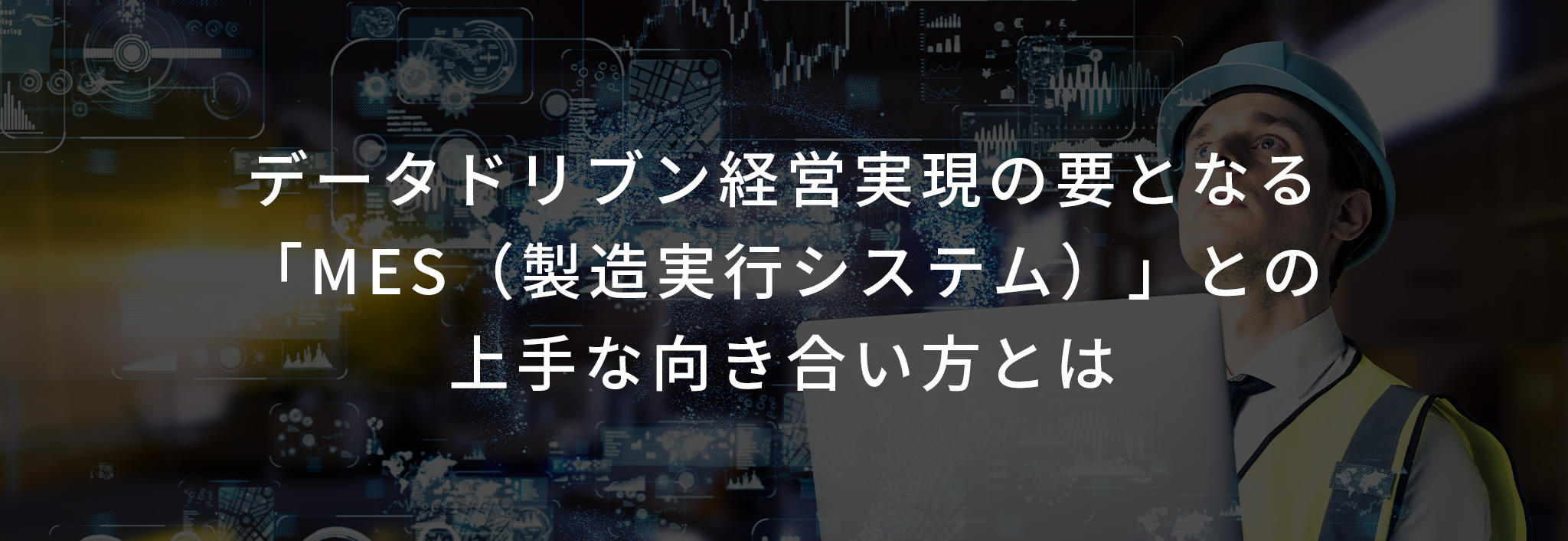
Japan's manufacturing industry is often talked about as lagging behind in digital transformation (DX).
One of the reasons for this is the state of data infrastructure development.
In order to lead Digital Manufacturing to success, it is essential to introduce an MES (Manufacturing Execution System), which is located at the center of data circulation.
Sakura from Macnica Innovation Strategic Business Headquarters talks about how to deal with MES, which is said to be difficult to implement.
Speaker information
Macnica
Innovation Strategy Business Headquarters Digital Industry Division
Professional Services Department 2 Section 1
Shunsuke Sakura
What are the factors that prevent the DX system from reaching actual operation?
There are still not many opportunities to hear success stories regarding DX in the manufacturing industry.
What are the barriers to success?
“At Macnica, we have supported approximately 300 projects so far, but less than 30% of these have reached the operational phase.When we started providing services in this area about 6 years ago, only 10% of cases reached the operational phase. "There were times when we couldn't even meet our expectations. There were many cases where we weren't able to accompany the crew until the final actual operation, and the situation continued to be very frustrating," Macnica 's Sakura said.
Through these bitter experiences, I realized that Macnica has a stuck point that causes it to stop before it even reaches the point of operation.
