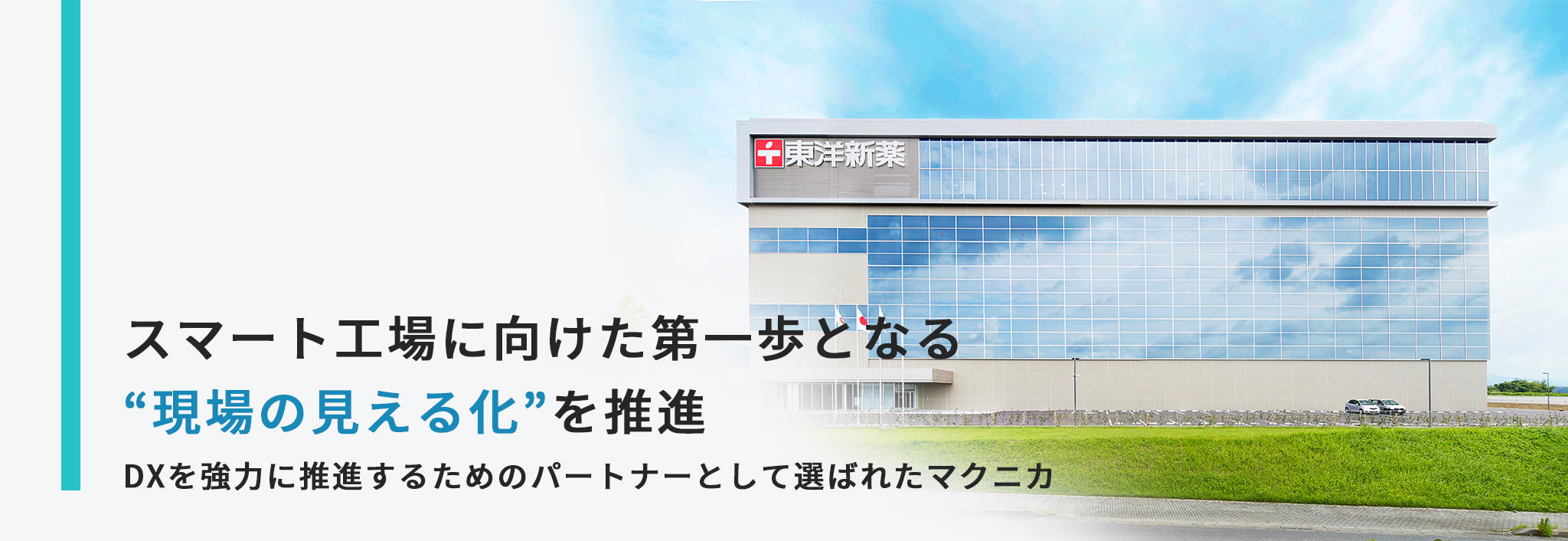
Toyo Shinyaku Co., Ltd. case study
Supporting health and beauty with a new business model called ODEM
Toyo Shinyaku Co., Ltd. was founded in 1993 as a cosmetics wholesaler, and was established in 1997 as an independent health food division within Seven Seas Co., Ltd.
As a comprehensive contract manufacturer that can manufacture both "health food" and "cosmetics" on a one-stop basis, we have established advanced manufacturing and quality control systems. We support "health" and "beauty".
We provide total support from product planning to formulation design, manufacturing, and sales promotion support. Research and development capabilities, intellectual property, and production cultivated through ODM (Original Design Manufacturing), which designs and manufactures products under the consignor's brand. Utilizing our capabilities, we also focus on OEM (Original Equipment Manufacturing), which manufactures products under the consignor's brand.
Armed with the company's unique business model of ODM and OEM, ODEM, we are promoting businesses that contribute to the health and beauty of people around the world by creating high-value-added products based on evidence. there is
USER PROFILE
■Company information: Toyo Shinyaku Co., Ltd.
■ Business content:
Toyo Shinyaku Co., Ltd. is at the forefront as an ODM/OEM manufacturer of health foods and cosmetics.
