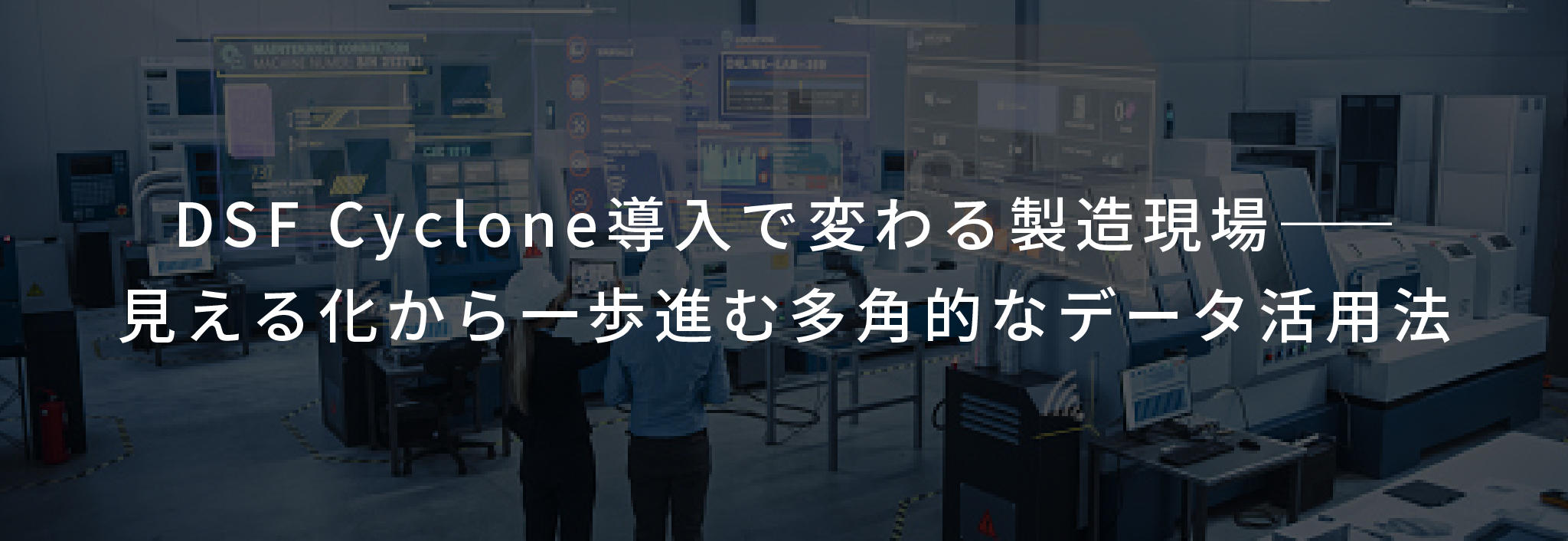
よくあるスマートファクトリー化の壁――「見える化」だけで終わっていませんか?
製造現場でのスマートファクトリー化は、多くの企業が着手している重要なプロジェクトです。特に設備の稼働状況をリアルタイムで監視し、データの「見える化」を進めることで、現場の状況が一目でわかるようになるといった取り組みは、効率化の第一歩として注目されています。製造ラインの稼働率、停止時間、停止理由を把握し、それに基づいて現場を改善するというアプローチは、多くの現場で導入が進んでいます。
しかし、ここで多くの製造現場が一度立ち止まってしまうことがあります。それは、「見える化」は問題を発見するのには有効ですが、それだけでは生産ラインの本質的な問題へのアプローチは難しいからです。設備の稼働データをリアルタイムで可視化できるようになったとしても、そこから得られるのは「結果」であり、「原因」ではありません。たとえば、なぜそのラインが頻繁に停止するのか、その停止が生産全体にどのような影響を与えているのかを解明するためには、さらなるデータと分析が必要です。
設備データだけでは解決できない「見えない問題」
