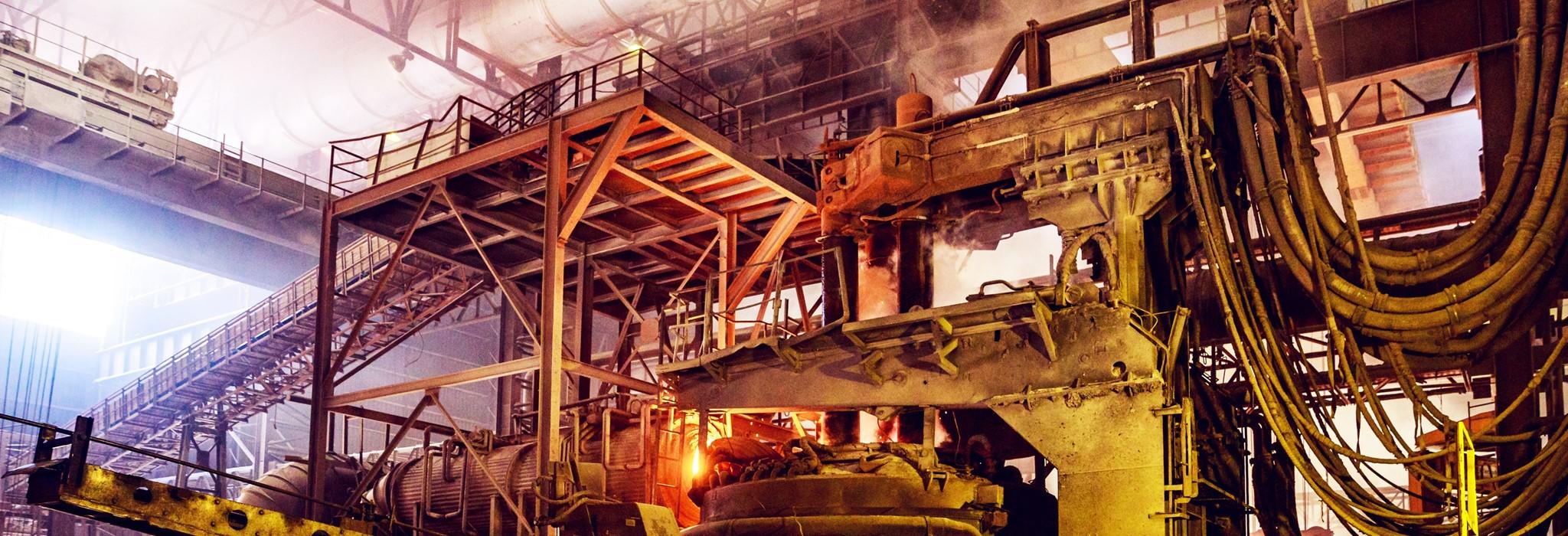
What is Macnica 's thermal solution?
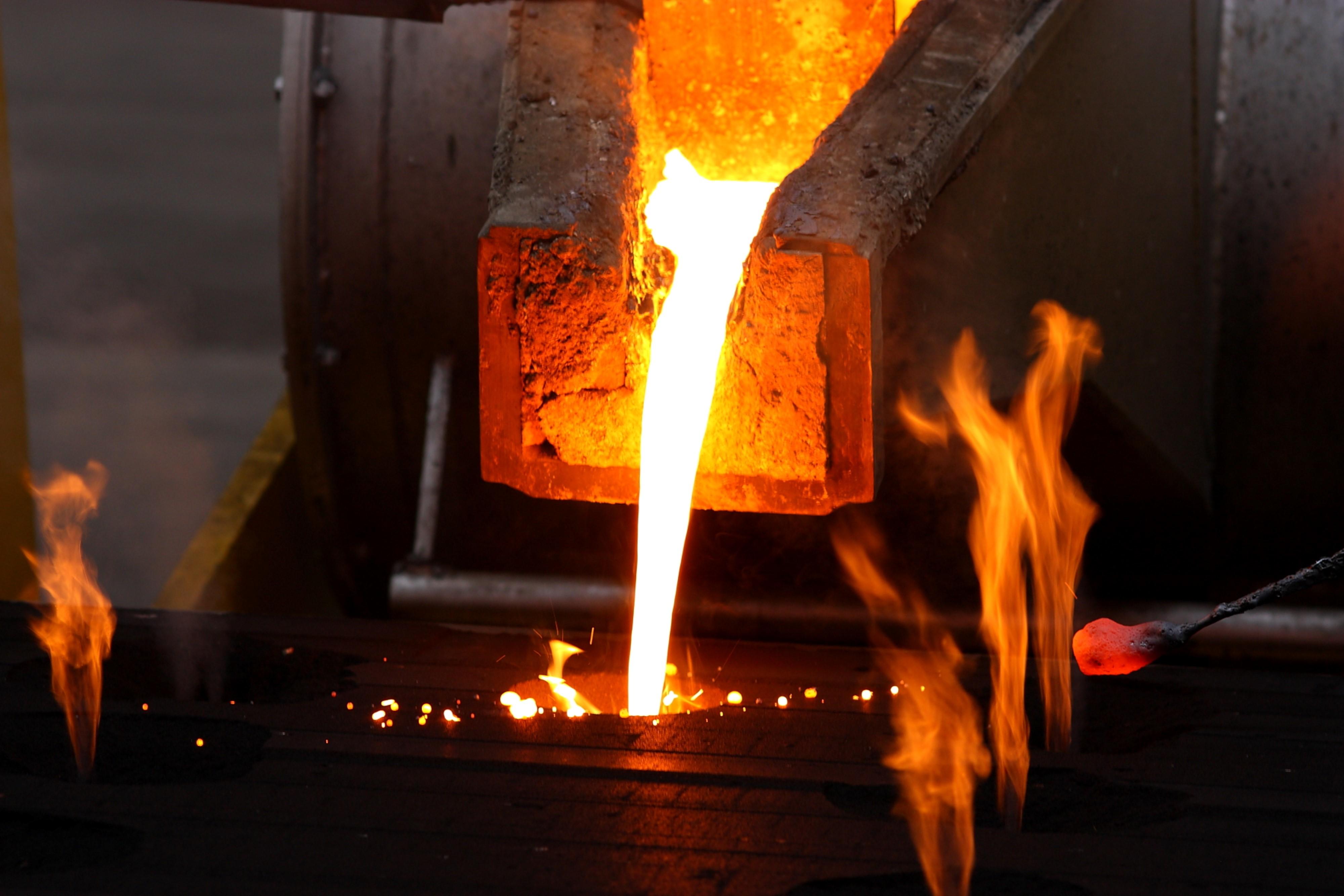
Thermal solutions using infrared cameras provided by Macnica contribute to advanced monitoring and optimization of manufacturing processes in the industrial sector, improving product quality, increasing production efficiency and reducing energy consumption. They also contribute to the promotion of sustainable manufacturing processes that take into account the impact on the environment.
Thermal solutions using Macnica 's infrared cameras are powerful tools that set new standards in the industrial world and solve many of the challenges companies face. We provide solutions tailored to our customers' needs and accompany them toward contributing to a sustainable future.
