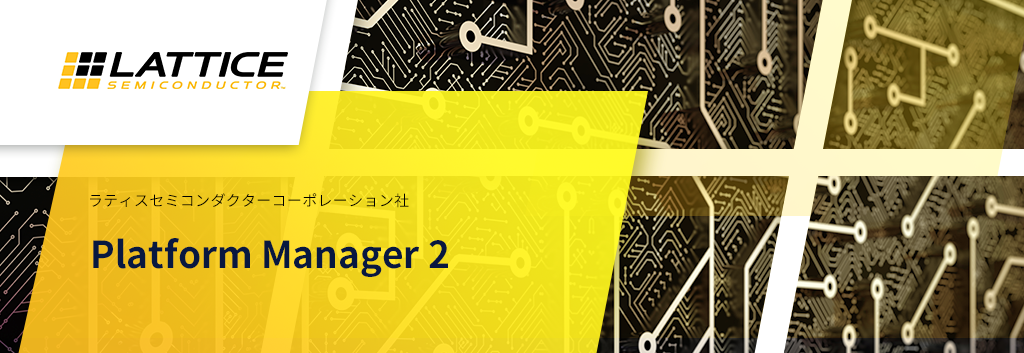
Product Summary
Platform Manager 2 is a power management device capable of integrated monitoring and control of voltage/current/temperature. In addition to the power sequencing/voltage monitoring available with Power Manager II [Pac-Power], current/temperature monitoring is possible. Another major feature is the ability to leave a Fault Log, and by setting triggers in advance, it is possible to detect power supply anomalies and their signs, and record various monitoring signals to the built-in EEPROM.
Installed hardware and functions
PLD
It has 1280LUT SRAM area (and built-in ROM for configuration), and arbitrary sequence can be created programmably with GUI on the development tool. In addition, it has GPIO, and arbitrary signals can be incorporated into the sequence. The remaining SRAM area and GPIO can be used to incorporate user logic created in Verilog/VHDL, just like other FPGAs. (The power supply control unit is designed with a GUI on the sub-development tool Platform Designer, and integrated with the user logic on the design development tool Diamond.)
Voltage Monitor Input
10ch analog voltage input is possible. A comparator for voltage monitoring is connected to each input port. By incorporating the comparator output into the sequence, it is possible to create a sequence based on the actual voltage and monitor voltage abnormalities during system operation. It can monitor from 0V to 5.75V, the comparator can be set up to 368 trip points, and the monitoring can be set with a high resolution of 15-20mV.
In addition, it has two comparators per channel and can monitor in a window. In addition, it is possible to monitor voltages outside the specified range (including negative voltages) by installing an external circuit, and reference documents are posted on the Lattice website.
Fault Log
By setting an arbitrary monitoring signal as a trigger, it is possible to detect system abnormalities/symptoms and record the comparator output values of various monitoring signals in the built-in EEPROM. By reading the record via the I2C interface, it is useful for various analyzes such as failure. It also supports recording to any external SPI Flash, allowing you to increase the number of recordings.
Current Monitor Input
2ch current monitoring is possible. Both ends of the several milliΩ sense resistor in the power supply circuit are connected to Platform Manager 2, but since the device has a built-in amplifier circuit, it does not require an amplifier circuit on the board, enabling space-saving current monitoring. is.
Temperature Monitor Input
2ch temperature monitoring is possible. It is a form to connect the Thermal Diode on the board to the Port of Platform Manager 2.
Fan control
If a cooling fan is installed in the system, by inputting the PWM signal output from Platform Manager 2 to the fan driver, etc., it is possible to easily control fan rotation according to system power consumption and board temperature. is. On the sub-development tool Platform Designer, you can set the frequency/duty of the PWM signal for fan rotation only by GUI operation. In addition, Duty can have 3 types of settings, and it is possible to switch settings with any signal, including the Current/Temperature Monitor signal mentioned above.
