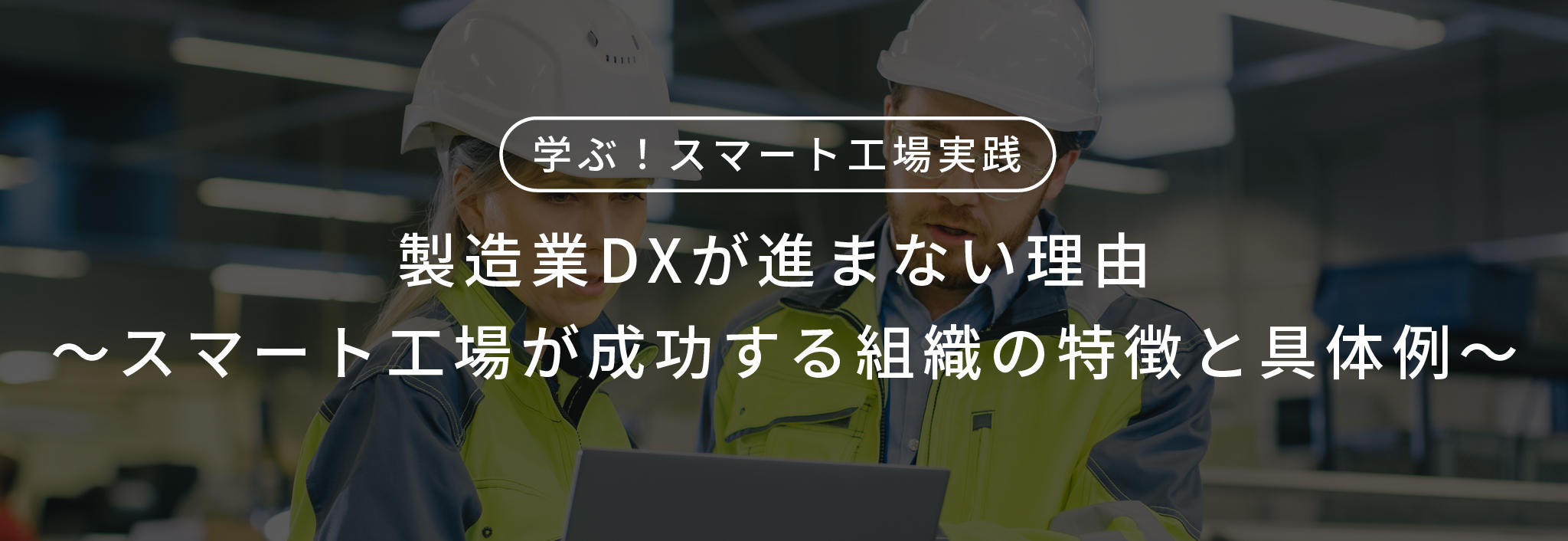
Introduction
In recent years, in response to rapid changes in the social environment, expectations for digital transformation (DX) are increasing year by year.
Among them, I meet many people who are troubled by the difficulty of promoting DX in the manufacturing industry. Many of you reading this article may feel the same way.
In this article, we will consider the actual situation and characteristics of organizations that are steadily promoting even in such circumstances.
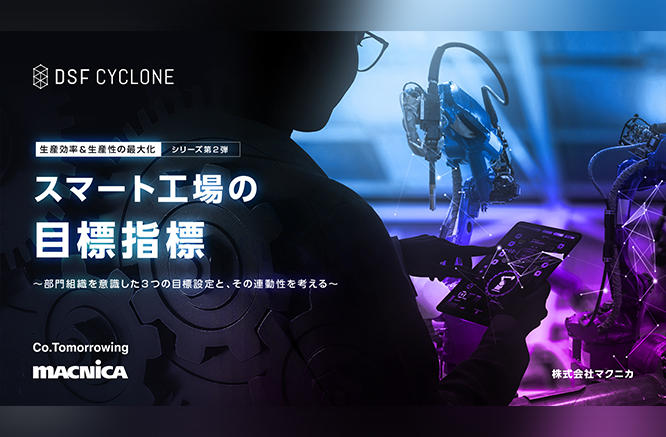
[Recommended white paper information]
For the smooth promotion of DX in the manufacturing industry, it is also important to specify “target indicators”.
This white paper introduces the points that the organization should be aware of in order to work together toward the goal of "continuing to be a profitable factory."
1. Reasons why DX in the manufacturing industry is not progressing
First of all, broadly speaking, DX in the manufacturing industry has various processes such as "development", "procurement", "production", and "sales" as a value chain. This time, I would like to focus on "production", which is unique to the manufacturing industry.
