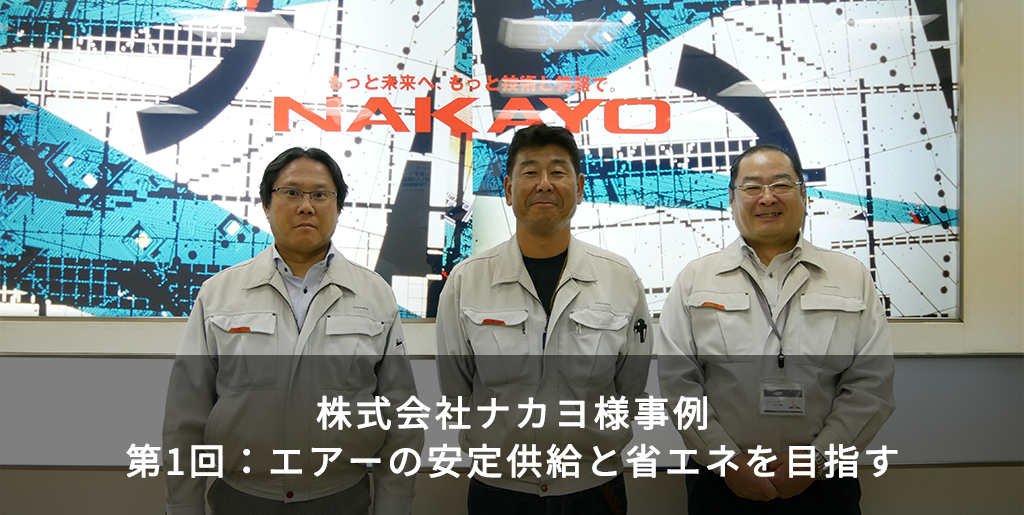
From the left, Mr. Mishima, General Manager of Nakayo Production Technology Department, Mr. Kobayashi, Manager of Equipment Design Section, Production Technology Section, and Mr. Motegi, Manager of Manufacturing Support Center
Since its founding in 1944, Nakayo Co., Ltd. has contributed greatly to the development of the information and communication equipment field as a manufacturer of information and communication equipment.
Currently, we are producing a variety of products that meet customer needs in the field of information and communications, centering on our mainstay business phone system.
We are also ambitious in introducing cutting-edge technology, and we are promoting manufacturing and providing services that incorporate new technologies such as IoT and AI.
This time, Mr. Motegi, Manager of the Manufacturing Support Center, Mr. Mishima, Manager of the Production Technology Department, Mr. Kobayashi, Assistant Manager of Equipment Design in the Production Technology Department, and Asami, our engineer, will talk about the efforts to ensure the stable operation of air compressors that are essential in factories. I heard about
We will divide it into several times until the problem is solved.
Active company-wide smart factory initiatives
―Please tell us what prompted you to work on the stable operation of the air compressor this time.
Mr. Mishima: I work in the Production Engineering Department, and my mission is to optimize the manufacturing process.
We are promoting visualization of the manufacturing process in-house, but we have not implemented visualization of the operational status of infrastructure other than power consumption.
However, there was a problem with the stable supply of the air required for the process, and this time we decided to visualize the operating status of the air compressor.
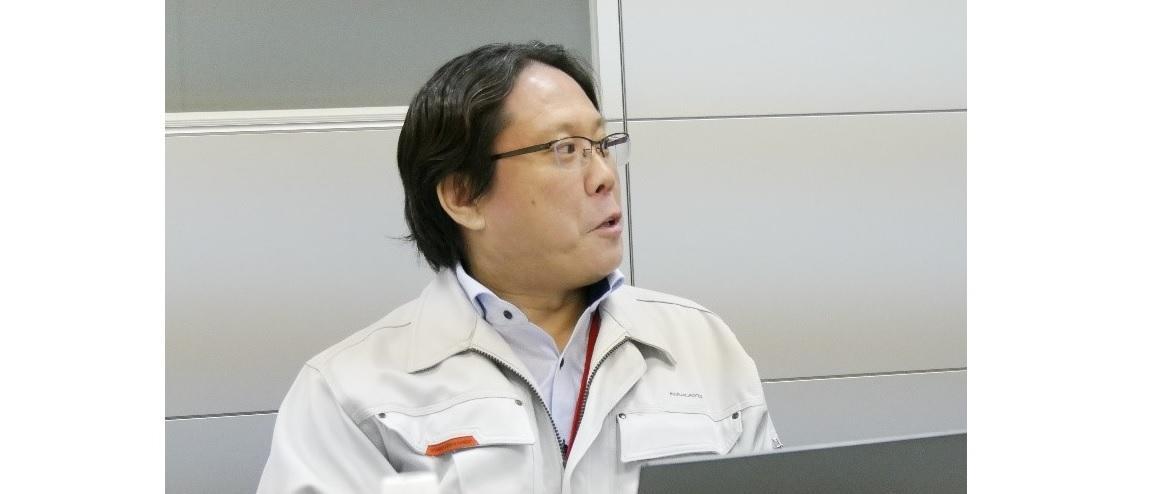
Mr. Mishima
―First of all, I understand that you are working to visualize the manufacturing process in-house.