設備データを集め、見える化することで、「今、どの設備がどれだけ稼働しているのか」「どの設備が停止しているのか」「停止の原因は何か」といった情報を取得することはできます。具体的には、以下に示したような月別停止ロス比較や週別停止ロス比較、日別稼働率推移、ロス理由別停止時間比較、停止理由別パレート図、停止時間の分解ツリーといったグラフを使用することで、設備の稼働状況や停止要因を視覚的に把握でき、現場の全体像を確認することが可能です。
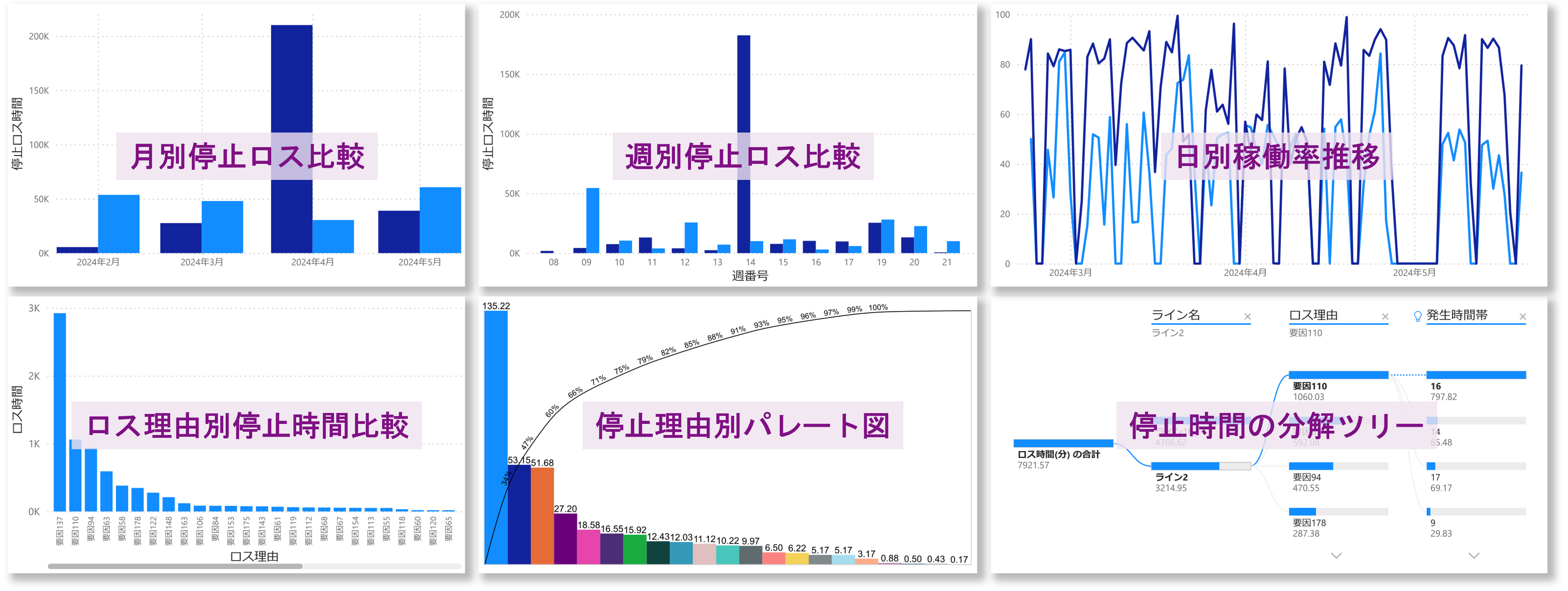
設備データを用いたグラフ例
しかし、これだけでは現場の本当の課題を解決できません。なぜなら、設備の稼働状況は単なる「表面的な現象」にすぎず、停止の根本原因や生産全体に与える影響については明らかにならないからです。
たとえば、ある生産ラインで頻発する停止があったとします。この停止は設備の故障やメンテナンス不足が原因かもしれませんが、それだけが理由ではなく、生産計画の変更や作業者の操作ミス、さらには材料供給の遅れなど、さまざまな要因が絡み合っている可能性もあります。
設備データだけでは、こうした複雑な原因をすべて把握することはできません。現場の課題を根本から解決するためには、単に設備の状態を監視するだけでなく、設備データと他の生産データを連携させた「多角的な分析」が必要です。
停止時間と停止要因データの限界