DX in production activities is often referred to as a "smart factory", which connects various facilities in the factory such as production lines and manufacturing machines with a network to optimize production activities and improve the efficiency of information management. It refers to a factory that aims to
Partly due to the influence of Industry 4.0 advocated by the German government, many manufacturing industries are working on DX using data from production sites.
Specifically, within the production department of the manufacturing industry, we will create specialized departments that work on DX in production activities, such as the "Smart Factory Promotion Office" and "Smart Factory Group". There are also cases where efforts are being promoted with the mission of incorporating new technology into production activities such as "Engineering Department".
In the creation of such a specialized department and the utilization of new technology, how should the "smart factory promoters (those who work on DX in production activities)" respond to the voice that "DX in the manufacturing industry is not progressing"? do you feel it?
"Smart factory promoters" are disgusted by general theories such as "labor productivity is low" and "to overcome the current situation, we should promote overall optimization based on objective facts using data." Isn't that the reality?
Gap between "ideal management perspective" and "specific measures to be implemented at the production site" for DX in the manufacturing industry
I believe that the reason why DX in the manufacturing industry has not progressed can be summed up in this word.
While supporting smart factories in various manufacturing industries, we have felt the difficulty of realizing smart factories.
Management talks about the future of smart factories, such as "data-driven management". There are many opinions such as, "What are the specific measures?" and "What are the benefits that can be obtained as a result?" It is very difficult for smart factory promoters to achieve both at the same time.
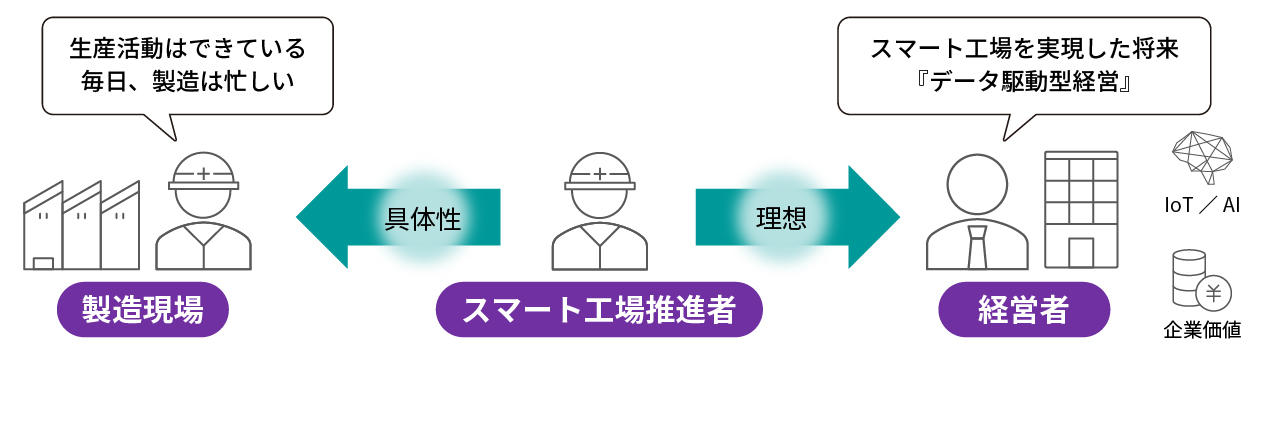
"Ideal management perspective" and "production site". A smart factory promoter who satisfies both sides
Our company accompanies many smart factory promoters who are working on such a very difficult project, and supports the realization of DX in production activities.
From here, we will consider the characteristics of the organization that is promoting the ideal smart factory, which we have learned through our activities so far.
2. How to promote smart factory initiatives?
[Organization and People] Personality of smart factory promotion leader
The smart factory promoters we have met who are steadily advancing their projects have something in common.
That is, having a high degree of sensitivity to changes in the external environment and having the driving force to involve the workplace.
In order to promote smart factories, it is necessary to aim for the realization of highly abstract ideals such as "data-driven management" and to proceed with hypothesis testing of methods that have not yet been established. Furthermore, when testing hypotheses, it is necessary to take step-by-step steps while involving production sites that are busy with daily production activities.
For this reason, those who are actually promoting smart factories tend to be highly sensitive to trends in the world, have curiosity about new technologies and their utilization, and are highly motivated to do something on their own initiative. Even if the method for success has not been established, you have the ability to think for yourself and proceed with a sense of conviction while gathering the necessary information and sometimes building new human relationships that are necessary.
In addition, in the course of our efforts, we are affected by the external environment, which changes significantly. In particular, in recent years, there have been various changes such as the spread of the new coronavirus infection, changes in work styles such as telework, rising resource prices, and the appreciation of the yen. I think there was a lot of things to realize. And in today's globalized international society, where geopolitical risks are high, the ability to respond to many changes in the external environment will continue to be required.
