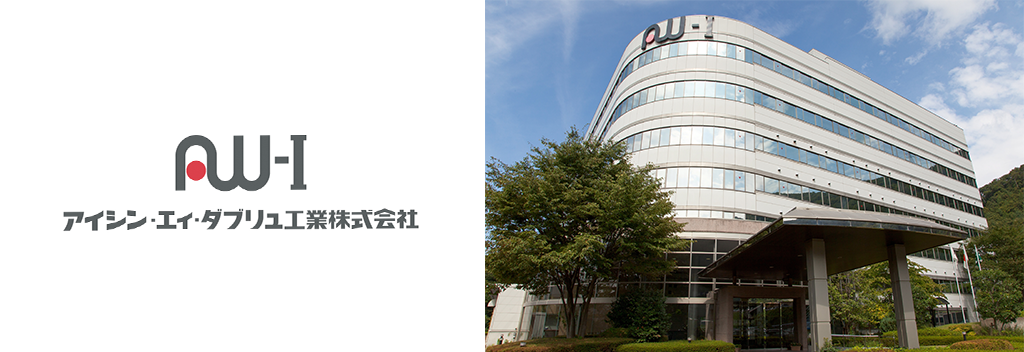
アイシン・エィ・ダブリュ工業株式会社様事例
少数精鋭チームが挑む生産ラインの品質管理AIを自社開発
アイシン・エィ・ダブリュ工業(AW-I)は、トルクコンバータ(T/C)とトランスミッション(T/M)の専門メーカーだ。
30年以上に渡り高品質なT/Cを生産できる理由は、同社が長年培ってきた品質管理(以下QC)と、世界に誇る最新技術を取り入れた高度な生産ラインにある。
2018年8月、同社はスマートな工場を達成するために、既存のQCとAI技術を組み合わせて生産ラインを管理する「DQC(デジタル・クオリティ・コントロール)」の実現を目指すプロジェクトを開始させた。
最初の取り組みはレーザ溶接工程のQCにAIを活用すること。
しかしAW-Iの真の目的は、AIの活用を単一工程の改善で終わらせることではない。社内のあらゆる課題解決へ水平展開し、コア技術全体の底上げに寄与することである。
ここでは、チームの立ち上げからAIの技術開発に至るまでの取り組みについて話を聞いた。
USER PROFILE
■企業情報:アイシン・エィ・ダブリュ工業株式会社
■事業内容:
「品質至上」
アイシン・エィ・ダブリュ工業株式会社は、1983年の創立以来「品質至上」の基本理念のもと、オートマチックトランスミッションの主要部品である、トルクコンバータとトランスミッション部品の専門メーカーとして、人と環境にやさしいクルマ社会の発展を目指し、長年培ってきた固有技術と技能に日々磨きをかけ、独自の価値創出に取り組んでいる。
サマリー
背景
・クリーンでスマートな工場の実現
・AIを活用した高度なQCの確立
・AI技術開発プロジェクトの推進
目的
・時間のかかる品質管理の効率化
・AIの活用による不良要因の推定および、負荷軽減
課題
・AIの開発サイクルをクイックに回す知見や技術の習得
・AIで扱うデータを準備する技術の習得
・AIを水平展開しやすい技術の習得
取り組み
・開発手法や知見の習得により開発を加速
・IoT技術を駆使して品質を語るデータを収集
・AI分析に向けた前処理プログラムの開発
・ものづくり×AI技術に精通したチーム活動を推進
こだわり
・凝り固まった思考から脱却できるOJTの活用
・すぐに現場で使えるツールの選定
・工場と連携し、AIを構築しものづくりを支援
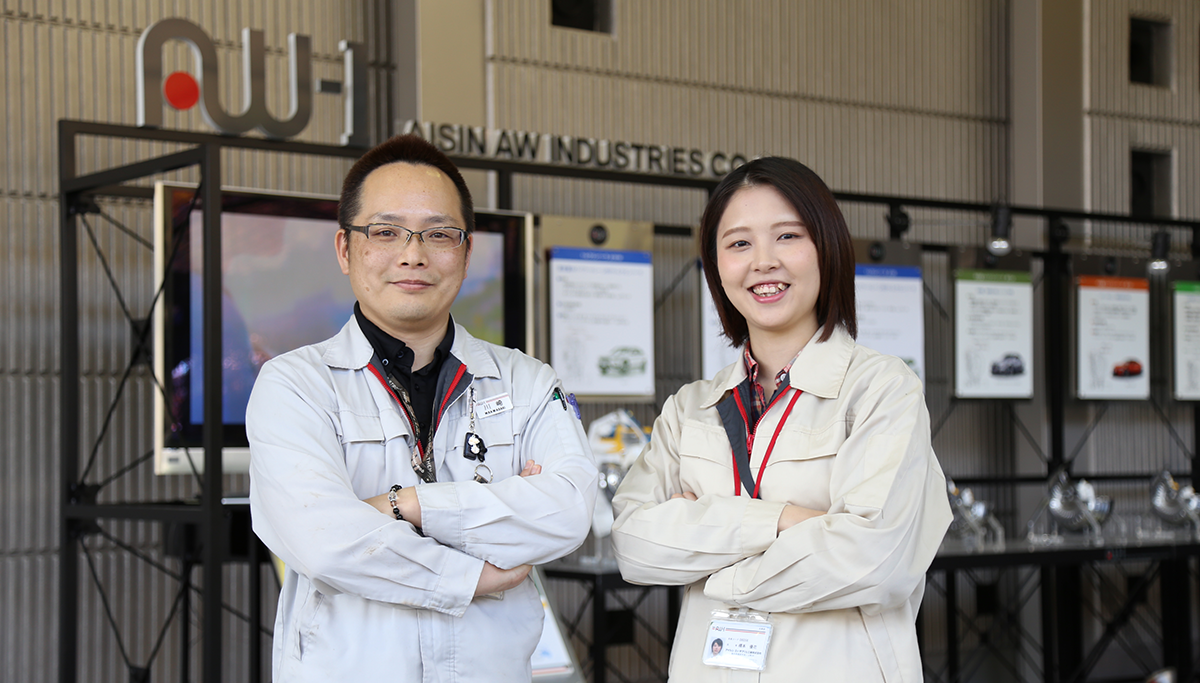