・製品ごとの停止要因の分解が難しい
製品特有の停止要因を特定するには、設備データだけでは足りません。製品ごとに発生する停止要因は異なり、それを特定するためには日報や作業オペレーションとの突き合わせが必要です。これにより、分析が複雑化し、現場での対応が遅れることがあります。
・生産計画時間とのズレを特定しにくい
実績時間が生産計画よりも長い場合、何が原因で計画から逸脱しているのかを特定するのは容易ではありません。停止要因が絡んでいる可能性もありますが、生産の開始時刻や終了時刻と照合しなければ、そのズレの正確な原因を特定することは困難です。
・設備やラインの生産標準時間に対する適正性の確認が不足
各ラインや設備が、その標準的な生産能力に対して適切に稼働しているかを評価するためには、標準時間との比較が不可欠です。これを行わなければ、見かけ上稼働していても、実際には無駄が発生していることがあります。
多角的なデータ分析で見えない課題を解決
このように、停止時間や設備データだけでは限界があることがわかりました。では、どうすれば本当の課題を解決できるのでしょうか? その答えは、多角的なデータ分析にあります。生産指図書や生産計画、品質データといった他のデータと設備データを統合して分析することで、根本的な課題を発見し、真の改善が可能となるのです。
正規化データの力――DSF Cycloneが生み出す本当のカイゼン
その多角的なデータ分析を支えるのが、「DSF Cyclone」です。DSF Cycloneは、単に設備の稼働データを収集するだけでなく、生産指図書や生産計画、品質データなど、工場内で生成されるあらゆるデータを正規化し、一元的に管理します。この「正規化データ」によって、設備の稼働状況だけでなく、製品ごとの生産実績、品質の変動、そして生産計画とのズレを詳細に把握できます。
たとえば、特定の製品があるラインで生産される際に不良品が多発する場合、DSF Cycloneを使えば、その製品がどの設備で、いつ、どのような条件下で生産されたかを詳細に分析できます。他の製品や他の生産ラインとの比較も容易になり、根本的な原因を特定できます。これにより、単なる設備の修理やメンテナンスに留まらず、生産計画や作業手順そのものを見直すという、より効果的なカイゼン策を立てることが可能です。
下記の図は、設備データと正規化データの違いを示しています。従来の設備データは、単に設備の稼働状況や停止理由を可視化するにすぎませんが、DSF Cycloneによって正規化されたデータは、指図書番号や標準生産時間、製品ごとの詳細な情報、さらには休止や保全作業のタイミングも統合されます。これにより、単なる「現象」を超えて「原因」まで掘り下げた分析が可能となり、より深い問題解決を実現します。
