Electronics products contain printed circuit boards of varying sizes, but do you know how they are manufactured?
Have you ever requested work from an electronic circuit assembly factory?
There are a lot of unfamiliar words when it comes to board mounting, right?
Here, we will draw a circuit diagram and make a board for the first time! Implement! Beginners such as People who vaguely knew something, but suddenly got asked a detailed question by a customer or senior colleague, and found themselves thinking, "Wow!" People who are thinking of ways to lower implementation costs even just a little.
I would like to explain the implementation process with photos for those people. If you are interested in Macnica 's manufacturing examples (development planning and manufacturing services centered on semiconductors), please refer to the following articles.
What kind of place is the implementation factory in the first place?
electronic circuit manufacturingboard manufacturingandComponent mountingAfter going through the processes at each factory, the electronic circuit is completed with components mounted on the green board that you see (there are blue, black, and other boards that are not green). I will come.
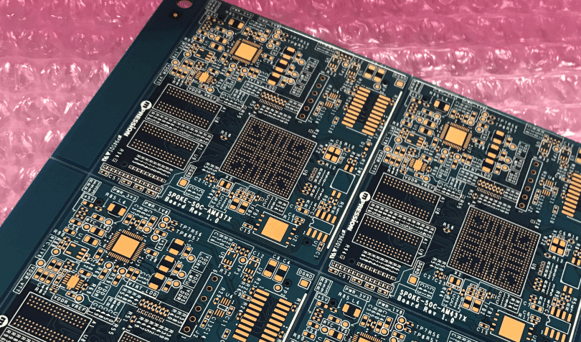
Mounting factories mass-produce electronic circuits by mounting parts such as ICs and connectors on printed circuit boards (also called raw boards, bare boards, substrates, and PCBs) that have no parts on them, as shown in this photo. It is a factory that aims to
If it is a normal process, the implementation period is about 1 week to about 10 days.
(During this period when the design team is out of their control, they often take a short break...)
Break down the component mounting process
Now, I would like to touch on the contents of the mounting factory.
The process of component mounting"Mounting surface mount components = SMT process"and"Mounting the pricked parts = DIP processcan be divided into
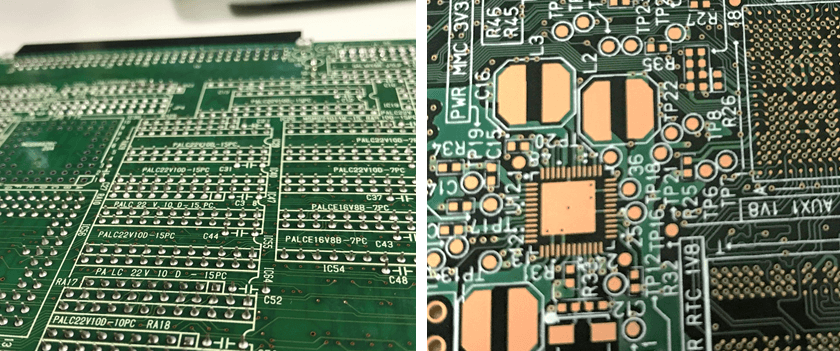
When mounting a component, if there is a hole in the board and the terminal of the component is inserted (left photo), it goes through the DIP process, otherwise (right photo) it goes through the SMT process. I haven't really seen DIP parts these days.
As a combination of processes,
・『SMT process only』
・"DIP process only"
・『SMT process + DIP process』
There is such a pattern.
SMT process (1) Solder material that can be applied Cream solder
The first step in the SMT process for surface mount components is to apply a paste-like solder material called cream solder to the lands of the printed circuit board in preparation for mounting the printed circuit board on an automatic mounting machine.
In electronic work, parts are mounted by melting thread-like solder material with a soldering iron, but cream solder, as its name suggests, is a solder material that is creamy even at room temperature.