Under such circumstances, for better or for worse, I feel that many people have a sense of urgency about the production activities that continue to carry out their old-fashioned approaches, and that sense of urgency is motivating them to promote smart factories.
That is why, while feeling the gap between the ideal and the reality, those who are promoting the essential efforts of smart factories should proactively reach out to related departments, including upper management and production sites. I think that we are able to get involved in initiatives and promote activities.
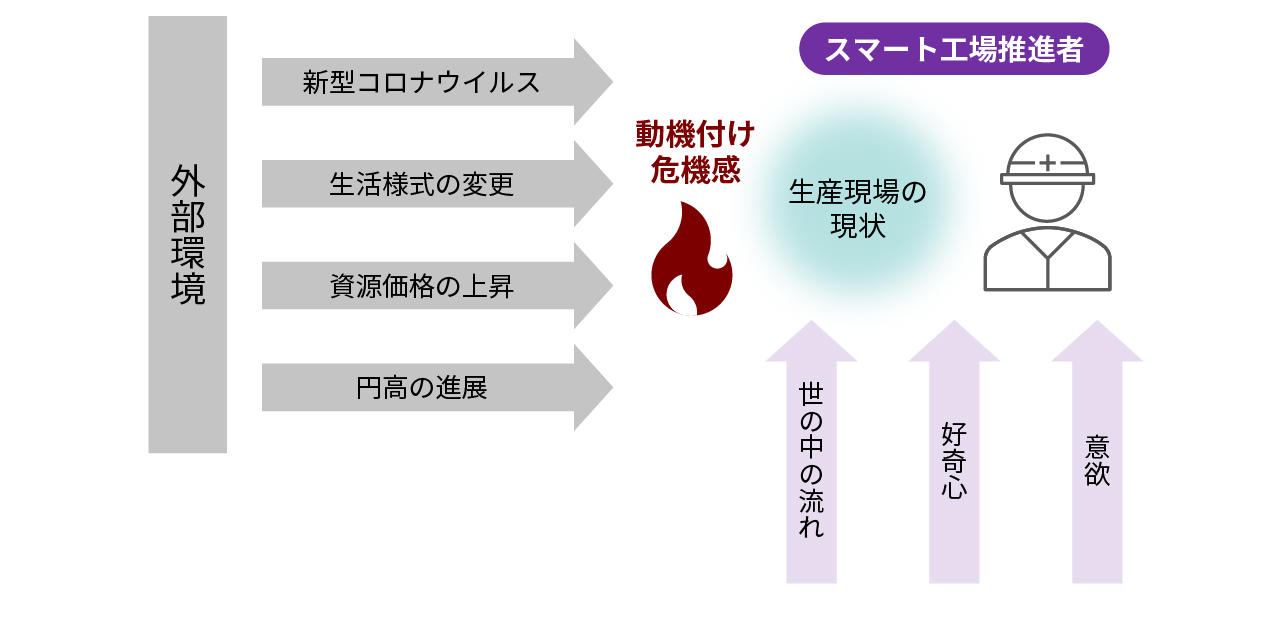
A sense of crisis about changes in the external environment motivates promotion
[Experience] Past failures are the catalyst for success! ?
Even so, it is not easy to arrive at the essential efforts while the direct attack method in DX has not been established. In particular, when it comes to smart factory initiatives, the words themselves are often buzzwords, and we tend to jump to catchy messages and easy-to-understand words.
And surprisingly, many of those who are promoting essential initiatives have actually experienced such catchy messages at least once.
For example, what was originally worked on at the production site, such as "Andon", has recently been used in smart factories to collect and visualize data from production equipment using the expression "visualization of the production site". practiced in the factory.
Specifically, equipment operation signals and production counter values of production equipment are acquired from PLCs and signal lights, and real-time graphs and Gantt charts are used as "visualization of production progress" and "visualization of equipment operation status". It means to display.
However, the effect of such real-time visualization is low at the production site, because the more people who have been involved in production activities for a long time, the more they understand it with their own senses. And from the production site leader's point of view, "Even if you know that the equipment is stopped, you don't know why it is stopped." "Even though it's a production progress rate, it's not an accurate value because the number of defective products is included in the production volume." Ultimately, there may be some of you who have had the experience of seeing such visualization screens no longer being viewed by anyone.
In fact, there are many people who are currently working on essential smart factories after such failures.