アイシン・エィ・ダブリュ工業株式会社 生技開発部 川崎 正哉 氏(左)
アイシン・エィ・ダブリュ工業株式会社 生技開発部 橋本 優花 氏(右)
株式会社マクニカ 楠 貴弘、本村 健登
背景
高度な生産ラインのQCにAIを活用
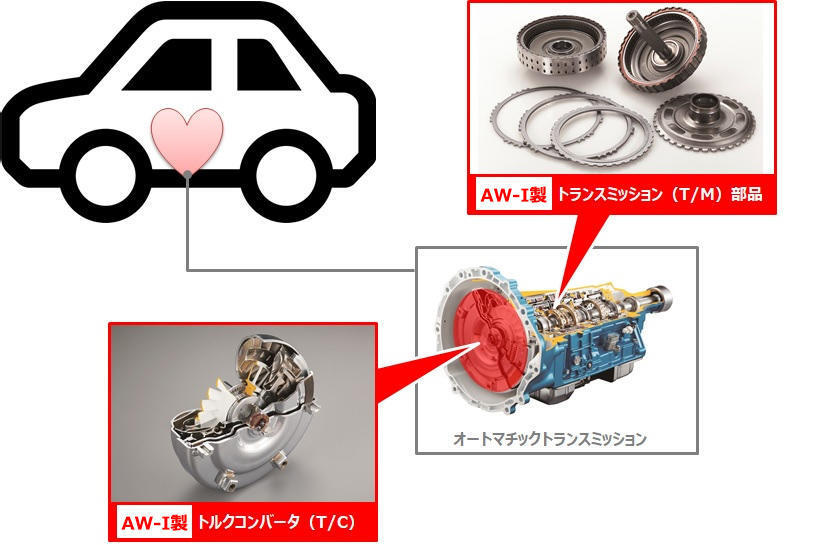
アイシン・エィ・ダブリュ工業(AW-I)は、トルクコンバータ(T/C)とトランスミッション(T/M)の専門メーカーだ。
創業時はプレス加工を得意とするT/Cの部品メーカーであったが、市場からの要望によりプレス以外の加工や組み立て作業にも挑戦し、1989年には同社初のT/C Assy製品(組み立て済み製品)の出荷に成功した。
その後30年以上に渡ってAT車の主要部品であるT/CとT/Mを主力製品として、経営理念である「品質至上」のもと、高品質なモノづくりに取り組んでいる。
ー 川崎氏
我々は革新的な生産技術の開発を成し遂げ、クリーンでスマートな工場の実現を目指しています。
クリーンはどの工場にも求められる要件です。
さらにスマートであること、つまりはどこで誰が生産しても安定した品質を達成し、AW-Iの誇る高品質な製品を無駄のないコストで生産できる工場をつくりたいと考えています。
これらの目標は、従来のQCのみでは達成できません。
そこで我々は、これまで長年に渡って蓄積してきた情報をデジタル化、AIによる分析技術を活用し、生産ラインのQCを高度化するDQC(デジタル・クオリティ・コントロール)の実現に向けたプロジェクトを立ち上げました。
膨大なデータを分析して活用できるAIを開発するチームは、川崎氏を含め3名の少数精鋭。
AI技術開発を専任とするデータサイエンティストである橋本氏はこのように語る。
ー 橋本氏
IoT技術を得意とするメンバーが生産ラインからデータを収集し、AI技術担当の私が様々な技法を活用して分析しています。
生産技術に精通した川崎がチームを統括しているため、現場を強く意識した現実的なDQCの実現に向けた開発ができます。
また、AIによる分析に必要なデータが追加で欲しい場合、少人数であるため、すぐにチーム全員へ提案でき、効率的にプロジェクトを推進できています。
課題
自社内のAI開発チームをゼロから立ち上げる
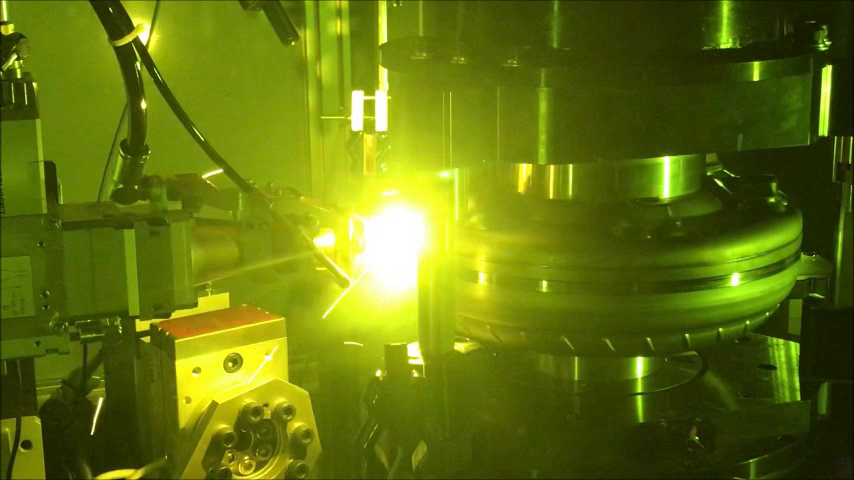
レーザ溶接工程は、従来の溶接工程よりも優れた加工ができる一方、工程の管理項目が多く不良が発生した際、要因を特定するまでに時間がかかる。
