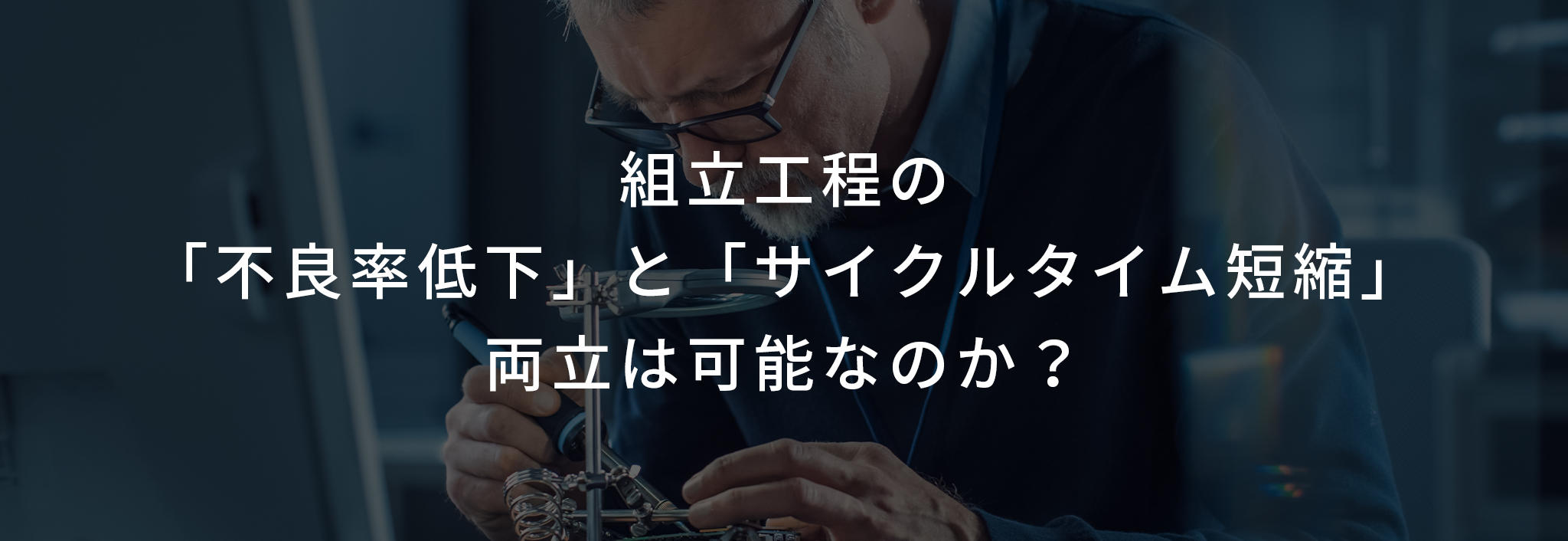
車載電装システム市場の好調をみなさん肌で感じているのではないでしょうか。
自動運転技術の向上、シェアリングエコノミーの加速と世の中は変化しつつありますが、それでもあと10年は車載電装システムの需要は伸び続けるともいわれています。
しかし、一方で不安要素があることを否定できません。
伸び続ける需要に耐え切れない国内製造業
不安要素として、需要の伸びに対応するための「人材不足」と「安定供給」という大きな課題を解決する必要があるのですが、国内の多くの企業が伸び続ける需要に対応する準備ができていません。
課題解決として、億単位の投資による自動化など「ロボット」の導入が進んでいる企業もありますが、日本の製造業は約99%が中小企業です。
もうひとつ会社を立ち上げるほどの大きな投資が必要なロボット推進を、10年以内に日本を支える中小企業が踏み切ることができるかといえば、非現実的でしょう。
残念ながら、現段階ですべての製造業を救う方法はありません。
しかし、「組立工程」のみにフォーカスするなら、一筋の光が見えています。
海外の製造業にヒントがあった!
ここ数年、車載部品に関わらず海外製品のクオリティが上がってきているのに気づいていますか?
従来は、海外工場で働く人員の多様性や理解度のバラつきによって「安かろう悪かろう」が一般常識でした。
しかし、いまではそうした「多様性」をAIによって平準化し、組立工程での不良率の低下を実現しています。
この仕組みを日本に導入した場合、どうなるでしょうか?
まじめな国民性×AIの効果は絶大
どれだけまじめに仕事をする国民性といっても、ポカミスをすべて防ぐことは難しいです。
組立工程においても、作業員の熟練度によってタクトタイムが変わるため、どこにボトルネックがあるのかを判断することも難しく、「不良率低下」や「サイクルタイムの改善」は困難ですよね。
しかし、AIを実装することにより「人材不足」も「サイクルタイムの改善」を両立できる可能性があるんです!
具体的には、見ていただいたほうがイメージできるでしょう。
ご覧いただくとわかるように、AIによって組立工程の作業ミスを検出しています。
指導員や検査員が常駐する必要がなく、「いまある人材」にAIを掛け合わせるだけで圧倒的に組立工程が最適化されているのがわかるかと思います。
このAI実装に必要なのは、作業に関する『AIモデルの学習』と『撮影カメラ』なので、自動化ロボットの導入よりも少ない投資で実現可能なのもわかるかと思います。
サイクルタイムが変われば「人材不足」にも光明が!
デモ動画のような組立工程において、AI実装を行えばサイクルタイムを短縮・改善することが可能です。
最初は組立工程のミスを防ぐことがミッションになりますが、データを蓄積していくなかで「どこでミスが起こりやすいのか」ボトルネックが分かるようにあります。
そうした改善を続けていくことによって、熟練度別に適切な人員配置も行うことができ、作業によっては国外のスタッフを積極的に採用することもできるようになります。
従来の言語による指導ではなく、AIが記録した適切な作業映像を教育に使うこともできますし、作業エラーについてもAIが指導員になってくれるわけです。
仕組みによって両立は十分に可能!
伸び続ける需要に対応するためには、商品の『安定供給』と『人材の確保』が必要になりますが、従来の紙ベースのチェックシートや、熟練者頼りのサイクルタイムでは限界があります。
AIを実装した組立工程の改善は、そうした3年後、5年後、そして10年後の変化に対応するための大きな武器になるのは間違いありません。
AI実装はロボット導入よりも少ない投資で、いまある人材をフルに活用して、不良率の低いものづくりを安定して実現できる現実的な手段と言えます。
より詳しく学びたいあなたへ!無料講演動画
こうしたサイクルタイムへの取り組みは、国内でも注目を集めています。
マクニカでは、「組み立て工程のQCD改善にむけたアプローチ」と題して、ウェビナーを開催しました。
下記の記事では、開催当日のグラレコと講演動画を無料でご覧いただけます。
より詳しい事例などを知りたい!という方はぜひチェックしてみてください。
\ 現場の本気質問に関するQ&Aにも注目 /