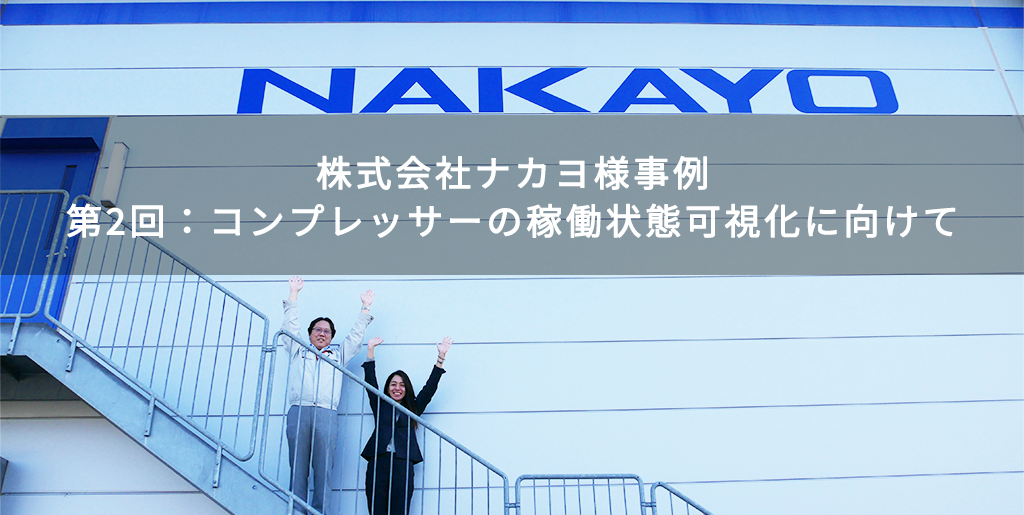
無線センサーで各箇所のエアーの供給状態データを取得
―課題解決のため、どのように取り組んだか教えてください。
小林様:まず、エアーの供給状態を正しく監視したいと思いました。遠隔からでもリアルタイムにデジタルでデータを見られるようにすることから始めようと思いました。
そこでマクニカさんへ相談しました。
―マクニカに依頼した理由を教えていただけますか?
茂木様:マクニカさんは半導体やネットワーク・セキュリティ関連商品を取り扱う商社で、私たちとは昔から取引がありました。
お付き合いしていく中で、製造業向けにIoTとAIのソリューションやサービスを提供していると聞き、相談することにしました。
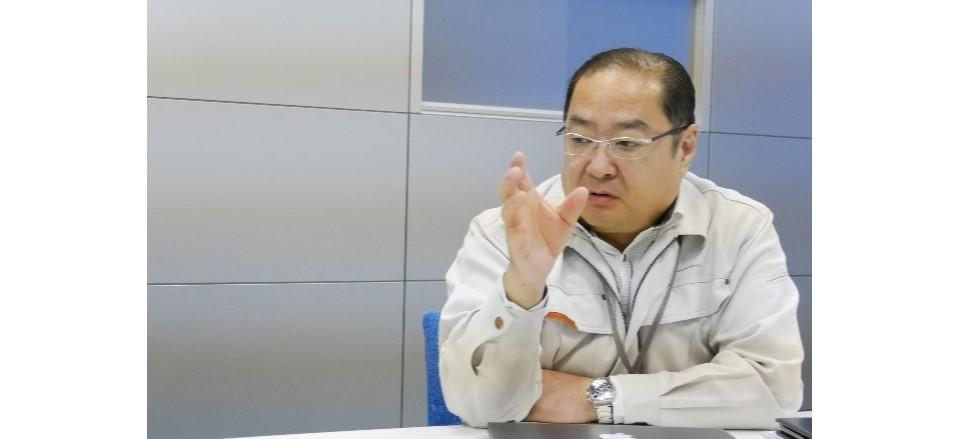
茂木様
小林様:まずは何のデータを取ればエアーの供給状態がわかるか検証しなければなりませんでした。
センシングノウハウを持っているマクニカさんに相談しながら、圧力と流量を見ることで状態がわかるだろうと仮説を立て、圧力センサーと流量センサーを取り付けることにしました。