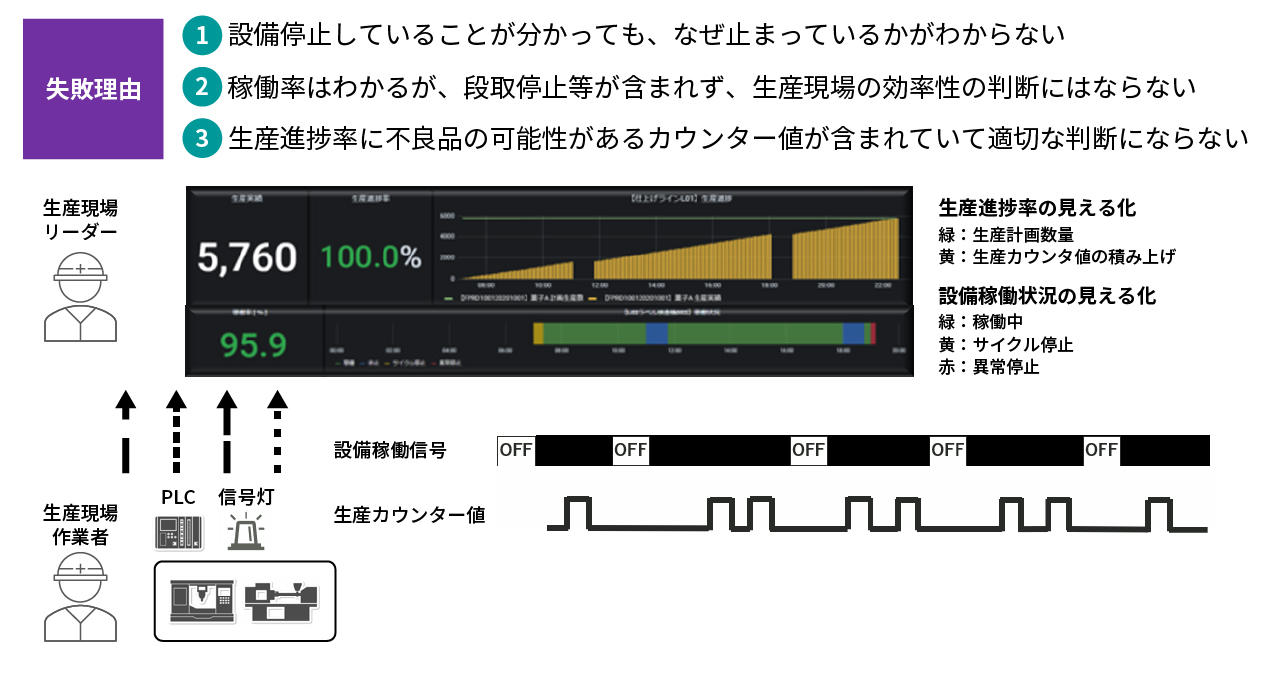
Real-time visualization based only on facility data is less effective
I think that those who are promoting essential initiatives in smart factories are thinking about past failures, such as "why things didn't go well" and "how to lead to essential activities." increase. And I think that the driving force behind this is our ability to respond to the rapid changes in the external environment that we feel every day, and we expect smart factories to respond to this.
3. Introduction of specific examples Key points of initiatives involving production sites
From here on, I would like to introduce some points for smart factory promoters to carry out specific activities involving production sites.
Point 1: Recognize it as “improvement of work at the manufacturing site”
The point of what we want to achieve through smart factories is to acquire dynamic capabilities in production activities, in other words, to think of it as "improving operations at the manufacturing site."
In Japan, work improvement at manufacturing sites has traditionally been systematized, like Kaizen in the Toyota Production System, and has been consciously addressed as ``genba power''. One of the important goals of what we want to achieve with smart factories is to use digital technology to further promote conventional kaizen initiatives even more strongly in today's world, where social change has become even more intense. The digital technology here means not only data collection and data analysis, but also the ability to judge good or bad based on data.
In addition, when thinking about making decisions based on data in "improvement of operations at manufacturing sites," I believe that the most important point is the organization and people who make decisions based on data.
Regarding this "organization" and "people", I would like to introduce some people who divide them into soft and hard aspects.
Intangible aspects refer to the common culture in an organization / person, the motivation / intention that forms the basis for better production activities, and the common way of thinking when making things better. I think that this soft aspect has long been regarded as important in production activities.
The hardware aspect is exactly the system that utilizes digital technology that is being considered for smart factories, the data accumulated by the system, and the index /KPI that is the axis for judging good or bad based on that data. This hardware aspect is newly needed to have a factual awareness in production activities in order to make decisions and change faster in the midst of drastic changes in the external environment.
This software and hardware are the two wheels, and based on the data, we objectively grasp the current situation and analyze the factors, and plan and implement countermeasures with a strong desire to improve common production activities, and the results of those activities. It is required to objectively evaluate how it was based on data again.