“There were several stack points, but the most important one was defining requirements for actual operations.After we saw some results in PoC (proof of concept), we were unable to reach a conclusion on defining requirements for actual operations. Macnica calls this the ``valley of death''. The reason why it is difficult to overcome this valley of death is that in PoC, data is collected by ``people''. This is because data is processed by humans, whereas in the actual operation phase it is collected automatically and processed automatically.In order to handle data automatically, it is flexible and can withstand high loads. It is not easy because it requires data infrastructure, and verification requires collaboration between departments and with existing systems.'' (Sakura)
In addition, it is difficult to raise funds at the field level, and the lack of human resources and organizations that can drive the project are also factors that make it difficult to overcome the valley of death.
Macnica recommends how to cross the “valley of death”
While supporting various companies, Macnica has accumulated knowledge on how to overcome the valley of death.
One answer is to identify the work flow and clarify the scope of responsibility in conjunction with an analysis of the current situation when formulating the initial concept.
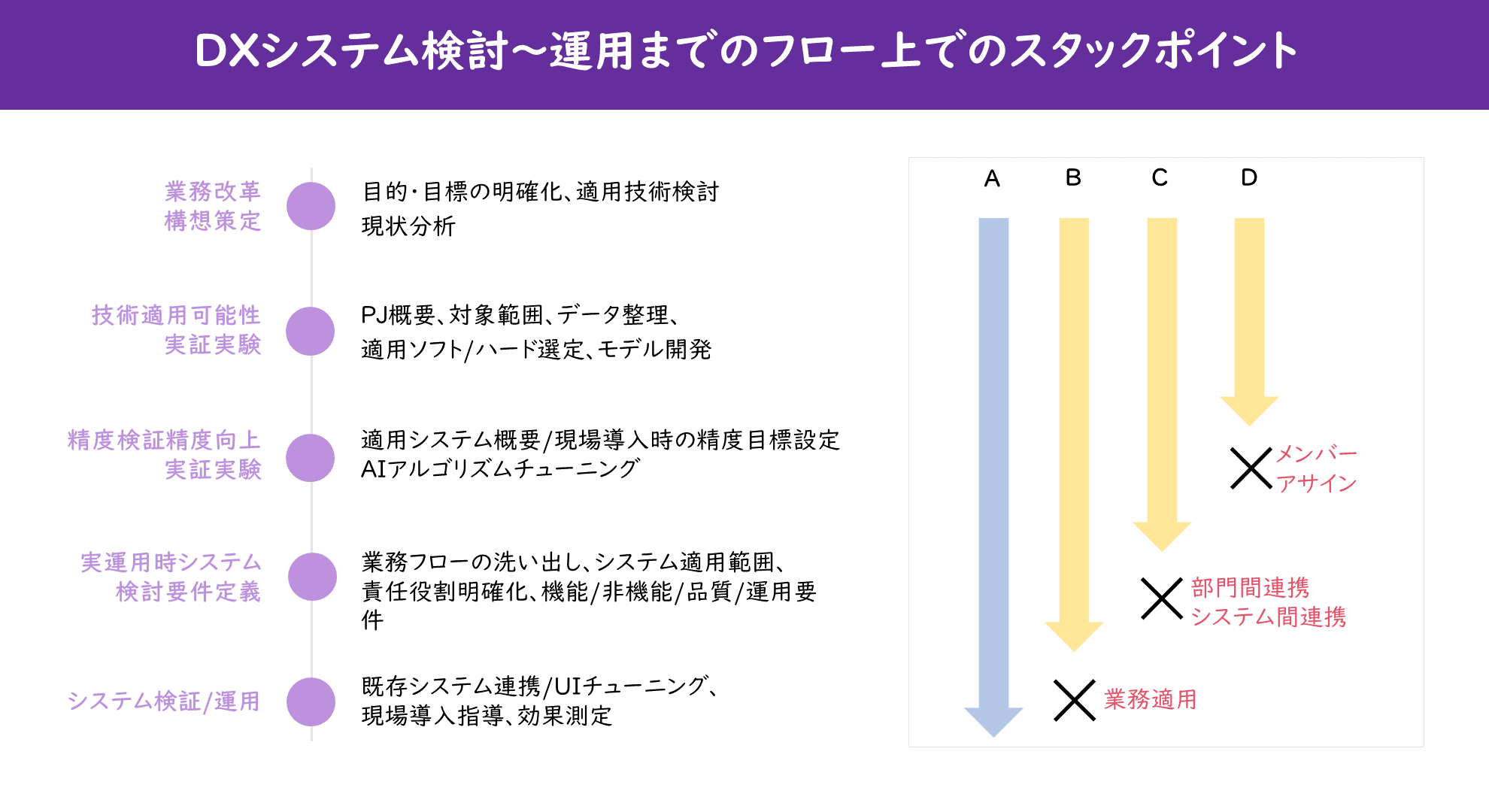
Collaboration between departments and systems is a big stack point, but it can be overcome by replacing the flow
As shown in the figure, it is necessary to be conscious of operation from the concept formulation stage, rather than thinking about operation after implementing PoC.
