初めての自作プリント基板
前回の記事「自作プリント基板で電源作成!(2)」で設計した回路の基板がついに届きました!
今回は、パターンレビュー前の基板(白色)とパターンレビュー後の基板(黒色)の二種類発注しているので、これを使ってパターンレイアウトによる変化も確認していこうと思います。
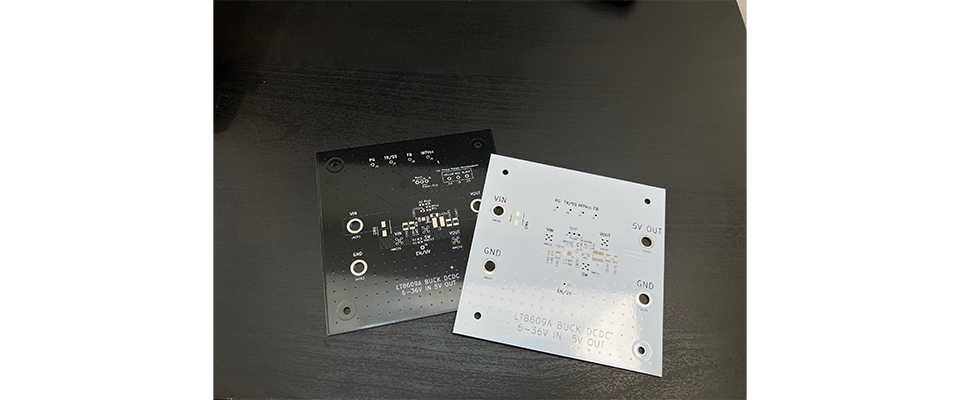
到着した基板
部品実装
基板が届いたので、さっそく部品を実装していきます。今回は Macnica-Mouser で購入した部品を使っています。
前回、ユニバーサル基板を使った際は、部品の足を穴に通してからはんだ付けしていましたが、今回はプリント基板で表面実装するため、同じ方法ではいきません。
そこで活躍するのが「ホットプレート」です!家庭で焼肉などを焼く、あのホットプレートの電気基板用バージョンです。これを使えば、部品を効率よく実装することができます。
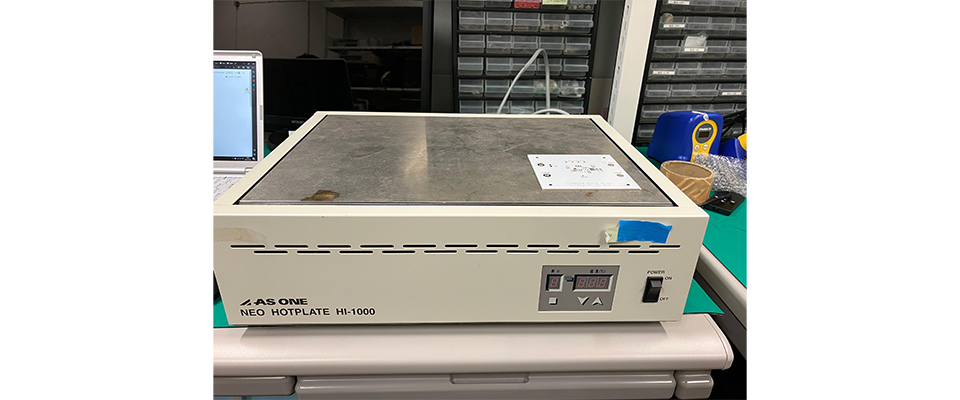
ホットプレート
このホットプレートの熱せられた鉄板の上に、基板を載せます。基板のはんだ付けされるべき銅箔の部分にはペースト状の半田を塗布して、その上に部品を載せておきます。そうすると、基板が熱せられるにつれてペースト状の半田が溶けて部品が実装されます。ちなみにはんだペーストを塗布した基板はこんな感じです。
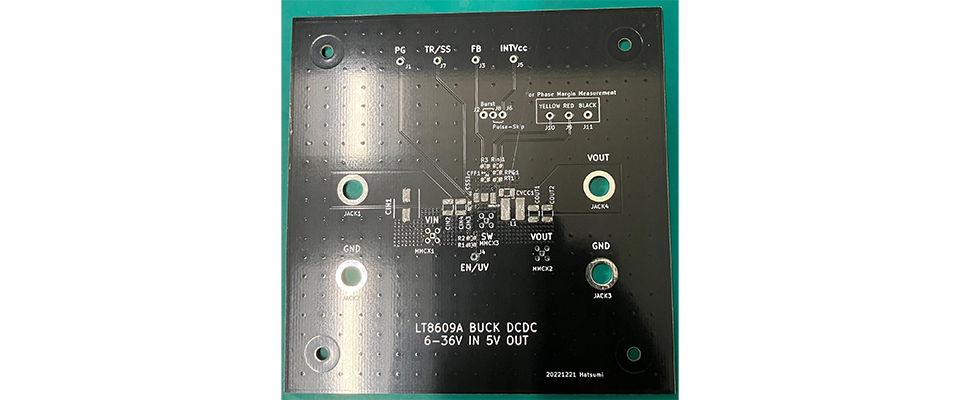