Open Drain Output
Apart from GPIO, it has 10ch 5V tolerant Open Drain output ports. Sequence control is possible by inputting to the Enable Port of the DC/DC converter. In addition, it has 4ch 12V tolerant Open Drain output port and MOSFET drive is also possible.
ADC
Equipped with 10bit ADC, each input value of voltage/current/temperature can be read externally via I2C interface.
TRIM Control
It has 4ch trim output. By connecting to a DC/DC converter with a trim port, it is possible to stabilize the output voltage with an accuracy of ±1% or less. In Platform Manager 2, monitoring voltage is read by ADC and then fed back, so you can expect stable output under temperature and over time while using inexpensive DC/DC. In addition, since 4 sets of output values can be held per channel, it can also be used for upper and lower limit inspections in shipping inspections.
Example of product use
The figure below is just an example, so please feel free to contact us from the inquiry button at the bottom of this page regarding the feasibility.
An example of system configuration. In addition to power sequence, Fault Log and Fan Control are possible.
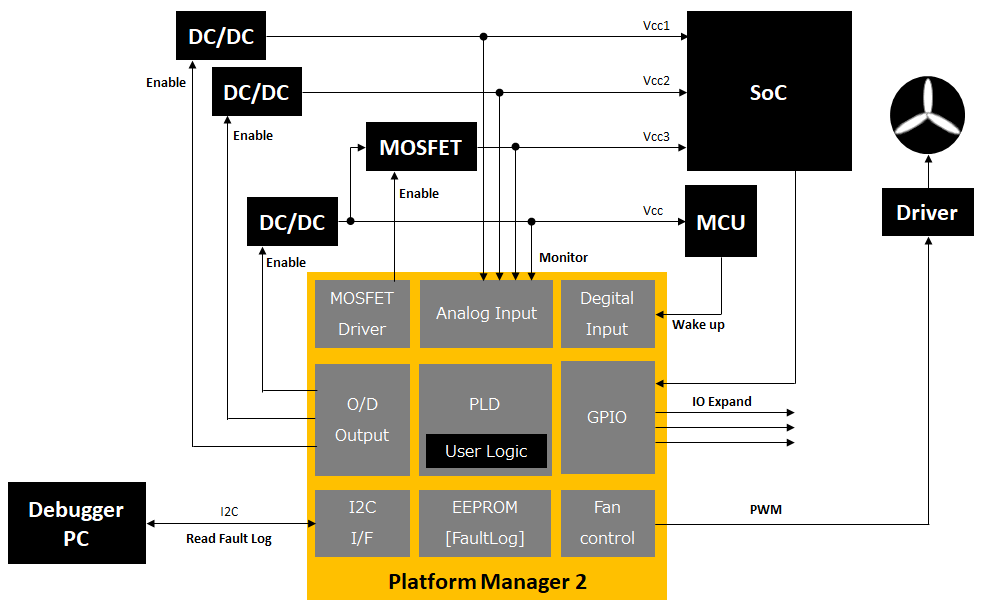
Product lineup
Hardware Management Controller |
|
parameter |
LPTM21 |
Voltage Monitoring Inputs |
10 |
Current Monitioring Inputs |
2 |
Temperature Monitioring Inputs |
2 |
Number of Trimming Channels |
4 |
MOSFET Drives |
4 |
On-Chip Non-Volatile Fault Log |
✔ |
Number of LUTs |
1280 |
Distributed RAM (kbits) |
10 |
EBR SRAM (kbits) |
64 |
Number of EBR Blocks (9 kbits) |
7 |
User Flash Memory (kbits) |
64 |
Number of PLLs |
1 |
Communication interface |
I2C /SPI/JTAG |
Programming Interface |
I2C/SPI/JTAG |
Operation voltage |
2.8V to 12V |
237-Ball ftBGA (1mm) (17x17) |
106 (Number of Digital Inputs) |
EBR stands for Embedded Block RAM
Evaluation Board
For more information about the evaluation board and those who are considering purchasing it, please contact us using the purchase button below.
Inquiry / Quotation
If you have any questions or requests for quotations regarding this product, please contact us using the form below.