The PCs and home appliances that we use casually in our offices and homes are connected to networks via Ethernet and exchange a huge amount of information. As the amount of data increases, it is possible to speed up communication, improve the efficiency of communication paths, and resend data in the unlikely event of a collision.
On the other hand, factory automation sites require different conditions from general networks, such as a huge number of devices connected to the network and reliable and real-time transmission of information. We will explain the points that you may be wondering about, such as what kind of standard is the industrial open network "EtherCAT®" that meets such conditions, and how it differs from Ethernet.
What is EtherCAT®?
EtherCAT® is one of the industrial open field network standards compatible with Ethernet, proposed by the German company Beckhoff Automation. The main features are that high-precision synchronization control can be achieved (synchronization of 1 us between devices), and duplexing is possible (prevents the entire network from going down due to communication path or slave failure).
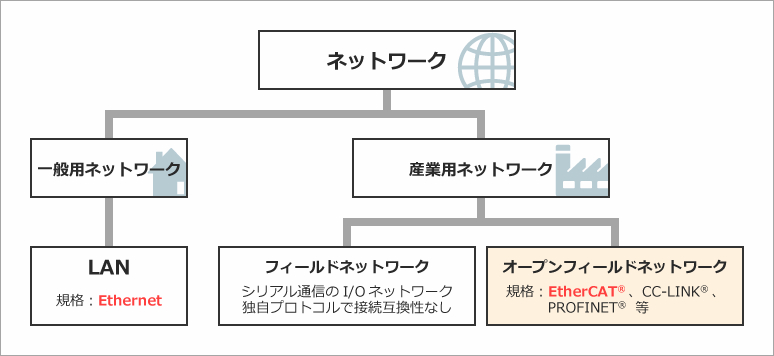
Applications where EtherCAT® is used
What kind of applications are EtherCAT® actually used in?
In FA (factory automation), various devices such as sensors, cameras, motors, input/output (I/O) devices, and controllers that bundle them all are connected to factory lines. EtherCAT® connects these devices and performs communication that satisfies industrial requirements.
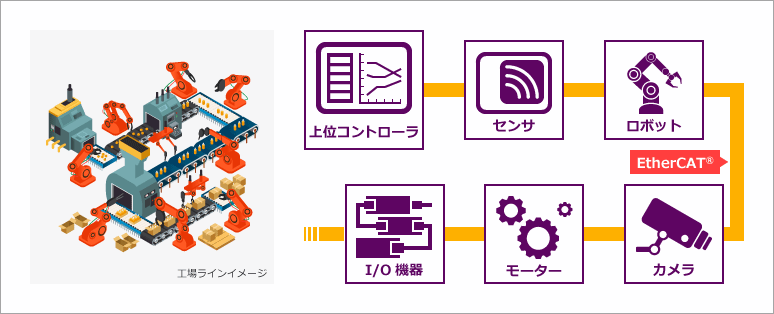
Difference between EtherCAT® and Ethernet
How is it different from the widely used Ethernet? Let's compare some points that should be considered when actually designing in the table.
Comparison item |
Ethernet |
EtherCAT® |
Physical layer hardware configuration | Same (MCU-EthernetPHY-Pulse Trans-RJ45) | |
Industrial ready for physical layer devices (Ethernet PHY) | unnecessary | Environmental resistance required High ESD protection, High operating temperature range (-40°C to 85°C) |
ネットワーク層より上位層 | TCP/IP protocol UDP/IP protocol | Industrial Ethernet protocol |
Maximum number of connections | Without limit | There is an upper limit (65535 units) |
Since EtherCAT® is required to be used in FA, the physical layer PHY device is required to withstand the environment, but the hardware configuration is the same as Ethernet.
Ethernet frames are used for software processing in communication, but TCP/IP protocol processing is not performed, and high-speed processing is performed using an original protocol. The Industrial Ethernet protocol does not require handshake to confirm transmission/reception between devices, which enables high-speed responsiveness.