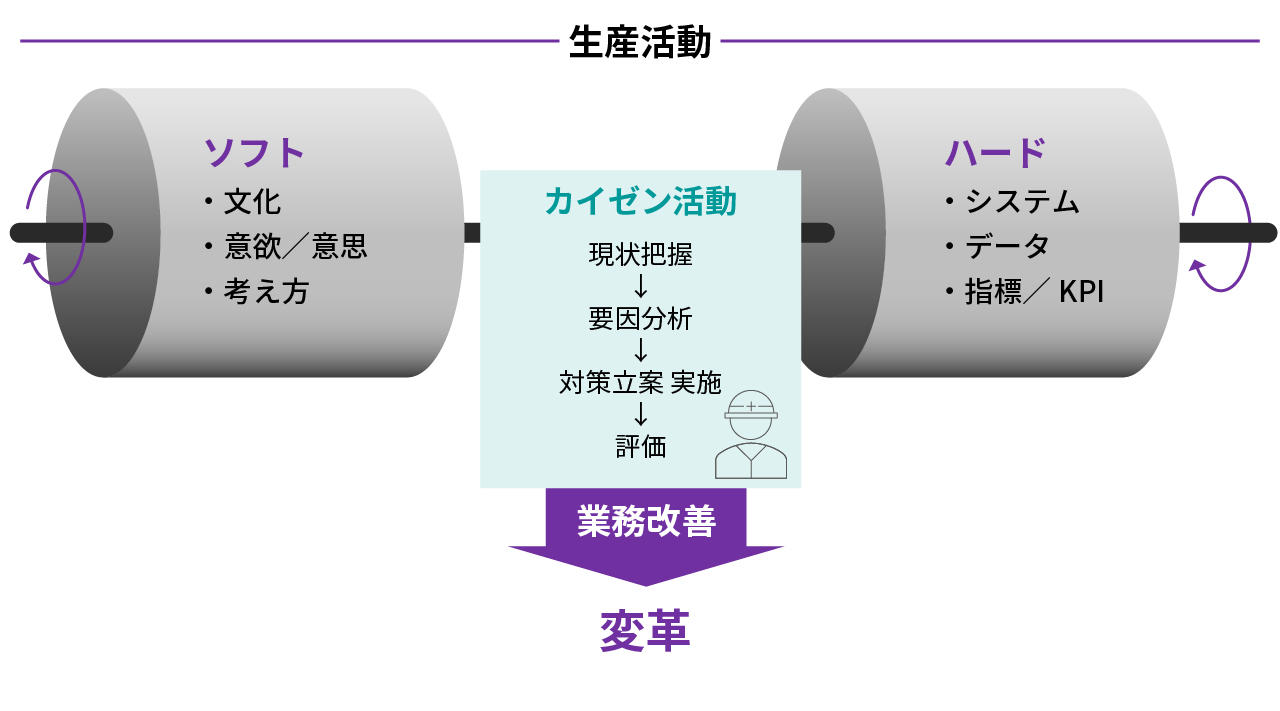
Both software and hardware are necessary to improve operations at production sites
Words such as IoT, DX, and AI tend to catch our eye, but efforts to promote essential smart factories are nothing more than the realization of steady steps to improve operations.
Information on the white paper that digs deeper into the points so far
Regarding the "soft" and "hard" aspects that are important in production activities,
For more information, please download this document.