This article will introduce some examples of thermal solution implementation.
Electric furnace monitoring solution
Optimization and automation of scrap input timing
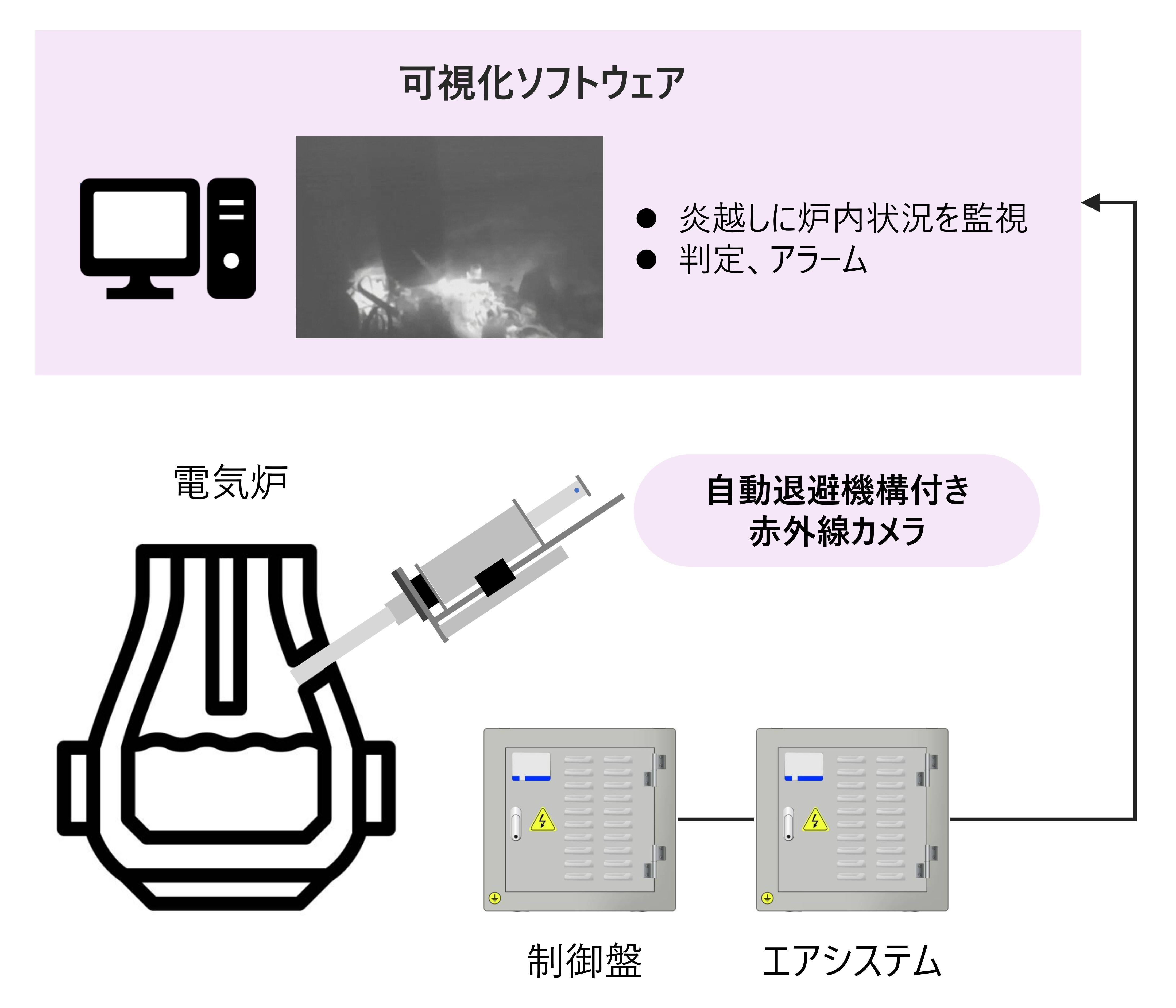
■ What I want to achieve
・Decarbonization, reducing CO2 emissions
- Improved energy efficiency
-Increased use of scrap steel
Improved automation and process management
■Challenges
・To optimize and automate operations, it is necessary to monitor the temperature and condition inside the furnace, but there is no way to do so.
・We want to optimize the timing of scrap feeding to improve energy efficiency, but we can't do it because we don't know the condition inside the furnace.
■ Solution