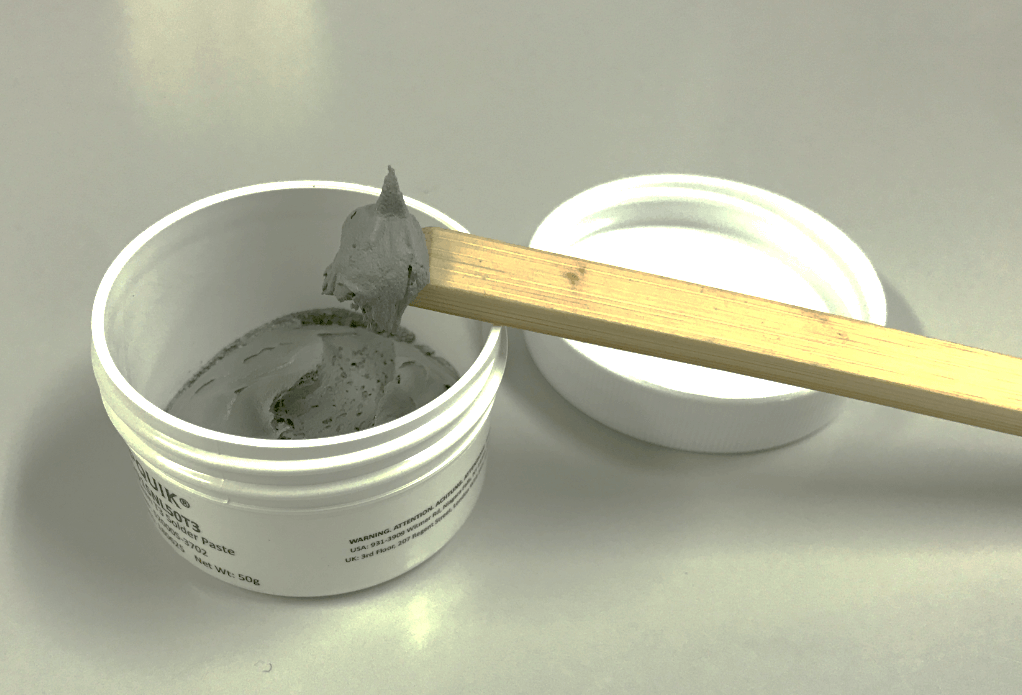
Soldering at room temperaturemelted stateInstead, it is also known as solder paste, which is a mixture of "very fine solder particles" and "flux". Sounds like the name of a special move. Then, a device that applies the cream solder to the printed circuit boardcream solder printing machinecalled.
SMT process (2) Metal mask that determines mounting quality
There is another important point in the process called cream solder printing. This means that you need a metal plate called a metal mask with holes at the same positions as the lands (where you want to solder) on the printed circuit board, as shown in this photo.
When you ask a mounting factory to do the work, it always comes out in the quotation.
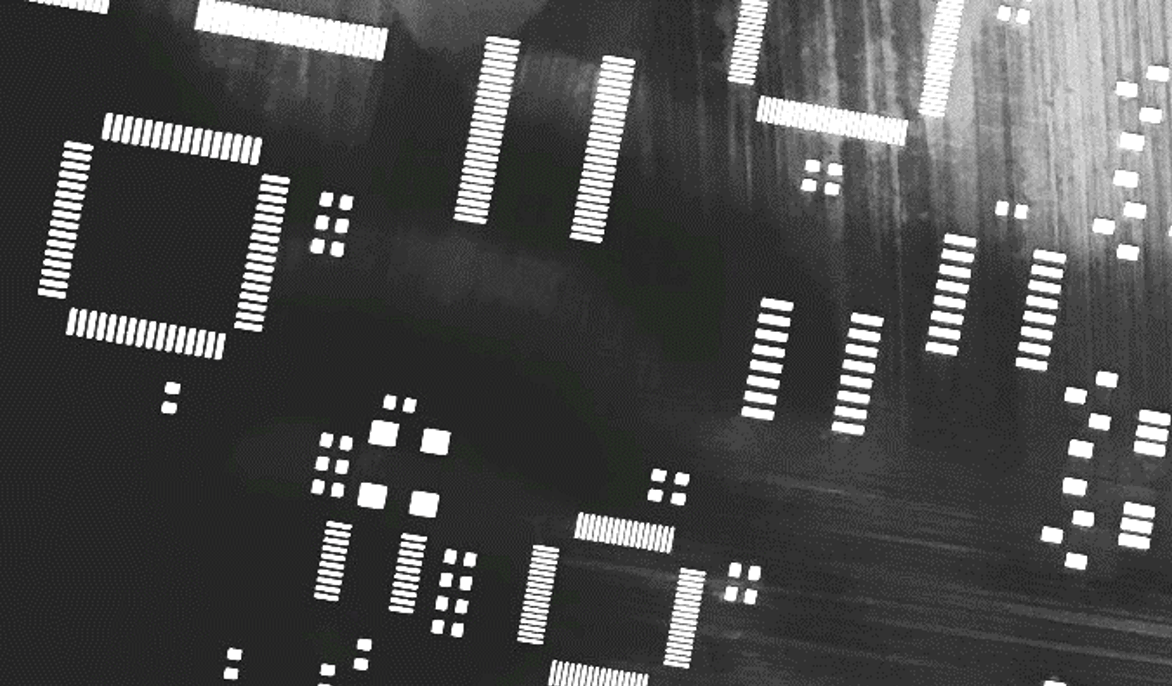
In fact, this metal mask is made quite elaborately, and it is a mass of know-how in mounting quality.