センサーの設置個所は私のほうで決定し、各箇所に適したセンサー選定とデータの可視化はマクニカさんに依頼しました。
―センサーの取り付け箇所や構成を教えてください。
今回は射出工程でデータを取得することにしました。成形機の稼働中はエアーが使用されること、清掃用にエアガンがついていたこと、圧力センサー、流量センサーが設置しやすかったためです。
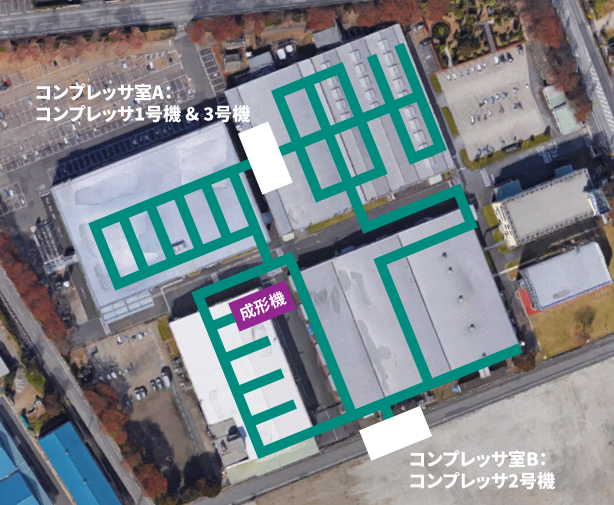
▲コンプレッサー室と工場へのエアー配管図
圧力センサーはエアーの配管に4か所取り付けました。
図を見ていただければわかるように、成形工程建屋内の1階と2階への分岐個所、1階にある成形機の手前、2階へ向かう途中、2階のエアガンのすぐ手前に設置して使用量を測定しました。
流量センサーは3か所で、1階の成形機稼働用の個所、成形機に付随しているエアガンと2階のエアガンのすぐ手前に設置しました。
成形機稼働のタイミングを取得するため、機械稼働信号も取得できるようにしました。
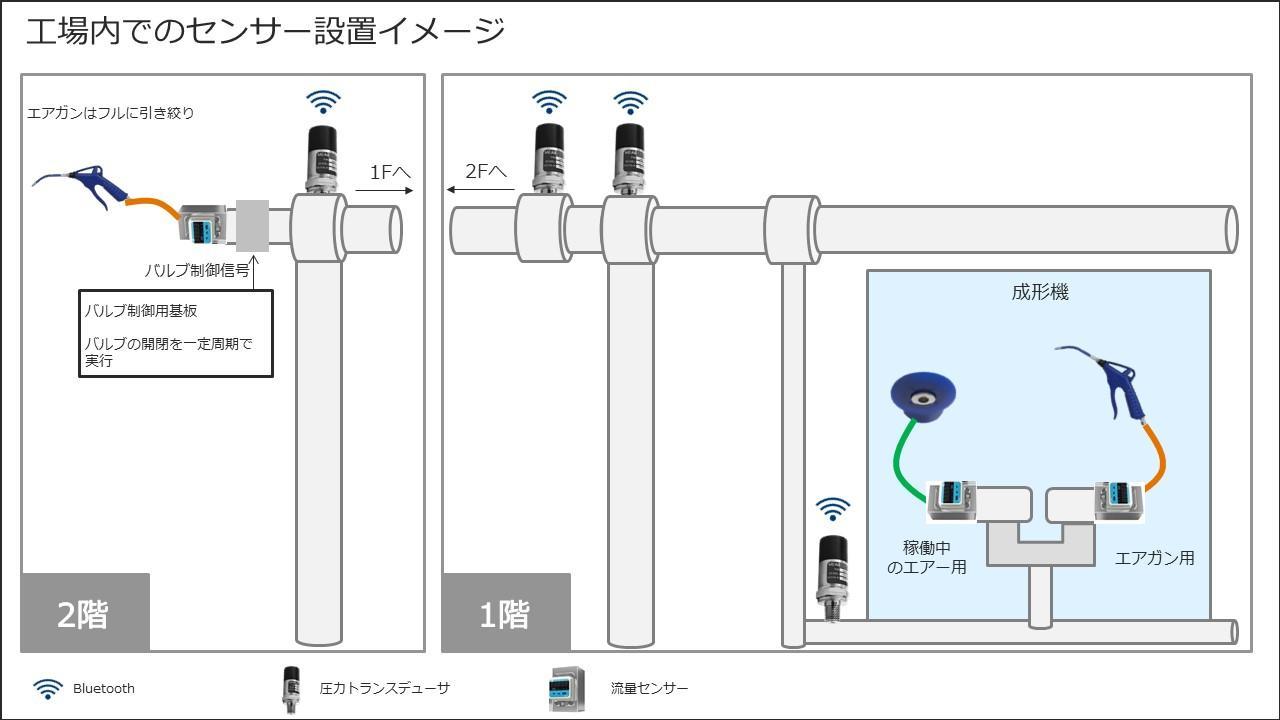
▲工場内でのセンサー設置イメージ
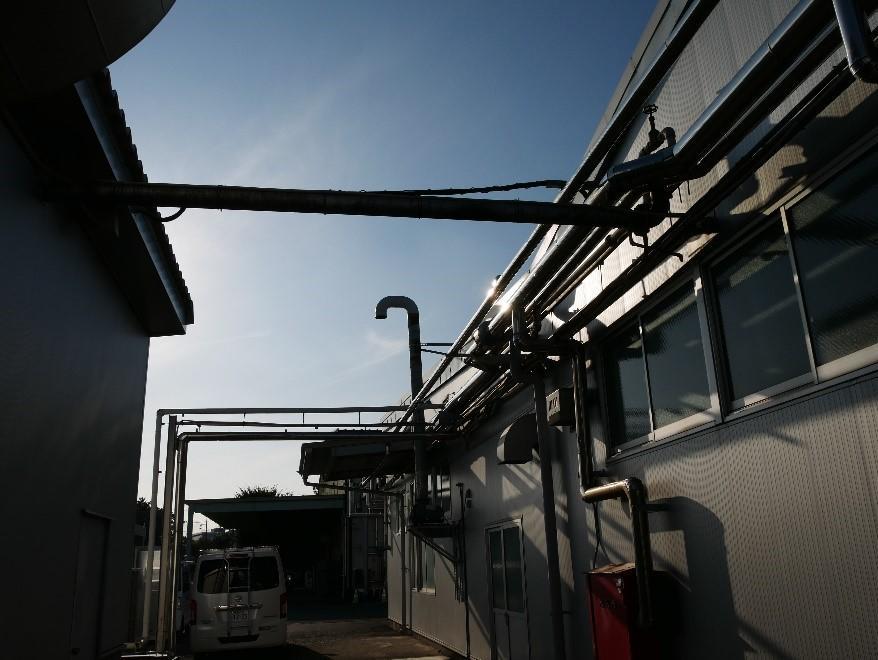