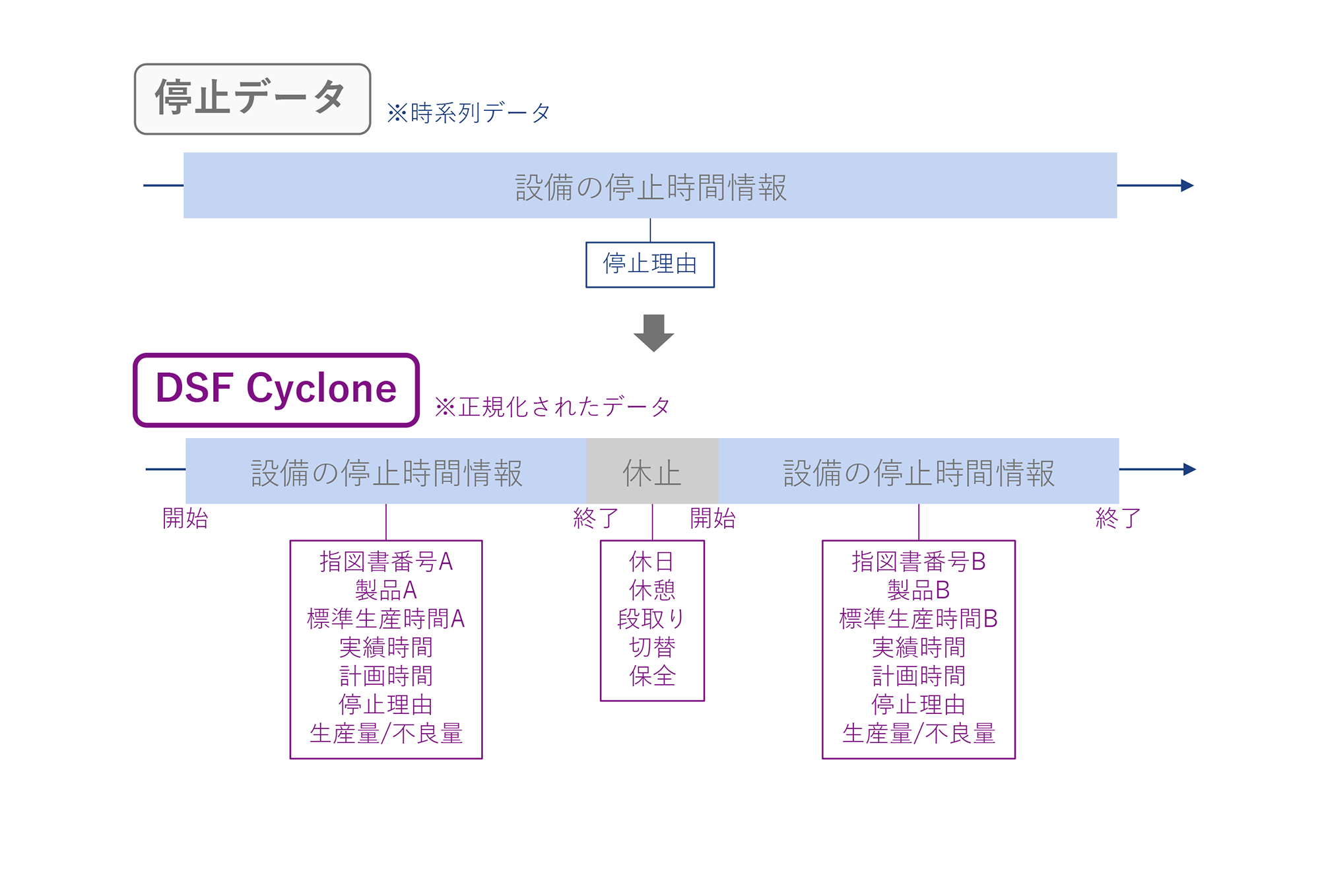
設備データとDSF Cycloneデータとのデータ構造比較
下記の表は、設備データとDSF Cycloneの正規化データとの「分析軸」の違いを示しています。分析軸が多いことで、より詳細な分析を行えます。
分析軸 |
設備データ |
DSF Cyclone |
---|---|---|
ライン |
〇 |
〇 |
設備 |
〇 |
〇 |
停止時間/回数 |
〇 |
〇 |
停止理由 |
〇 |
〇 |
生産計画時間 |
〇 |
〇 |
標準生産能力値 |
― |
〇 |
生産製品 |
― |
〇 |
製造指図書 |
― |
〇 |
実績生産時間 |
― |
〇 |
生産量/不良量 |
― |
〇 |
シフト |
― |
〇 |
保全記録 |
― |
〇 |
サイクル停止情報 |
― |
〇 |
DSF Cycloneが提供する具体的なメリット
DSF Cycloneの導入によるメリットは以下の通りです:
1.停止原因の多角的分析
設備の停止原因を生産指図書や品質データと照合し、背後にある根本的な原因を特定できます。これにより、単なる設備の修理ではなく、全体の改善に繋がる具体的なアクションを計画できます。