If this is not ideal,
・Nearby pins short circuit
・ void (Bubbles in the mounting part) are formed, resulting in poor contact between the component and the board.
・ Self-alignment does not work due to too much solder solder ball may remain on the substrate as
For semiconductor parts in ultra-small packages, the guidelines include ultra-fine processing instructions in units of tens of microns, such as mask thickness, opening dimensions and shapes, and the addition of slits. The guidelines written in English are Stencil I think it is introduced as
The flow will look something like this.
① Set the printed circuit board in the printing machine
② Cover with a metal mask
(3) Press cream solder from above with a squeegee
④ Remove the metal mask
(5) The board land is coated with cream solder.
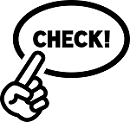
(1) Whether it is a prototype or a mass production, it is necessary to create a metal mask when passing through an automatic mounting machine.
(2) Since it is necessary to make a metal mask for each mounting surface of the printed circuit board, when mounting components on both sides of the printed circuit board, two types of metal masks are required, which doubles the cost.
SMT process (3) Mounting (placing) parts
An automatic mounting machine called achip mounter is used to mount hundreds of components on a printed circuit board coated with cream solder.
The chip mounter needs to prepare a program consisting of "image recognition data", "component dimension data", and "board layout data" in advance, and set the components to be mounted on the printed circuit board in a device called a feeder when mounting. Therefore, the more parts there are, the more man-hours for setup.
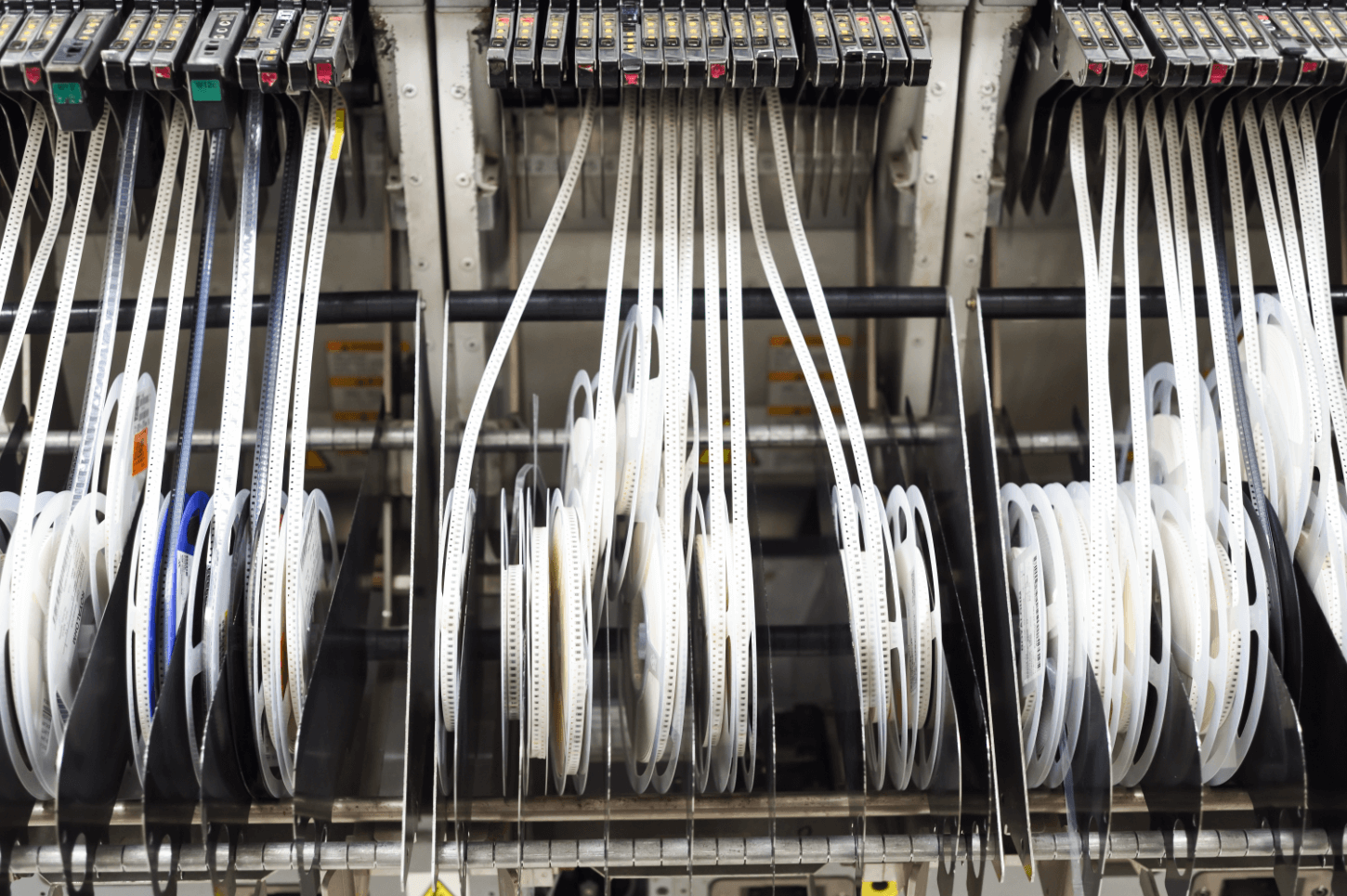
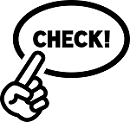
(1) As shown in this photo, the automatic mounting machine is designed so that the rolls packed in a tape shape are pulled into the mounting machine, so even if the required number of tape-cut parts is supplied to the mounting factory, it will not be fed to the feeder. may not be set. In that case, there are cases where additional costs such as "rewinding" and extra man-hours may occur, so in the case of parts supply, I would like to give it to you in a state where you can afford it.