はんだペーストを塗布する際には「ステンシル」を使用します。実際の現場では、足同士のショートを避けるために、ステンシルのサイズを塗布する部分に対して少し小さめに作成するというノウハウがあります。しかし、今回の発注先ではステンシルのサイズ調整ができず、その結果デバイスの足部分で問題が発生しました。パターンの間隔が狭いため、隣り合う足同士がショートしてしまったのです。
そのため、今回はデバイスの裏面の PAD 部分はホットプレートで取り付け、足の部分は手作業で慎重に取り付けることにしました。
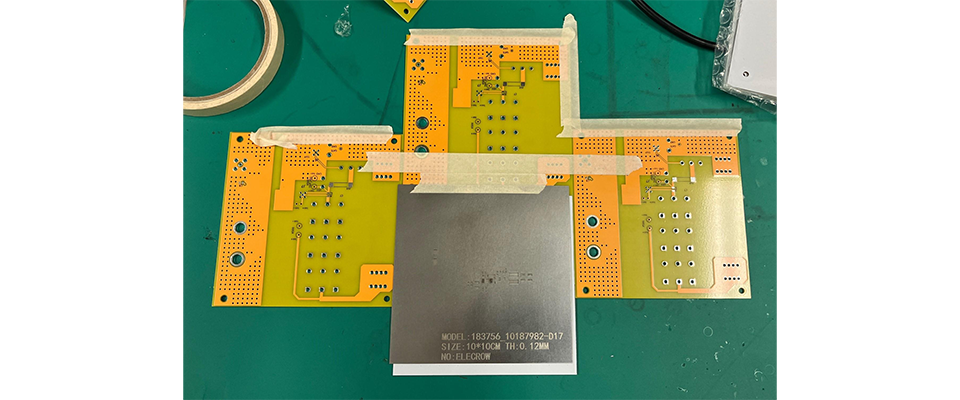
ステンシルでのはんだペースト塗布
実はこの手作業での実装にも結構コツが必要で、最初はかなり苦戦しました。しかし、フラックスをデバイスの足にたっぷり塗っておくことで、はんだが足にしっかり吸い付いてくれるようになり、結果的にはうまく取り付けることができました。
そして、こちらが完成した基板です!
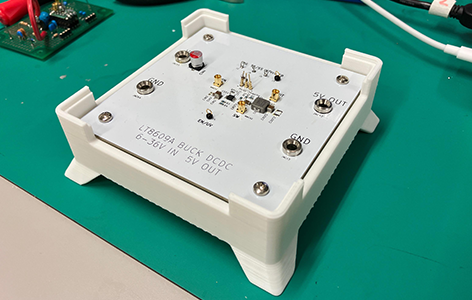
完成した基板(白色、レビュー前回路)
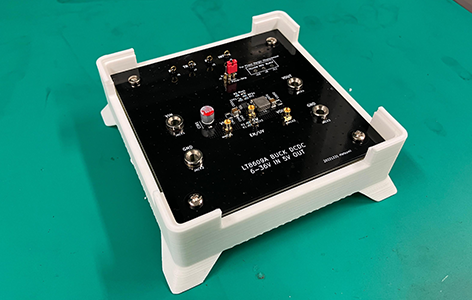
完成した基板(黒色、レビュー後回路)
効率測定
早速、完成した基板に火入れをおこない、効率を測定してみました。今回は、レビュー前とレビュー後でパターンが異なる2つの基板を作成しているので、それぞれの効率の差を確認していきます。
どんな結果になるのか、楽しみですね!
