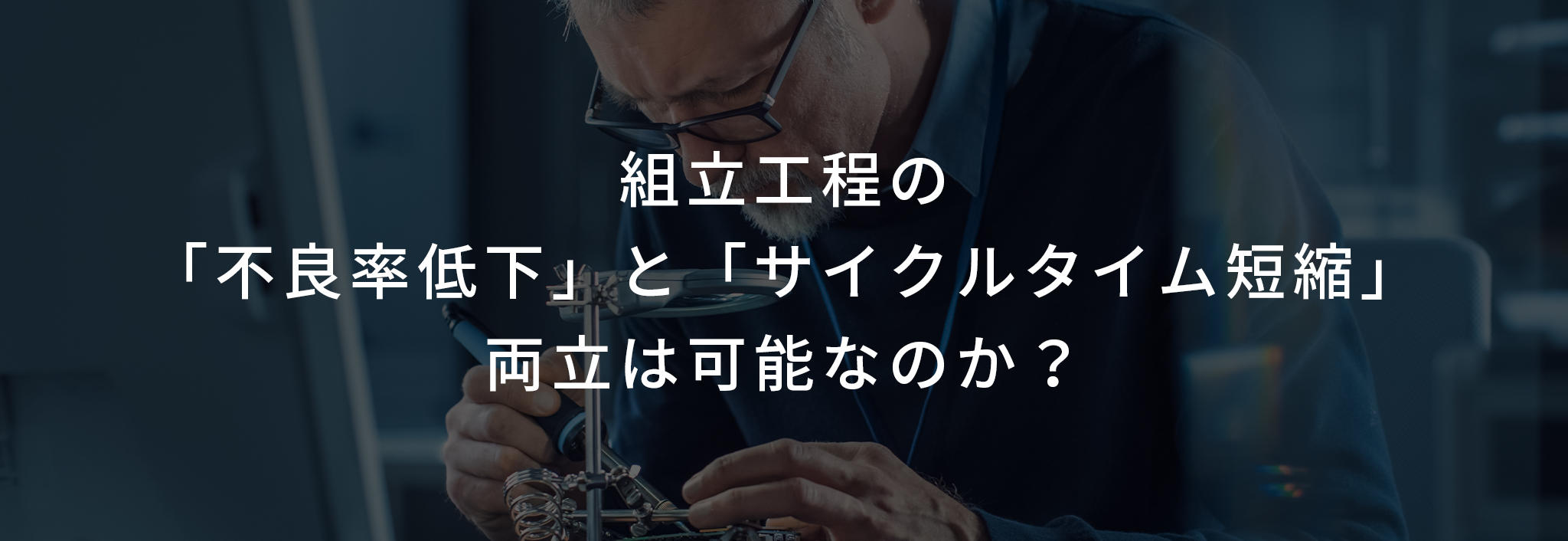
I'm sure everyone is feeling the boom in the in-vehicle electrical system market.
The world is changing with the improvement of autonomous driving technology and the acceleration of the sharing economy, but it is said that the demand for in-vehicle electrical systems will continue to grow for the next 10 years.
However, it cannot be denied that there is an element of anxiety.
Domestic manufacturing industry unable to withstand ever-growing demand
不安要素として、需要の伸びに対応するための「人材不足」と「安定供給」という大きな課題を解決する必要があるのですが、国内の多くの企業が伸び続ける需要に対応する準備ができていません。
課題解決として、億単位の投資による自動化など「ロボット」の導入が進んでいる企業もありますが、日本の製造業は約99%が中小企業です。
It is unrealistic to think that small and medium-sized enterprises that support Japan will be able to take the initiative in promoting robots, which requires a large investment to launch another company within 10 years.
Unfortunately, there is no way to save all manufacturing at this stage.
However, if we focus only on the "assembly process", we see a ray of light.
There was a hint in the overseas manufacturing industry!
In recent years, have you noticed that the quality of overseas products has improved regardless of whether they are automotive parts?
In the past, it was common knowledge that "whether it's cheap or not" depends on the diversity and understanding of the people working at overseas factories.
However, AI is now used to level out such "diversity" and reduce the defect rate in the assembly process.
What will happen if this system is introduced to Japan?
Serious national character × AI effect is tremendous
No matter how serious the national character is to work, it is difficult to prevent all careless mistakes.
Even in the assembly process, the takt time changes depending on the skill level of the workers, so it is difficult to determine where the bottleneck is, and it is difficult to "reduce the defect rate" and "improve the cycle time".
However, by implementing AI, there is a possibility that both "shortage of human resources" and "improvement of cycle time" can be achieved!
Specifically, you will be able to imagine it better if you see it.
As you can see, AI detects work errors in the assembly process.
You can see that the assembly process is overwhelmingly optimized simply by multiplying the "existing human resources" with AI, without the need for instructors or inspectors to be permanently stationed.
What is necessary for this AI implementation is "AI model learning" and "shooting camera" related to work, so you can see that it can be realized with less investment than introducing an automated robot.
If the cycle time changes, the light will come to the "lack of human resources"!
In the assembly process like the demonstration video, it is possible to shorten and improve the cycle time by implementing AI.
At first, our mission is to prevent mistakes in the assembly process, but as we accumulate data, we can find bottlenecks where mistakes are likely to occur.
By continuing to make these improvements, we will be able to appropriately allocate personnel according to skill level, and we will be able to actively recruit staff from overseas depending on the work.
Instead of traditional language guidance, AI-recorded appropriate work videos can be used for training, and AI can also be an instructor for work errors.
Both are fully possible depending on the mechanism!
In order to meet the ever-growing demand, it is necessary to have a "stable supply" of products and "securing human resources", but there is a limit to the conventional paper-based check sheets and the cycle time that relies on skilled workers.
There is no doubt that the improvement of the assembly process by implementing AI will be a great weapon for responding to such changes in 3, 5 and 10 years.
AI implementation can be said to be a realistic means of realizing stable manufacturing with a low defect rate by making full use of existing human resources with less investment than introducing robots.
For those who want to learn more! Free lecture video
These efforts to reduce cycle time are attracting attention in Japan as well.
Macnica held a webinar titled ``An Approach to QCD Improvement in Assembly Processes.''
In the article below, you can view the recordings and lecture videos from the day of the event for free.
I want to know more detailed examples! If you are interested, please check it out.
\ Also pay attention to Q&A about serious questions on site /
■ I want to read together ■
"Approach to improve QCD of assembly process ~ Event report delivered by Grareco! ~"