2.生産計画の最適化
リアルタイムで取得された生産データを基に、生産計画を最適化することができます。計画と実績の差異を把握し、適切な調整を行うことで、生産効率の向上を実現します。
3.品質改善と不良品削減
設備の稼働状況と品質データを関連付けて分析することで、どの設備や工程が不良品の発生に影響を与えているかを特定し、品質改善に向けた具体的なカイゼンを進めることができます。
DSF Cyclone導入による具体的な分析例
1.指図単位での停止時間分析
製造指図番号に対して停止時間を集計し、製造指図番号ごとの停止時間のばらつきを把握できます。
週ごとに製造指図番号別の停止時間を比較し、生産の安定度を確認することで、改善策を迅速に検討できます 。
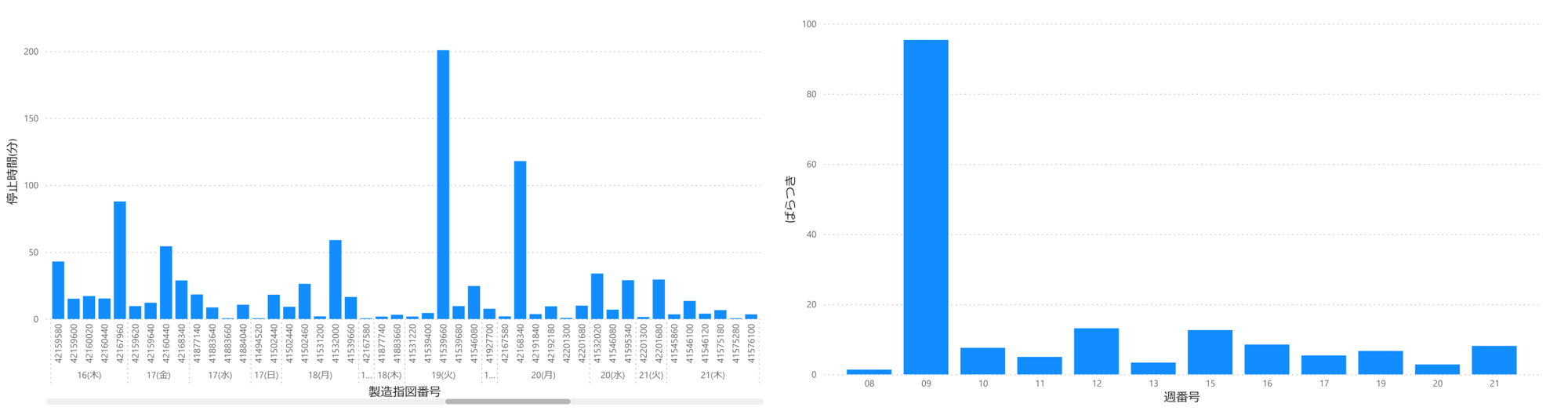
2.生産日単位での停止時間分析
停止時間を生産日単位で集計し、さらに製品ごとに凡例を加えることで、どの日にどの製品が停止時間を多く発生させているのかを特定できます。
これにより特定の日や製品の異常を把握し、対応策を講じられます 。
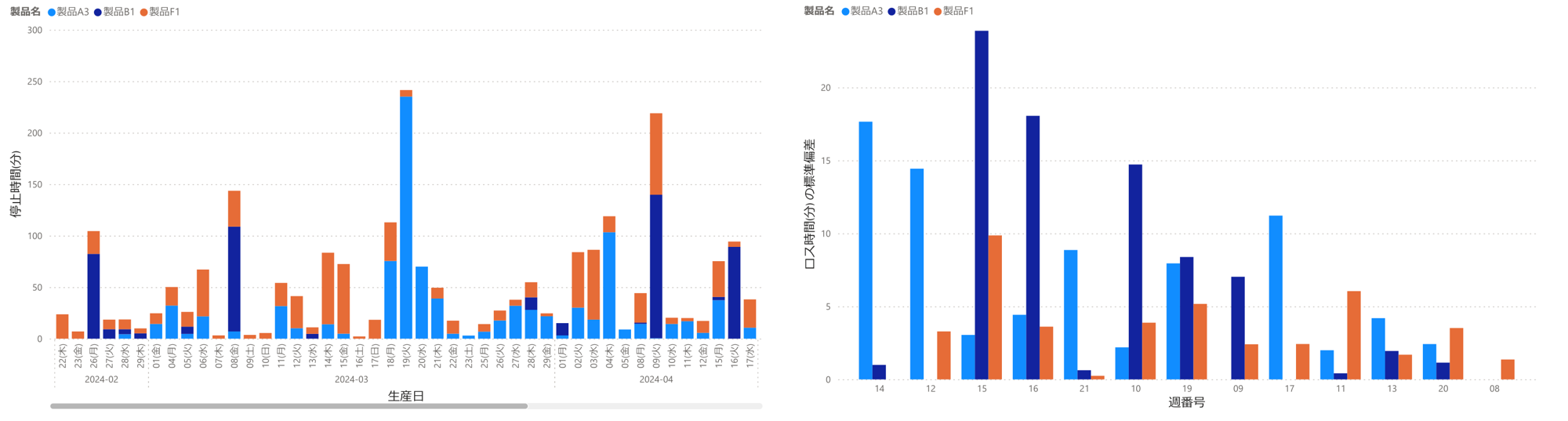