(2) In order to pass through the mounting machine, it takes several hours to set the parts on the feeder with human hands. The number of components to be mounted is important, but reducing the types of components to be mounted also has a large impact on cost.
SMT process ④ Melt the solder in a reflow furnace
The printed circuit board on which the components have been mounted by the chip mounter has not yet been soldered, so it is not fixed to the circuit board.
Shaking or swinging the board will cause the parts to fly away.
Therefore, a device that melts cream solder and firmly attaches parts to the board appears. That's the reflow oven. Note that the word “flow”, which will be introduced later, is similar, but it refers to a different process.
In the reflow furnace, the inside of the equipment is temperature controlled, and when the board with the parts passes through, the cream solder melts and is completely fixed to the printed board. Each company has the know-how to improve the mounting quality of this temperature control, and of course the parts are not damaged by heat, but the temperature profile allows the melting of the solder and the activation of the flux to work at maximum efficiency to maintain the mounting quality. The temperature inside the device is controlled so that
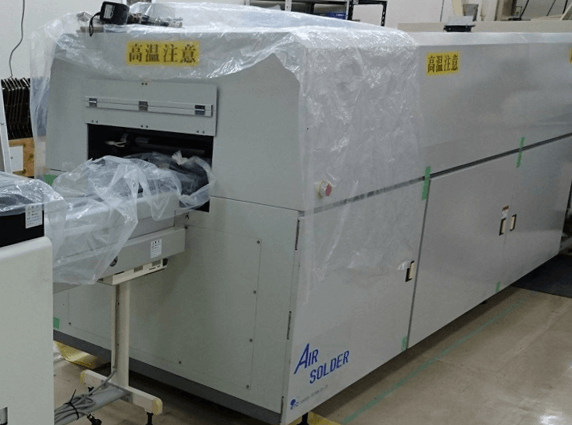
The reflow furnace is like this, functionally it can be called a big oven toaster, the furnace has a length of several meters.
(By the way, the photo is borrowed from the opening ceremony of the reflow furnace.)
I've seen people mounting semiconductors in a toaster oven, and I think it's the same reasoning.
SMT process bonus 1 When reflowing the front and back of the board
In the case of a printed circuit board with SMT components on both sides, the second SMT process is performed with the board turned over after reflow.
Skipping the second SMT step means that two solder prints are required.
But the second solder print is different than the first, do you know why?
