Motors that move machines are used in a variety of applications such as robots, 3D printers, and microscopes. Precise motor control improves the performance of applications, but for reasons such as ``no in-house know-how'' or ``limited development period,'' there are many reasons why it is difficult to quickly achieve smooth motor control without spending time on detailed design. I'm sure there are many people who have a serious need to incorporate it.
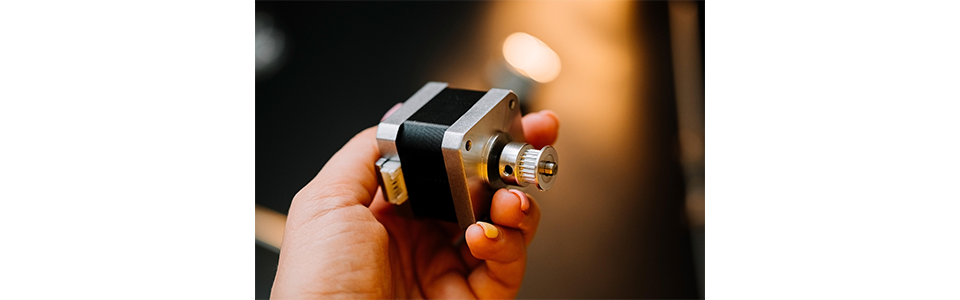
This time, we will introduce the "ADI Trinamic™ series" that meets those expectations. Please read this book if you are interested in highly functional motor control that can be used without any know-how, or if you want to increase the added value of your applications by using sensorless load detection and energy saving functions.
What is the ADI Trinamic™ series?
The ADI Trinamic™ series (hereinafter referred to as the Trinamic™ series) is a lineup of motion control ICs from Germany's Trinamic, which was integrated into Analog Devices, Inc. in 2021.
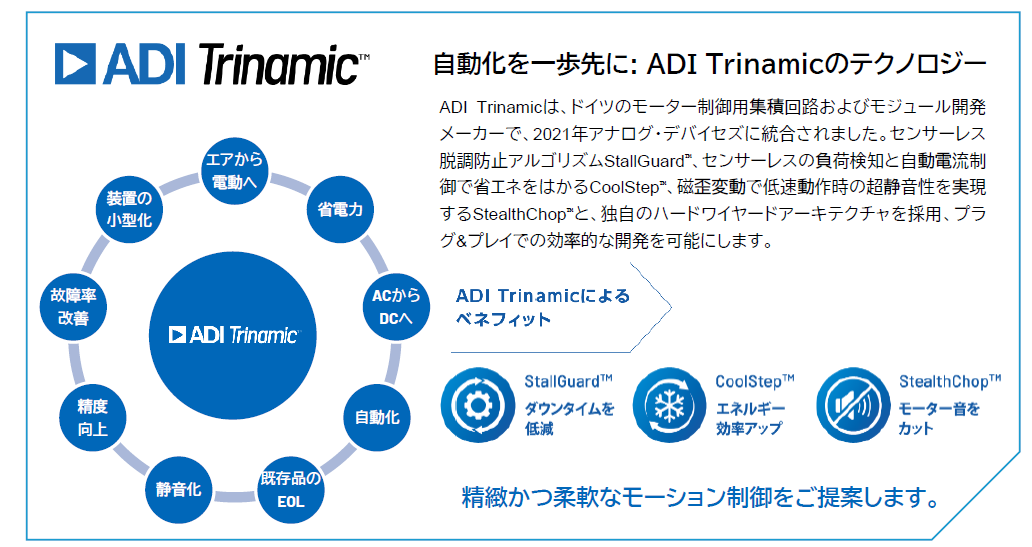
Highly functional proprietary algorithms such as "StealthChop™", which achieves surprisingly quiet operation, and "StallGuard™", which detects step-out without a sensor, are installed as standard in the hardwired architecture, allowing precise and flexible motion control. You can develop efficiently.
Ideal for applications that require quietness, accuracy, and power savings. For example, it can be used for the following applications.