▲コンプレッサー室からのびるエアー配管
―無線タイプのセンサーを採用された理由を教えていただけますか?
小林様:工場内で階が分かれていることもあり、有線の場合は何百メーターも配線させなければならず、現実的ではありませんでした。
ただ、無線にしたときに既存設備にどう影響が出るかもわからなかったので、もし影響が出た場合は最悪有線にするしかないと腹をくくっていましたが、検証した結果、既存設備に影響を与えず無事に無線でデータを取ることができほっとしました。
データの可視化を実現するためには?
―システム構成について詳しく教えてください。
浅見:今回のシステム構成についてですが、圧力をBluetooth、流量と機械稼働信号をWi-Fiで送信、Bluetoothルーターと無線アクセスポイントで受信して、それらをIndustrial PCに送信しています。
Industrial PCにはリアルタイムデータ処理ソフトウェアをインストールしており、そこに圧力・流量・機械稼働信号のデータを蓄積することで、リアルタイムに稼働状況を表示する構成となっています。
圧力センサーはBluetoothを内蔵したワイヤレス製品を使用しています。Bluetoothの受信にはCassia Networks製のBluetoothルーター(E1000、X1000)を使用しました。
流量センサーはアナログ出力(4-20mA)の製品を使用しており、機械稼働信号はナカヨ製 稼働情報収集装置NT920-IBより接点信号を取得しています。
アナログ信号と接点信号を無線化するために、無線対応のリモートIOを使用しました。受信は汎用のアクセスポイントを使っています。
また、BluetoothルーターからはMQTT、WiFiの信号はModbus/TCPと異なるプロトコルで通信しており、異なるプロトコルの信号をリアルタイムに処理するためにFogHornを使用しています。
構成図は以下をご覧ください。
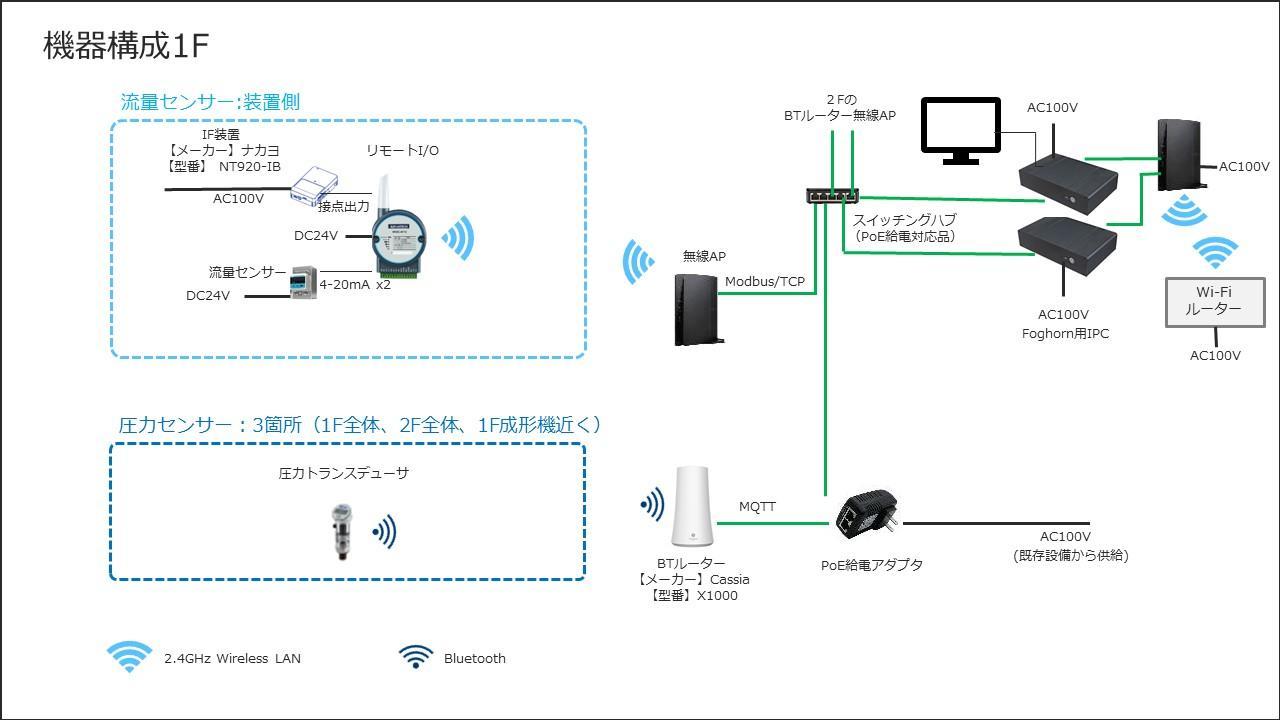
▲構成図 1階
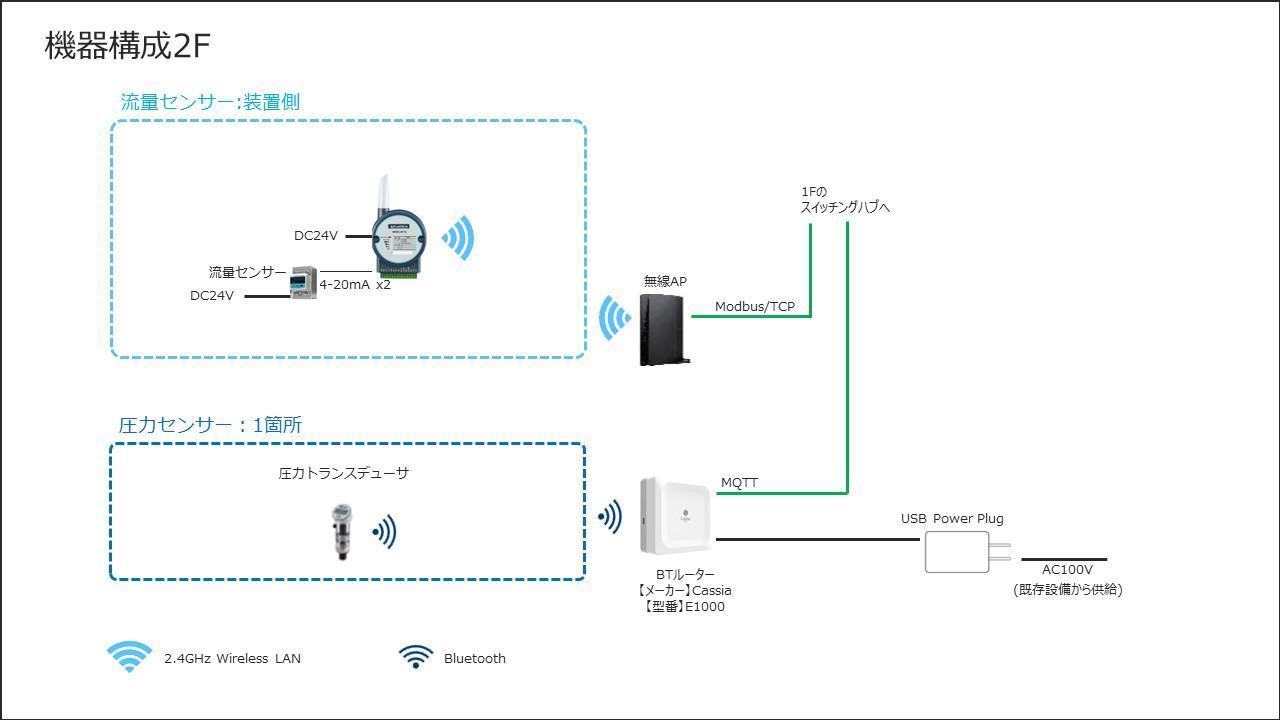
▲構成図 2階
浅見:測定した結果、圧力の変動が見えました。
圧力はコンプレッサーで一定値(0.69MPa)に制御されているため、圧力変化が見えない可能性があると想定し、流量データも取得するようにしていたのですが、実際に取得した結果、圧力が0.1MPa程度変化しているデータを取得できました。エアガンによる圧力低下も見えたため、流量を取得せずとも状態が把握できると判断しました。