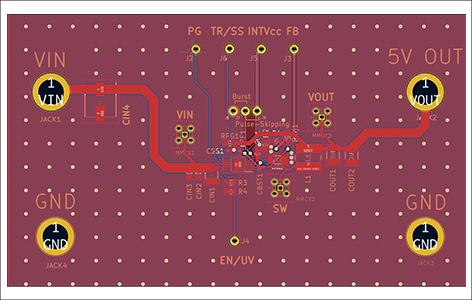
レビュー前基板パターン
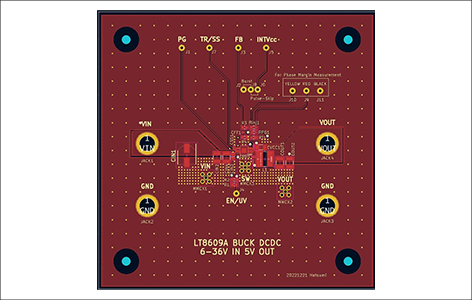
レビュー後基板パターン
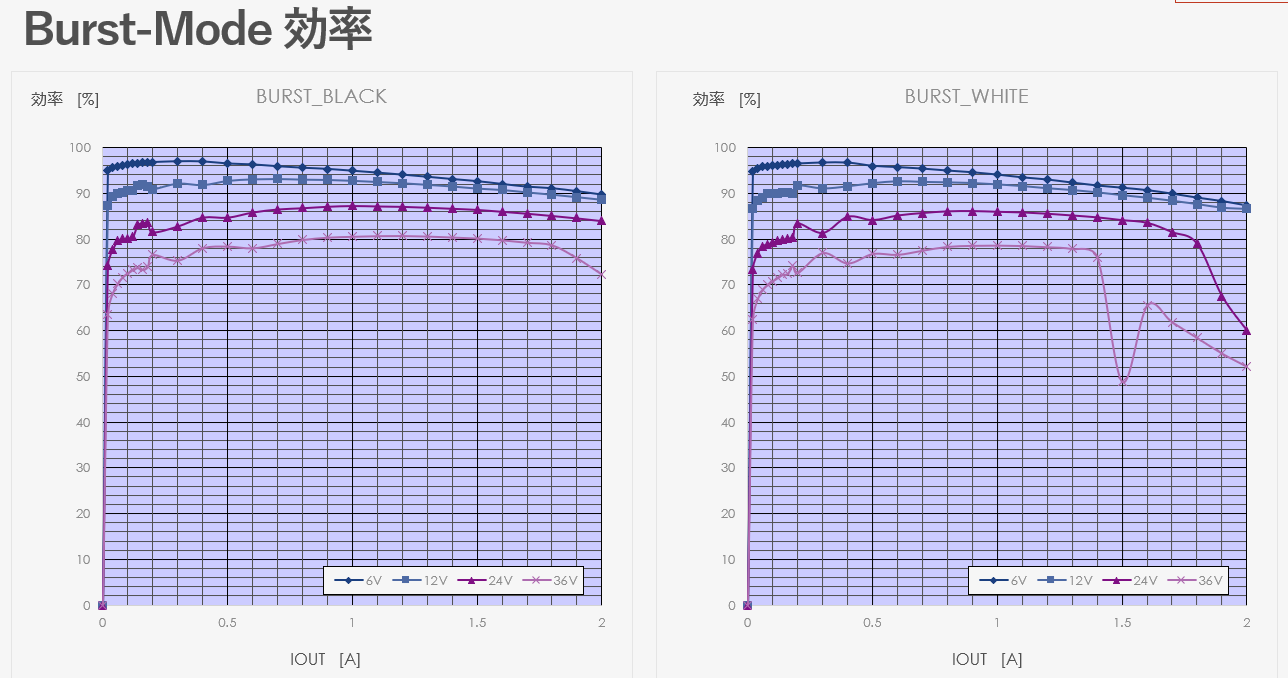
効率グラフ
効率グラフを観察すると、どうでしょうか。出力電力 (W) が大きくなるにつれて、基板間で効率に差が出ているのが確認できます。特に、WHITE 基板では 36V 入力、1.5A 出力時に局所的な効率低下が見られるため、ここは要チェックポイントです。
次回は、この効率の違いが出た理由を詳しく探っていきます。お楽しみに!
ユニバーサル基板編 / プリント基板編一覧
■ユニバーサル基板編
・ユニバーサル基板でDC/DCコンバーターを作ってみた (1)
・ユニバーサル基板でDC/DCコンバーターを作ってみた (2)
・ユニバーサル基板でDC/DCコンバーターを作ってみた (3)
・ユニバーサル基板でDC/DCコンバーターを作ってみた (4)
■プリント基板編
・自作プリント基板で電源作成!(3)