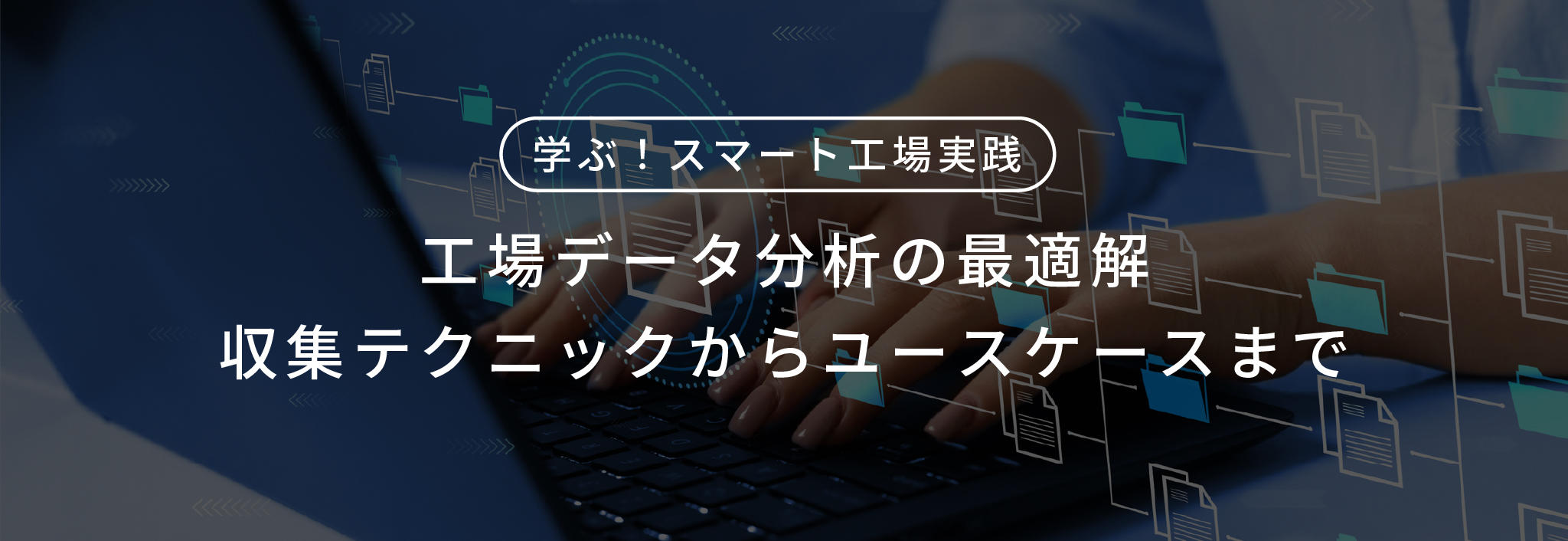
1.データ収集前に知っておきたいこと
工場データ収集において、大切なことは、どのように工場データ活用をしたいかというテーマや課題を明確にしたうえでデータ収集を行うことです。スマート工場やIoTが注目された頃、製造現場では「とりあえずデータ収集して、収集できたデータから課題は何か?を考える」ということが行われてしまっていました。
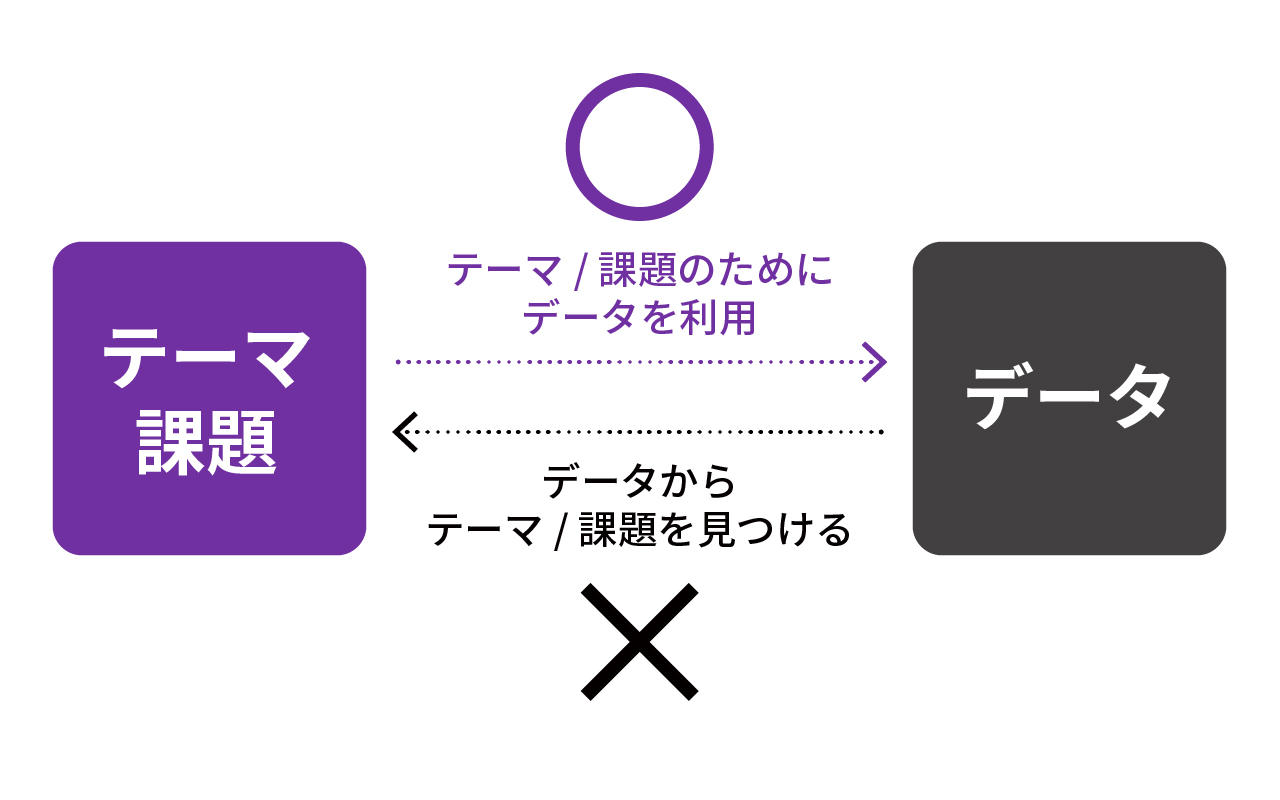
図:テーマや課題からデータへのアプローチの重要性
工場の主な目的は、事業会社の製造プロセスとして「儲かる工場であり続けること」です。そのためには、ロスを顕在化させて撲滅し続ける改善活動を通じて、原価低減・生産リードタイム短縮・資本回転率の向上を実現することが至上命題になります。具体的に製造プロセスにおけるロスは、公益社団法人日本プラントメンテナンス協会により提唱されています。