・Monitoring the inside of the furnace using a camera that can visualize the inside of the furnace
■ Advantages
・Reduction of power consumption by optimizing scrap input timing
・Automating scrap input timing and improving processes to reduce labor and improve quality
Ladle shell temperature monitoring solution
Preventing molten metal leaks from ladles, ladles and torpedo cars and optimizing maintenance schedules
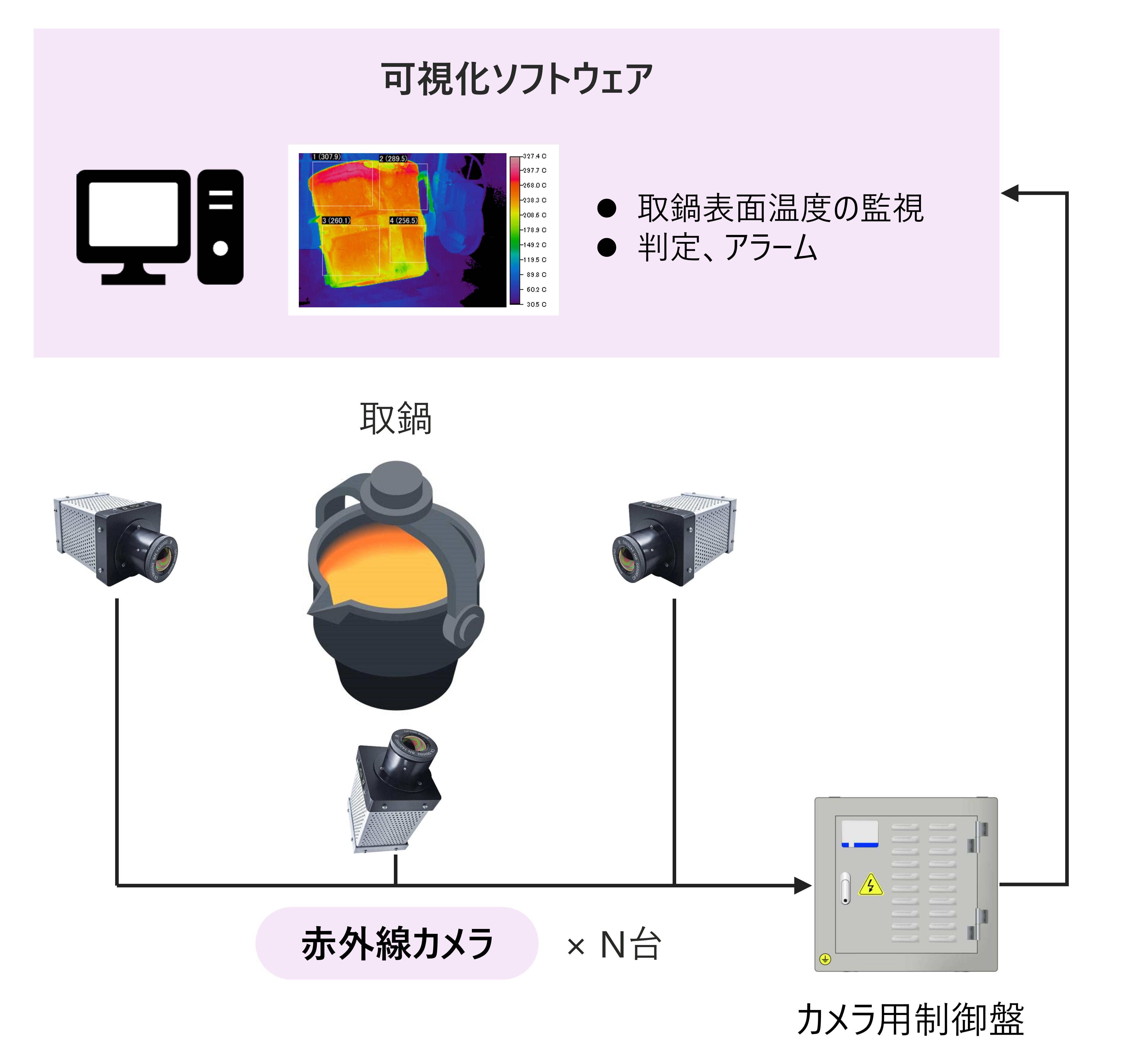
■ What I want to achieve
- Monitoring damage to ladle shell
- Trend monitoring of equipment deterioration
■Challenges
・The ladle is subject to large thermal stress due to repeated heating and cooling, and the deterioration of the refractory material can lead to molten metal leaks.
・If a molten metal leak occurs, there is a possibility that serious injury may occur.