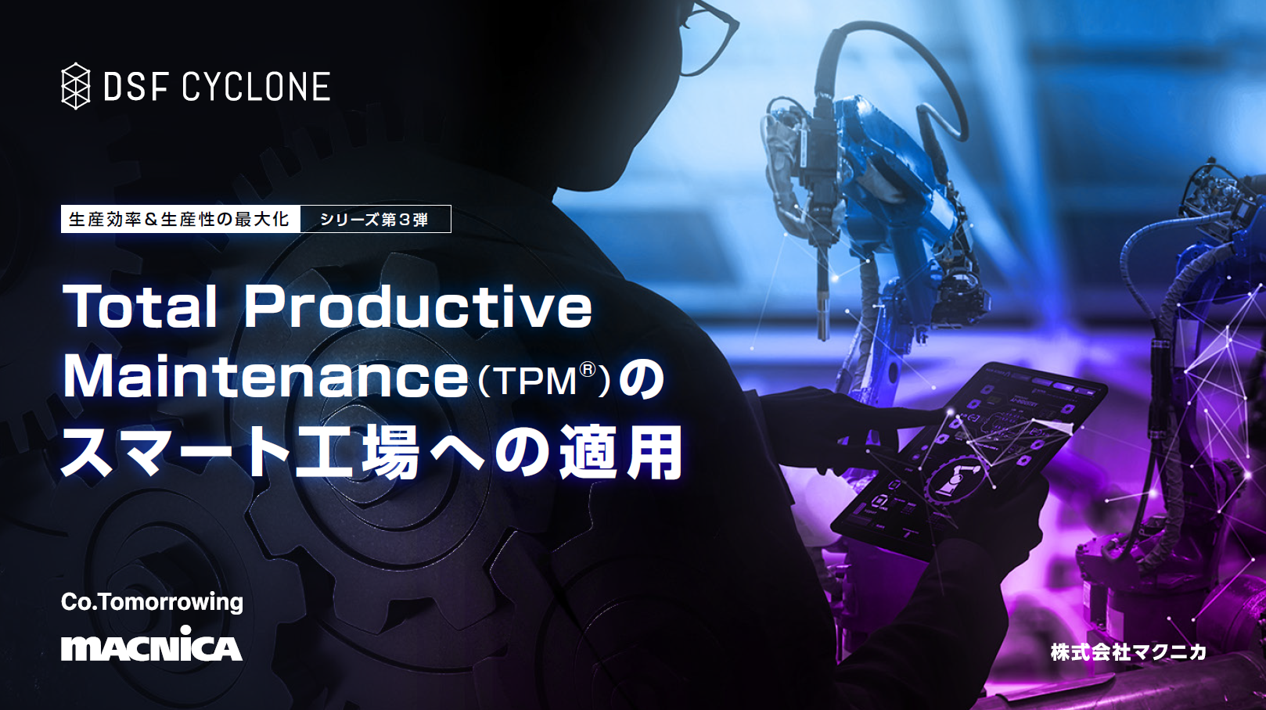
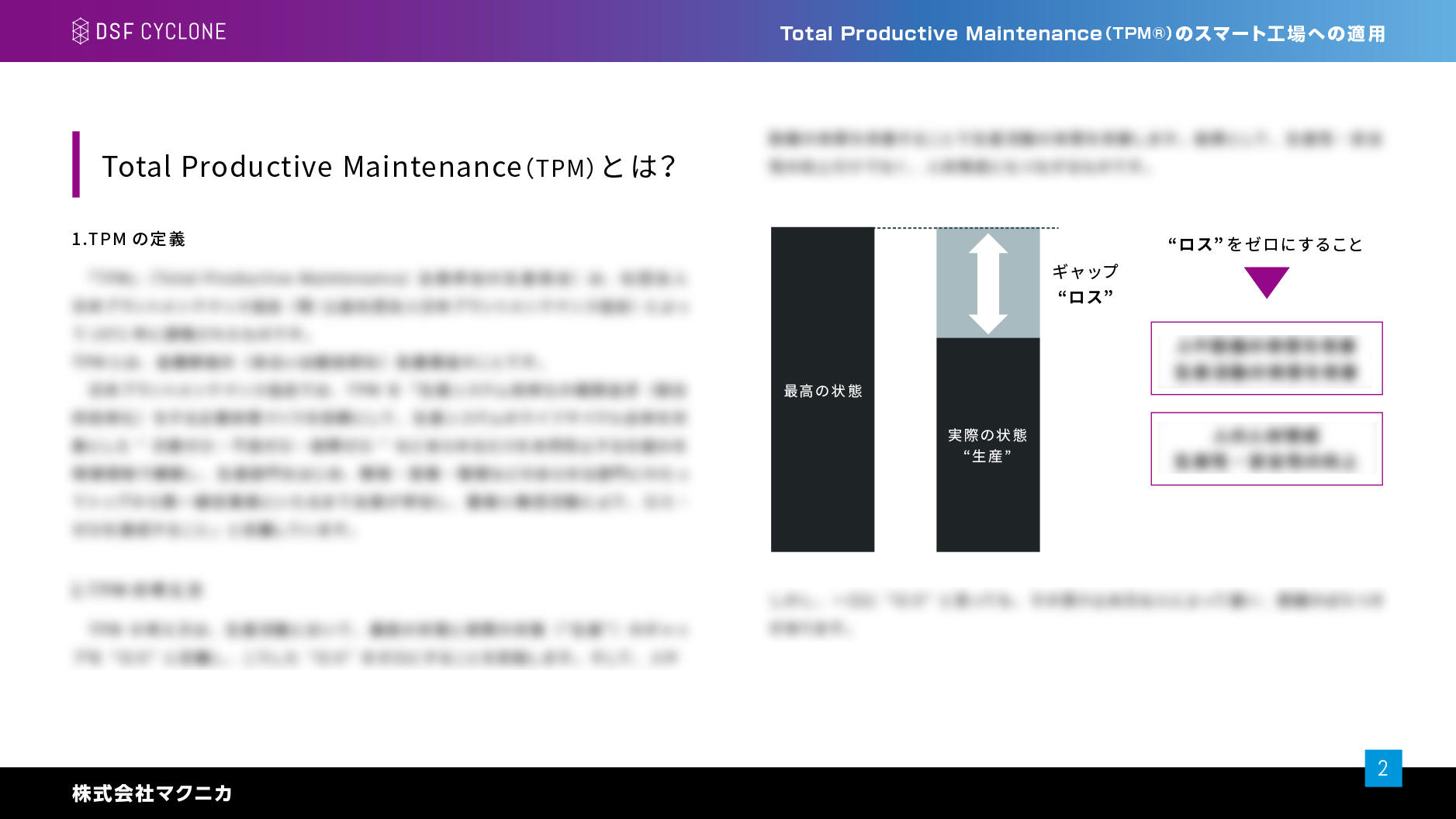
Point 2: Make full use of indicators/KPIs after introducing the DX system
Finally, I would like to summarize how to understand the effect of introducing the DX system, which is the hardware aspect.