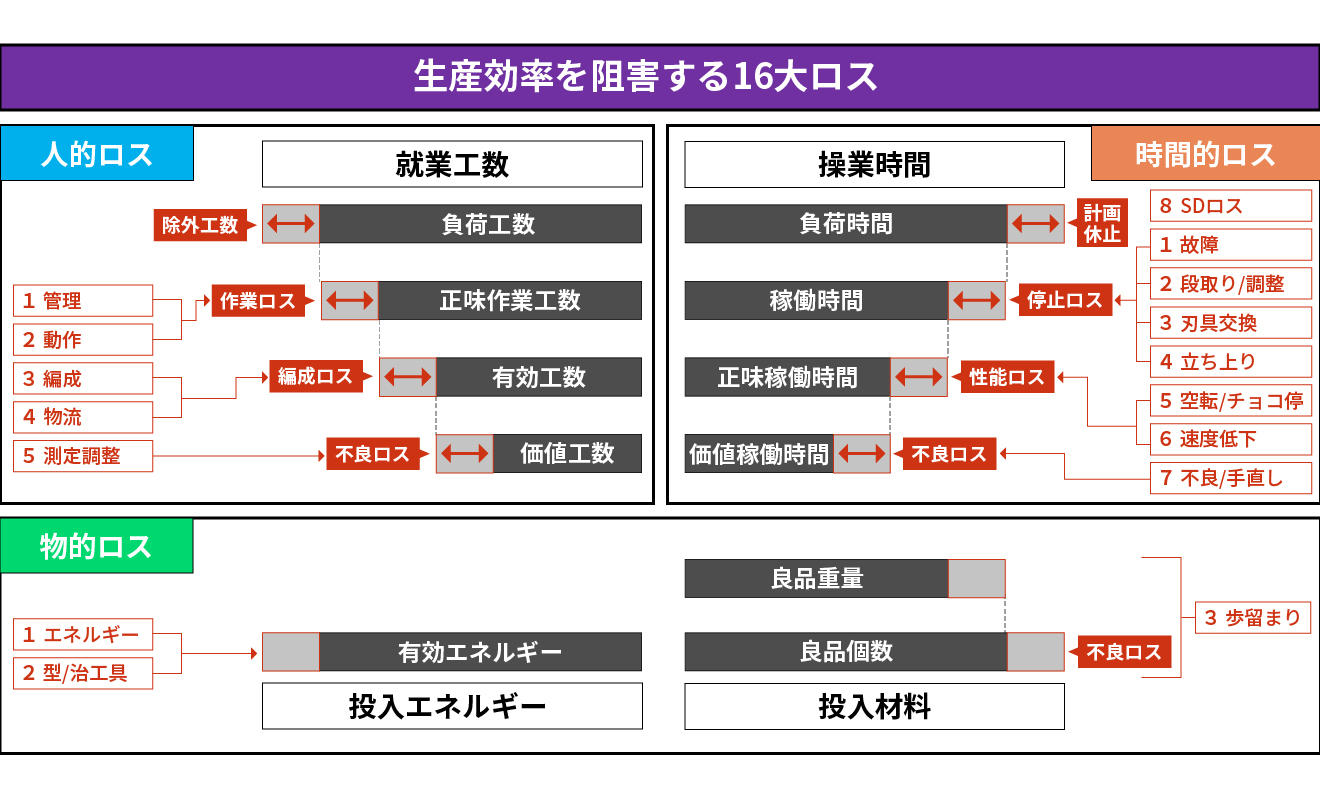
図:公益社団法人日本プラントメンテナンス協会提唱16大ロス
2.工場データ活用の難しさ ~製造現場の多様性~
しかしながら、そうはいっても工場データ収集~活用は困難です。
2011年のドイツ政府が提唱したインダストリー4.0をきっかけに、様々な企業の生産現場でデータ収集が活発化しましたが、なかなかうまくいかず苦労した経験がある方も多いのではないでしょうか?
その難しさの原因は「製造現場の多様性」にあります。製品・設備・データ項目は多種多様で、非同期に発生し、さらに設備メンテナンスなどを通じて変わってしまいます。
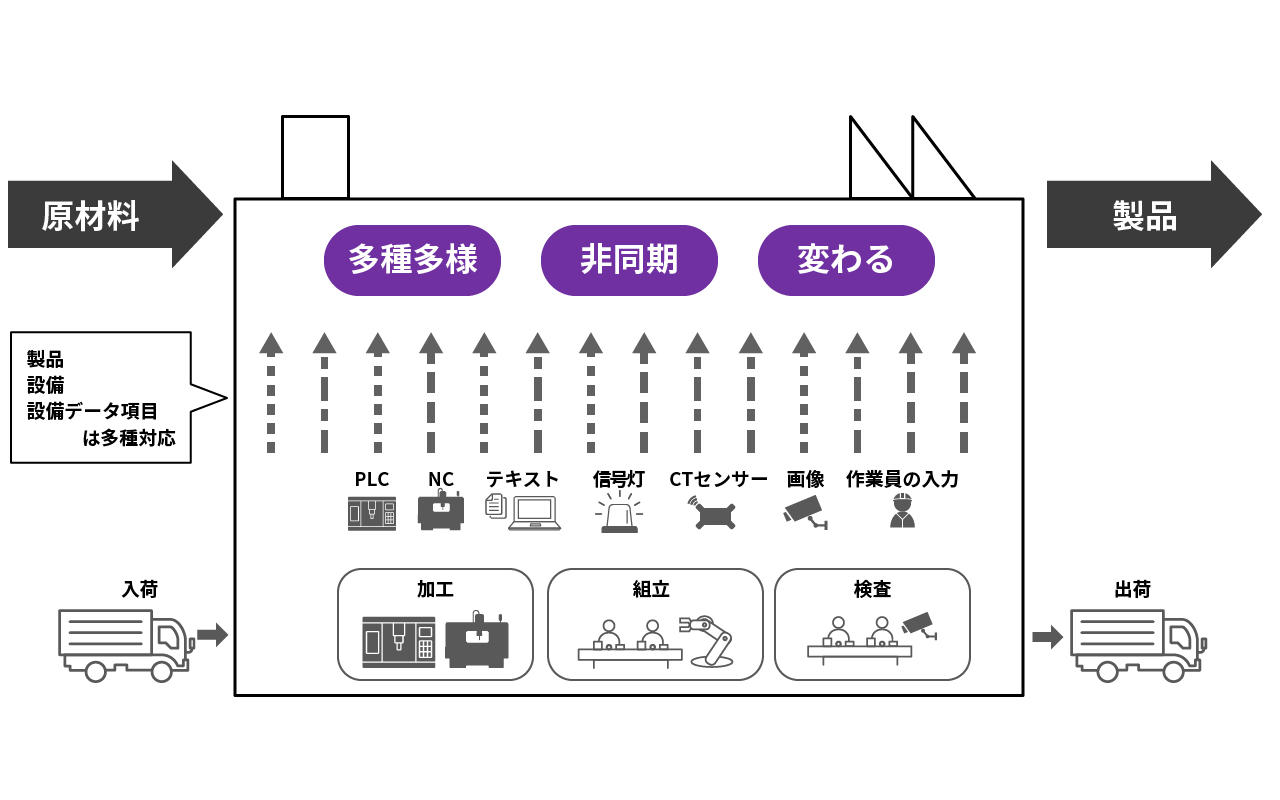
図:製造現場の多様性
実際に製造現場のデータ活用のために、PLCや信号灯などの設備からデータを収集した経験のある方は多いのではないでしょうか? また、それらの設備からデータ収集が可能な工程は比較的容易で多くの方が取り組んでおり、それ以外の工程のデータ収集が難しく苦労されているのではないでしょうか?