The reason for this is that when the first reflow is completed and many parts are already attached to the second solder printing, it is not possible to lay the board horizontally when the first mounted surface faces downward.
At that time, in order to print cream solder on the side where no parts are placed, a jig such as a "printing tray" with a counterbore according to the shape of the mounted parts is required as shown in the photo below. increase. This may not be seen so often by electronic circuit designers.
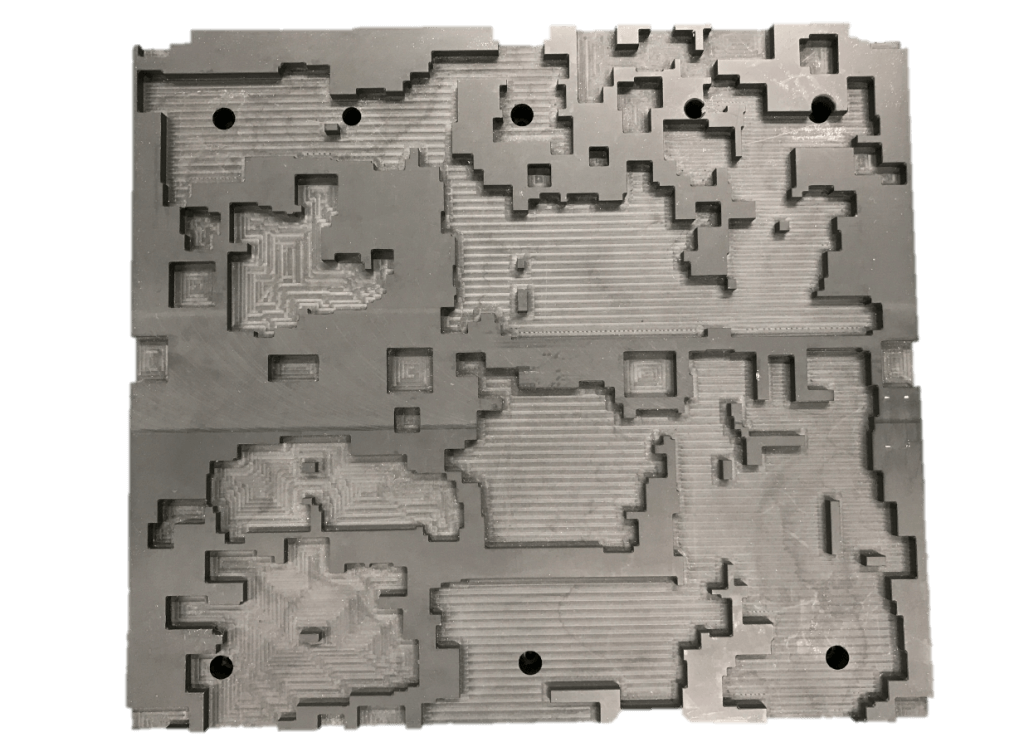
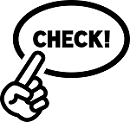
Therefore, double-sided reflow mounting boards may add costs due to additional equipment.
Depending on the prototype and mounting conditions, such equipment may not be necessary, and there are cases where jigs that can be aligned can be used, so please consult with the mounting factory.
SMT process bonus 2 Which is the front and which is the back?
Slightly digressing from the topic, when reflow-mounting the front and back of the board, we tend to think that we mount the front side first and then the back side, but in reality, we often start from the back side.
Persons in charge of HW design and artwork design have a strong tendency to place large parts, large SoCs, FPGAs, etc. that supplement the main functions of products on the surface unless there are restrictions on the housing situation, right? It makes sense when you think about debugging. (Or, we tend to call the side on which these main parts are placed the "surface", "component side", or "A side")
What do you think would happen if we mounted these heavy parts first and then performed a second reflow? The answer is that when the solder melts again in the reflow oven, the weight of the part causes the part to fall in the reflow oven. For this reason, we have incorporated the idea of reflowing the surface on which heavy parts are mounted in the second reflow process.
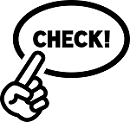
It is possible to fix the board and the part by applying a bond so that the part does not fall off even if the solder melts. I'm devising the order of component mounting.
SMT process (5) Visual inspection of the mounted state
After the SMT process, it is necessary to check whether the components are securely mounted.
I think that it can be confirmed to some extent by visual inspection, but in terms of accuracy, speed and quantity, we will use a visual inspection device called AOI (Auto Optical Inspection).