- Conveyor with smooth movement
- Microscopes, optometry machines, and surveillance cameras that require quiet operation
- Small battery-powered equipment
- Robot arm that requires load detection
Features of Trinamic™
Hardwired architecture with high-precision control algorithms as standard |
Parameter changes can be made on the fly |
Precise control algorithms for power saving/quietness/downtime reduction, etc. |
Enabling efficient plug-and-play development |
Differences between traditional solutions and the Trinamic™ series
What makes the Trinamic ™ series different from traditional common solutions? The figure below represents that image.
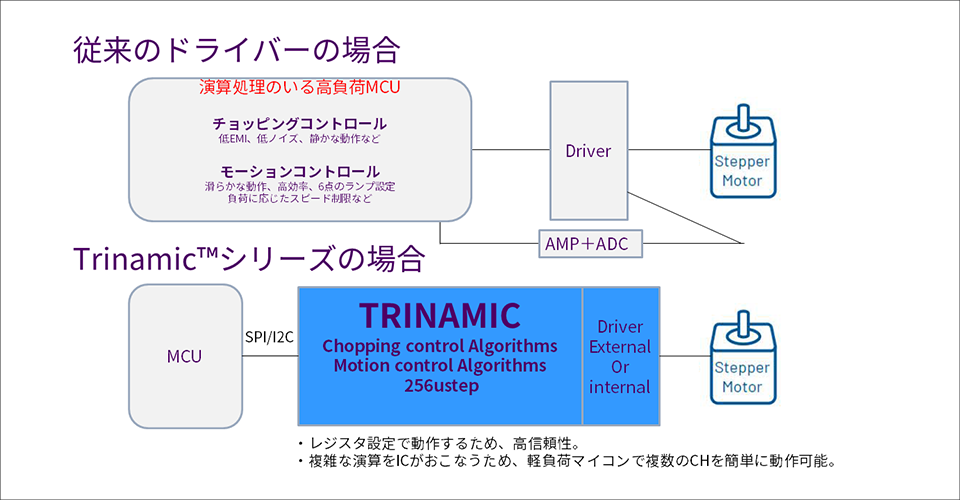
Traditional motor drivers require a lot of effort to develop motor control algorithms and write them to the MCU. Additionally, the power stage needs to be built in, which creates issues with miniaturization and heat dissipation.
The Trinamic ™ series incorporates sophisticated control algorithms into the hardware, allowing you to create highly functional motors by simply changing register settings on the fly. Since there is no need to write complex arithmetic processing, simultaneous operation of multiple channels can be easily developed.
The Trinamic ™ series also includes a lineup with a built-in power stage. It is easy to miniaturize, has low on-resistance, and suppresses heat generation. As a result, hardware design time can be significantly reduced.
The comparison table below summarizes the differences between the Trinamic ™ series and traditional solutions.
ADI Trinamic™ |
Traditional solution |
|
product |
Motion control IC |
|
Target motor |
Stepper motor and BLDC |
|
control algorithm | High-precision algorithms are hardwired as standard | software |
Motion control parameters | Register settings | software |
Changing parameter settings | Can be changed on the fly | Software changes required |
Algorithms held | Precise control algorithms for power saving/quietness/downtime reduction, etc. | - |
Evaluation environment | TMCL-IDE (download free) Plug-and-play and intuitive GUI. Motion system development while checking in real time |
It may take some time to get used to the evaluation board. |
Product lineup | IC/board module/motor (finished product) | - |
By using the Trinamic™ series, you can achieve advanced motion control while significantly reducing development man-hours.
The download-free integrated development environment "TMCL-IDE" is intuitive and allows you to change parameters while checking actual operation. It is much easier to use than a general evaluation board, and you can get the motor running in as little as 30 minutes. Entire systems can be designed quickly.
Our product lineup is wide ranging from ICs to modules, and you can choose according to your application.
Motion control with Trinamic™ series
Specifically, what kind of movements can be achieved? The video below is an image of motion control using the Trinamic ™ series.