3.工場データの分類
マクニカでは様々な業種や工程での工場データ活用を通じて、そういった多種多様な生産現場を捉えながら、製造における主体(設備/作業者)や、設備の種類(新しい/古い)が異なる場合でも、共通化された考え方を確立し、その基準に則ってデータを収集することが重要だと考えています。そして、そのデータをインプットとして、データを標準化し蓄積することで、工場全体を俯瞰的に捉えた精度の高い分析や予測といったデータの活用が可能になります。
ここからは、工場のデータを特性に応じて分類してみたいと思います。前述した通り、設備主体/作業者主体の製造ラインの分類ができます。
設備主体の場合
新しい設備であればPLCや信号灯からデータ収集が可能ですが、古い設備(イーサネット通信に非対応など、データ収集困難な設備)の場合、機械の信号を設備の改造によって収集する、または後付センサーをつけてデータを収集するといった方法が考えられます。古い設備はデータ収集の難易度が高くなります。
作業者主体の場合
そもそもデータソースが存在しないため、作業者が状況入力するなど何かしてもらう必要が出てきてしまい、データ収集に伴う製造現場の負担が増します。
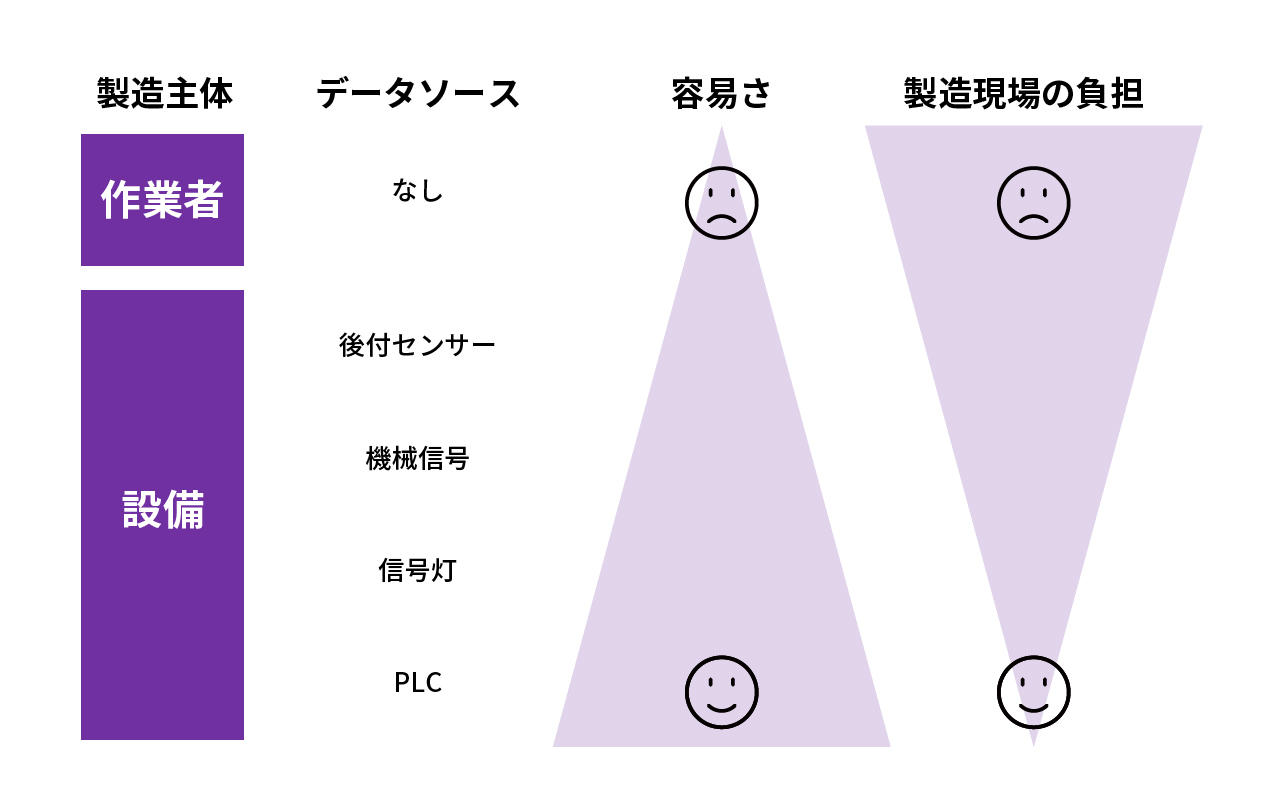
図:工場データ 収集の容易さと現場の負担の関係
近年、作業者主体の製造ラインにおいてもロボットや搬送機を活用した自動化の検討進められている場合もあります。しかし、多種多様な消費者需要への対応が求められる中で、柔軟性が高い作業者主体のラインを維持することが、製造業の強みとなることもあり、簡単に設備化が進まない現状があります。
4.工場データ収集のアプローチ手法
こうした生産現場のデータ収集では何を意識すべきでしょうか?
マクニカが今まで取り組んだアプローチ手法をご紹介します。
新しい設備の場合
PLCや信号灯といった設備データの収集は、マスターPLCやロガー、IoTゲートウェイといったツールを活用すれば、数十万円で複数の生産ラインに対して実現できます。
古い設備や作業者主体の場合
・設備を改造し、古い機械のアナログ信号データの収集を行う
・新たなセンサーを設置し計測データの収集を行う
・生産現場にスイッチやカードを配置して作業者の操作によりデータ収集を行う
・タブレット(電子帳票ソフトなど)にアプリケーション入力されたデータ収集を行う
・作業者がIT機器を活用した音声登録を元にデータ収集を行う
・作業者にウェアラブルデバイスやビーコン(通信端末)を保持させ位置情報から作業状況判定のデータ収集を行う
・作業動作をカメラで撮影し、その動画のAI解析により作業状況判定のデータ収集を行う
これらのアプローチを実施する際には、現場の具体的な状況やニーズや制約に応じて最適な方法を選択することが重要です。
5.工場データ収集において押さえるべきポイント
次に、様々なアプローチがある中で、最適な方法をどのように選択すればよいのでしょうか?
