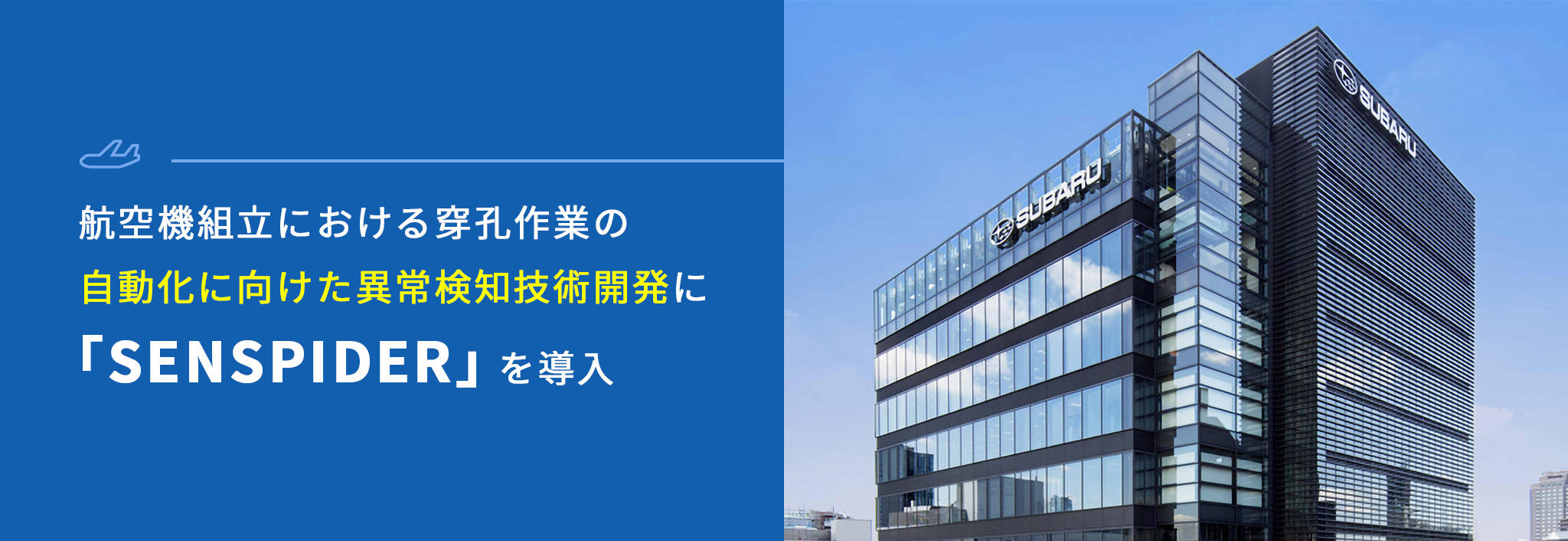
SUBARU CORPORATION Case Study
Supporting abnormality detection in drilling work with sensing technology and data analysis
The aerospace company of SUBARU CORPORATION, a leading company in the Japanese aerospace industry.
We develop and produce a wide variety of aircraft and components (main wings, tail wings, center wings, etc.) for customers represented by the Ministry of Defense and the Boeing Company of the United States. At the company's Handa factory, the drilling work that requires advanced technology in aircraft assembly has started to be automated in order to eliminate human intervention and enable drilling with stable quality.
This time, the company has introduced "SENSPIDER" as a drilling anomaly detection system, which is essential for advancing the automation of drilling work.
USER PROFILE
■Corporate information: SUBARU CORPORATION
■ Business content:
SUBARU is widely known for its automobiles, but its roots can be found in Nakajima Aircraft, which was established in 1917, just 14 years after the Wright brothers succeeded in their first powered flight in 1903.
Since then, we have inherited the technology and spirit of aircraft manufacturing, and currently develop and manufacture helicopters, passenger aircraft components, and unmanned aerial vehicles.
The company's Aerospace Company continues to lead the Japanese aerospace industry by establishing number one technologies in various categories.
summary
background
-
Extremely strict hole diameter requirements in drilling operations
-
Promoting automation of drilling work
-
Without a mechanism to detect abnormal pore diameters, a large number of defective products will be generated.