■ Solution
・Prevention of molten metal leakage and optimization of maintenance timing by monitoring the ladle surface temperature can be achieved using standard application software.
■ Advantages
- Improving work site safety and working conditions
・Reduction of worker man-hours
Continuous Casting Monitoring Solution
Process automation, skill standardization, and database construction
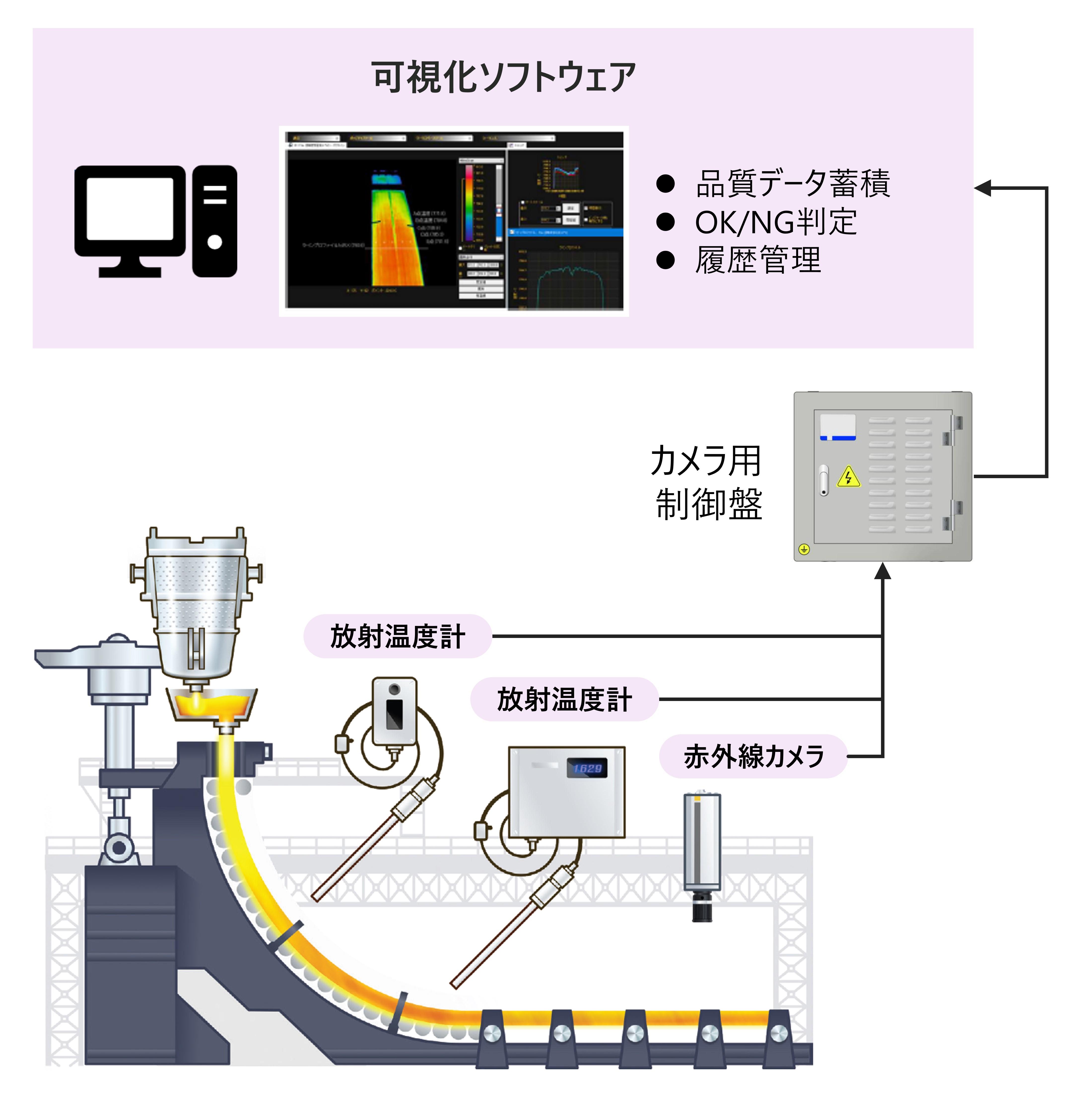
■ What I want to achieve
・Automating and digitalizing quality control
・Increased production of high quality products
■Challenges
・Production temperature trends cannot be managed for each lot
・It is difficult to maintain stable slab quality
・Deterioration of skills due to lack of workers
■ Solution