3.指図単位での停止理由別停止時間の比較
各製造指図番号に停止理由別の時間差を分析することで、特定の製造指図番号が他の製造指図番号よりも長時間の停止を引き起こしている原因を特定し、対策を講じることができます 。
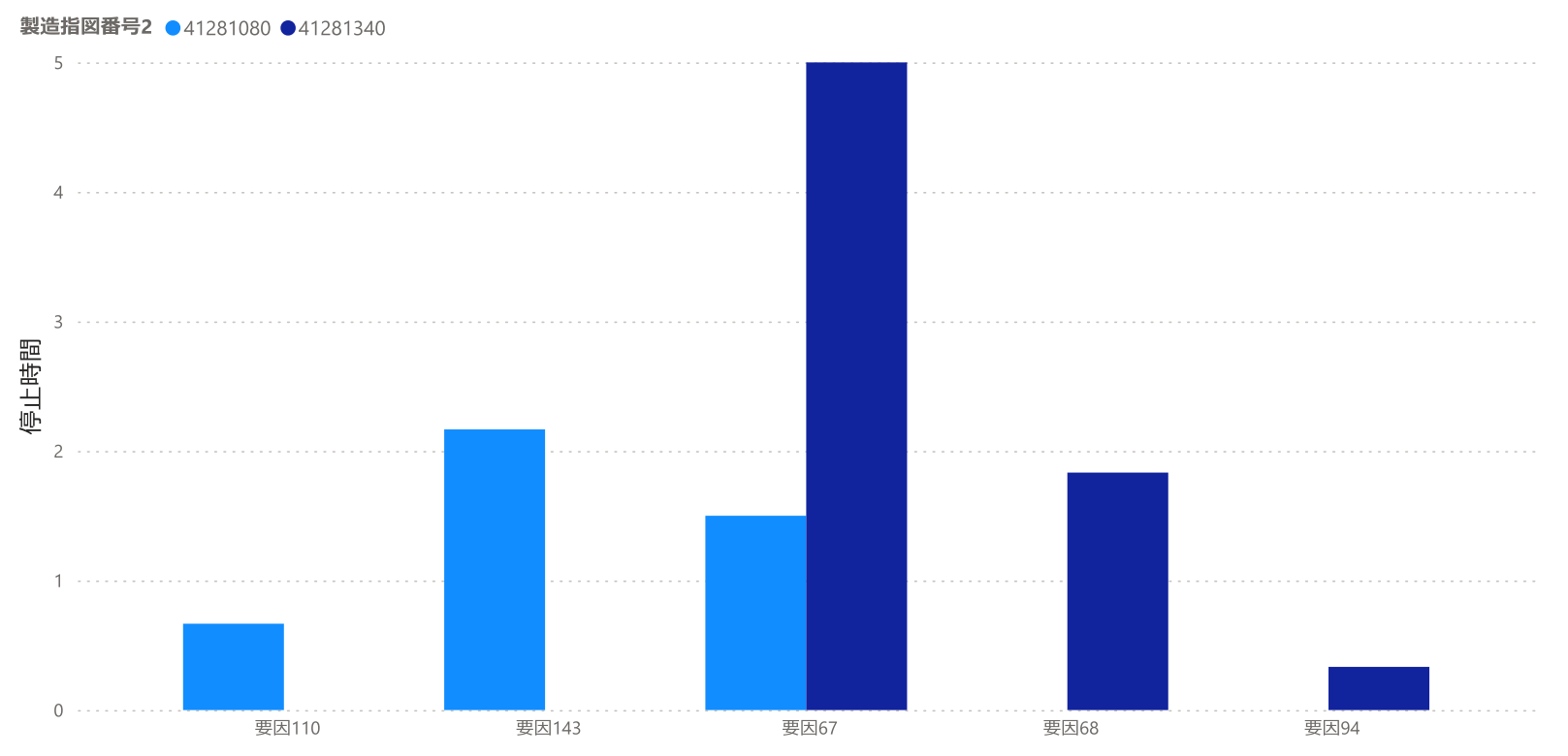
4.製品単位でのロス理由別停止時間の比較
特定の製品における停止理由ごとの時間を比較することで、その製品が他の製品よりも長い停止時間を必要とする場合、その原因を探り改善策を検討できます 。
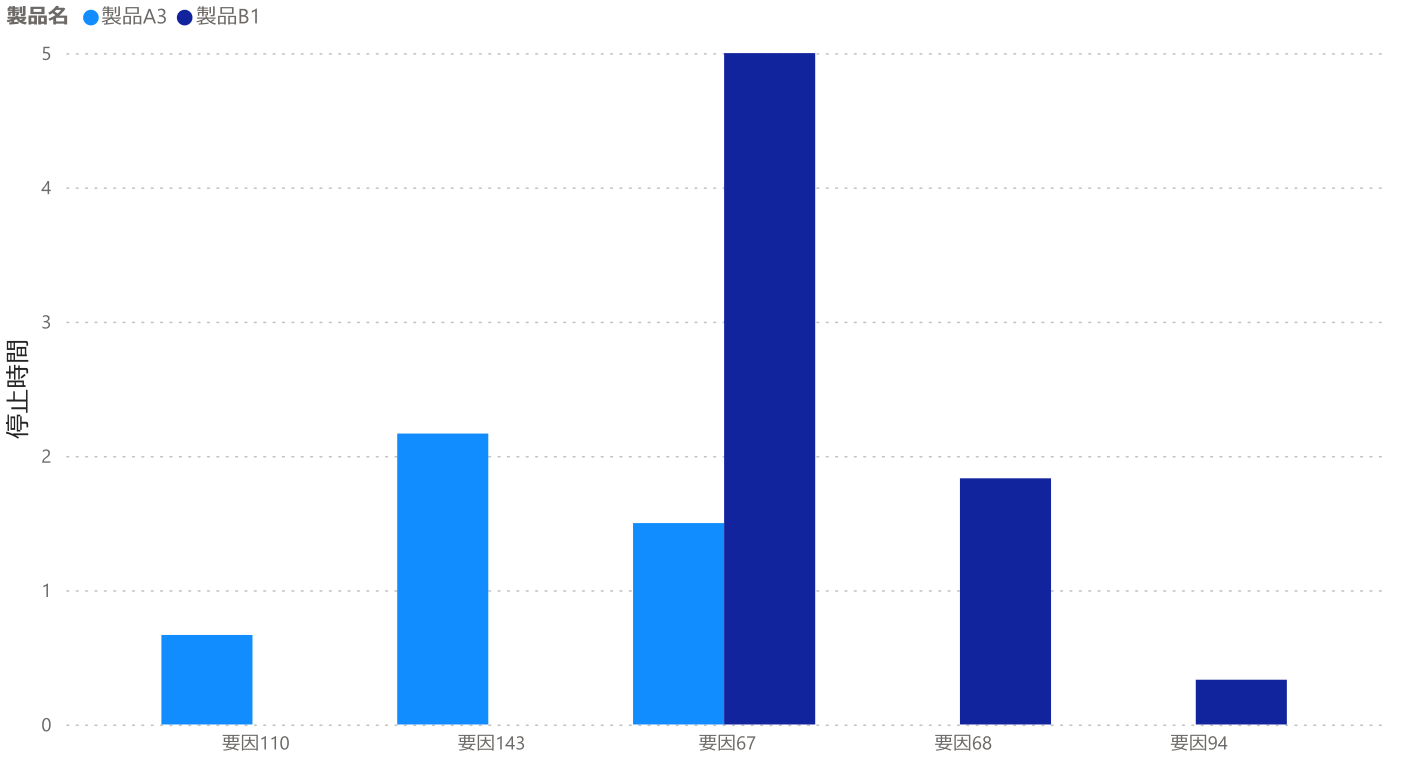
5.製造指図番号や製品などを含めた分解ツリー
設備だけでなく、指図番号や製品などの要素も含めた分析が可能です。これにより、停止の原因をより詳細に分析し、改善策を見つけ出せます。
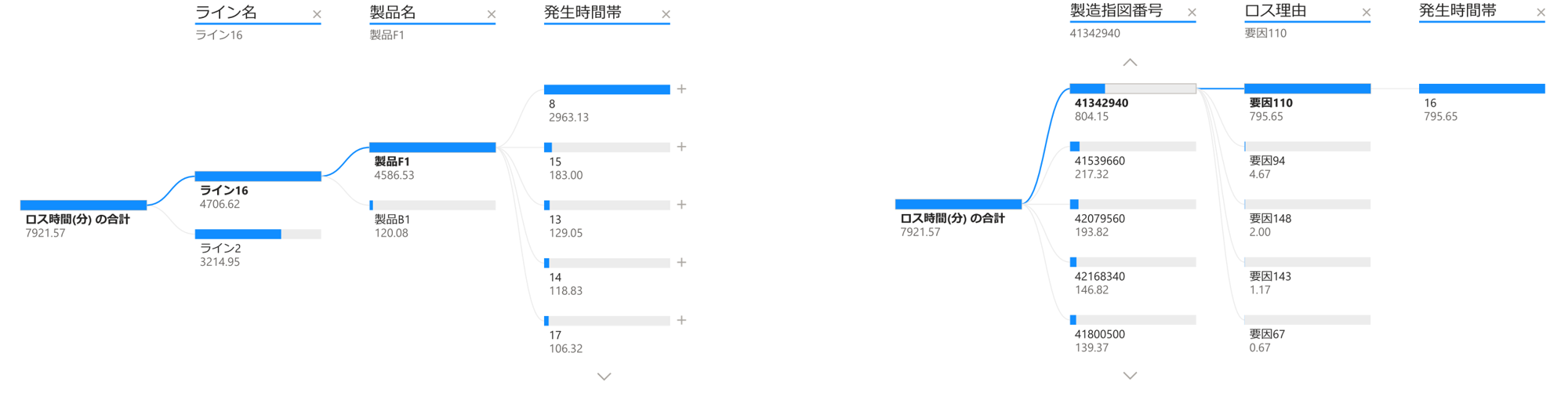
6.停止時間と生産量や稼働時間での相関分析
停止時間に対して生産量や稼働時間で相関を確認することで、異常に停止時間が長い指図番号や生産の時間帯、製品などを特定し、対策を講じられます。
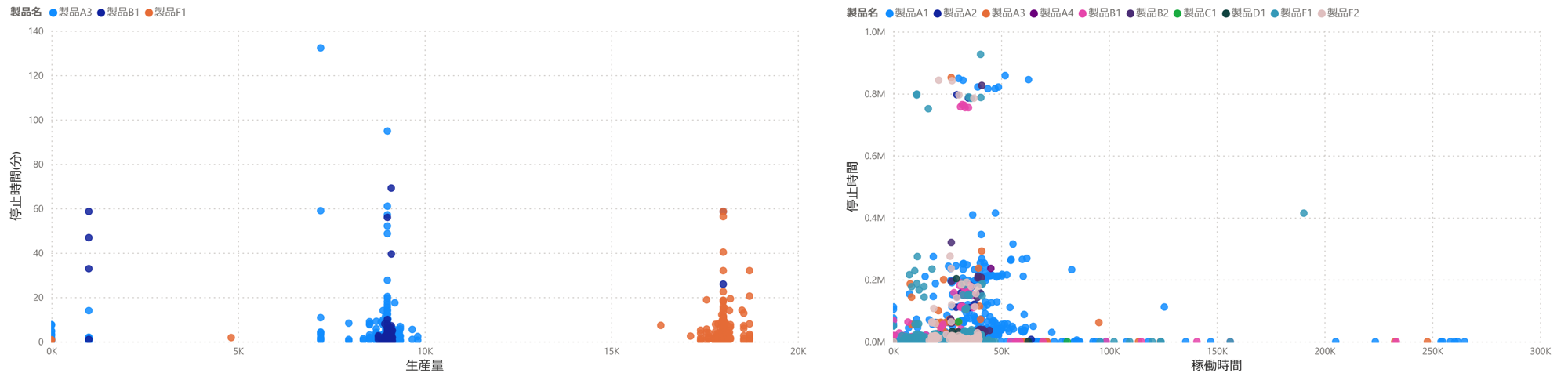
7.生産計画時間と実績時間の差異分析