For tasks and systems that change from the current situation, we have reduced the number of cases of getting stuck when defining requirements by obtaining agreements in advance among the parties involved and preparing an environment in advance so that the systems can work together.
Next, Sakura explains the points of concern in the data infrastructure part as follows.
"When considering the infrastructure for data collection, the MES (production execution layer) is always the intersection of data no matter which angle you enter. When considering the functional hierarchy model, consider the IT side and the OT side separately. Even if you do, there will always be an MES as an intersection point.Also, when you think about the value chain, the MES is located at the intersection point of the manufacturing process value chain and the system value chain.No matter where you enter from, you will always hit the MES. Conversely, if this MES is not properly constructed, it will not be possible to expand the plan horizontally.” (Sakura)
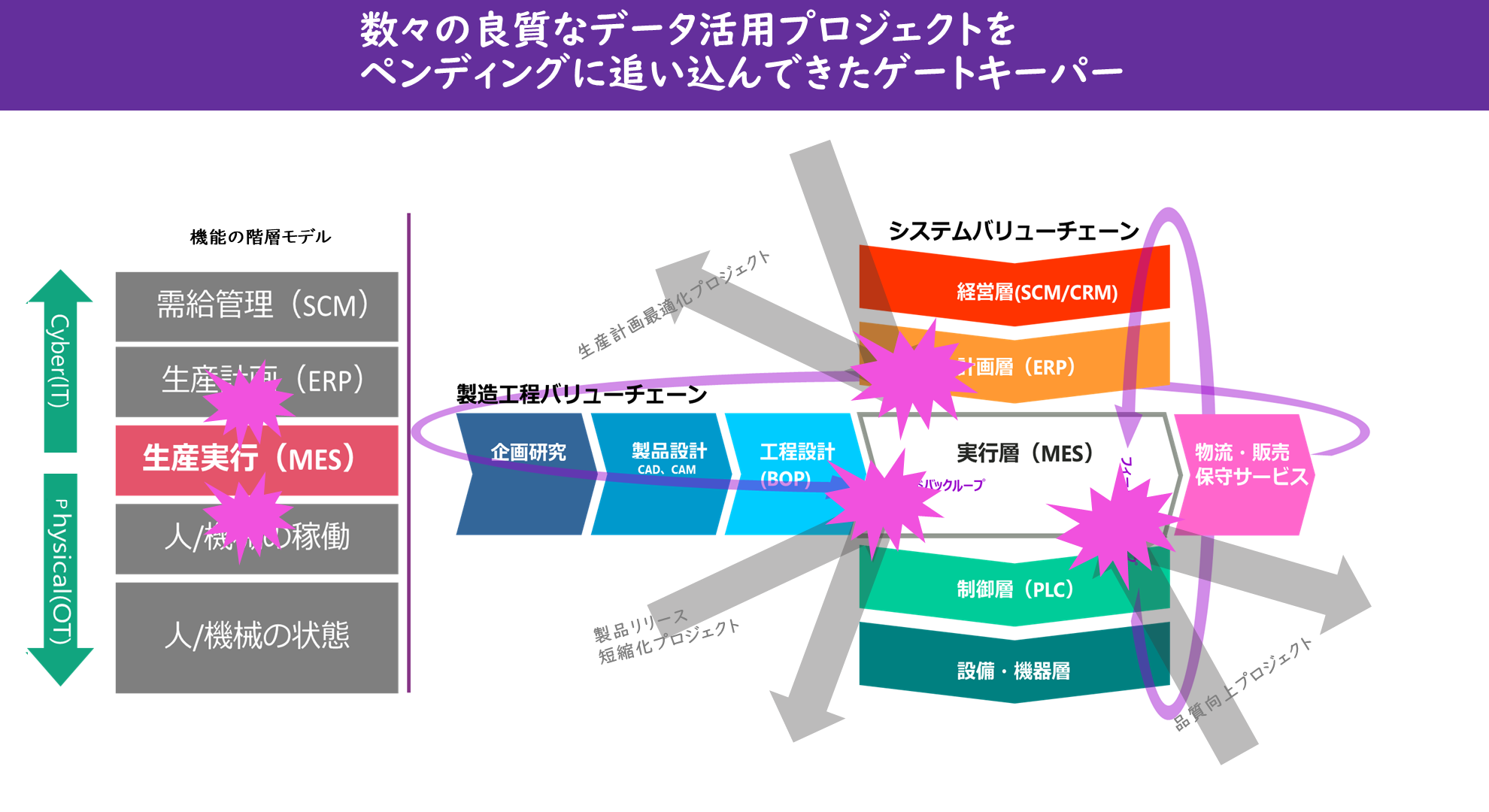