・Automate processes and standardize skills by measuring and quantifying surface temperature distribution using infrared cameras/radiation thermometers
■ Advantages
・Improved quality control
・Building a database of manufacturing temperature quality
・Automating the cooling process
Slag removal automation solution
Improving safety and working conditions at casting slag removal work sites
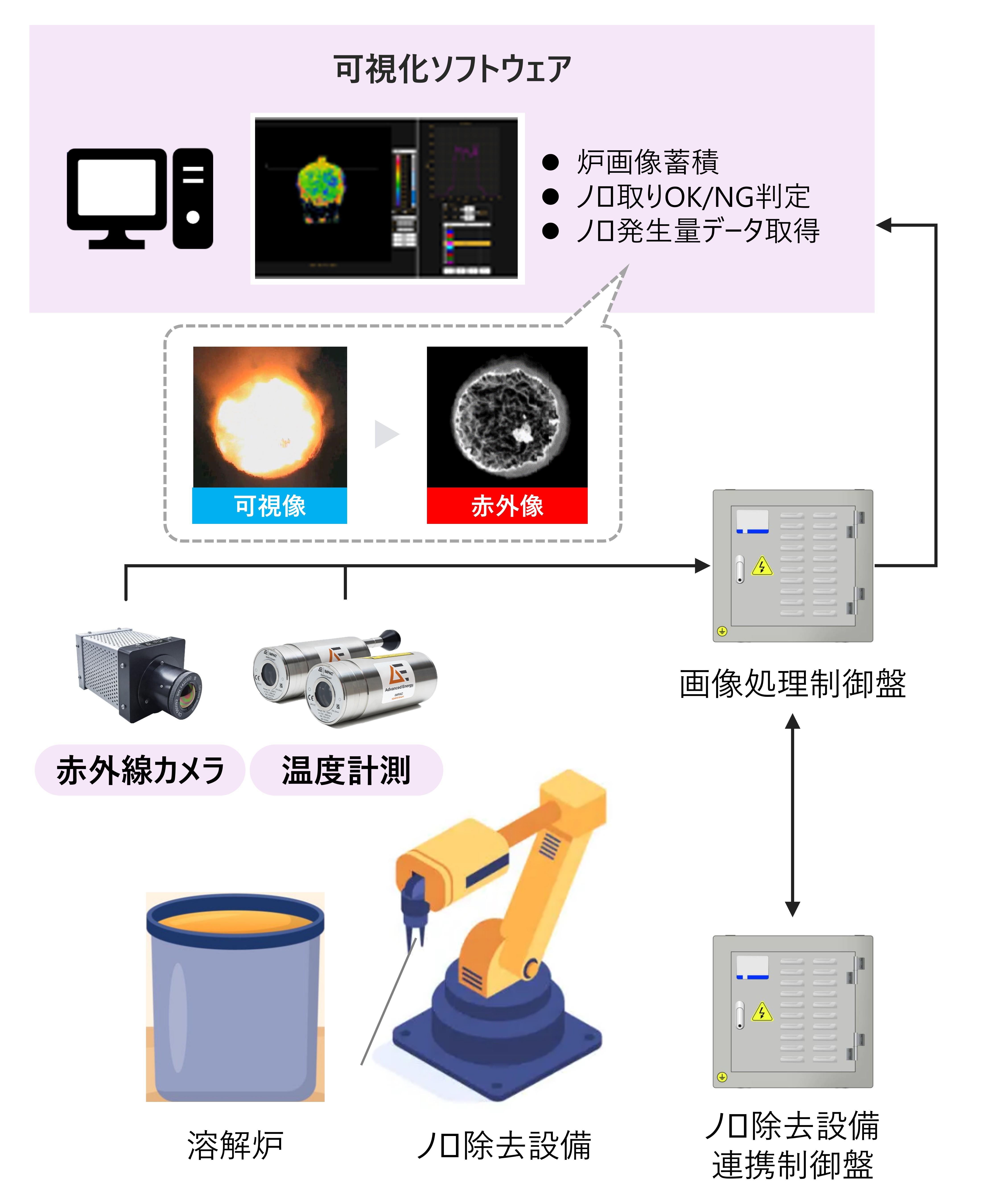
■ What I want to achieve
- Improving work site safety and working conditions
・Resolving employment issues to ensure business continuity
■Challenges
- Dangerous working environment
・Due to the declining birthrate and aging population, the number of beginner workers is increasing, which poses safety issues.
・Quality is affected by differences in worker skills