また、同じ建屋内だったら取り付けたどの圧力センサーでも、数値に大きな差異はないことがわかりました。
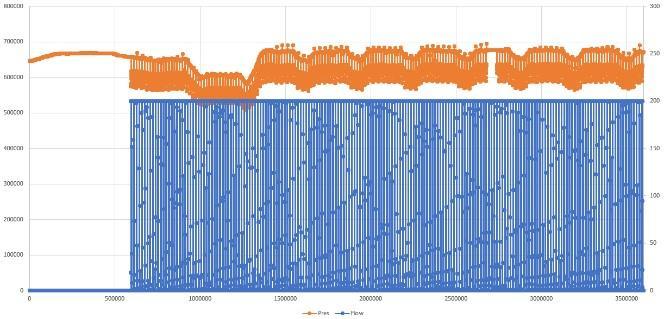
▲流量・圧力のデータ オレンジ色のグラフが圧力で、青色のグラフが流量。
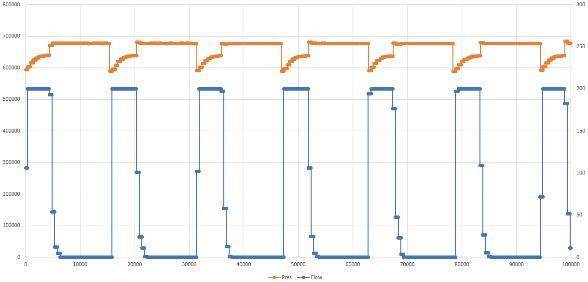
―圧力センサーだけでエアーの状態が可視化でき、同じ建屋内であればどの場所でも変化がないことがわかったんですね。
これでデータの可視化ができたと思いますがエアーが不意に止まってしまう問題に対してこれからどのようなことができるのでしょうか。
小林様:今回の実証実験でエアガンでのエアー使用が多いことがわかりました。ですが、エアガンを数本使っても建屋内全体での圧力はあまり落ちておらず、ほとんど設備に影響を与えていないことがわかりました。
当初、エアガンの使用率が今回の問題に関わると考えていたため、今回の結果は想定と違いました。
想定外なことが何かしらの原因で発生しているという事実がデータで判断できましたので、別のアプローチを考えなければならないということがわかりました。