押さえるべきポイントは「信憑性の高いデータ」と「データ収集にかかるコスト」です。
信憑性の高いデータ
精度の高い分析には信憑性の高いインプットデータが必要です。比較的新しい設備データは生産機械そのもののデータであるため虚偽のデータが含まれる可能性が低く信憑性が高いデータといえます。
一方、古い設備や作業者主体の製造ラインでは、データ収集に工夫を要します。そのため、無理に設定した判定基準に則った不確実なデータとなることが多く、そのようなデータを収集しても意味がありません。
信憑性の高いデータを収集することは、データ収集を開始する際に必ず意識していただきたいポイントです。
データ収集にかかるコスト
次に、データ収集にかかるコストの問題についてです。データ収集に高額な予算が認められるケースは、最新技術の調査を兼ねた試験フェーズであることが多いです。試験が通り、いざ工場全体に導入して工場データを収集しようとなると、投資対効果が求められてしまいます。1ラインに数十万円を超えた投資は受け入れられないこともあり、そこで立ち止まってしまうことが多いため、現実的なコスト感で進めていくことも意識していただきたいポイントです。
工場データの収集を考える際には、データの信憑性とコストを意識しながら、現実的に検討を進めていくことが重要です。
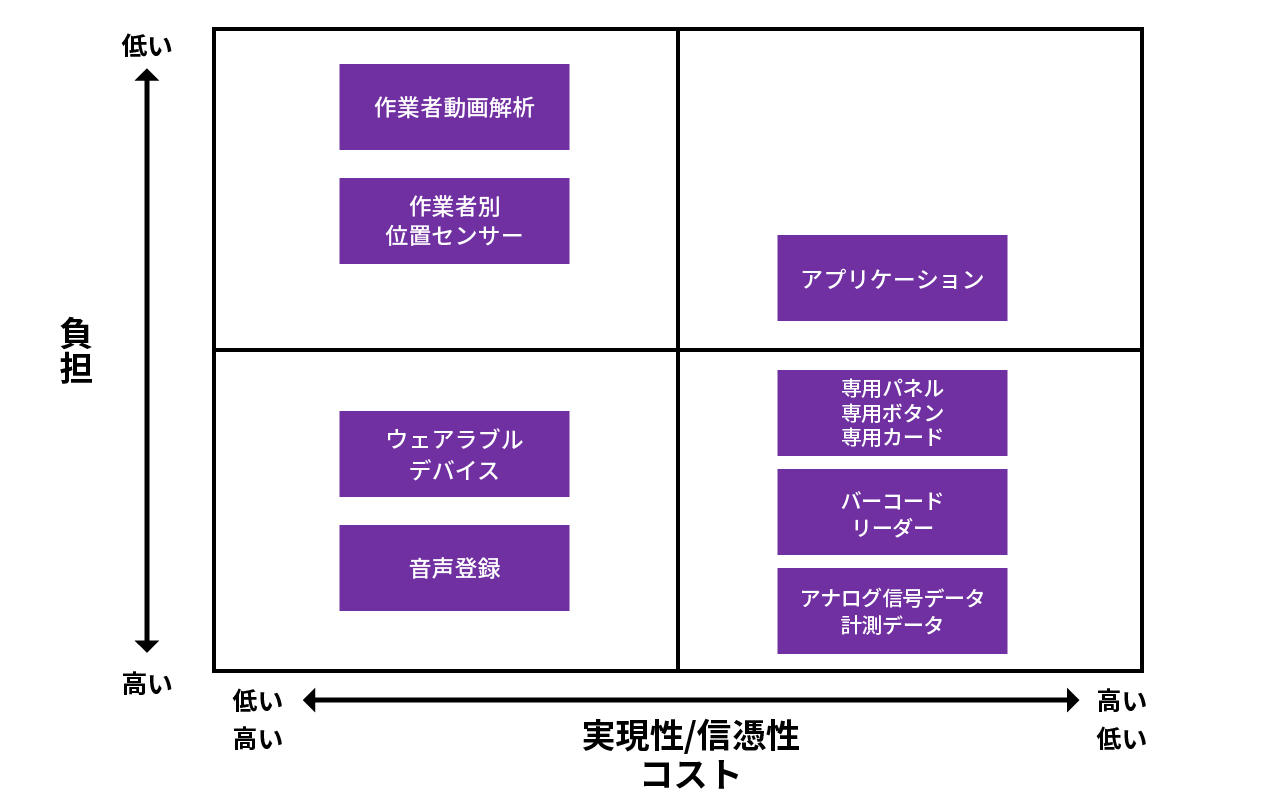
図:古い設備や作業者主体の工場データ収集検討例
6.工場データ分析のユースケース
このように多種多様な生産現場を捉えながら、製造における主体(設備/作業者)や、設備の種類(新しい/古い)が異なるとしても、共通化された考え方を確立し、その基準に則ってデータを収集することが重要です。一方で、データ収集そのものは手段にすぎず、工場データを活用できることが何もよりも大切です。この章ではデータ活用分析のユースケースをみていきます。
工場データ分析には、一見すると様々な種類があるように思えるかもしれませんが、実際には数えられる程度の種類しかありません。蓄積されたヒストリカルデータを基に実情を把握して原因を追及する分析と、リアルタイムで収集される工場データを基に現状をいち早く察知して対応を行う監視の2種類に過ぎないのです。
※関連資料※