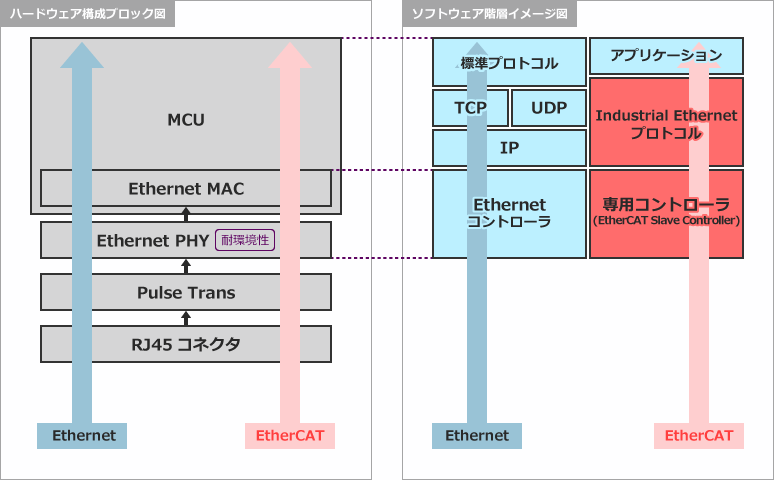
EtherCAT® system configuration and actual operation
Let's take a look at the system configuration and communication behavior when using EtherCAT®.
The system consists of Master and Slave, and the following connections are possible.
- daisy chain
- star type
- ring type
The diagram below shows a daisy chain connection. Here's how it actually works.
- Frames sent from Master pass through each Slave
An Ethernet frame is sent from the Master, passes through all Slaves in order, and returns to the Master again. - When 1, each node writes transmit data to the frame.
The data part of the Ethernet frame used in EtherCAT® has an output/input data bit for each Slave. Each Slave also knows the bit position and width given to itself, so it writes the transmission data there. - Read received data at each node from the frame after 2
After writing the transmitted data, each Slave reads the received data.
This communication method achieves high speed and real-time performance.
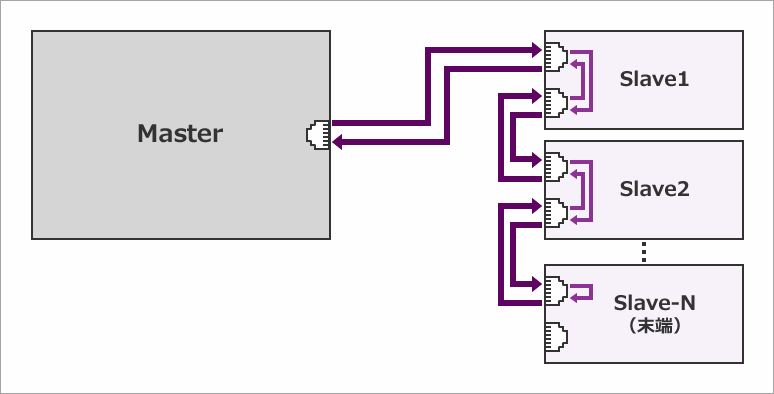
Texas Instruments Ethernet PHY DP83822 with excellent environmental resistance
As mentioned above, PHYs used in FA are required to be robust, such as environmental resistance (wide temperature range) and electrical resistance (ESD protection). We will introduce the features of the Ethernet PHY DP83822, a Texas Instruments (hereafter TI) product that satisfies these requirements.
Features of Ethernet PHY DP83822
- Electrostatic discharge (HBM): ±16 kV or more
- Electrostatic discharge protection performance: ±8 kV or more (IEC61000-4-2 compliant)
- Temperature range: -40 to 125°C, -40 to 85°C
- Link loss reaction time: less than 10 µs (for CAT) / 250 us (for Net) Various settings possible
- Small package: 32pin VQFN (5.0mm x 5.0mm)
An evaluation board equipped with this product and an EtherCAT® reference board are available. Please use all means.
DP83822 series list
DP83822I *Supported temperature range: -40 to 85°C
DP83822H *Supported temperature range: -40 to 125°C
DP83822 EVMs
EtherCAT® Reference Board with DP83822
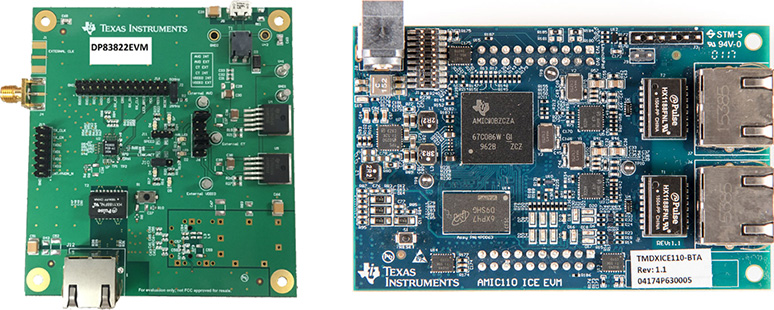
Supports industrial protocols! Texas Instruments product Sitara series
By introducing a protocol stack to the internal "PRU-ICSS" of TI's Sitara processor family, it is possible to incorporate functions according to industrial networks (EtherCAT, EthernetIP, Profinet, etc.), so it is possible to use various industrial networks by replacing software. Compatible with slave devices. Doing so eliminates the need for external dedicated ASICs and FPGAs, leading to a reduction in the number of components. It also reduces development costs by optimizing system costs and supporting multiple protocols on the same platform.
