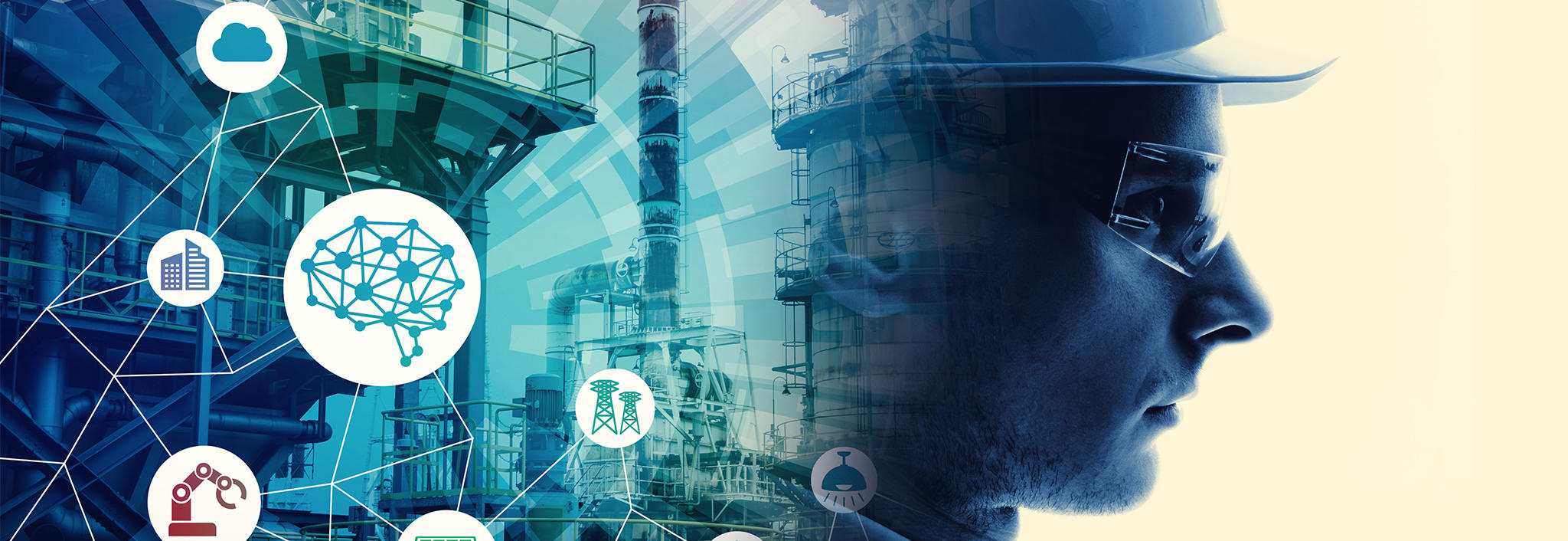
CBM ~Anomaly Detection, Failure & Degradation Prediction~
All you need is
"We want to optimize maintenance."
Only passion.
in the digital space,
We embody that “hot feeling”.
\ A popular example of anomaly detection! /
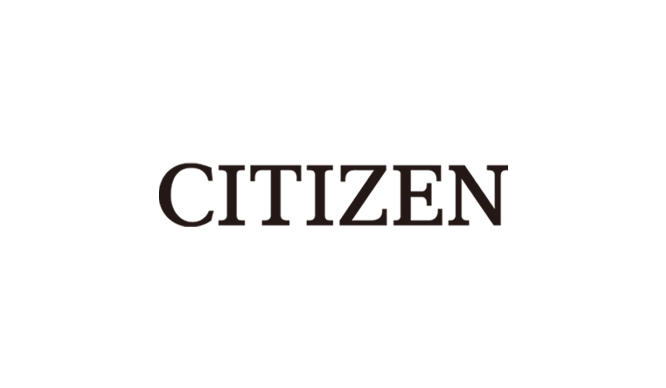
CITIZEN MACHINERY CO., LTD.