Attempt
-
Creation of a mechanism to detect the drilling state of the drilling machine in real time
-
Use SENSPIDER to collect vibration sensor data that can detect drilling conditions with high accuracy
-
Utilize the collected data and analysis software to build a highly accurate judgment algorithm from the dimensionless parameter RMS ratio
Outcome
-
Succeeded in building an anomaly detection system that detects anomalies in drilling conditions in real time
-
A big step towards automation of drilling work
background
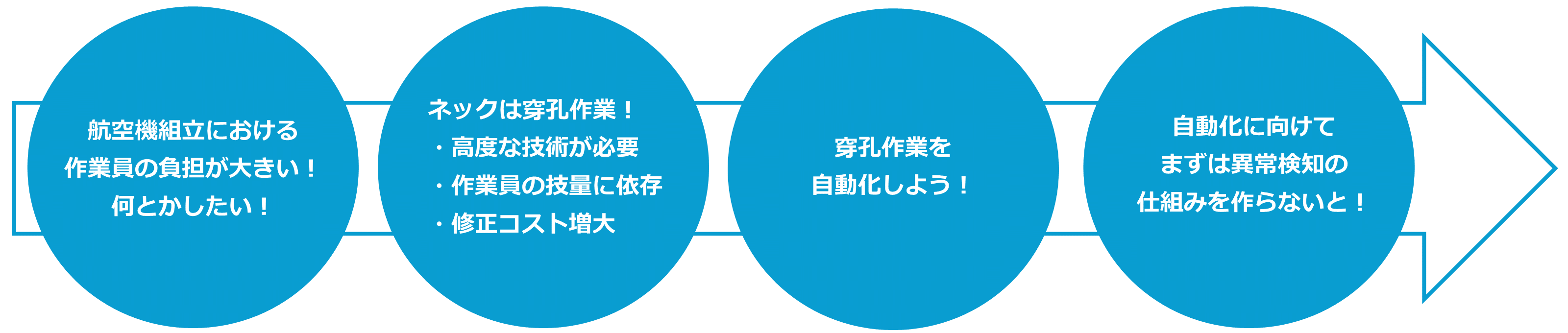
An anomaly detection system is essential for process automation!
The company manufactures center wings for aircraft (Fig. 1).
The center wing is the unit that connects the main wings of an aircraft.
Therefore, it has a complicated structure, which makes it difficult to automate the assembly process.
The most important part of the center wing assembly process (Fig. 2) is drilling.
It may seem that you can pre-drill holes in the parts and fasten them, but this is not possible when assembling the center wing.
This is because the hole tolerance required for fastening is very strictly defined in order to prevent fuel leaks and vaporized fuel gas leaks that can lead to serious accidents.
Therefore, it is necessary to assemble with high technology.
In fact, if the tolerance of this hole does not meet the requirements, it will have to be corrected, which is costly and labor intensive.
Therefore, in the drilling work, which is important in aircraft assembly, if the tolerance of the hole does not meet the requirements, an abnormality detection mechanism is required to notify the abnormality.
Against this background, the company has decided to develop anomaly detection technology in order to promote the automation of drilling work.
Figure 1: Aircraft center wing
Figure 2: Example of Aircraft Assembly Procedure
Attempt
Introducing Macnica 's sensing technology to build an anomaly detection system as an add-on to existing equipment!
When introducing SENSPIDER to the company's existing equipment, the following efforts were made.
❶ |
Parameter setting using "normal drill" and "chipped drill" |
❷ |
Development of an anomaly detection system that acquires "eight lines of data" and linkage with SENSPIDER |
❸ |
Analyzing vibration data from a “cracked drill” |
*Registration required for viewing/downloading
download moreA big step towards process automation with the introduction of "SENSPIDER"!
This time, SUBARU CORPORATION, Ltd. introduced "SENSPIDER", which enabled detection of abnormalities in drilling from vibration data, and made a big step towards automating drilling work.
Currently, we are building a system that will activate an alarm in the event of an anomaly in drilling by incorporating this anomaly detection system into a drilling machine developed by the company.
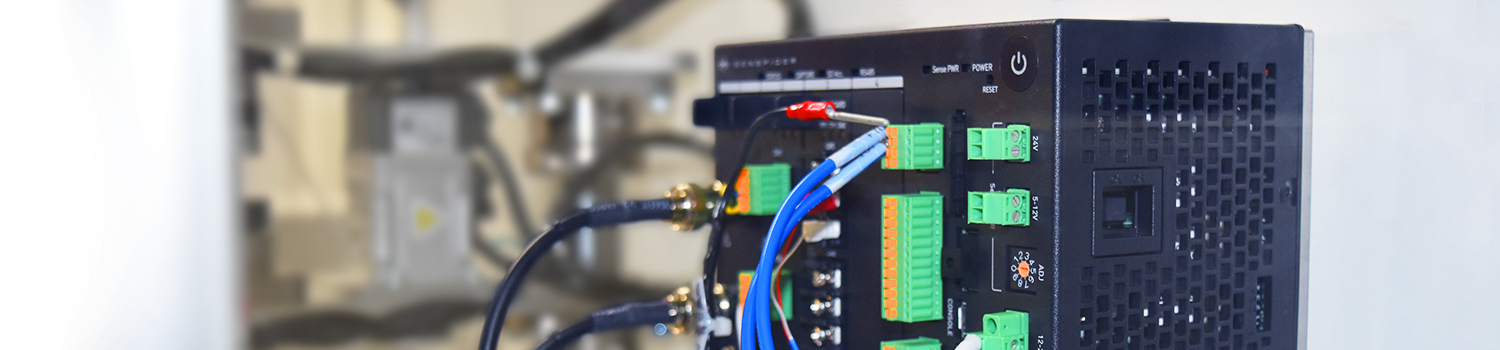
▽ What is the all-in-one unit "SENSPIDER"? ▽
Our approach to predictive maintenance and anomaly detection
*Registration required for viewing/downloading
▽ Our approach to "anomaly detection/failure prediction" ▽
*"SENSPIDER" is a registered trademark of Macnica