In the upper stage, the motor accelerates smoothly, reducing shock and achieving high-speed conveyance. Achieving such smooth movement is important in applications that require delicate handling of conveyed objects. However, with general motion control ICs, control is complicated, as calculations are performed on the CPU side.
On the other hand, the bottom row shows the case of simply accelerating and decelerating to a constant speed. In this case, the difficulty of development is reduced, but the possibility of shock being transmitted to the conveyed object increases, which may affect the conveyance situation such as spillage or overturning.
The Trinamic ™ series provides a command set with control algorithms such as ``executing speed changes in multiple stages'' and ``smoothly complementing movements,'' making it easy to realize complex movements.
Four unique algorithms enable smooth operation
Four unique algorithms enable the smooth operation of the Trinamic ™ series.
- "SpreadCycle™" optimizes motor drive current
- "StealthChop™" controls voltage and reduces drive sound and noise
- "StallGuard™" measures BEMF (back electromotive force) and detects motor load
- "CoolStep™" reduces power consumption by controlling current according to motor load
Let's introduce them in order.
“SpreadCycle™” and “StealthChop™” contribute to quietness
The technologies that contribute to the quietness of the motor are "SpreadCycle™" that optimizes current and "StealthChop ™" that optimizes voltage.
In order to improve the efficiency and stability of a stepping motor, current control using chopping and decay techniques is essential. This suppresses motor vibration and improves quietness. The Trinamic ™ series performs this current control automatically. Let's take a look at the image below.
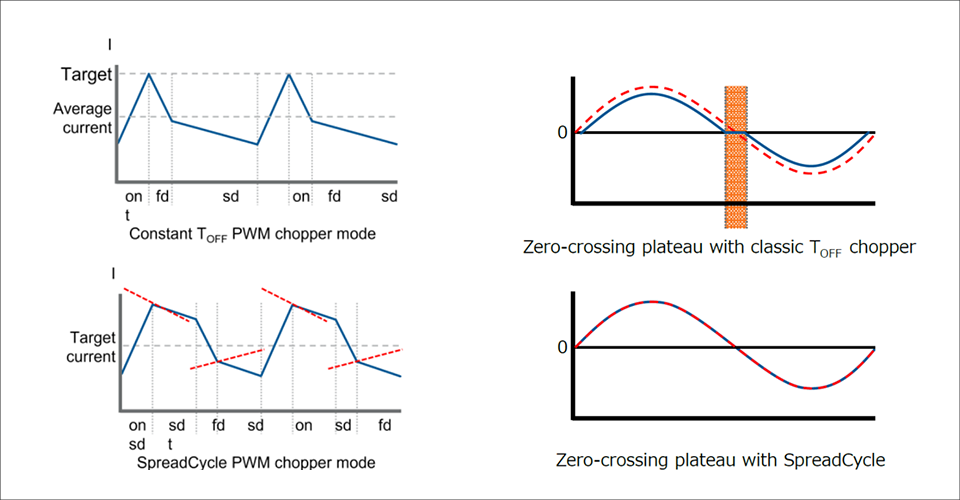
The upper stage shows current control using a general motor driver. I am using Fast Decay and Slow Decay, but the current suddenly changes or deviates from the target current (Figure, top left). In addition, control is difficult when the current is around 0A (ampere), and the waveform becomes flat (upper right of the figure).
The lower row is an image of the automatic control of the Trinamic ™ series. By optimizing the current using SpreadCycle™ and optimizing the voltage using StealthChop ™, sudden changes in current and deviations from the target current are minimized (bottom left of the figure). Furthermore, the waveform around 0A is automatically corrected to achieve quiet movement (Figure, bottom right).
StealthChop™ voltage control also dramatically reduces motor sound and noise. StealthChop™ makes the Trinamic™ series exceptionally quiet, unrivaled by the competition.
