Air Quality Blog Part 3: Measures against odors in factories. Is complying with laws and regulations not enough? What else can be done to prevent bad odors?
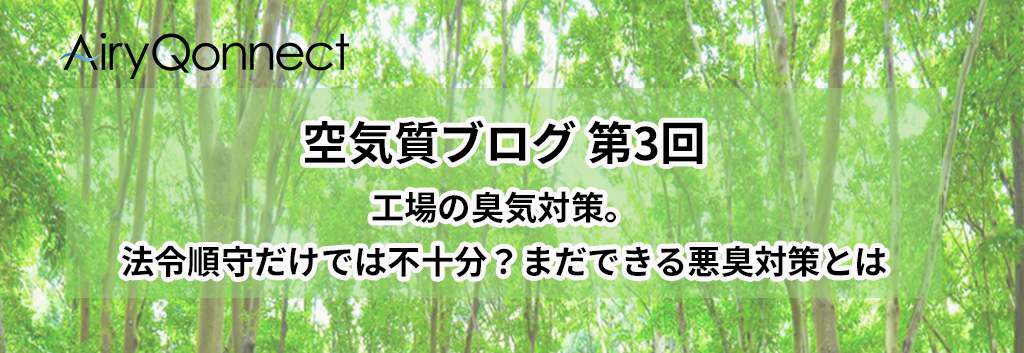
Odors from factories can lead to complaints from neighbors and violations of laws and regulations. However, odors are unavoidable depending on the process, and many factory managers are troubled by the problem of not knowing how to deal with them or the odor remaining even after taking measures.
Here, we will summarize the risks of odors in factories and consider effective odor control measures.
Odor control and compliance with laws and regulations: Why just complying with the Offensive Odor Prevention Law is not enough
Neglecting odor control measures will result in violation of the Offensive Odor Prevention Law
Odors generated by factories are regulated by the Offensive Odor Prevention Law. The purpose of this law is to protect the living environment of nearby residents.
Factory workers are exposed to odors on a daily basis and become accustomed to them. As a result, odors that are not noticed by the company often lead to complaints from nearby residents. When complaints are received by the government, the factory is required to take action, and if it fails to make improvements, it will be subject to administrative guidance and penalties.
Complaints occur even though the standards of the Offensive Odor Prevention Law are being followed
The Offensive Odor Control Law uses either the "concentration of 22 specific offensive odor substances" or the "odor index" as a control method. The head of the local government decides which method to adopt, and sets the control standard (No. 1 standard) on the site boundary line according to the actual situation in the area.
However, following these standards does not mean that there will be no complaints. People have different perceptions of odor, and odors can vary depending on the time of day, wind direction, humidity, etc., so there are cases where the odor seems too strong.
Odor control measures affect company image
In recent years, consideration for the environment has become important as a part of corporate social responsibility (CSR). If you wait until a complaint occurs before dealing with it, your company may be seen as lacking in consideration for the environment. As a result, your company's image will be damaged, and this will have an impact on your company's value and the ability to secure human resources.
In order to build good relationships with local residents and protect your company's image, it is not enough to simply meet legal standards. You need to be more proactive in taking measures against odors.
"Air quality" and related laws and regulations that should be considered at the same time as odor control
When the amount of malodorous substances in the air increases, the smell becomes stronger. Air contains various components, including malodorous substances. Effective odor control requires a perspective that comprehensively manages the air environment throughout the factory.
There are various laws and regulations that govern air quality management. All of them aim to protect the health and safety of employees and to prevent environmental pollution. Below are some examples.
Major laws and regulations governing air quality
- Volatile organic compounds (VOC) indoor concentration guideline values
Volatile organic compounds (VOCs) not only cause unpleasant odors, but also have adverse effects on the human body. The Ministry of Health, Labour and Welfare has established indoor concentration guideline values for 13 VOC substances.
- Industrial Safety and Health Act and related regulations
Among the specific odorous substances in the Offensive Odor Prevention Law, ammonia and hydrogen sulfide are also regulated by the Industrial Safety and Health Law. In addition, the relevant regulations of the Industrial Safety and Health Law stipulate the permissible concentration of harmful substances, carbon dioxide (CO2) concentration, temperature and humidity standards in the workplace, and require air quality measurements to be taken once every two months.