Optimize maintenance with machine tool failure prediction
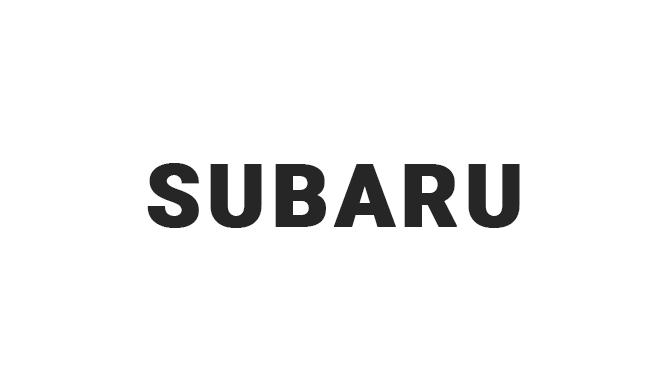
SUBARU CORPORATION
Development of anomaly detection technology for automation of drilling work in aircraft assembly
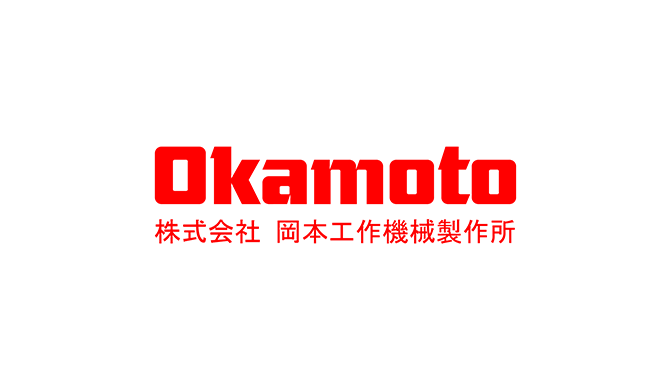
Okamoto Machine Tool Works,Ltd.
Transfer know-how of grinding process to AI
Are you facing challenges to CBM implementation?
At Macnica,
Introducing a system that allows you to easily build CBM,
We will guide you through the installation.
Toward maintenance optimization
Have you encountered such a problem?
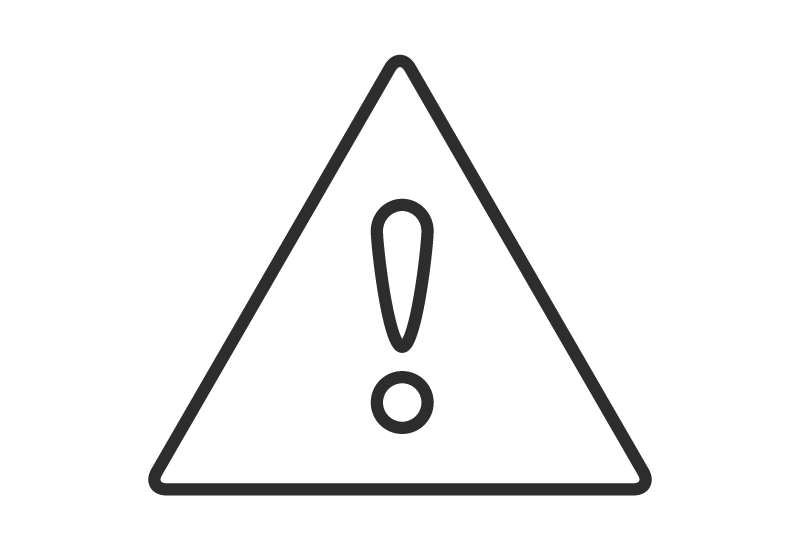
for dealing with sudden failures
"Excess parts stock"