Mr. Mishima: Nakayo is a company that is ambitious about improving the efficiency of its manufacturing sites.
As one of these projects, about five years ago, we started working on a smart factory, including visualization of the manufacturing process of machinery.
This is a project that involves the production engineering department, to which I belong, as well as the field and the development department.
Currently, sensors are attached to various devices in each process so that the quality status is displayed on the screen so that anyone can understand it, and problems can be noticed immediately.
We independently install the sensors, and the visualization software is developed from scratch by our in-house development department according to the requests of the on-site staff in each process.
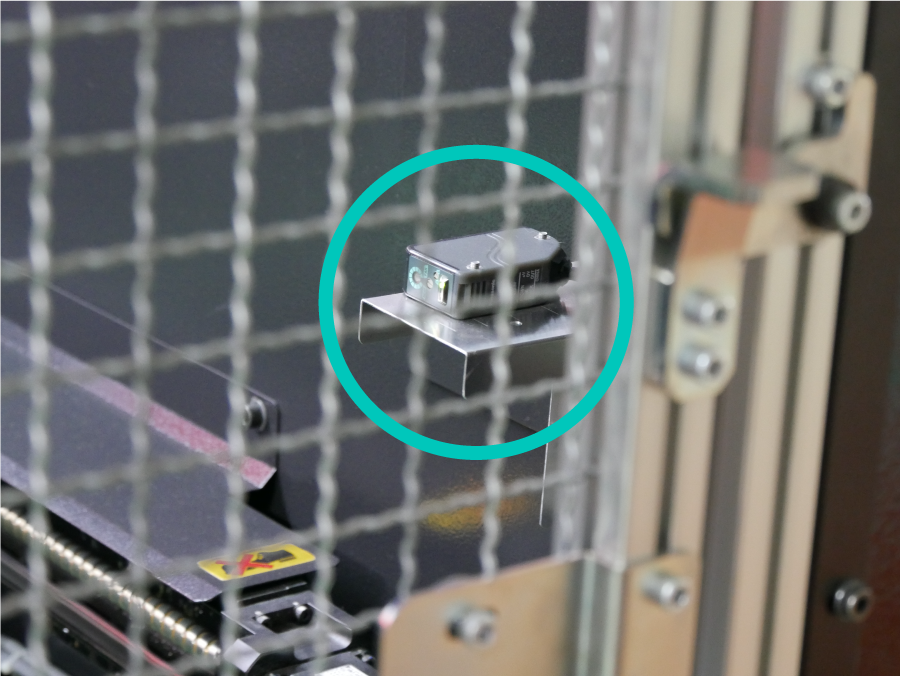
▲External sensor attached to the machine
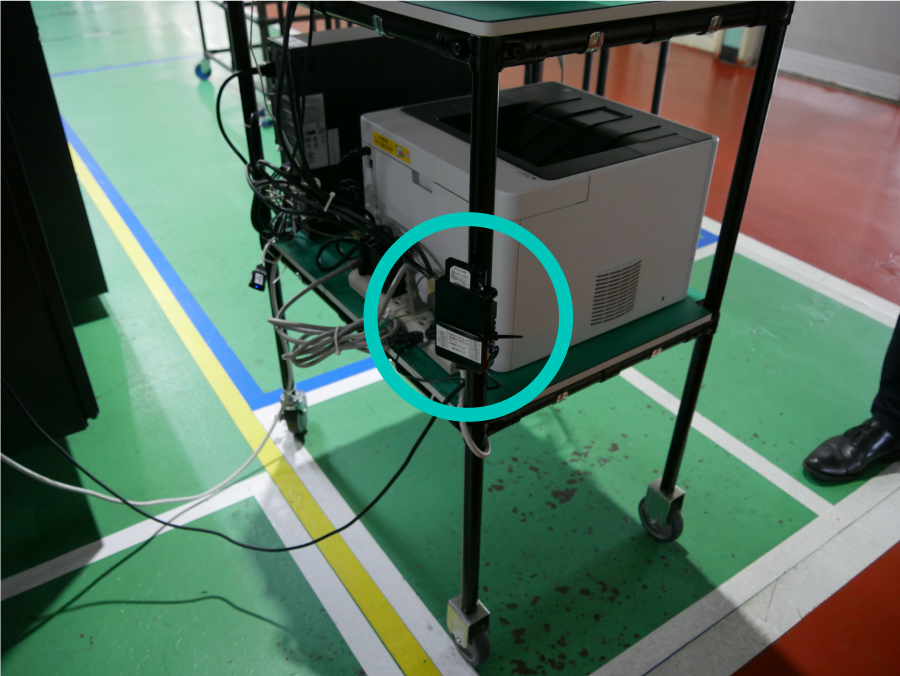
▲ Operation information collection device made by Nakayo
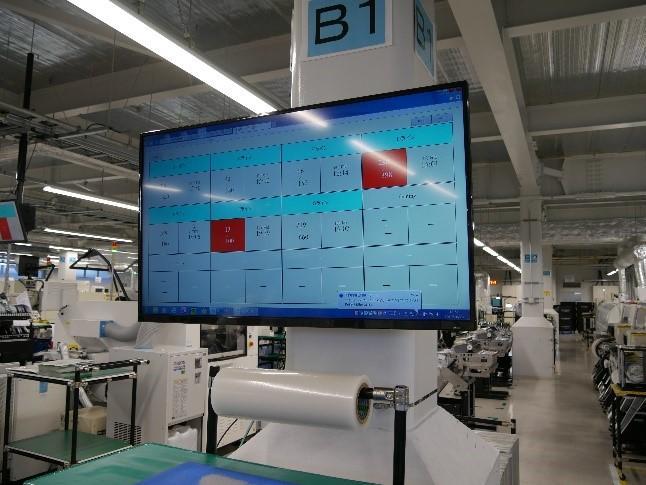
Photo of the visualization screen installed in each process
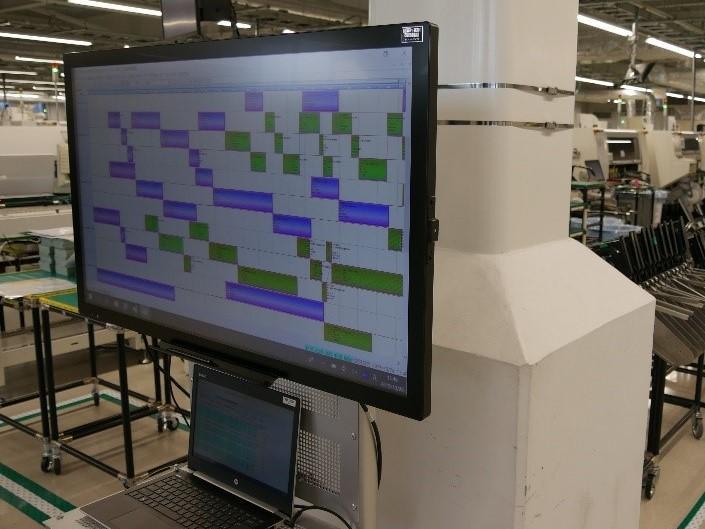
―It's amazing that you do everything from installing sensors to developing visualization software in-house!
We have four factory buildings, and almost all processes are being digitized, making it possible to monitor the operating status. Robots were also introduced.
Mr. Mishima: We are proceeding with the aim of optimizing every process.
Robots were introduced to automate assembly work and transportation.
When we first introduced it, we had a lot of trouble getting it up and running.
―You have been able to realize a smart factory by steadily advancing the digitization and visualization of machines for about five years.
I thought it was a wonderful factory that was proactively taking advanced initiatives.
Stable Air Supply and Energy Conservation Issues
―By the way, about the compressor, why did you decide to work on monitoring the operating status of the compressor in the factory infrastructure?
Mr. Mishima: In the past, there was an incident where the discharge pressure of the compressor dropped and the air supply to some machines and air guns suddenly stopped.
I thought it was because I used a lot of air at the same time, so I increased the compressor pressure and set it to give it some leeway.
Although this prevented an unexpected stoppage of the production equipment, the increased pressure resulted in increased power consumption.