- Air Pollution Control Act and related regulations
The Air Pollution Control Act regulates the emission of VOCs. Among VOCs, toluene and xylene are specified as offensive odor substances and are subject to regulation under the Offensive Odor Control Act.
law |
the purpose |
Contents of the regulations |
Industrial Safety and Health Act |
Ensuring worker safety and health |
Work environment measurement, management of hazardous substances, installation of ventilation equipment |
Air Pollution Control Act |
Prevent air pollution |
Regulations on emission standards for harmful substances, equipment and methods |
Specific Chemical Substances Hazard Prevention Regulations |
Preventing health risks from chemicals |
Management of chemical substance concentrations and implementation of safety measures |
Organic Solvent Poisoning Prevention Regulations |
Preventing organic solvent poisoning |
Ventilation and protective equipment standards |
Occupational Health Act |
Protecting workers' health |
Implementation of health checkups and measures to maintain and improve health |
Air quality is not just about odor control; it is also directly linked to health and productivity
In recent years, the components and state of air have come to be called "air quality." Air quality has a significant impact on health and productivity. For example, the following effects have been proven:
- Health risks
Chemical substances and particulate matter (PM) contained in the air can cause a variety of symptoms and illnesses, including headaches, fatigue, and respiratory disorders. As a long-term risk, many substances have been identified as carcinogenic.
- Reduced productivity
As the concentration of CO2 in the air increases, work efficiency decreases. It has also been pointed out that increased concentrations of particulate matter (PM) can also lead to reduced productivity.
- Psychological impact
Clean air in the workplace has been shown to increase employee motivation. A comfortable working environment reduces stress and has a positive effect on psychological well-being.
Air quality is directly linked to employee health, improved productivity, and a comfortable workplace. Working to improve air quality, along with odor control measures, will lead to the development of your company.
What are the specific measures for air quality management in factories? - Achieving odor control, air quality improvement, and legal compliance -
What methods are there to deal with odors and improve air quality in factories? We will introduce some of the most common methods.
Main methods of air quality control for factories
- Monitoring System
In addition to odorous substances such as VOCs, we monitor the concentration of CO2 and particulate matter (PM), temperature, humidity, etc. Through constant monitoring, we can grasp the fluctuations in odors and air quality in real time and respond quickly.
- Space Purification Equipment
Harmful substances are oxidized and decomposed using oxygen cluster spray, plasma ion spray, ozone spray, photocatalyst, UV-C, hypochlorous acid spray, etc.
- Ventilation system
It expels harmful substances and provides fresh air.
- Filter Device
Captures and removes harmful substances.
- Other deodorizing equipment
Representative examples include deodorants, chemical cleaning, physical adsorption, direct combustion, and biodegradation.
Key points for improving air quality and combating odors
For proper air quality management, it is important to consider the following points:
- Analyze the cause and implement measures appropriate for the factory
The same measures will not produce the same results in all factories. It is necessary to analyze the causes of poor air quality, including odorous substances, and take appropriate measures for each factory.
- Making invisible odors and air visible through monitoring
Since odors become hard to notice once you get used to them, and air is invisible, quantitative management through monitoring is effective.
- A safe air environment ensures health and productivity
By controlling not only odors but also CO2, particulate matter (PM), temperature and humidity, etc., you can ensure the safety of the air environment. This reduces health risks to employees and improves productivity.
- A comfortable working environment improves work efficiency
By improving odors and air quality, the work environment becomes more comfortable, which is expected to reduce employee stress and increase motivation. By making it easier to work, we can also expect a decrease in employee turnover.
The latest solutions for air quality management in factories -Macnica 's proposals for ideal air quality and odor control -
Macnica offers "AQ-Factory" as an integrated air quality and odor control solution for factories. It makes odors that are difficult to notice visible inside factory facilities and outdoors (at the site boundary). It can create a safe and comfortable air environment. It allows you to take measures that consider not only compliance with laws and regulations, but also the preservation of the surrounding environment and the ease of work for employees.
Main Features
- Outdoor odor sensors constantly monitor odor leakage at the site boundary
- Air quality sensors monitor the air quality in the workplace, including VOCs, CO2, temperature and humidity
- It is also possible to monitor workers' vital signs.
- Purify your space with advanced sterilization and deodorization technology
- Integrated visualization and management via a platform
Together with nationally qualified odor assessors, we will investigate and analyze the impact and causes of odors in your factory and propose effective countermeasures. Furthermore, we will provide comprehensive support, including conducting demonstration tests, predicting the impact after implementation, and providing ongoing after-sales maintenance.
By installing a combination of high-performance sensors and various countermeasure solutions, you can comprehensively manage not only odors but also air quality.
Improving odors not only prevents complaints from neighbors, but also improves the working environment for employees. Realizing safe and comfortable air quality is expected to increase productivity and motivation, and reduce employee turnover.