計画された生産時間と実際の生産時間の差異を分析することで、生産のズレが発生している箇所を特定できます。計画から大きく逸脱している場合は、計画そのものを見直す必要があります。
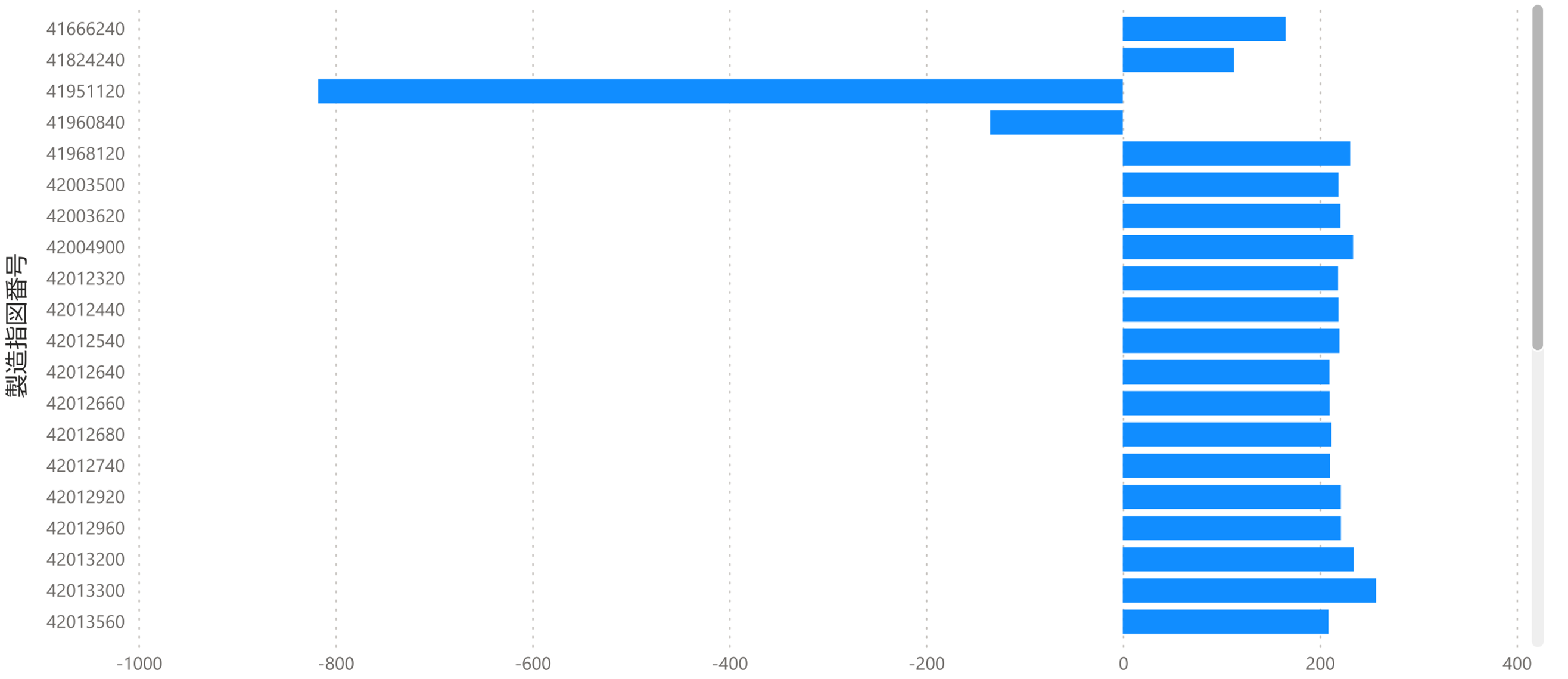
8.標準生産能力に対する実績の比較
ラインごとに定められた単位時間あたりの生産量を実績と比較することで、生産効率を測定します。これにより、保全活動や標準時間の見直しが必要な箇所を特定できます 。
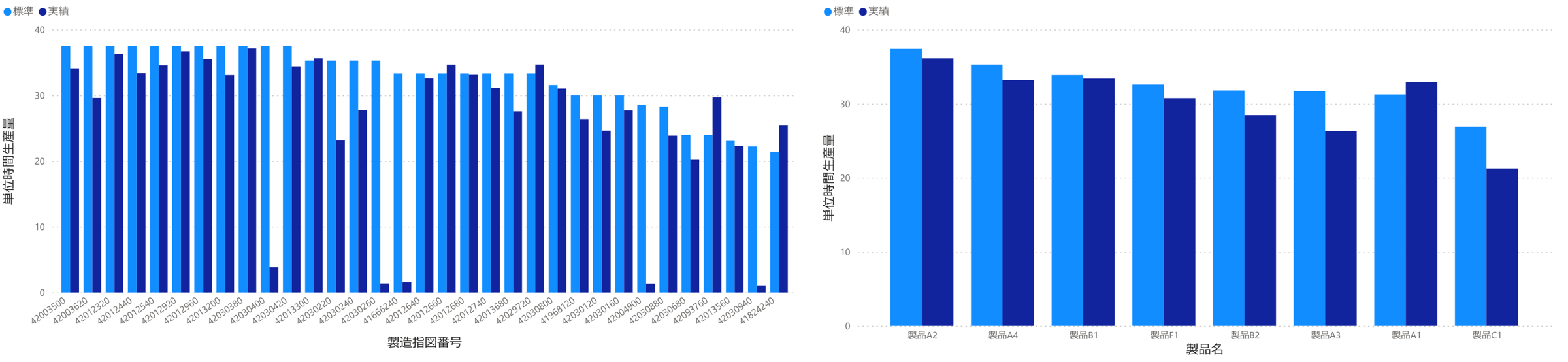
まとめ:見える化を超えて、データドリブンのカイゼンを実現
製造現場の「見える化」は、カイゼンのスタート地点です。しかし、見える化だけで終わっていては、本質的な改善にはたどり着けません。DSF Cycloneを活用することで、見える化されたデータをもとに、設備データ、生産指図書、品質データなどを正規化し、現場全体を俯瞰しながら詳細な分析が可能となります。
結果、単なる設備の改善に留まらず、生産計画の最適化、不良品削減、さらには製造全体の効率化に向けた一貫した改善活動を推進できます。AI技術や自動化との連携も視野に入れ、現場の未来は今、ますます広がっています。DSF Cycloneは、あなたの生産現場に革新をもたらします。