There are many cases where data utilization projects are suspended due to the absence of an MES.
Why is MES essential for data-driven management?
Various issues such as quality control and traceability will arise as we proceed with the use of data at manufacturing sites. However, in order to realize data-driven management, it can be said that MES is an unavoidable path.
“Because it is not possible to respond quickly to today’s uncertain and rapidly changing market trends with only data from a specific layer or a part of the value chain, we introduced MES and built a data infrastructure, and then started data-driven operations. I feel that more and more companies are aiming for more efficient management.” (Sakura)
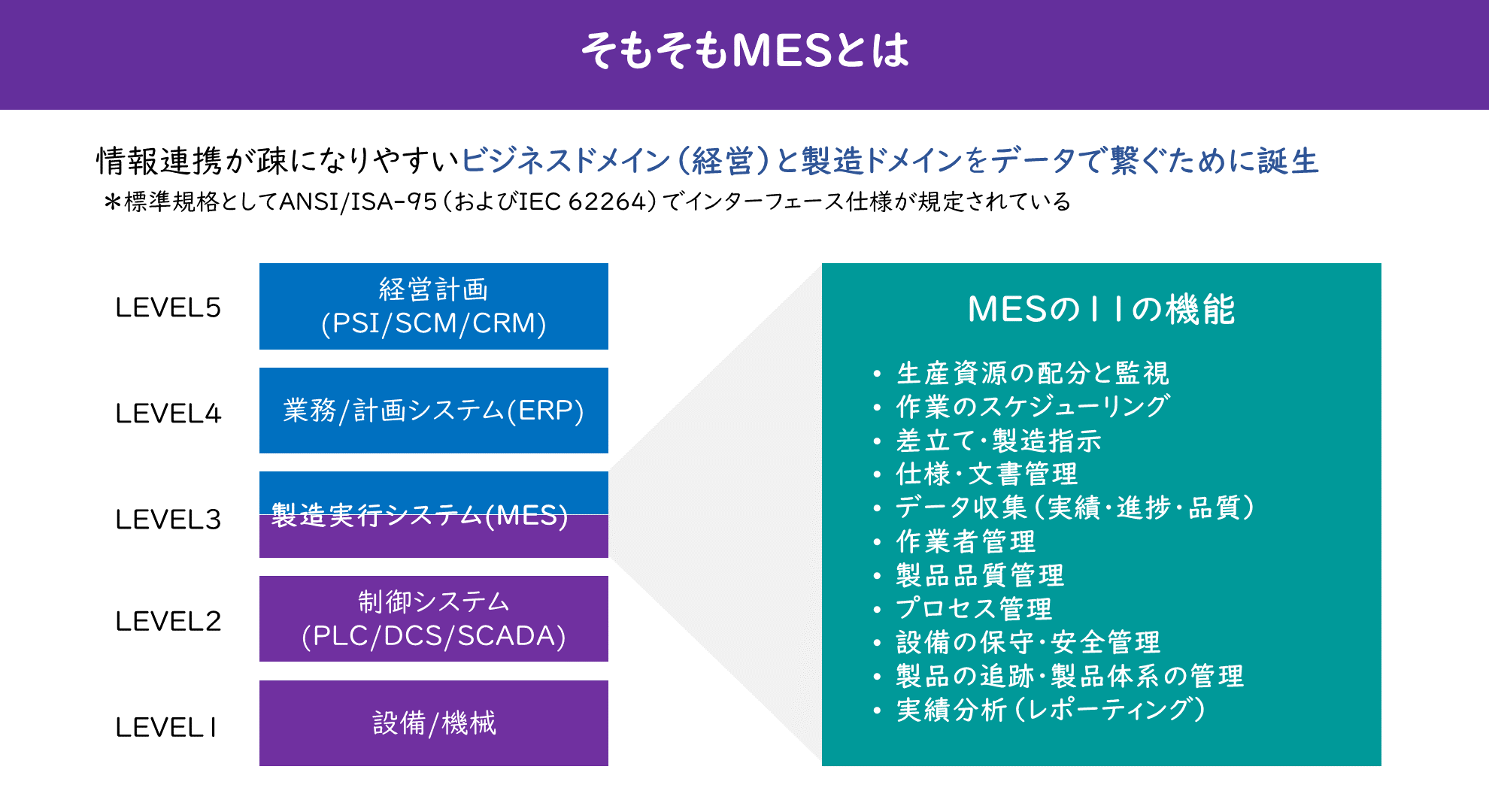
Most of the 11 functions of the MES are carried out in some way
Focusing on parts other than MES, MES cannot be avoided even when considering a data integration platform.
In other words, by digitizing the MES area, which is the intersection of data on the system, data linkage becomes dramatically easier.
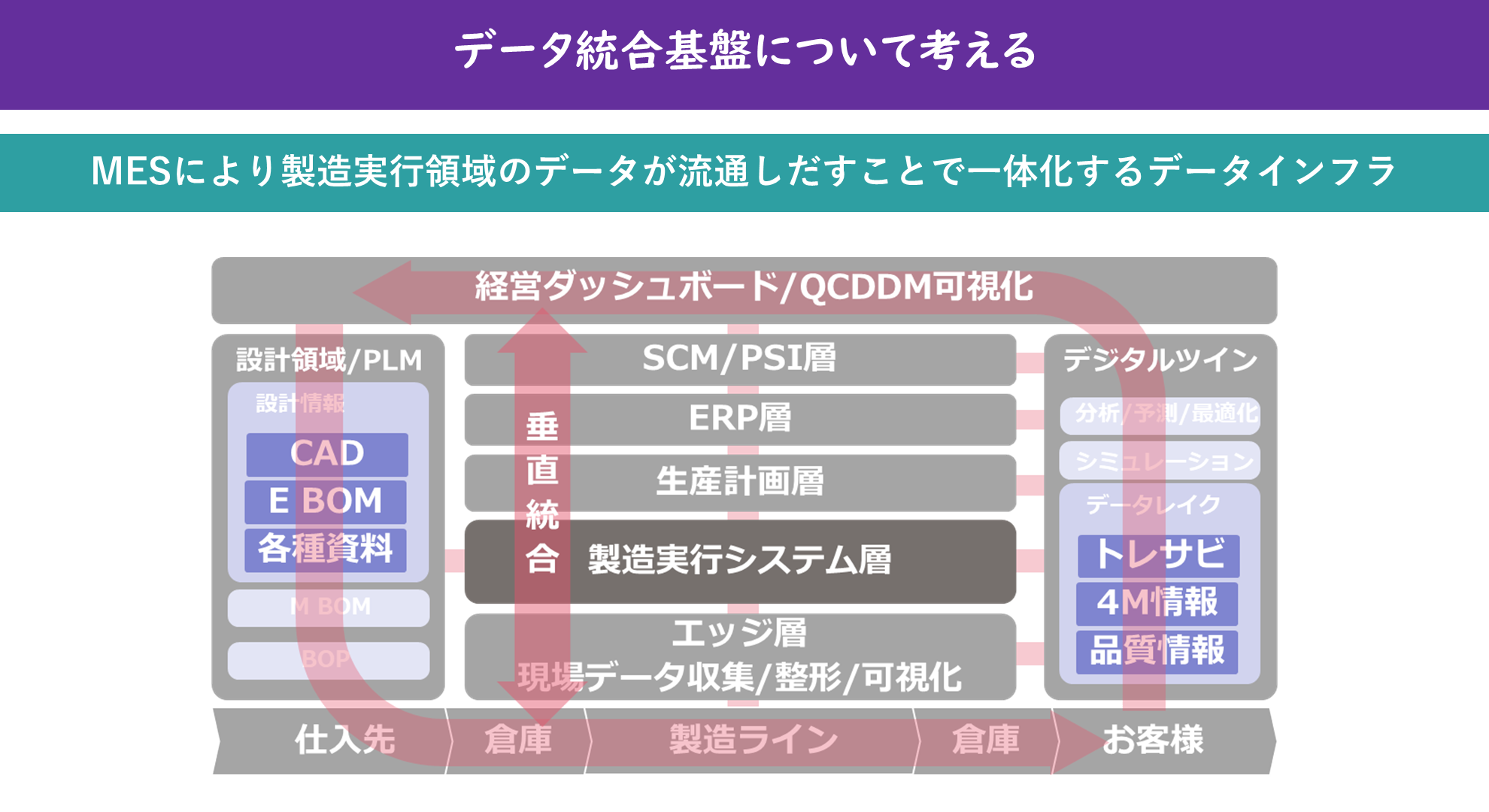