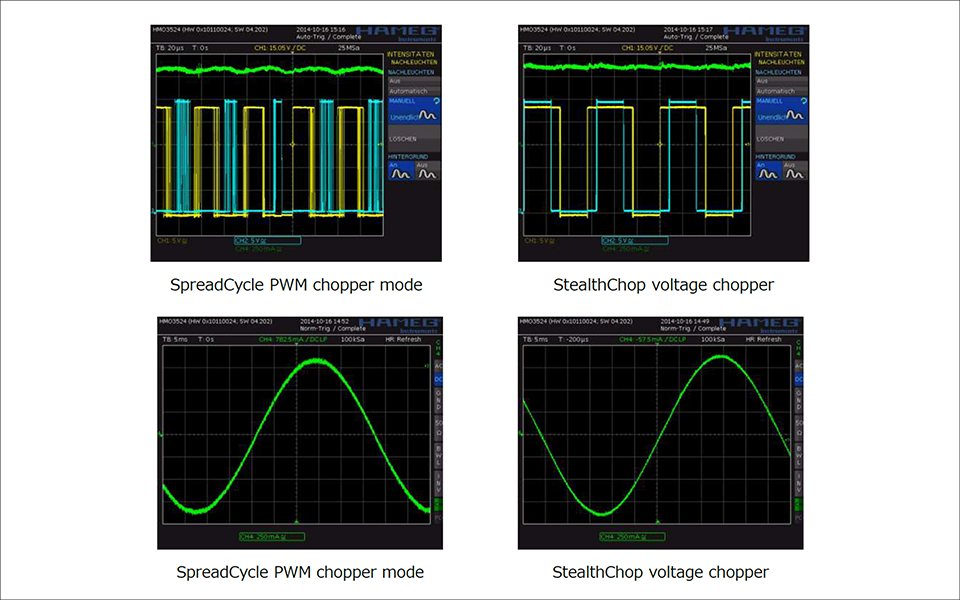
“StallGuard™” and “CoolStep™” realize sensorless load detection and energy savings
Next, we will introduce two technologies that contribute to load detection and energy conservation. "StallGuard™" which detects the motor status and "CoolStep™" which improves energy efficiency.
StallGuard™ is a technology that measures BEMF in areas where no current is flowing through the motor to understand the state of the motor. Not only can it detect when a step-out occurs, but it can also detect signs leading up to a step-out.
CoolStep™ is a technology that optimizes the current according to the motor load detected by StallGuard™. Reactive current, which was previously consumed as heat, can be reduced and energy savings can be improved. At low loads, current can be reduced by up to 70 %.
Utilize StallGuard™ as a sensor
StallGuard™, which detects motor load, can also be used in place of a sensor. You can consider using it for various applications, as shown in the examples below.