■ Solution
- Quantification of slag residue rate using infrared cameras and judgment software
・Automating furnace front work by linking slag removal equipment and infrared cameras
■ Advantages
- Improving work site safety and working conditions
・Improve quality
・Reduction of worker man-hours
Flare Monitoring Solution
Flare stack control, automation and compliance with environmental regulations
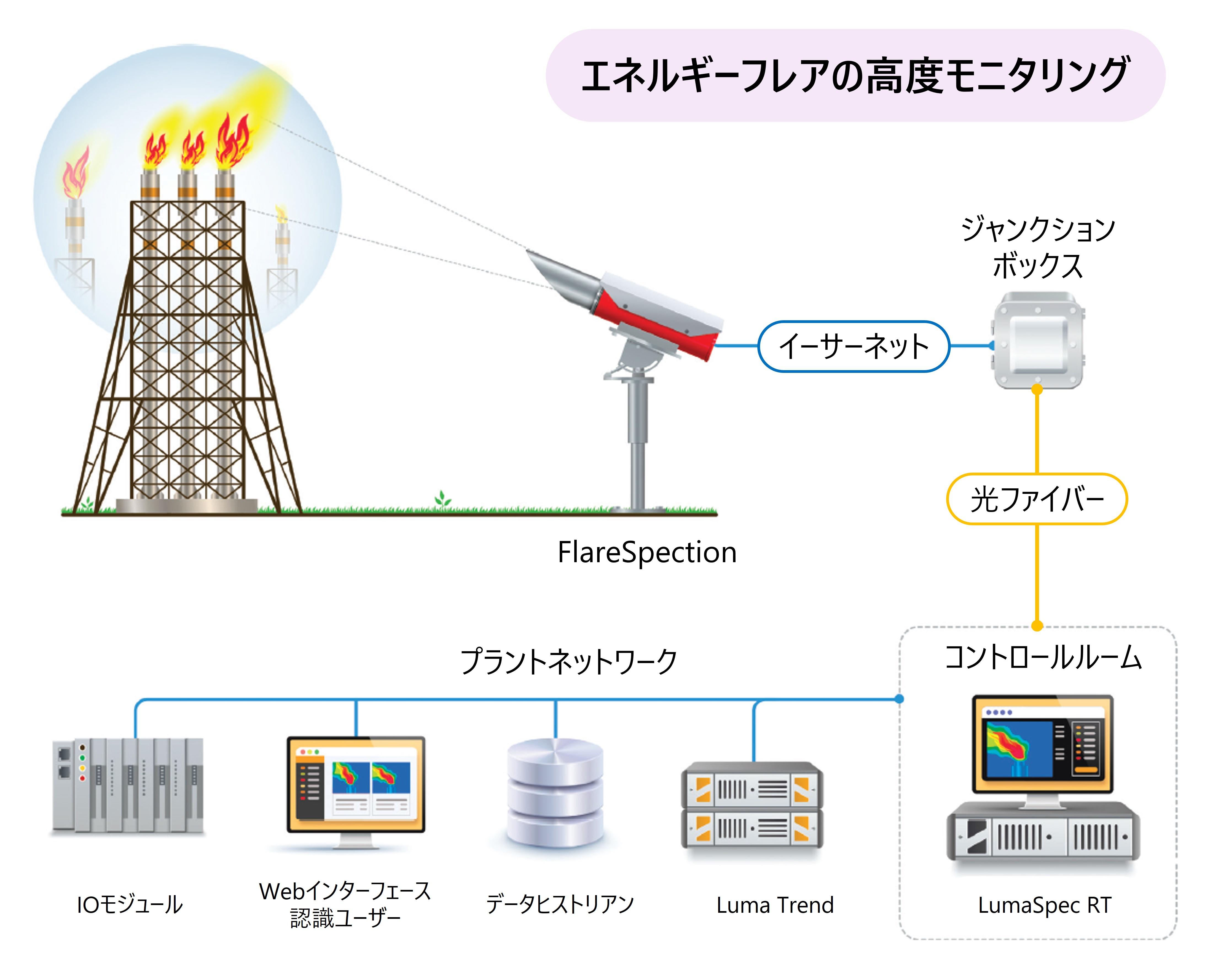
■ What I want to achieve
- Compliance with environmental regulations
・Automated control
・Improvement of sensing technology
■Challenges
・Compliance with environmental regulations is necessary but not possible
・The size of the flame coming out of the flare stack cannot be monitored.