特に複数の要因が重なった不良はさらに複雑で特定は困難を極める。
そこでAW-Iは、人が気付けない要因を推定するためAI活用の開発に着手した。開発では以下の内容が課題となった。
1. データ分析・AI開発サイクルをクイックに回したい
DQCの実現には、AIの開発活用だけでなく、データ収集をはじめ、要因分析運用に向けたシステムの構築、業務シナリオの検討といった様々な要素に対応しなければならない。
また、これらの課題解決を最短経路で進めるには、開発を始めやすいパッケージ型でありながら、分析要件に即した形へカスタマイズできるAIツールが不可欠となる。
2. AIの扱うデータを準備する方法が知りたい
AIを活用するには、過去に収集した膨大なデータに加えて、分析を高精度化するため加工点に近いデータを取得、前処理し、入力データへ変換する作業が不可欠だ。
加えて、変換後のデータを使ってAIが期待通りに機能するかを繰り返し確認する作業も必要となる。
3. AIに精通したチームを社内で運営したい
同社は、AIをレーザ溶接工程だけでなく、将来的には社内にある様々な課題の解決に活用したいと考えている。
そのため、AIを開発するだけでなく、チーム運営の技術支援が必要。
こうした事情を理解し、最先端のAI技術情報を整理、最適な開発方法を提案してくれるパートナーを探していた。
取り組み
少数精鋭のチームでは手が足りない範囲への細やかな支援
FA革新のキーワードである「Industry 4.0」は、AW-Iが生産ラインへAI技術を取り入れるきっかけとなった。
既に2017年からIndustrial-IoT(IIoT)の推進に取り組んでいた同社は、2018年8月からマクニカをパートナーとしAIを活用してDQCを実現するプロジェクトに着手。
ー 川崎氏
今回のプロジェクトではAIを要因分析に適用するため、自社で技術開発できる体制をつくることが必須要件でした。
マクニカはAIを自前化するために必要となる活用手法やその知見を提供してくれました。
ツールの提供に限れば他社からの提案もありましたが、マクニカは我々の技術レベルを確認しながら、AI導入の効果や独力で学ぶための下地となる技術情報の共有をはじめ、運用するために不可欠な設計技法の提案まで、幅広く支援してくれました。
マクニカでスマートファクトリーのコンサルティングに従事する本村はこのように振り返る。
ー 本村