【ホワイトペーパー】この2種類をさらに分けた9種類のデータ活用ユースケースについてはこちらをご覧ください
テーマ | 概略 | 作業者 | リーダー | 保全/検査 | 生産技術 | 生産管理 |
---|---|---|---|---|---|---|
ヒストリカル | 日別ラインの実績値を定量的に把握する | - | 〇 | - | 〇 | - |
素養値を下げるロス(要因)を設定する | 〇 | 〇 | - | 〇 | - | |
要因を引き起こす原因(因子)を特定する | 〇 | 〇 | - | 〇 | - | |
異常発生時に日報、検査記録などを参照する | 〇 | 〇 | 〇 | 〇 | - | |
ある製品をあるラインで製造した場合の実績値を把握する | - | 〇 | - | 〇 | 〇 | |
リアルタイム | 設備がどれだけ生産したか、稼働しているかを表示する | 〇 | - | 〇 | - | 〇 |
生産指示に対する現状の生産進捗度合いを表示 | - | △ (製造エリアが広い場合) | - | - | 〇 | |
設備停止情報/停止継続時間を表示 | △ (製造エリアが分かれている場合) |
△ (製造エリアが広い場合) |
〇 | - | - | |
設備情報や品質異常を引き起こす因子(製造値/検査値)を表示 | △ (製造エリアが分かれている場合) |
△ (製造エリアが広い場合) |
- | 〇 | - | |
スタッフ空き状況 | 保全や検査のスタッフが空いているかどうかを表示 | 〇 | - | - | - | - |
図:生産現場のデータ活用のユースケース
7.最後に
工場データ活用において一番大切なことは、こういったデータ収集やデータ活用を通じて、より良い姿を目指して改善活動推進することです。
このブログでは、データ収集に課題を抱える製造業のみなさま向けにマクニカの経験を整理してまとめております。
関連動画
多種多様な生産現場に対して、最適なデータ収集方法をご提案しております。
およそ10分でわかる参考動画もございますので、ぜひご視聴ください。
「多種多様な生産現場 どうするデータ収集!」
「DSF Cyclone」は製造実績と生産計画を構造化されたデータでつなぎ「生産性の高い工場」を実現する製造実績システムです。ご興味のある方はこちらもご参照ください。