・Control cannot be performed according to the combustion conditions
■ Solution
・Use flare stack monitoring sensors to monitor and store the size of the flames with time stamps.
- Quantify and control the size of the flare
■ Advantages
・Environmental regulations can be met
・Operations can be automated
Energy usage visualization solution
Visualization of energy usage and process optimization in steel, casting, glass factories, etc.
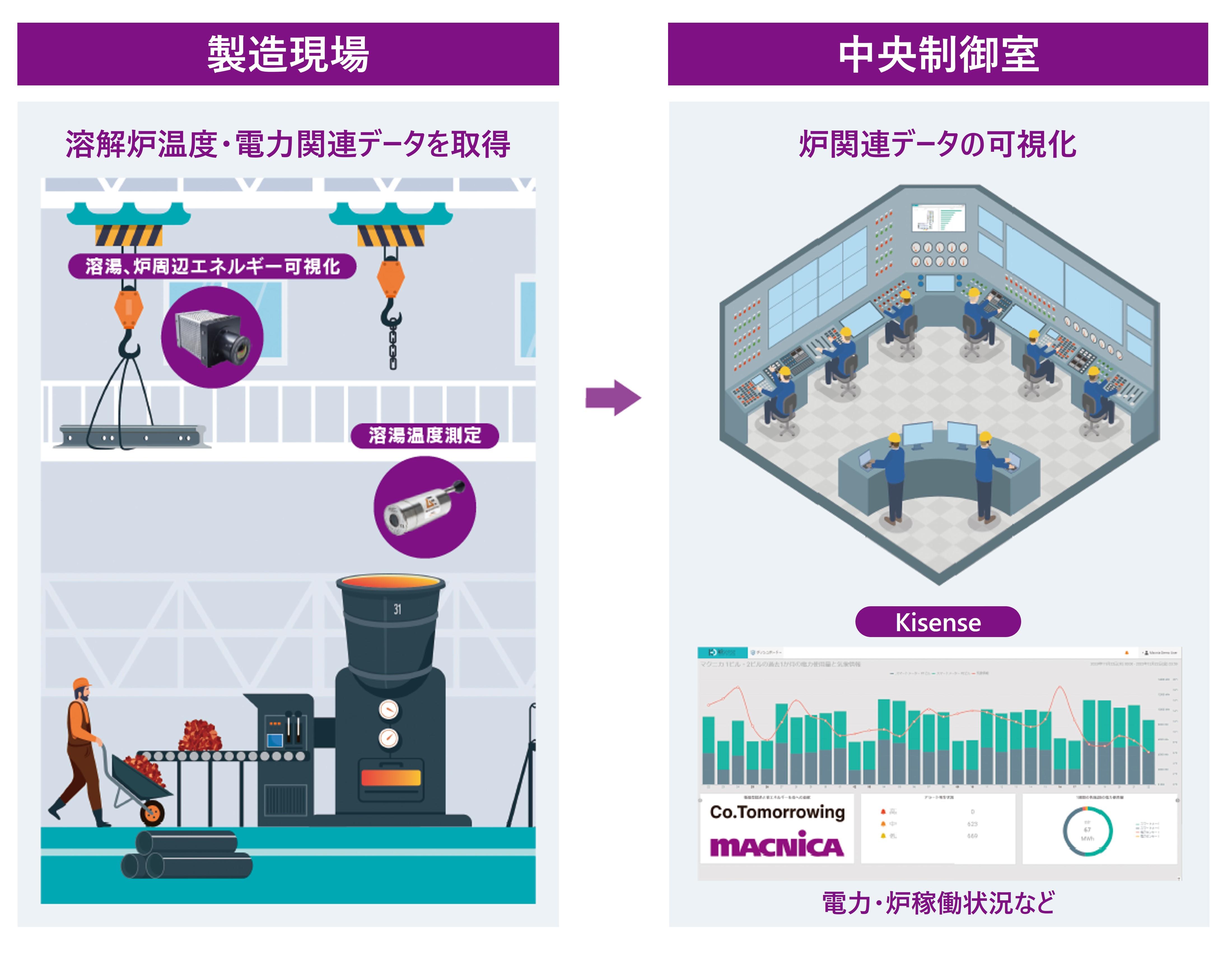
■ What I want to achieve
・Achieving carbon neutrality
- Improved energy efficiency
■Challenges
・Electric furnaces and industrial furnaces used in steel and casting consume a lot of electricity and are the dominant source of energy consumption within the factory, but the power consumption is not being managed.