最初にお会いした際、AW-I様ご自身でQC向けのAIを開発するプロジェクトを推進したいと伺いました。
そこで私たちは、製造工程におけるドメイン知識や最新AI技術の知見を豊富に備える当社のAI Research & Innovation Hubとの連携を軸とした提案を作成しました。
マクニカのサポート内容
1. AI技術開発を加速する開発手法やツールの提案
まず、マクニカはAW-Iの課題解決に最適なAI開発手法を提案した。
ー 楠(AI Research & Innovation Hubプリンシパル)
私たちは、世界中の最先端のAI技術を日々調査しています。
今回のプロジェクトではスピード感のある課題解決を目指し、AI開発手法やツールなどを提案、ツールに不足するアルゴリズムの開発も支援させていただきました。
本プロジェクトでは、AW-Iへ3種類のAIツールを提案し、AW-Iが最終的に製品を選定した。
ー 川崎氏
我々のこれまでの知見から不良品を計測した際のセンサーデータと加工データの間に、ある程度の結びつきがあることを把握しており、AIツールでは、センサーデータを分析し、要因のランキングを出力できる機能を期待していました。
実際、マクニカと意見交換をしながら必要な要件を絞り込み、当初の目的に合致する製品を選定できました
2. 計測データをAI入力データへ変換する支援
続いて、AW-Iがこれまでに収集した膨大な情報を、AIの入力データへ変換する、データ変換プログラムの開発を支援した。
まず、マクニカがデータ変換プログラムをPythonで実装し、変換後のデータがAIの入力として正しく機能することを確認した。
その後、AI技術開発担当の橋本氏へプログラムと開発ナレッジを引き継いだ。
ー 楠
AIの入力データを準備するためには多くの時間が必要です。
そこで私たちがこれまでに蓄えたAIの知見を基に、データの時間軸の扱い方や、波形の整形方法、学習のためのラベリングといった作業を支援し、橋本様とデータの扱い方の妥当性について確認を重ねながらデータ変換プログラムの下地を作りました。
ー 橋本氏
データ変換プログラムの開発だけでなく、プログラムの設計や実装についても共有いただけました。
さらに、将来的に我々がデータ変換を独力で開発できるよう、Python言語の基礎もハンズオン形式で教えていただけました。
今では、独力でPythonや開発ツールについてさらに学習し、我々自身でデータ解析プログラムを開発できるようになりました。