As one of the elements of smart factory promotion, I have told you a case where objective indicators /KPIs are used. After the introduction, it goes without saying that numerical values such as production efficiency, which is the indicator /KPI for judging success, have improved. increase.
At the production site, it is necessary to produce good products by the deadline while responding to various changes such as equipment failure and the physical condition of workers against the target production volume on a daily basis. Therefore, it is difficult to keep production at a high and constant level, and even if you look only at the previous week, you can clearly see the good days and bad days from Monday to Friday.
The point here is not to categorize good days and bad days, but to discuss the differences between good days and bad days. For example, if production efficiency, which is an index /KPI in general production activities, was the best on Monday at 75 % and the worst on Tuesday at 65 %, what kind of loss would be the difference of 10 %? So, what cause (change point) caused the loss? It is important to discuss and consider countermeasures.
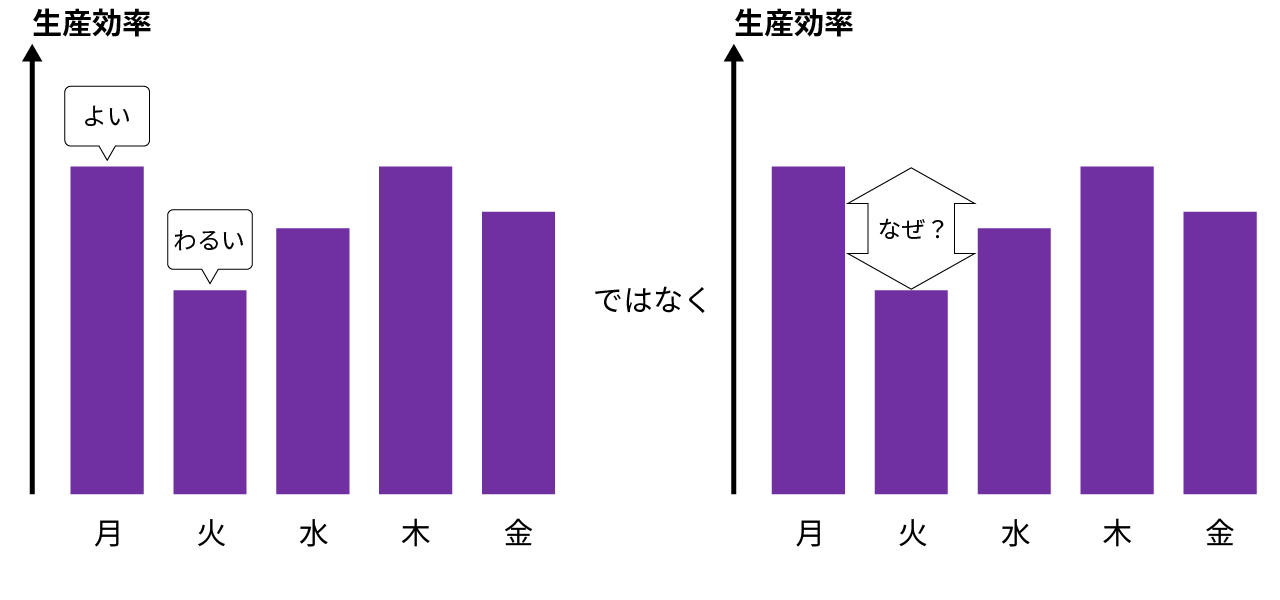
It is important to discuss the causes and countermeasures for loss, which is the difference between a good day and a bad day.