Based on our corporate philosophy of "HIGH-END VALUE", we are meeting the expectations of people around the world for their "health" and "beauty" by leveraging our strengths in "research and development capabilities," "quality control system," and "factory equipment that meets international standards." We aim to be the company that is most supported by customers and consumers by responding to "value".
summary
background
-
Supporting health and beauty with a new business model called “ODEM (ODM & OEM)”
-
設備稼働率の最大化と業務シンプル化
-
Promote company-wide DX and aim to link all information
Task
-
Visualization of the progress of the production line
-
Understanding real-time operating status
-
Consistent data from sales to manufacturing
selection
-
Familiar with both IT and OT
-
Together we can draw a vision of the future with a view to reality
-
Management-conscious KPI management
Attempt
-
Real-time data processing and visualization of acquired equipment information on specific lines
-
Visualized information includes inspection and filling results / alarms / yield numbers / target achievement rates, etc.
-
Pre-training on how to use
from now on
-
Aiming for one-stop access to all information from sales to logistics by linking with core systems
-
Incorporating new ideas, such as calculating standard man-hours through preventive maintenance and flow line analysis, toward a smart factory
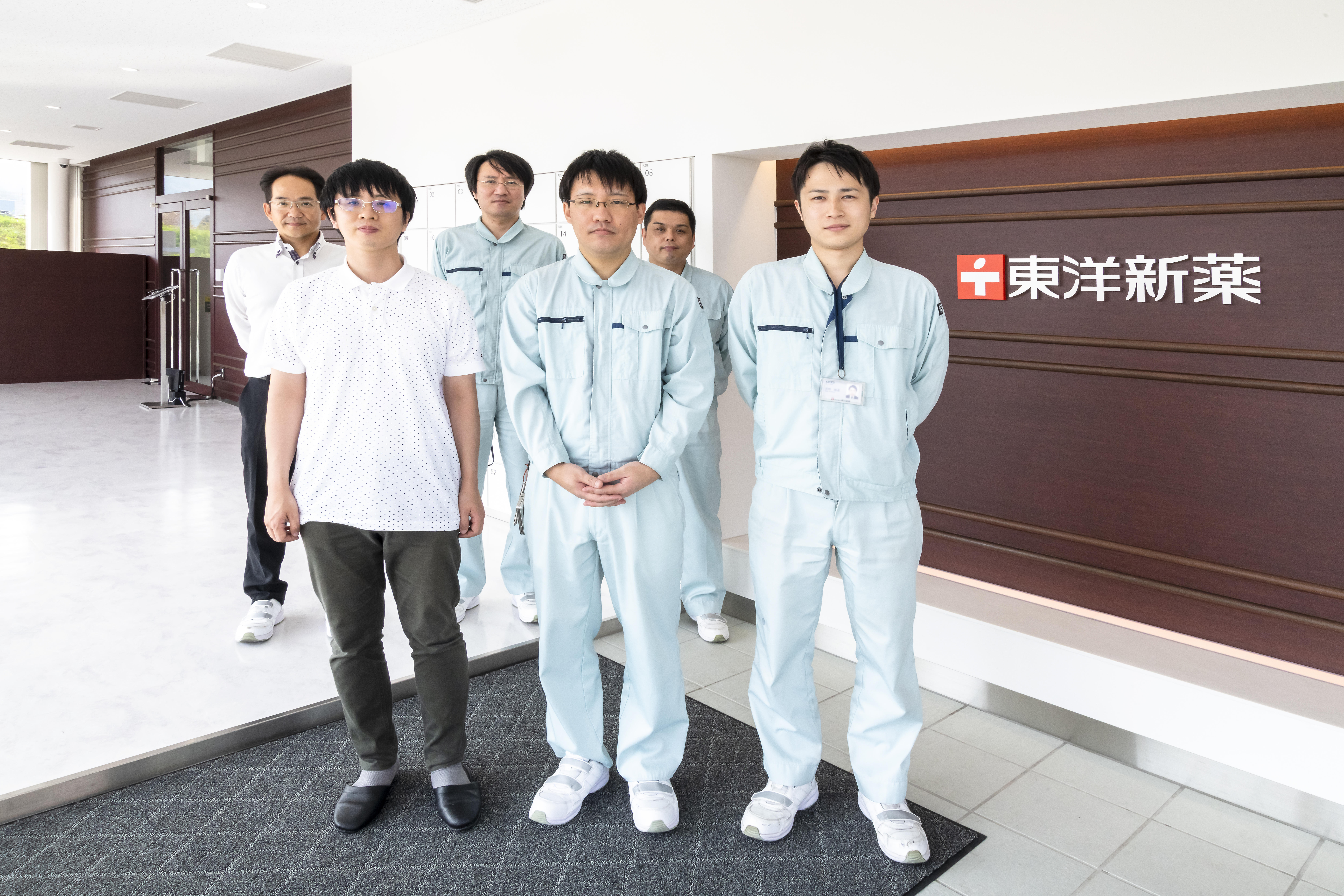
<From the back left>
Mr. Yoshifumi Koseki, General Manager, Design Engineering Department, Manufacturing Headquarters
Mr. Takashi Toyoda, Deputy Manager, Equipment Technology Section, Design Technology Department, Manufacturing Headquarters
Mr. Hisao Moriyama, Deputy Factory Manager, IP Factory
<From front left>
Mr. Daisuke Ito, System Development Department
Mr. Noriaki Sakata, Equipment Engineering Section, Design Engineering Department, Manufacturing Headquarters
Mr. Jumichi Nagano, Equipment Engineering Section, Design Engineering Department, Manufacturing Headquarters
background
The Manufacturing Headquarters, which supports the company's factories that produce high-quality products, is actively reviewing the work flow and developing human resources.
ー Mr. Moriyama
In 2019, we established a new Intelligence Park (IP) factory as a next-generation manufacturing base, and it is designed as a flexible building that allows us to introduce equipment according to customer requests. Using state-of-the-art equipment, we manufacture high-value-added health foods, including foods with function claims.
At this IP factory, we have set three goals: thorough implementation of 5S, realization of a non-stop factory to maximize equipment utilization, and practice of front-loading to simplify operations through thorough pre-setup. It is said that there is
In addition, the company, which continues to grow steadily, has built a single-function system in the sales department, quality assurance, and research and development fields. We are in the process of renovating the entire infrastructure, including