It seems that there are several methods of appearance inspection equipment, but some factories use the latest equipment that supports 3D and inspect the mounting state with tremendous speed and accuracy. In fact, I once asked about the percentage of errors that occurred in the inspection, and it was said that there were no errors, but on the contrary, the accuracy was too good and misjudgment (the state where errors actually occurred) It seems that there are many cases where the inspector confirms that there is no problem), and they said that they still need improvement.
If there is really a problem with the mounting quality, a process such as rework and other measures will be entered by human hands. Also, the inspection process using AOI introduced here is the work to check the state after SMT mounting, but the appearance inspection itself is included in each process.
For example, there are factories that use an optical inspection device called SPI (Solder Paste Inspection) to check the quality of solder printing to make sure that the solder paste is properly pasted even after solder paste printing. If you can check the manufacturing quality so much, you can leave the mass production to us with peace of mind.
DIP process Estimates change greatly depending on how to attach parts
After the SMT process, the next step is the DIP process for piercing parts.
As explained earlier, the DIP process is the process of mounting components other than the actual product on the surface.
Other than surface mount products = DIP components, insert components, lead components, axial components, radial components, etc. There are several names, but basically they are recognized as components that need to be mounted through the board. I think it's fine.
I don't see DIP IC products very often these days, but many of them are DIP products because connectors need mounting strength to withstand insertion and removal.
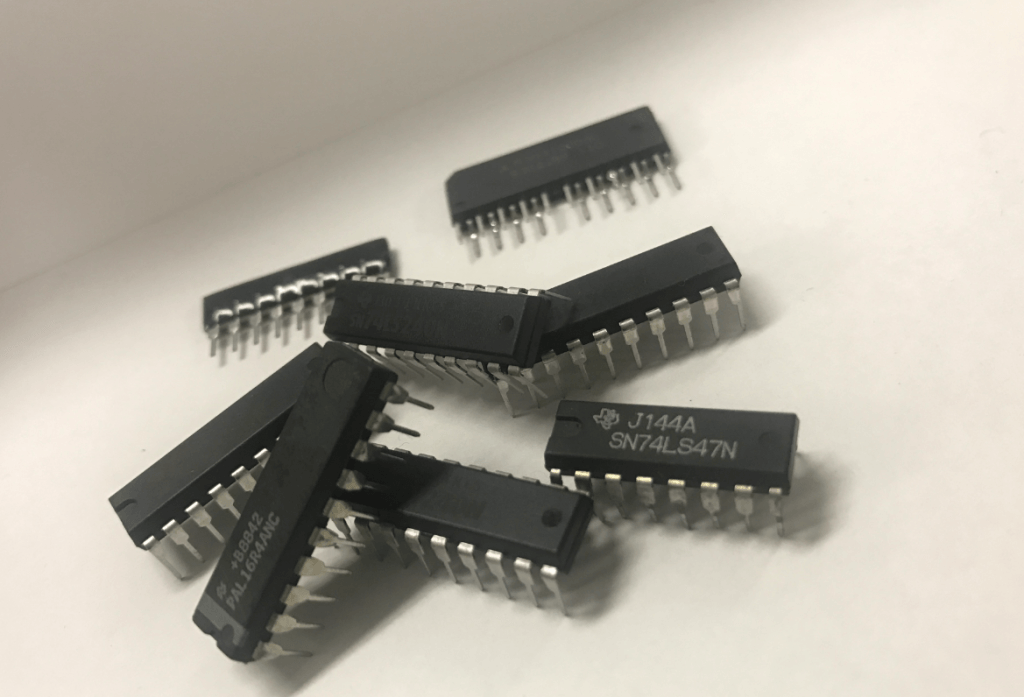
(Nostalgic DIP items that were hard to find)
We will now discuss three implementation methods.
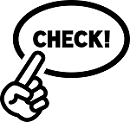
This process is not necessary for boards with only SMT components that do not use DIP products at all.
Based on my experience, there are relatively many manual interventions in the process, so if you consider the production speed and quality, the fewer the parts that need to be pierced, the more stable the production can be expected.
DIP process ① Flow mounting
Flow mounting is a method of mounting components using a device called a flow tank.
Since the names are similar, it is often googled as "flow reflow difference", but the work content is different implementation method.