Next, the second effect of introducing the DX system is that the person responsible for business improvement, such as the production site leader, can have discussions based on objective data with related parties such as production site workers and maintenance staff. increase.
For example, let's say that we have a Kaizen meeting every Friday afternoon to discuss the results of that week's production results based on indicators /KPIs. In that case, from Monday to Friday morning of the week, the actual metric /KPI values can be found by referring to the DX system at the meeting.
Therefore, the person in charge of business improvement should clarify in advance which loss to discuss on which day. At the beginning of the meeting, participants are informed of the items to be improved, the relevant lines, the date and time, and the loss, and the degree of impact that the loss has on the production efficiency of the week (production efficiency inhibition rate, loss time, number of losses). Tell you. It is very important to share facts based on this objective data. You will be able to concentrate and discuss only what kind of measures should be taken in the future.
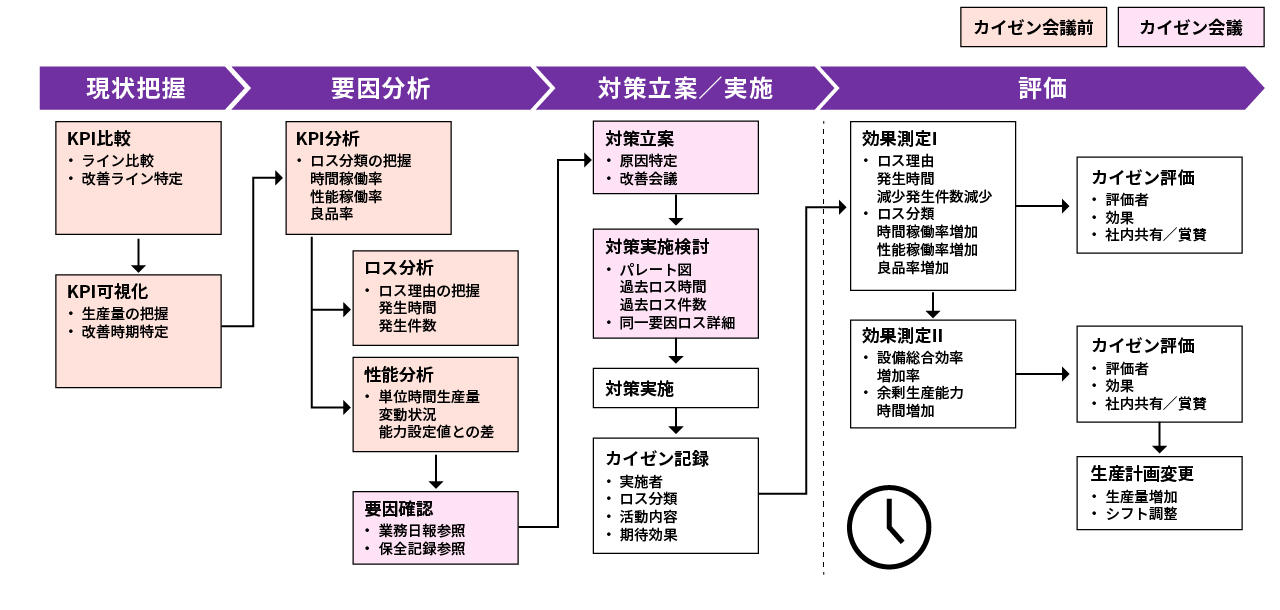
Kaizen meetings focus on identifying causes and planning countermeasures based on analysis results
In the manufacturing industry, workers at manufacturing sites who create products are the source of sales, and securing manufacturing time itself leads to value. On the other hand, there is also the fact that discussions on efficiency such as Kaizen meetings are important for workers, but they spend a lot of time.
In other words, the DX system introduced in the smart factory becomes a business reform support tool for effective and efficient discussions with related parties.
4. at the end
In the digital age, digital human resources generally sought after may be employees who can handle programming languages such as Python and C ++. On the other hand, the digital human resources that we have seen while supporting the promotion of smart factories at our company are employees who lead the realization of digital transformation toward a better state while actively utilizing new technologies and technologies. I feel like it's also about.
This article hopes to be of help to those promoting smart factories in the face of the sluggish DX in the manufacturing industry. I was introduced.
Many people may have felt the story of leadership and project promotion in the promotion of smart factories.
As we continue to promote smart factories while worrying about the lack of progress in DX in the manufacturing industry, we hope this will be an opportunity for you to stop and think again.
\Recommended videos for those who are worried about promoting smart factories/
Supporting quick start & quick win of smart factory
"DSF Cyclone" is a service that enables the construction and utilization of hardware aspects (systems, data, indicators /KPIs) that are important in production activities.
If you are interested, please also refer to here