Digitalization of MES makes data linkage more efficient
We also have to think about how to utilize data in the midst of various mechanisms.
“Because the MES is the cornerstone of the system, it is not possible to process the data on the MES. If the MES data is processed, the traceability information may be lost, and it is also desirable from the viewpoint of legal compliance. No. Therefore, when utilizing MES data, it is desirable to prepare a separate data lake, copy the MES data there, and process it, instead of processing the data on the MES. As a point of time, rather than simply copying only the MES data and storing it in a data lake, the final image of data utilization and the purpose of utilization are clearly defined, and various data other than MES are used as necessary. For example, link the 4M information, serial number, lot number, and other data held in MES with sensor data." (Sakura)
On the other hand, since it is easy to collect sensing data these days, it is necessary to pay attention to the fact that a large amount of useless data is generated.
You should go back to your project plan and consider what data to collect.
Approach to reduce the difficulty of introducing MES
So, how should we proceed with considerations when introducing MES, which is indispensable for data-driven management?
“Since the 11 functions of MES are already in some form of operation, when integrating them, we have to thoroughly discuss what is there and what is not, or what should be left and what should be discarded. I can't move forward without it." (Sakura)
Additionally, when implementing an MES, it is necessary to understand the entire system, but since each department is often in charge of each system, it is important to coordinate the entire system. At Macnica, we take a Fit to Standard approach to overcome this problem.
“Until now, many customers have proceeded with Fit and Gap, but this ends up not utilizing most of the packages. On the other hand, with Fit to Standard, the idea is to use the package standard as it is and rewrite the work to the standard.We will operate it with an external application for our company's requirements."