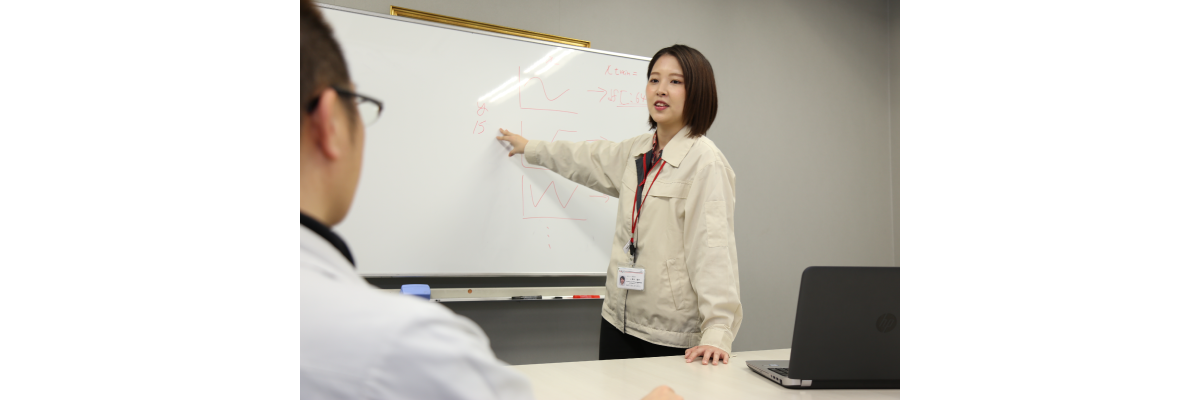
3. AI関連技術のナレッジトランスファー
今回のプロジェクトでは、AW-IはAI技術に精通したチームを社内で運営開始することに成功した。
また、チーム運営に向けて、マクニカはAI技術開発チームの運営を支援する「ナレッジトランスファー」を実施した。
ー 川崎氏
これまで社内にノウハウがなかったAIを開発活用する際の進捗管理方法や、開発プロセスの立て方、AIの精度を管理する方法などマネジメントに関する情報を得ることができました。
また、技術の要点や、最新の論文から収集した技術情報、開発ツールの使い方といった技術面での知識も多く支援いただきました。
プロジェクト開始直後の早い段階からハンズオントレーニングにより、様々な知見の習得や技術について質問する機会を設けていただけたため、AIを活用する足場を固めることができました。
また、ナレッジトランスファーはマクニカにとってもメリットがある。
ー 本村
ナレッジトランスファーを実施せず、何かあったら声をかけて欲しいという体制のプロジェクトの多くは、PoCの段階で頓挫します。
プロジェクトを成功に導くためには、お客様の中にもAIエンジニアが居ることが大切であり、AIエンジニア育成のためにナレッジトランスファーを実施しています。
お客様がAIを深く理解することにより、そういえばこういう課題もあってね、といったご相談も増えるため、私たちにとっても大きなメリットがあります。
本プロジェクトでのこだわり
IoT×AIに生産技術を組み合わせ、スマートな工場の実現を目指す
最後に、それぞれのメンバーから本プロジェクト成功に向けてのこだわりを聞いた。
1. 凝り固まった思考から脱却するOJTの活用
本プロジェクトでは人材育成が大きなテーマとなった。
ー 川崎氏
生産技術的な考え方を身につけなければQCのシステムを設計することはできません。
しかし先に生産技術を深くまで理解してしまうと、考え方が凝り固まり新しい発想が生まれにくくなります。
そこで、各メンバーが生産技術、IoT技術、AI技術それぞれに特化し、チーム内の意見をうまくミックスするようにプロジェクトを推進しました。
ただ、AI技術は橋本に任せていますが、私自身もAIのことをある程度理解する必要があり、また橋本も生産技術について理解する必要があると考えています。
こうした情報交換はOJTとして開発をしながら技術を学び合いました。