'Wasteful staffing'
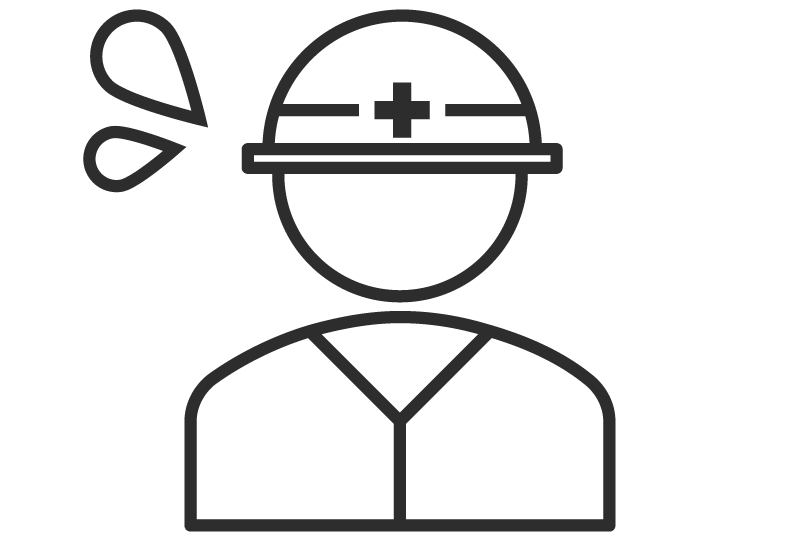
Due to personalization of maintenance
"Variation in work"
"Lack of successors"
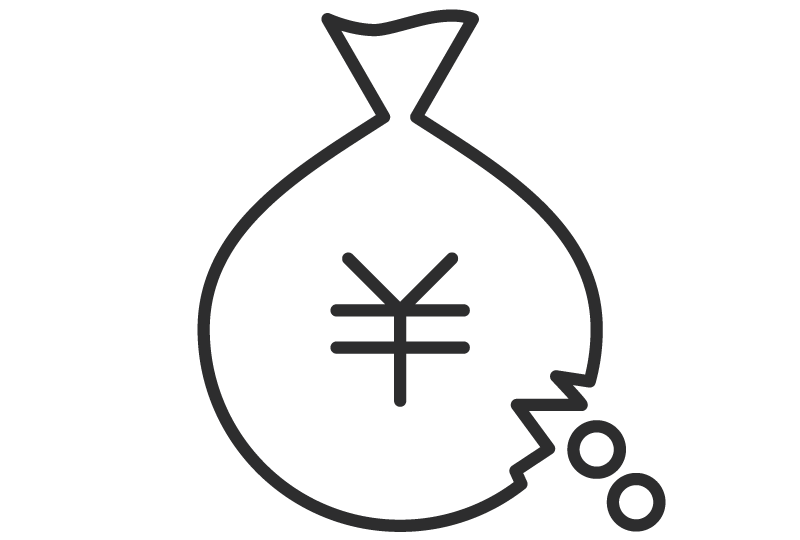
due to unexpected failure
"High maintenance costs"
"Prolonged downtime"
Macnica is the solution!
From setting issues to how to utilize technology,
until the optimal approach.
We will support you with everything.
What Macnica can do
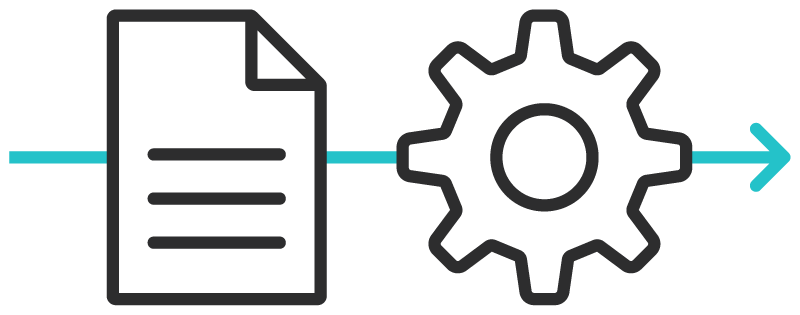
Accompanying support from planning to operation
One-stop support from clarification of objectives and issues to data collection, analysis, AI model construction, and actual operation. Realize the fastest actual operation.