ー Mr. Fujimura
As the company continues to grow, we are at a turning point, and we aim to make it function as a new strategic tool through system renewal.
Currently, information obtained from the field is analyzed manually, mainly using Excel. I'm drawing a future.
Task
Aiming for real-time on-site visualization through information utilization, which has been a chronic issue
While promoting such DX company-wide, we decided to consider initiatives for a smart factory as a measure to "maximize the facility utilization rate", which is one of the themes of the newly completed IP factory. It is said that
- Mr. Koseki
At the new factory, the problem of not being able to fully visualize the progress of the production line had become apparent.
This has been a chronic issue for some time, but by promoting information sharing not only on the shop floor but also in the management department, we will be able to create optimal manufacturing plans, and make it possible for manufacturing data to provide information to each department. I wanted to do it.
and look back on those days.
In fact, in order to improve the operating rate of the newly introduced equipment, Mr. Koseki, who was in the manufacturing department at the time, and others continued to make improvements while sticking to the site, and the operating rate was raised to a considerable level. Although
ー Mr. Toyoda
While it was clear that the business would expand and the number of lines would increase, this method would soon lead to bankruptcy. That kind of thinking was a big driving force.
explains.
A similar problem was also apparent at the manufacturing site.
ー Mr. Sasaki
It is true that we managed data using Excel, etc., but we had to go to see it, and we had to collect and analyze it ourselves. If the operating status can be properly grasped in real time, it will also lead to loss reduction. We wanted an environment where we could constantly grasp the situation on the ground using numbers.
In addition, the data itself was not visible in the manufacturing control department, which gives work instructions for the entire factory, and it was an environment where it was difficult to grasp the situation as the distance from the site increased.
ー Mr. Fujimura
Originally, depending on the production output, it would be necessary to cooperate with the inspection department and the distribution department to the post-process, but it was not enough. For us, whose business is centered on ODEM, which is made-to-order manufacturing, the company itself will not function unless data flows all the way from sales to manufacturing. We want a shared environment.
As a starting point, we aimed to visualize the worksite by utilizing IT and connect it to the post-process.
:
For those who want to read more
Download the PDF document here