マクニカのハンズオントレーニングも、互いの理解を深める上で役に立ちました。
2. すぐに誰でも使えるツールの選定
今回開発しているAIは、今後の水平展開を踏まえPoCの先を見据えた、実運用時に快適な操作ができるGUIの開発ツールをマクニカと共に選定した。
ー 楠
AIのツールにはそれぞれ癖があります。
生産ラインのデータを扱えることはもちろんのこと、GUIにより不良要因の特定に必要な情報をグラフィカルにわかりやすく表示でき、且つ分析結果の説明性に富んだものを選定しました。
ツールの分析結果を理解する時間を短縮できるだけでなく、データ分析やAIの本質を学べる環境としても推奨いたしました。
3. 生産現場と連携しAIを育て、完成したAIで支援する
AIが分析するデータと、現場の知見を擦り合わせる役目はIoT技術を担当するメンバーが担っている。
ー 川崎氏
AIの入出力データを生産現場の作業員へ直接見せることはありません。
工場は原理原則に基づいて活動しているため、AIへの入力データに疑問がある場合にはIoTを担当するメンバーが生産現場へ足を運び、情報を収集します。
こうした活動により、IoTを担当するメンバーがデータをすべて揃え、橋本がAIの開発に注力するという非常に効率的な開発を実現できます。
さらに工場へのAI活用方法については、
ー 川崎氏
AIは学習に基づいて成長するため、AIを構成するひとつひとつのパラメータがどのような意味を持っているかを説明できません。
そのため、説明性が求められる生産ラインのQCすべてをAIに任せることはせず、加工工程の不良を抑え込む役割としての裏方的な活用を進めています。
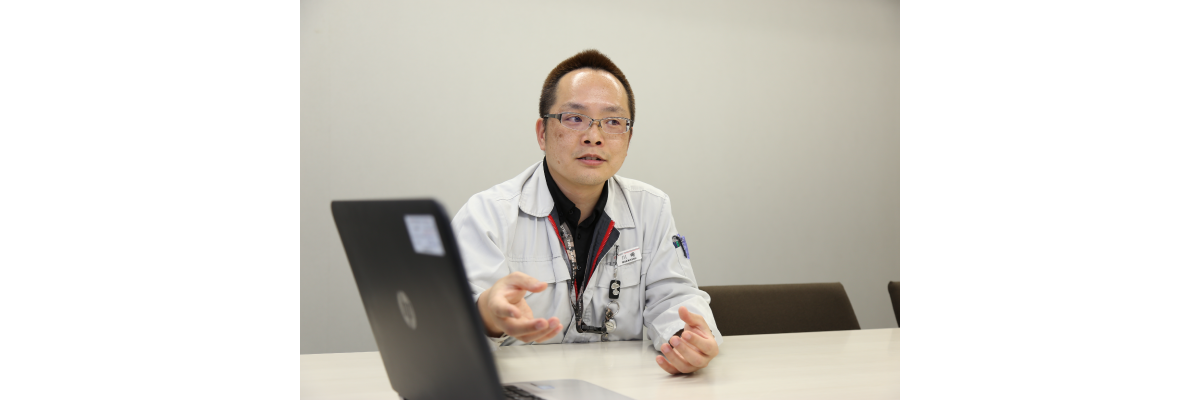
今後
生産現場のさらなるAI活用に向けて動き出したAW-I
AIによってDQCを実現する取り組みは、将来的にはレーザ溶接工程だけでなく、あらゆる生産工程へ水平展開できる。
AW-Iの今後の目標について川崎氏はこのように語る。
ー 川崎氏
DQCを適用することにより、検査工程ではなく加工工程で不良を押さえ込むことができるようになるでしょう。
また、不良自体を作らないようにする要因解析や不良予測といったAIの技術応用にも期待しています。
今後はさらにAI活用を進め、スマート工場へ強く貢献できる新しい技術を自分たちの手で作っていきたいですね。
※本文中に記載のある情報、および会社名は2020年7月時点のものです。