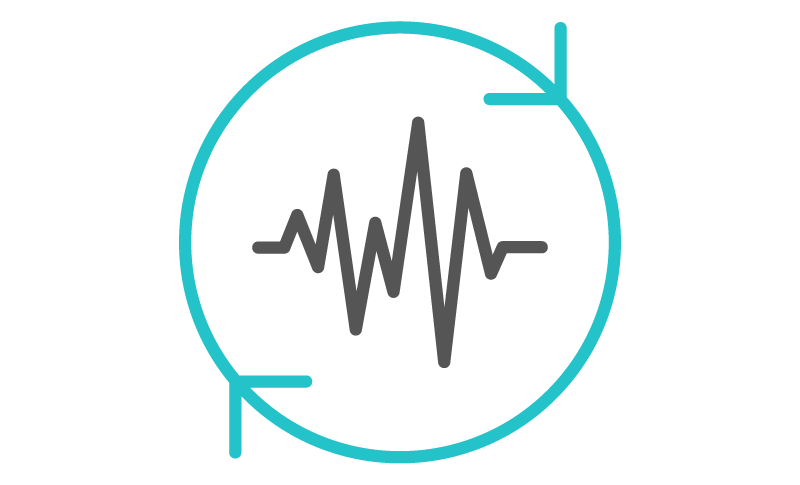
Understanding domain knowledge
Data utilization
We understand domain knowledge such as the mechanisms and physical phenomena of each facility, and implement and support data utilization with the most appropriate approach.
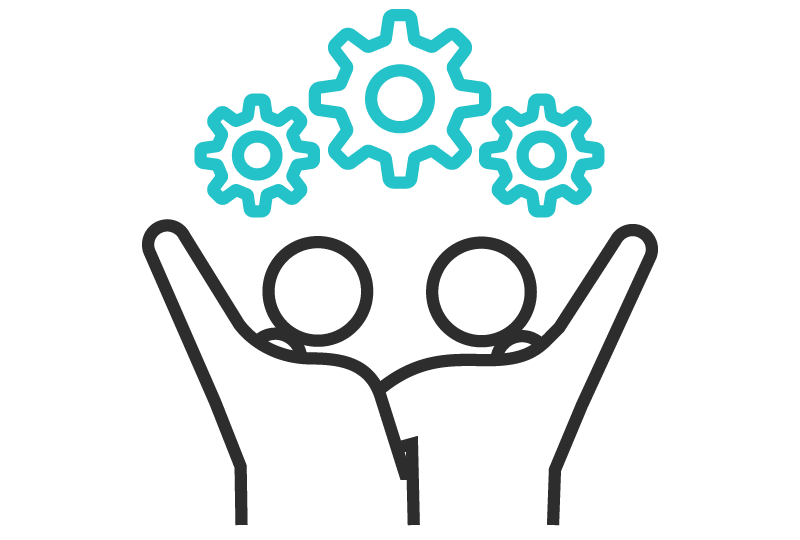
AI system construction and operation management
We accompany the operation management “after” introducing AI to the production environment so that the customer can concentrate only on optimizing maintenance.
Maintenance optimization flow and what to do
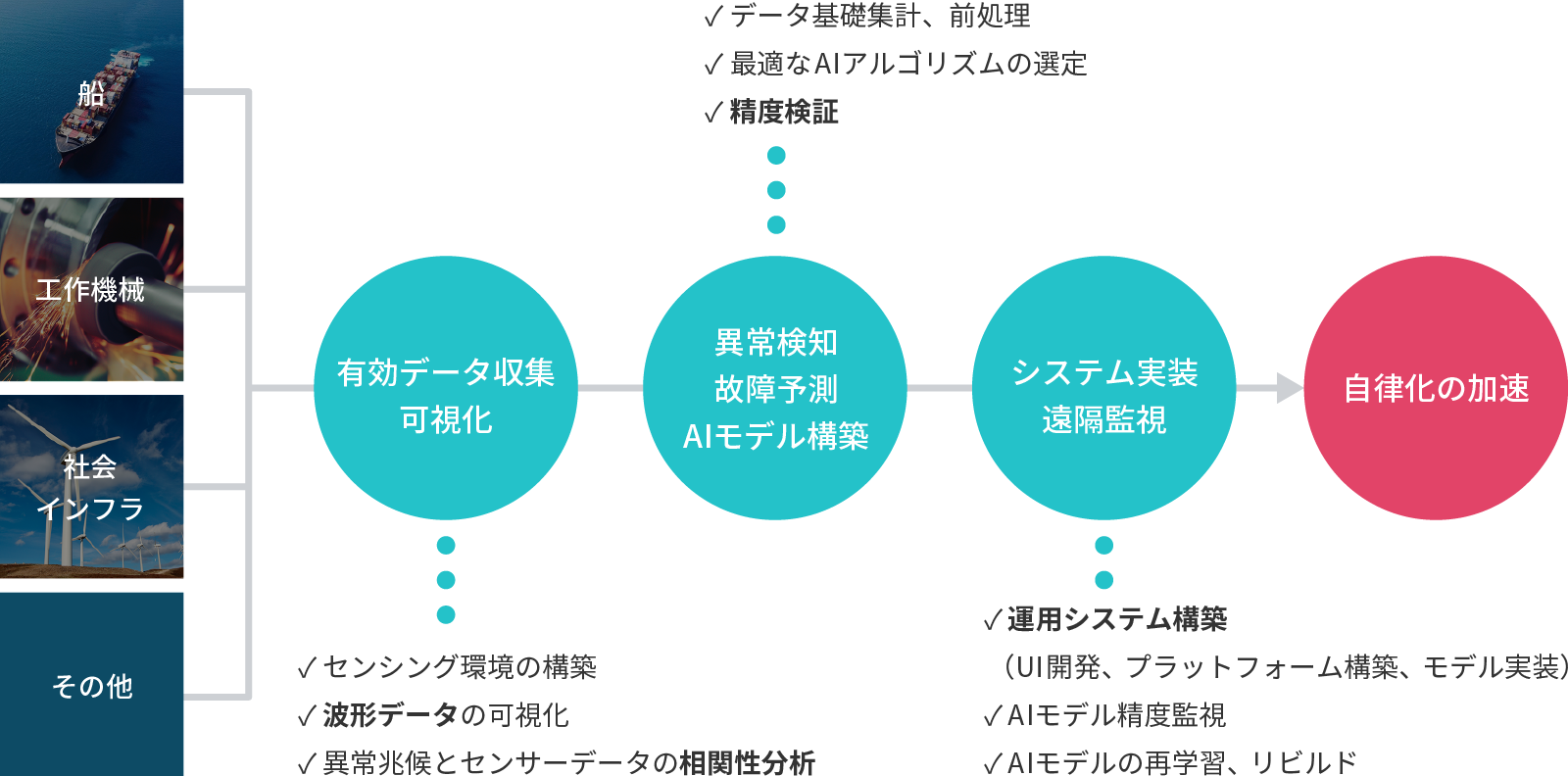
Target domains for anomaly detection and failure prediction
We have a track record in various industries
large ship
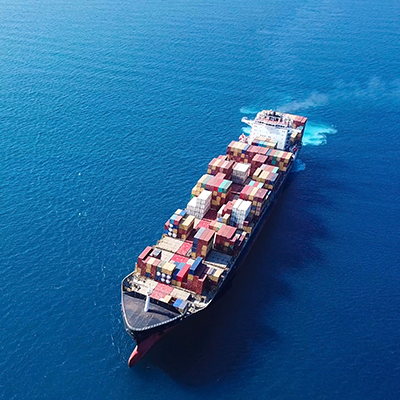
Semiconductor manufacturing equipment
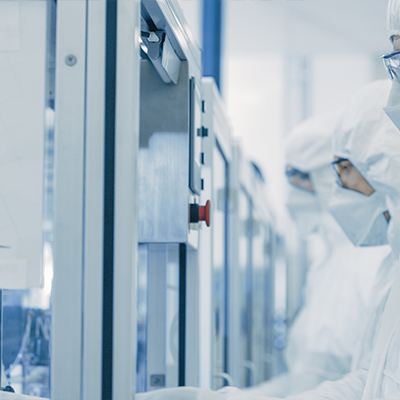