“What the Company want to tell you is that most of the projects you are responsible for are extremely difficult, so we would like you to increase the probability of success by showing us a success pattern for the problems that you are likely to fall into. ”(Sakura)
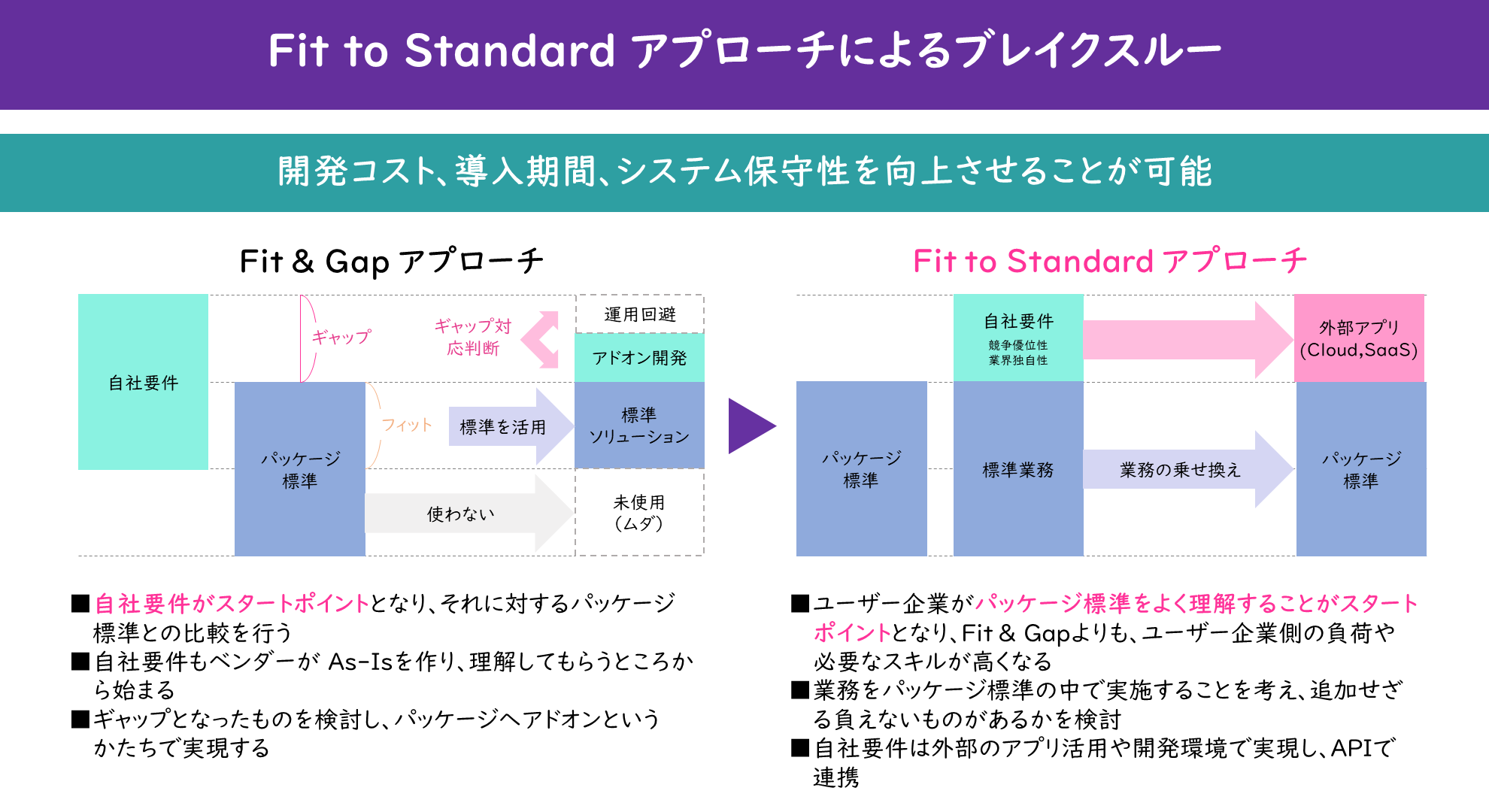
Fit to Standard approach makes MES implementation less difficult
Reference material
*Registration is required to view materials.
This is a guide to a white paper that summarizes three initiatives that will make a breakthrough in the DX project.