Reflow ⇒ Method for soldering surface mount components
Flow ⇒ Method of soldering piercing parts
Melted solder accumulates in the flow tank like a pool, and the DIP parts are soldered by attaching the back side of the board to it. The photo below shows a resin plate called a DIP pallet, DIP carrier, or flow pallet used for flow mounting.
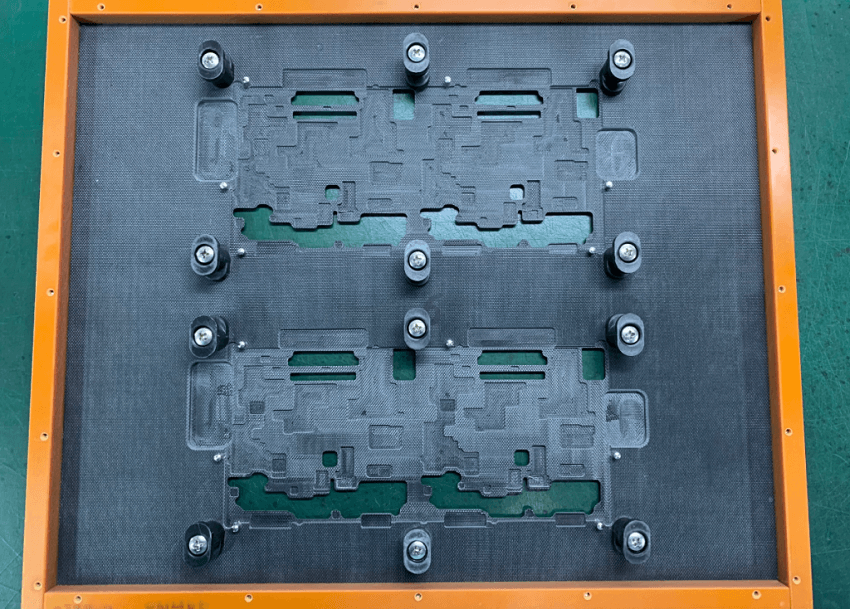
This is an example of a pallet on which 4 boards can be placed. It is profitable to be able to mount 4 cards at once.
Since the pallet is made to cover the parts other than the DIP mounting part like this, there is no danger of solder adhering to other parts. There are also cases to consider and use the following point implementation.
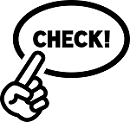
When mass-producing boards with flow mounting, it is necessary to prepare nearly 10 DIP pallets to increase the continuity of production. The initial cost will be in the hundreds of thousands of dollars. Productivity per hour is high, so more electronic circuits can be produced. If you want to use flow mounting, the most important thing is the distance between the surrounding components.
DIP process (2) Mounting by point soldering
It is a mounting method called point soldering, Takurobo, and local soldering.
Flow mounting is also a device used for mounting DIP products, but the difference from flow mounting with a jabot is that a thin metal tube into which solder flows protrudes from the bottom and can be moved by teaching in flow mounting. It enables local implementation that is difficult to deal with.
In point mounting, soldering is done one point at a time by this teaching operation, so it is not suitable for mass mounting manufacturing.
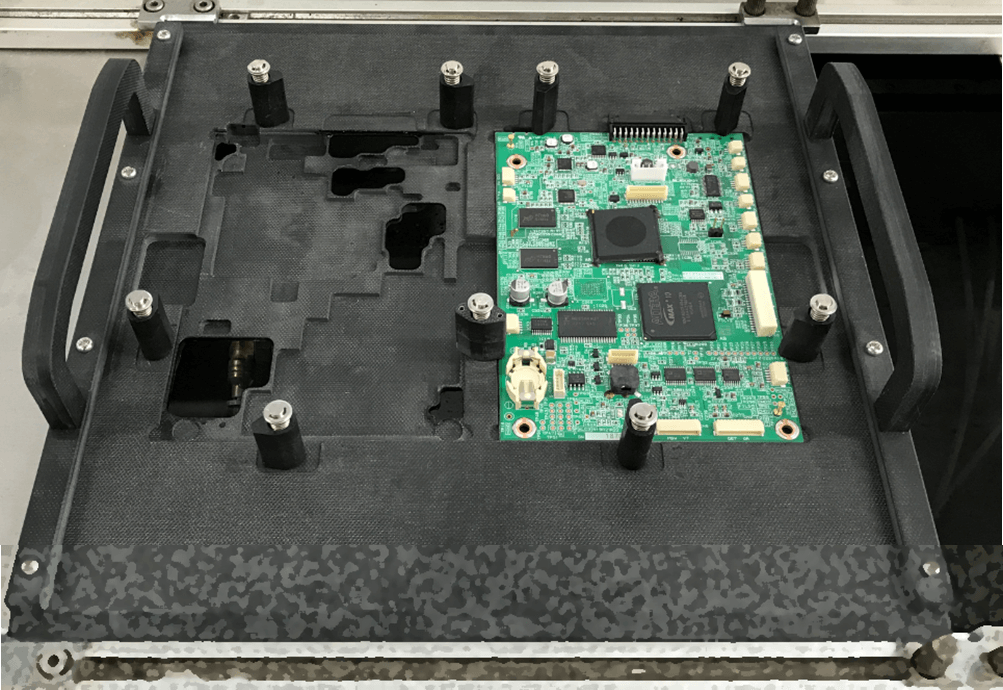
On the back of this black pallet, there is something like a nozzle that jets solder, aiming at the DIP part from the back of the board.