The Energy Conservation Law established by the government stipulates that factories are obliged to make efforts to reduce their energy intensity by an average of 1% or more per year over the medium to long term. *1
It is said that compressors generally consume about 20% of the power consumed in factories, so reducing the energy consumption of compressor equipment is an important issue in promoting energy conservation in factories.
However, the pressure of the compressor was increased in order to give priority to stable air operation, and the situation became difficult.
―Please tell us about the configuration of your compressor and the circumstances under which the problem occurred.
Mr. Kobayashi: I am in charge of maintaining and managing the infrastructure of the factory. For this issue, I am actually working on solving the problem with Macnica 's help.
First, regarding the composition of the compressors, Nakayo has three compressors, which are centrally controlled in two compressor rooms outside the factory building.
Air is supplied to each process and equipment through piping from these two compressor rooms.
We have 1.5 machines in operation at all times, and in preparation for unforeseen circumstances, we have set up a system in which 1.5 machines on standby are automatically activated.
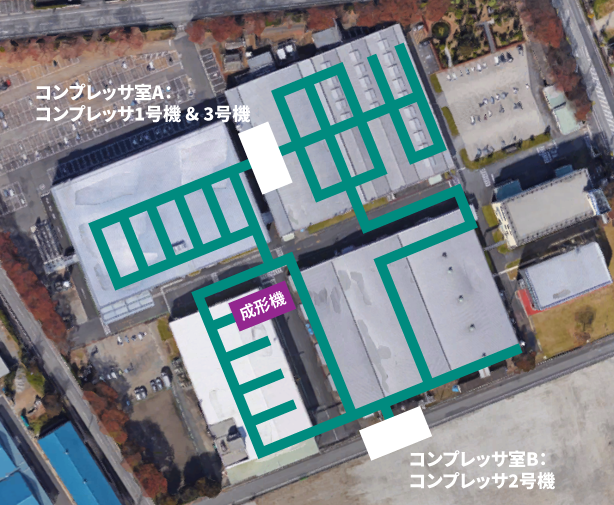
Even if the air pressure of the compressor is insufficient, it is configured so that it will not be affected, but a problem such as this time occurred.
When the air supply actually stopped, the person in charge of the site reported that the air supply had stopped.
After all, you can only check if there is no leakage on the spot.
I thought that if I knew when the air was used intensively, I would be able to spot the problem. There is no prediction about the air gun used by. This is because the timing of use differs depending on the person, the day, and the product.
Whether the problem is in the piping, on the edge of each process, or in the main compressor, there are various ways to approach the problem. I was at a loss as to whether it was okay or not.
We then learned that Macnica, with whom we have had a long-standing relationship, was working on a smart factory initiative, and decided to consult with them.
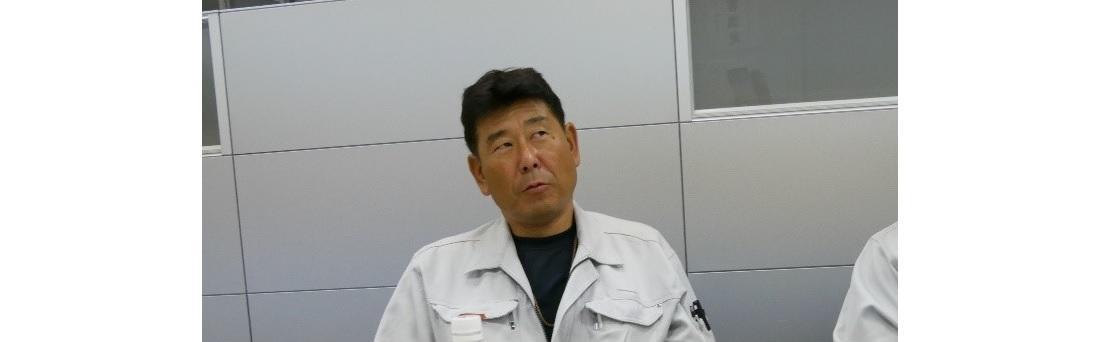
Mr. Kobayashi
―Since the cause of the air supply stop was unknown, the pressure had to be increased to ensure a stable supply.
In Part 2, we will aim to visualize the operating status of compressors, and will tell you about our efforts to understand the air supply status of a specific factory building.
*1 Source: From the website of the Energy Agency, Ministry of Economy, Trade and Industry
https://www.enecho.meti.go.jp/category/saving_and_new/saving/enterprise/overview/