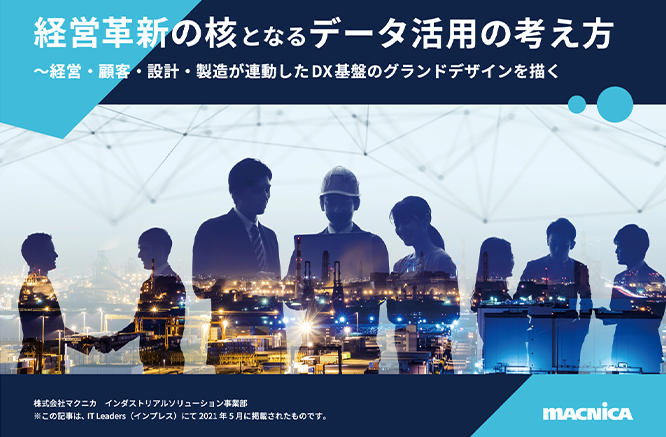
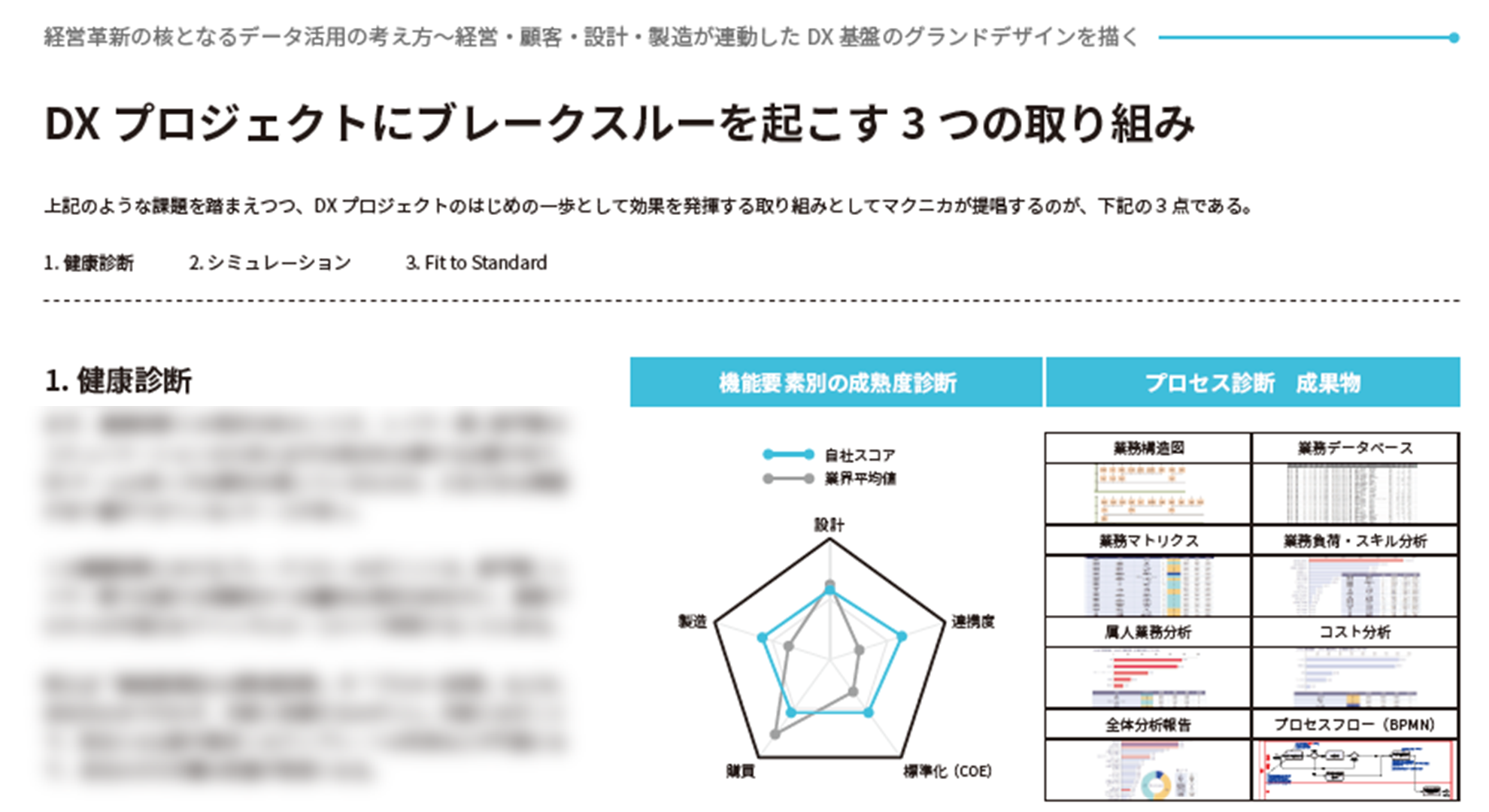