■ Solution
・Optimize the operation process by visualizing power usage status by acquiring temperature measurements using infrared cameras and radiation thermometers, as well as the power and operating status of each piece of equipment.
■ Advantages
- Reduced power consumption
- Improving operational processes to reduce power consumption
Inquiry
The steps to introduce the thermal solution are as follows:
If you have any questions about improving site safety, optimizing operations, or decarbonization, or if there is a solution you are interested in, please feel free to contact us.
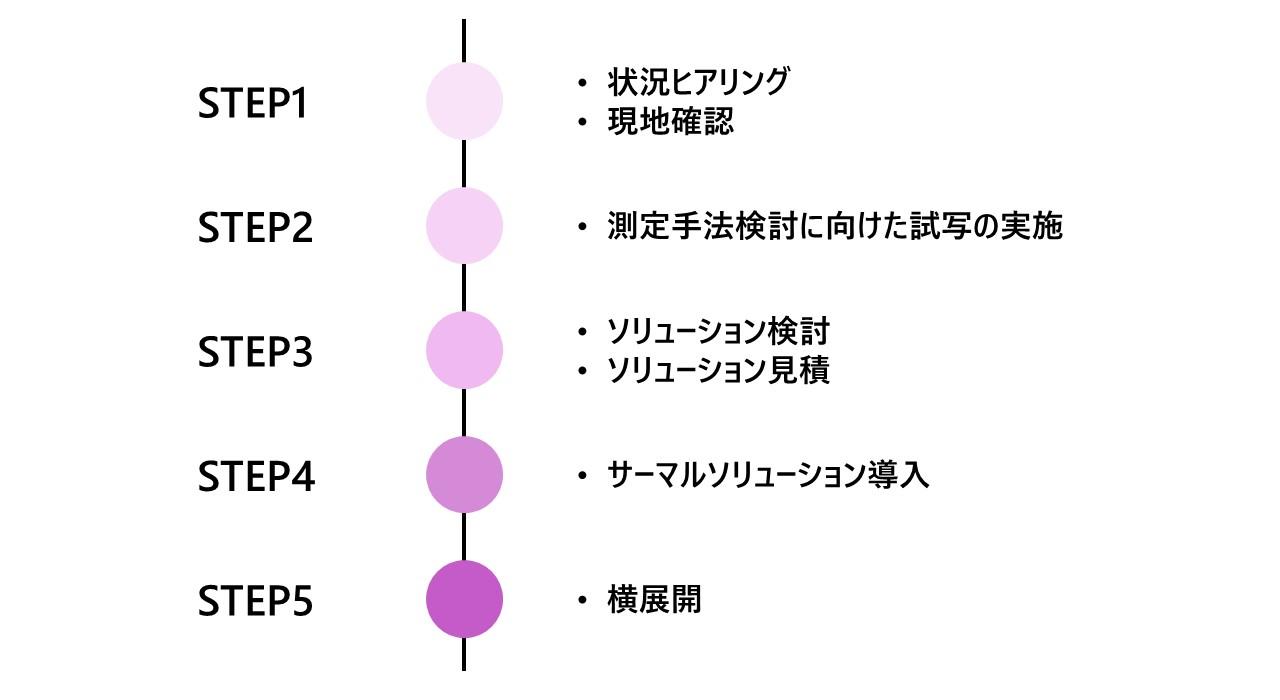