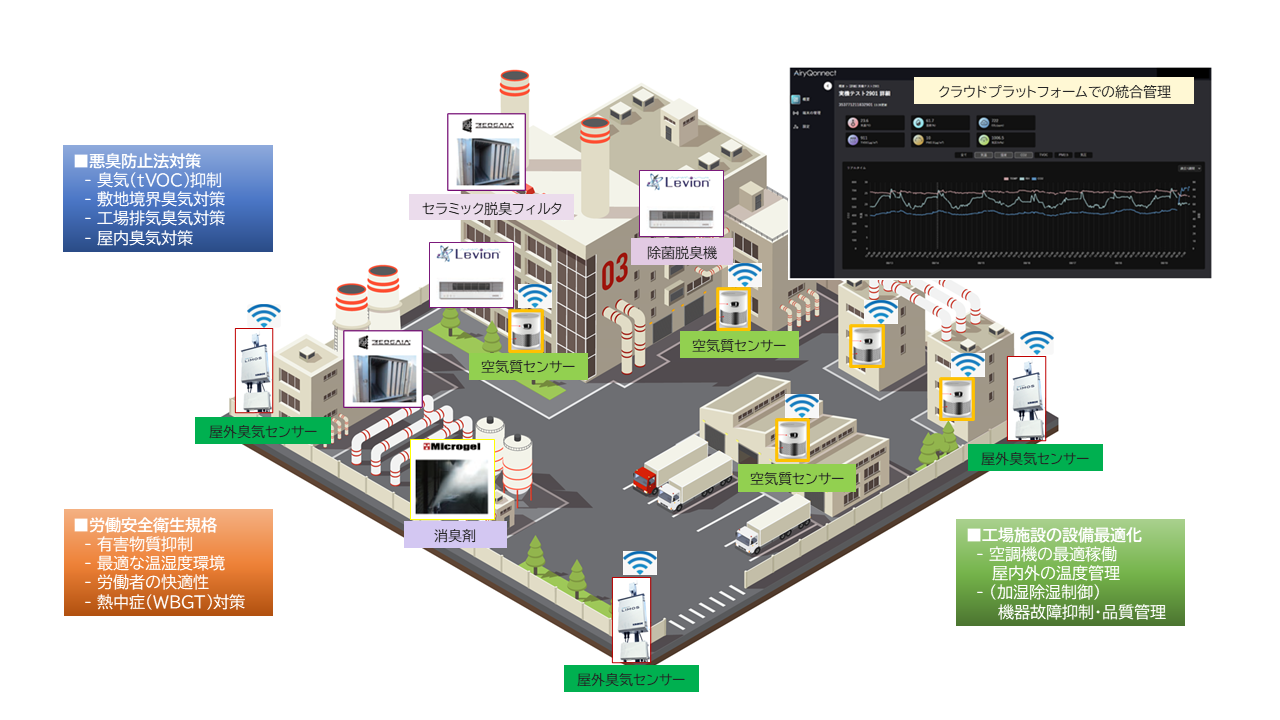
Figure: Outdoor odor sensors are installed at the site boundary to constantly monitor odor leakage to neighboring areas. Non-flammable ceramic deodorizing filters are installed in the exhaust ducts, and a scrubber deodorizing device is installed in the wastewater treatment tank. Odors are suppressed in work areas by spraying oxygen clusters. Indoor air quality sensors measure VOCs, CO2, temperature and humidity, optimizing the work environment. Measurement data is wirelessly shared, enabling integrated management on a cloud platform.
Summary
This time, we introduced odor control measures for factories. Odor control measures for factories are essential to consider the neighboring residents and the environment, and also lead to maintaining the company's image and securing human resources. It is important not to just comply with the law, but to take a proactive approach.
In addition, by working on improving air quality in conjunction with odor control, you can create a comfortable air environment that helps improve employee health and productivity. By constantly monitoring and quantitatively managing, it is possible to take measures against odors and improve air quality at the same time.
■Reference materials:
Ministry of the Environment "Odor Prevention Law: Aiming for a comfortable odor environment" (Ministry of the Environment)
https://www.env.go.jp/air/akushuu.pdf (accessed 2025-03-07)
"Interim Report - Summary of 24th to 28th Meetings" of the Study Group on Sick House (Indoor Air Pollution) Issues (Ministry of Health, Labor and Welfare)
https://www.mhlw.go.jp/content/001378160.pdf (accessed 2025-03-07)
"Use organic solvents correctly" (Ministry of Health, Labor and Welfare)
https://www.mhlw.go.jp/new-info/kobetu/roudou/gyousei/anzen/dl/120815-01.pdf (accessed 2025-03-07)
"Revision of standard measurement methods (summary)" by the Ministry of Health, Labor and Welfare, Pharmaceutical Affairs Bureau, Pharmaceutical Evaluation and Licensing Division, Chemical Safety Countermeasures Office (Ministry of Health, Labor and Welfare)
https://www.mhlw.go.jp/content/10803000/001290011.pdf (accessed 2025-03-07)
Inquiry
If you are interested in this article or would like to know more about AiryQonnect, please feel free to contact us.
Go to AiryQonnect service overview page
To return to the AiryQonnect service overview page, please click below.