Sitara製品ラインナップ
series name | AM24x | AM64x | AM57x | AM437x | AM335x |
Features | Gigabit industrial communication ready Microcomputer |
Gigabit industrial communication ready processor |
High performance multi-core processor |
Video input support processor |
most versatile processor |
industrial communication (EtherCAT, EthernetIP, Profinet, etc.) |
2つのプロトコルを同時処理 |
Handles one protocol | |||
Processing | Cortex®-R5F@0.8GHz x4 (Max5120DMIPS) |
Cortex®-A53@1GHz x2 (Max6000DMIPS) Cortex®-R5F@0.8GHz x4 (Max5120DMIPS) |
Cortex®-A15@1.5GHzx2 (Max10500DMIPS) DSP(C66x@750MHz)x2 |
Cortex®-A9@1GHz (Max2500DMIPS) |
Cortex®-A8@1GHz (Max2000DMIPS) |
Graphics |
- |
- |
2xSGX5443D, GC3202D, IVAHDVideoAccelerator |
SGX530 | |
memory | DDR4/LPDDR4 | DDR3(L) | LPDDR2/DDR3(L) | LPDDR1/DDR2/DDR3(L) | |
Peripheral | USB3.0 10/100/1000EMACx2 OSPI, PCIe |
USB3.0 ディスプレイサブシステム (HDMI,3系統LCD出力) Video入出力 10/100/1000EMACx2 QSPI, SATA, PCIe |
USB2.0 ディスプレイサブシステム Video入力 10/100/1000EMACx2 QSPI |
USB2.0 LCDコントローラー 10/100/1000EMACx2 |
|
PMIC | LP87334D | TPS65220 | TPS659037 TPS65916 LP8732+LP8733 |
TPS65218 | TPS65910A/A3 TPS65217 TPS650250 TPS65218 |
An evaluation environment that allows you to immediately try an industrial network
By using the evaluation board provided by TI, it is possible to immediately evaluate the industrial network.
A development platform specifically designed for industrial communication systems within the Sitara AM64x Arm® Cortex®-A53 processor family.
At the end
I have introduced an overview of EtherCAT®. How was it? The presence of EtherCAT® is increasing as the development of industrial networks accelerates. Please use it as a reference for your development. For more information about factory automation, please visit the following pages.
factory automation
http://www.tij.co.jp/ja-jp/applications/industrial/factory-automation/overview.html
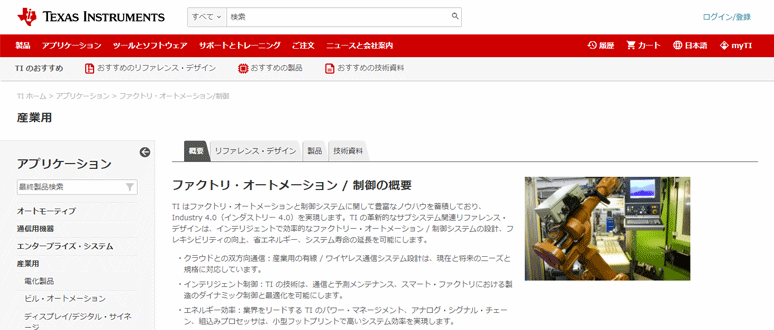
Listed application
Automated Equipment / Field Actuator / Field Transmitter / Programmable Logic Controller (PLC) / Human Machine Interface (HMI) / Industrial Robot / Logistics Robot / Machine Vision
Contact Us
For more information on the Ethernet PHY DP83822 featured in this article, or any other TI product for industrial networking, please contact us.
Related information
Click here for recommended articles/materials
Supports multiple industrial Ethernet standards! Processor without ASIC or FPGA
Click here to purchase products
DP83822 EVMs
*The following items can be purchased individually, but the number of full reels is different, so they have different model numbers.
There is no difference in product specifications.
DP83822IRHBR temperature range: -40 to 85°C (order in multiples of 3000 to purchase all reels)
DP83822IRHBT supported temperature range: -40 to 85°C (order in multiples of 250 to purchase all reels)
DP83822HRHBR Temperature Range: -40 to 125°C (order in multiples of 3000 to purchase all reels)
DP83822HRHBT supported temperature range: -40 to 125°C (order in multiples of 250 to purchase all reels)