*The reason why the parts are slightly raised is that the temperature profile was analyzed in the reflow process.
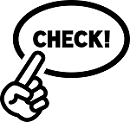
As with flow mounting, there are cases where a dedicated pallet is required, but the jig pallet is for the fluxer, and the mounting pallet is only a small number, so point solder mounting is better for the initial investment.
DIP process ③ Mounting method by manual mounting
If flow mounting or point mounting is unmanageable, or for manufacturing that does not require mechanical mounting in the first place, the parts may be attached by craftsmen. Many factories have certified professionals to handle such manual work. Since it is done manually, no initial cost is required, and the number of man-hours for mounting is simply calculated.
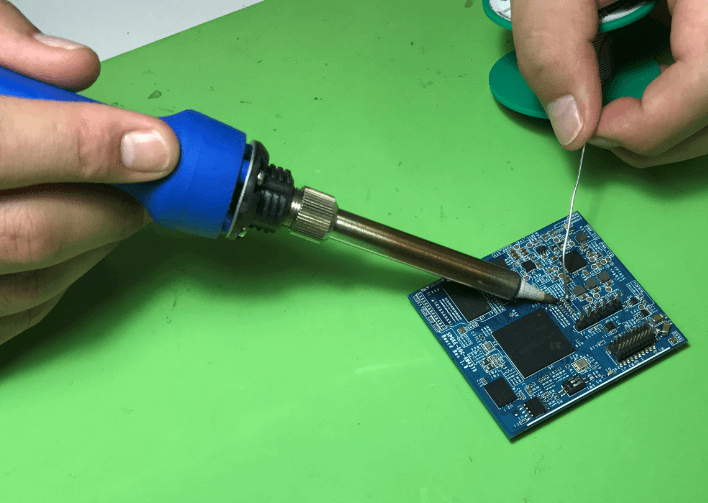
Summary
As an extension of our customer development project support, we are sometimes asked to manufacture prototypes and mass-produce products. There was a time when I wondered, "Why does it change so much when it's just soldering?"
With so many options for mounting methods and equipment input, it makes sense that estimates and processes would change depending on the mounting factory. I think it's a little subjective, but I think it's like this.
process |
surface mount |
DIP product mounting |
||
---|---|---|---|---|
Implementation method | Reflow | flow | point implementation | hand mounting |
Initial jig equipment | Metal mask (possibly a print tray) |
DIP carrier (Unnecessary if there are no parts on the back) |
No pallets or jigs | unnecessary |
jig cost | During ~ | high | low | Nothing |
Productivity | ◎ | 〇 | △ | ☓ |
Even for startups who are manufacturing electronic circuits for the first time for mass production, if they understand the mounting flow and initial equipment, they will not affect the product concept. Don't put the front and back randomly!"
Well, this time, I briefly introduced the mounting process and equipment until the electronic circuit is completed in "The flow of printed circuit board mounting that even people with no electronics experience can understand." How was it?
Depending on the factory, there may be differences from the introduced content, such as "this work or equipment is not available", "the order of work is different", or "additional XX is being done". I think that such places are also packed with the know-how of each factory.
Do you have any problems with manufacturing?
As I wrote at the beginning, in addition to semiconductor procurement and technical support, we also provide development planning and manufacturing services centered on the semiconductors we handle.We specialize in small-lot, high-mix production and medium-scale production, such as hundreds of units. Please let us know.
Manufacturing consulting service
Manufacturing consulting service Please refer to the button below for details.