Processing machine
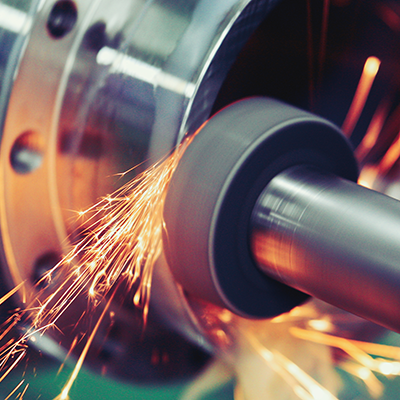
industrial robot
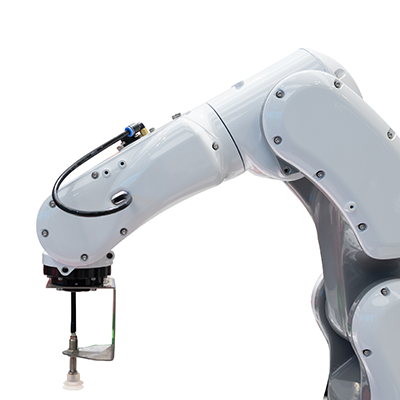
compressor
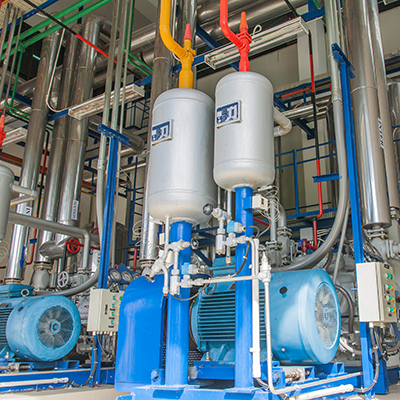
railroad
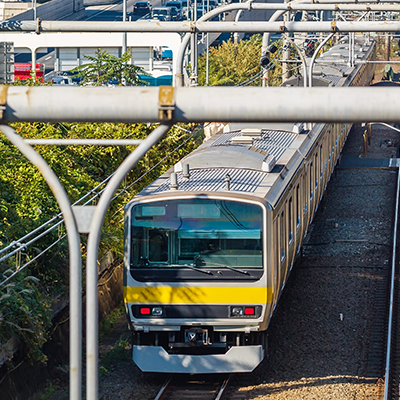
wind power
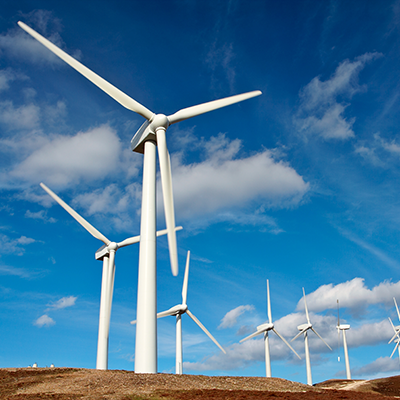
electric power
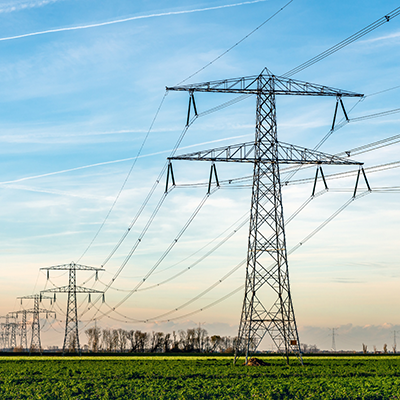
Case study
Social Infrastructure Equipment x Reduction of Downtime (Ship)
Target device |
Driving equipment for large ships (container ships, car carriers, bulk carriers, LNG carriers) |
---|---|
monitor item |
・
Main engine/supercharger/boiler/turbine/purifier/pump Temperature, flow rate, rotation speed, load, output, etc. for each facility ・
Disturbance factors (seawater temperature, wind speed, depth, wind direction, operational status, ocean current, fuel, wave resistance, frictional resistance, vortex resistance, etc.) |
System features |
・
Like a power plant, multiple large-scale facilities are linked and driven by intermittent operation. ・
There are a large number of maintenance inspection points, and constant monitoring is required. ・
There are many variable factors that affect equipment, such as sea conditions, operating conditions, positions, fuel, etc. ・
In the event of a malfunction, durability is required to allow operation until the next port of call. |
Points to care |
・
Analysis that considers the mechanism and physical effects of ship drive equipment ・
Modeling considering various variable factors such as ship operation status / route / ECA / weather |
- Although regular maintenance is being carried out, it is difficult to constantly monitor all facilities because many operations occur during the voyage.