<Example of StallGuard™ usage>
- Feedback motor load and adjust grip strength so that the robot arm can hold soft objects
- Detects the difference in the load applied to each tire on rough roads, etc. and performs torque correction.
- Detects machine collision and stops operation without using other sensors
- Detect abnormalities in motor rotation and torque and use for predictive maintenance of machinery
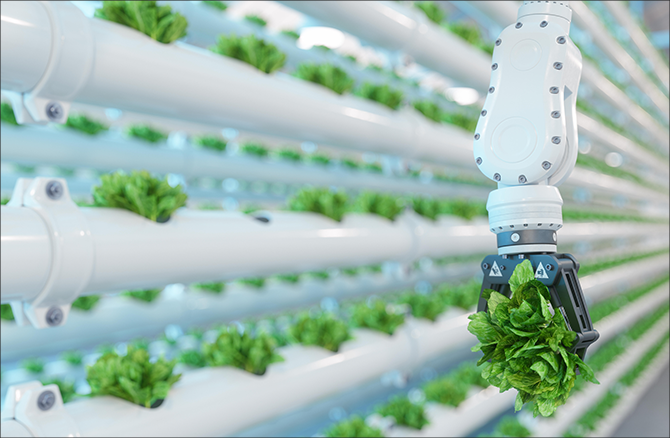
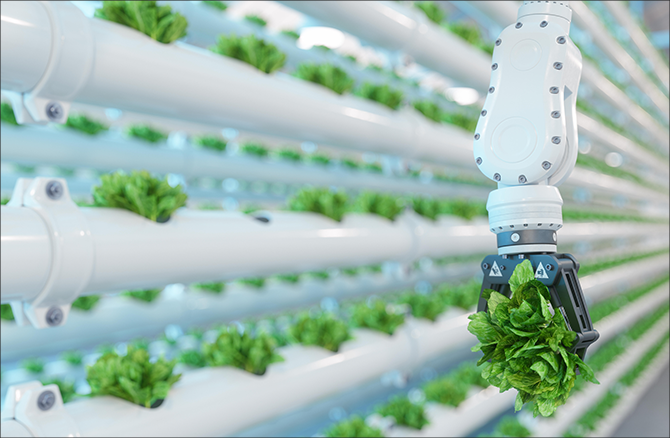
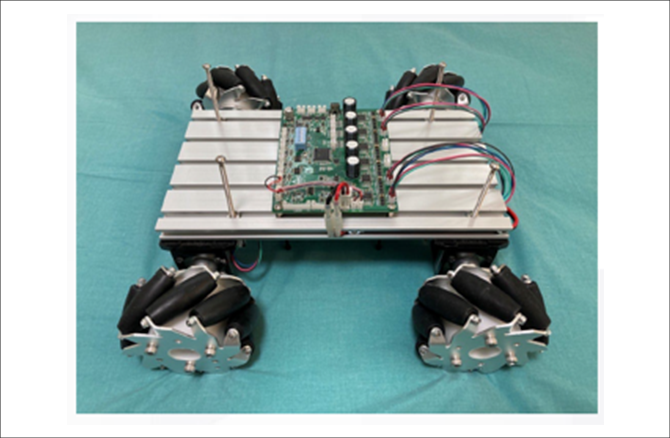
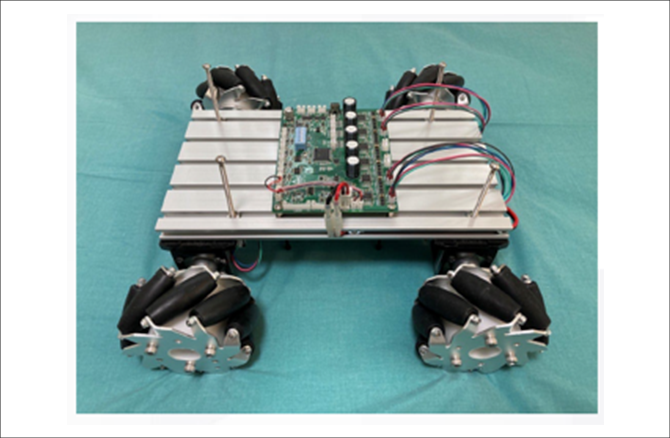
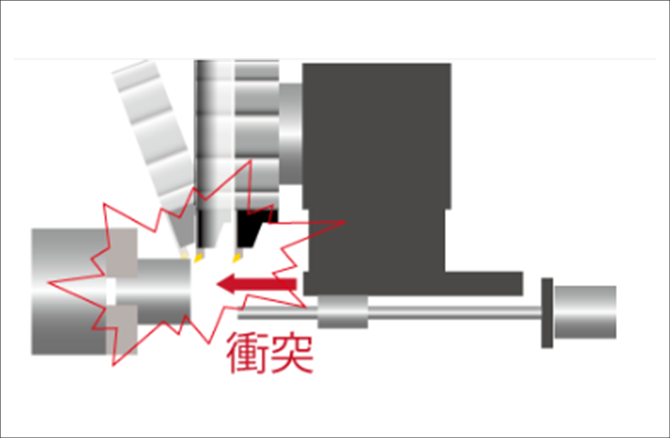
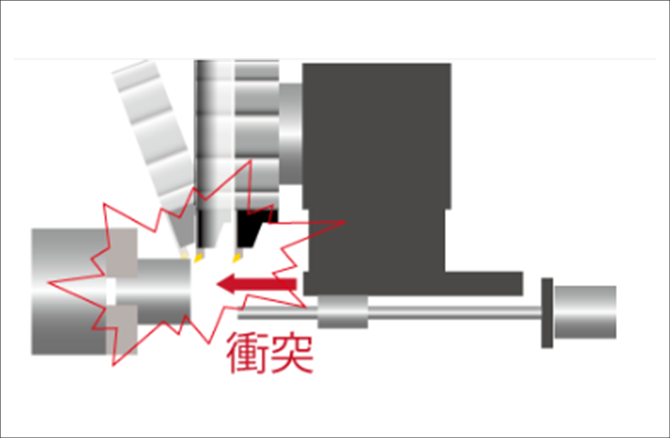
Highly sensitive control is also possible, such as stopping at the slightest contact during high-speed rotation. It is attracting increasing attention because it can be applied to a wide range of applications, such as frequency analysis of numerical load amounts.