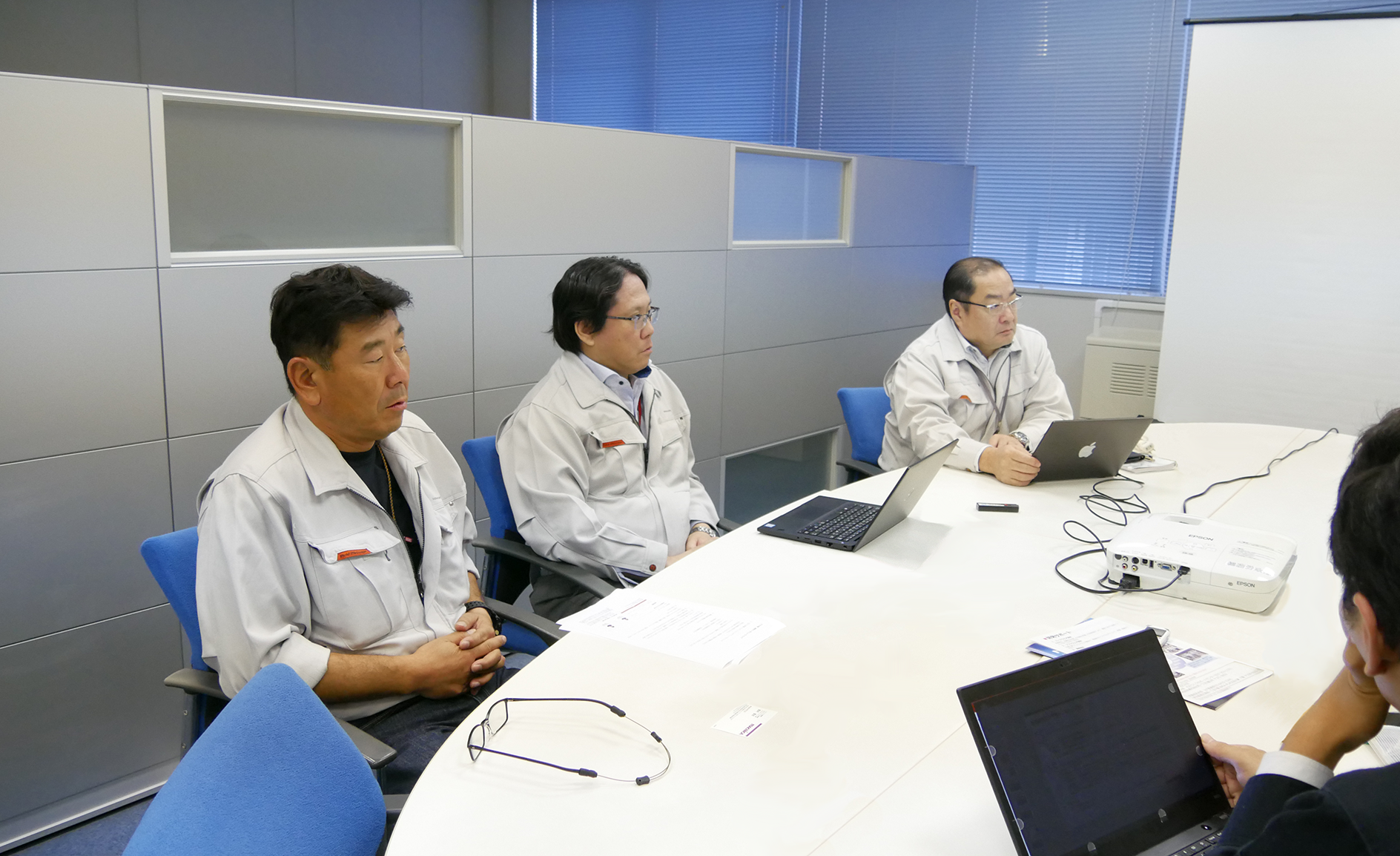
―なるほど。データが見えるようになったことで課題解決のためのアプローチも変わってくるということですね。
三島様:工場全体の稼働状態、コンプレッサーの稼働状況、各エアー配管の圧力データを付け合わさないとコンプレッサーの安定稼働は実現しないかもしれません。
ただ、一度にすべてを実施するのは大変です。今回のようにデータが見えてくると問題が変わっていきます。
一歩一歩できるところから始めて、着実に進めていきたいと思います。
―ありがとうございます。最後に、スマートファクトリーを進めるために重要なポイントを教えていただけますか?
三島様:情報を取得しても行動を起こさなければ何も変わりません。目標を定め、得られたデータを分析して問題を発見し、改善を行うことが重要です。
また、将来人材不足も懸念されるので、自動化も進めていく必要があると考えています。
―貴重なお話をお聞かせいただき、ありがとうございました!
引き続き「省電力化かつ生産設備工具へのエアー供給の停止を予防する」ため、継続してナカヨ様と解決に向けて進めていきます。
次回の記事も、乞うご期待!