- Downtime is prolonged because inspections and response methods are being considered at the dock at the time of port call.
- Since it is a manned operation, there is a risk of trouble due to the judgment of the crew.
- By using AI to detect equipment anomalies and predict failures, maintenance can be performed at the optimum timing before critical anomalies occur. Reduces man-hours for engineers.
- By using remote monitoring and AI predictions to grasp the status of ships on land, it is possible to give instructions on how to best respond in advance, thereby significantly reducing downtime.
- It is possible to formulate a maintenance plan when calling at a port.
- By introducing a CBM system to manned autonomous operation, we reduce marine accidents and losses due to non-operation.
Large industrial equipment × Downtime reduction
Target device |
Semiconductor manufacturing equipment |
---|---|
monitor item |
・
Wafer transfer robot: bearing failure ・
Vacuum dry pump: Adhesion of foreign matter ・
deterioration of the stage |
- Batch process equipment has a large impact because all wafers in production must be discarded when downtime occurs.
- Manufacturers recommend regular maintenance, but users often fail to do so, resulting in downtime on rare occasions.
- Semiconductor manufacturing factories have a high security level, and it is extremely difficult to remotely monitor equipment.
- By detecting signs of deterioration, it is possible to prevent sudden downtime.
- Condition-based maintenance (CBM) enables planned maintenance at optimal cost.
- Security issues are resolved by constructing a mechanism that allows the device to complete status determination.
Machine Tools x Prevention of Spoiled Goods (Machining Center)
Target device |
machining center |
---|---|
monitor item |
Missing or abnormal tool |
- Machining quality is affected by the occurrence of sudden abnormalities and defects in tools during machining.
- Special machine for mass production line: A large number of defective products are generated due to the processing of a large number of parts.
- Large-scale processing machine: Since processing takes several hours at a time, if processing is continued while an abnormality has occurred, it will lead to a large loss of material costs and processing time.
- Build a system that can detect tool abnormalities based on their status.
- Losses can be minimized by constructing a system at the edge that detects abnormalities in real time and feeds them back to control.
About CBM Solution
Contact us below
Click here to find out more!
Materials to understand the points of the CBM project
Related product
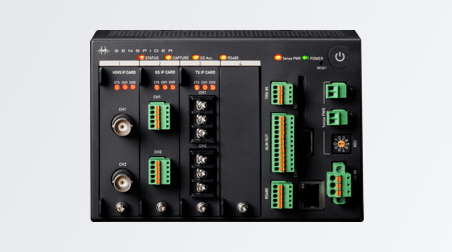
SENSSPIDER®
Ideal for getting started with manufacturing equipment data acquisition
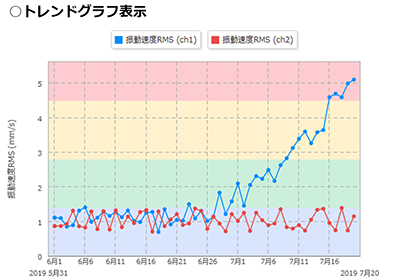
Sigma
Time series data analysis software
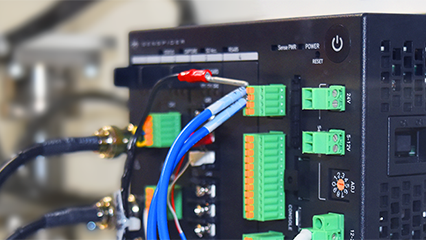
SENSPIDER Embedded Development PoC Kit
Optimal for function development of anomaly detection/predictive maintenance using AI in industrial machinery
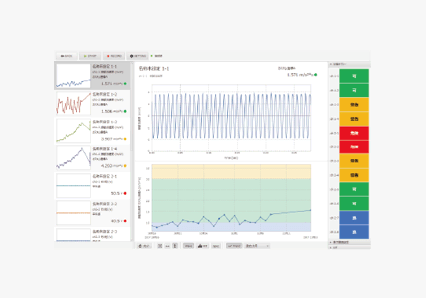
Sensing data analysis package
Sensing data analysis starter kit