Trinamic™ series product lineup
Finally, let's introduce the Trinamic ™ series lineup. We have a rich lineup ranging from ICs to modules.
Trinamic™ series lineup classification
・PAN Driver (with/without encoder)
This is a product that combines a motor, motor driver, and motion controller into a module. Products with built-in encoders are also available.
→ Click here for the lineup
・Motor module
This product combines a motor driver and motion controller into one module. We also offer a lineup that can output multiple channels, such as 4 channels and 6 channels.
→ Click here for the lineup
・Driver IC・Controller IC
This is an IC with motor driver function or motion control function.
→ Click here for the lineup
·motor
A stepping motor that can be used in combination with a motor module or IC.
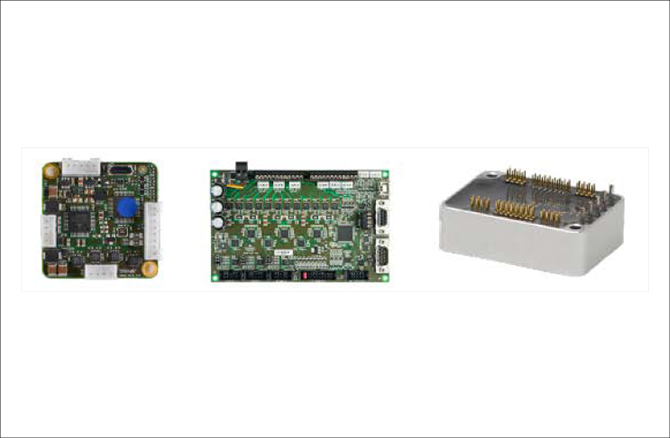
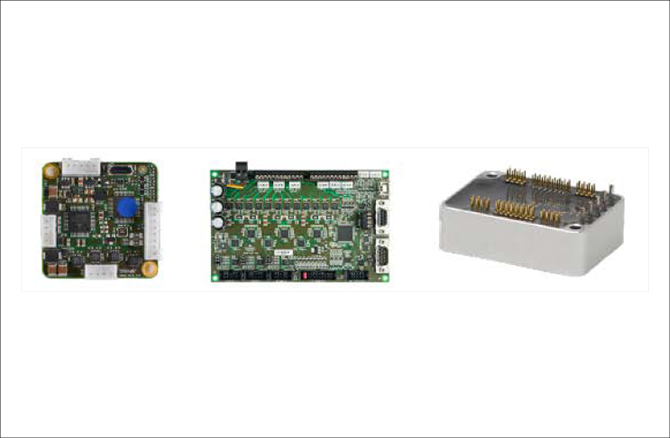
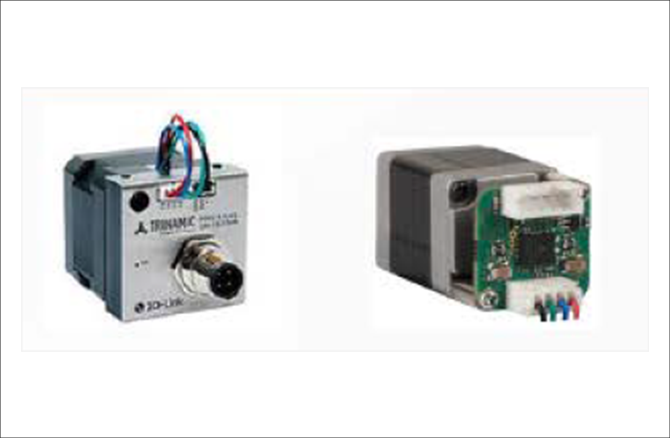
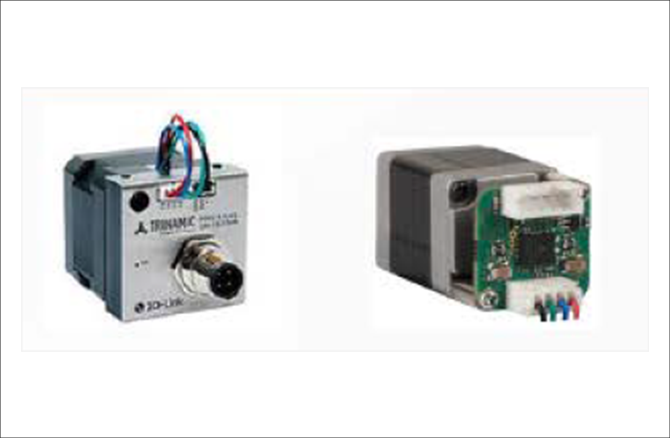
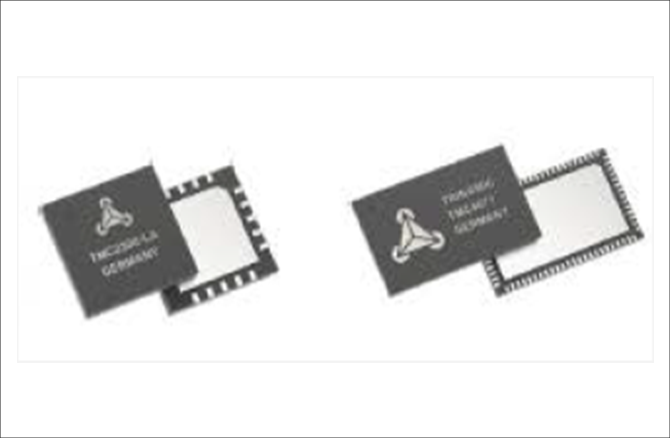
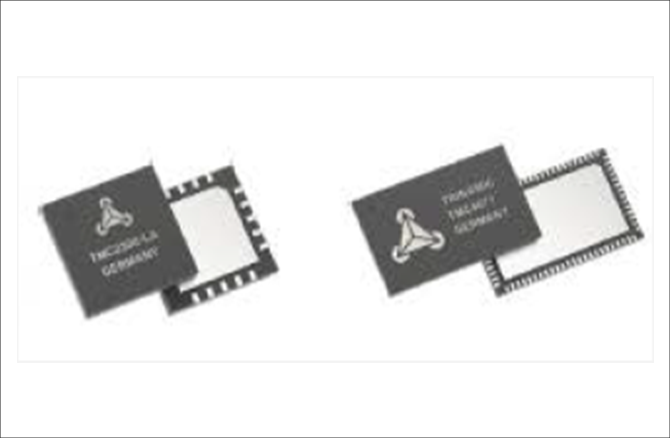
・ Lineup for BLDC motors
We also have a lineup for BLDC motors. The vector control algorithm is built into the hardware, so even those without know-how can easily implement vector control.
This time, we introduced Analog Devices' Trinamic™ series, which makes it easy to achieve delicate motion control. An evaluation board is available, so if you are interested, please try it out.
If you have any questions, please feel free to contact us.
Click here to purchase products
Click here for manufacturer site/other related links
- ADI Trinamic Support | Analog Devices
- Do you know the important "decay" in stepping motor control? ~Part 1: Decay~
- Types of stepping motors and their characteristics
- Three perspectives to consider in motor control
- What is the EVAL-ADUM4135EBZ that improves the reliability of industrial motor control?
Inquiry
If you have any questions regarding this article, please contact us below.
Analog Devices Manufacturer Information Top
If you want to return to Analog Devices Manufacturer Information Top, please click the button below.