はじめに
著者・山下様よりご挨拶
|
初めまして、この度、コラムを書かせていただくことになったシーメンス EDA ジャパンの山下です。どうぞよろしくお願いいたします。 |
掲載内容のご紹介
熱問題はまだまだ他人事と思っていませんか?しかし、実は熱が原因で生じている問題も多いのではないでしょうか?デバイスの高性能化・基板の高密度化・機器の小型化により、熱の問題は設計者にも無視はできないものとなってきています。
今こそ知っておきたい、熱問題。熱伝達のメカニズムから解析・解決方法まで、熱問題の基本を紹介いたします。
1.熱解析はトレンドの卵
「熱解析に興味がある」、最近このような電気設計者が増えています。高性能なデバイスを使用することにより消費電力は増え、機器の小型により基板は高密度化し、同じく機器の小型化により熱を逃がすためのスペースはより小さくなる一方で、熱を逃がすための部品はコストダウンを達成するために、できるだけ使いたくないという状況があるのではないでしょうか?そのため、設計者は問題を未然に防ぐための手段として、「熱解析」というキーワードに興味を持ち始めているようです。
熱に対する問題は、ここ数年の間に突然浮上してきたものではありません。熱を解析するためのシミュレータの歴史も、20 年以上あります。超高性能なデバイスを複数使用した場合や特殊な条件下で使用する場合など、以前は解析ツールの使用範囲が限られていたかも知ませんが、最近はコンシューマー製品などでもその対象となることが多くなりました。もし、熱対策で失敗をしてしまうと、大きな損失につながる可能性がありますが、その例として有名なのが、2007 年に発生したゲーム機の不具合ではないでしょうか。
熱解析ツールは、これから発展していく分野だと私は予想していますが、現在の状況は、シグナル・インテグリティーが一部の解析専門職の担当者から、各電気設計者に広がっていった、その初めの段階と似ているように思います。熱の問題が増えれば、熱解析専任者だけで全てをフォローすることは難しくなり、各電気設計者がその役割を担わなければならなくなるでしょう。そうなる前に、最低限の準備はしておきたいものですが、電気設計者の熱解析ツールに関する認知度はまだ低いように思われます。
今まで一言で熱解析と言って参りましたが、熱解析ツールはいくつかの種類に分けることができ、解析したい対象によって、使用する解析ツールも異なります。例えば、パッケージ単体、基板、それらを含んだ筐体の内部など、解析対象によって使用するツールも異なれば、使用する担当者も異なります。基板は、電気担当者、筐体については、解析の難易度のハードルが上がるので熱解析の専任者が使用する場合が多いようです。
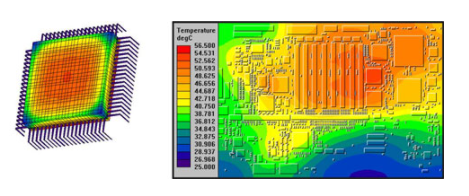
伝送線路の問題については伝送線路解析ツール、EMI の場合にはルール・チェッカーなど、その対象によって使用するツールは異なるように、熱解析でも問題になる対象によって、解析ツールを使い分けないと、個々の問題の原因究明は時間と労力がかかります。もし、電気設計者であれば、使用するのは基板用の熱解析ツールでしょう。基板用の熱解析ツールであれば、基板上で起こりうる熱の問題を事前に把握することができ、根本から解決をするための糸口にすることができます。この基板用の熱解析ツールがこれからのトレンドになるかもしれません。
2 熱の伝達のメカニズムを知っておこう
熱の問題を解決するには、熱を発生させない様にすれば一番簡単なのですが、製品のスペックを満足させるためには、ある程度の発熱は仕方ないことですし、逆に発熱の問題をクリアすることも良い製品作りには欠かせない要素だと思います。可能な限りの手段を総動員して熱の対策をしなければならなくなりますが、その際に熱がどの様な仕組みで伝わるのかを正しく理解していれば、限られた条件の下で熱の対策をする手助けになります。
熱の伝わり方は、次の3つがあります。逆に言うと3つしか無いので、それぞれの特性をうまく利用すれば、発生した熱を効果的に排出するための方法を導き出す手助けになります。
● 熱伝導 : IC からピンなどを通して、基板に直接熱が伝わること
● 熱対流 : IC の表面から空気中に対流として熱が伝わること
● 放熱 : 離れた場所にある2つのオブジェクトに温度差がある場合に、直接熱を伝えます。
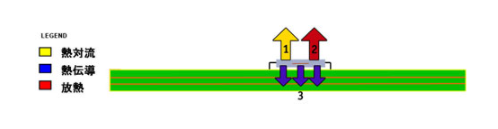
少し言い方を変えると、温かい缶コーヒーの缶を直接触ることで熱を感じますが、これが熱伝導です。
オイルヒーターで部屋が暖かくなるのは、温かいオイルヒーターに触れた空気が部屋の中で循環したからで、これは熱対流によるものです。太陽の光を直接浴びると暖かさを感じます。直接触れた訳でも、空気を通じて暖かさを感じたものでもないもの、これが放熱です。
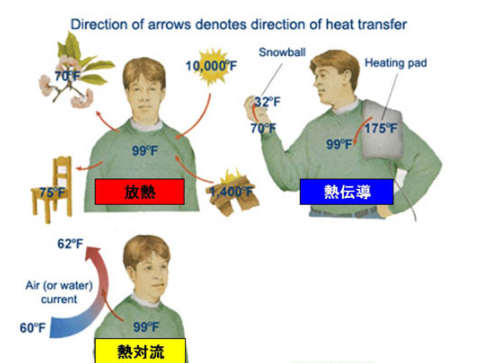
基板上では、部品の大きさも熱を外に伝える性能に影響してきます。空気と触れている面積が大きければ、それだけ熱を放出しやすくなりますので、大きな部品の方が熱を放出する上では有利です。一方で、消費電力が小さい部品であっても表面積が小さければ、意外なほど高温になる可能性があります。
また、高温になる部品を密集して配置してしまうと、熱対流による放熱の効果が薄くなりますので、部品の配置時には、細かな配慮が必要です。
熱が高くなると機器の性能や寿命に影響が出てきます。「10℃ 2倍則」 と言う法則をお聞きになったことは無いでしょうか。温度が 2 倍に上がると、部品の寿命は半減するというものです。特に、電解コンデンサーは熱に弱い部品です。故障率が上がることが無いように、しっかりとした対策が求められています。
3 What-if 解析で問題を解決
基板専用の熱解析ツールについてお話をしたいと思います。基板専用の熱解析ツールは、基板設計 CAD か解析に必要な情報を取り込むことができるので、解析にかかる労力をある程度減らすことができ、解析スピードも期待できるので、電気設計者が扱うことになった場合でも負担を最小限に抑えることができます。
シグナル・インテグリティー(SI)の解析でもそうですが、設計者が解析ツール扱う場合は、操作性と解析スピードは、必要条件となると思います。手間がかかり、解析スピードの遅いツールでは、What-if 解析は気の重い作業になり、やる気を削ぐからです。
基板用の熱解析ツールでは、基板設計 CAD からは、基板の形状と部品の配置情報・部品の大きさに関する情報を受け取ることができます。これに、各部品の消費電力の情報と、基板の置かれる環境条件を付け加えれば、解析結果を見ることが可能です。
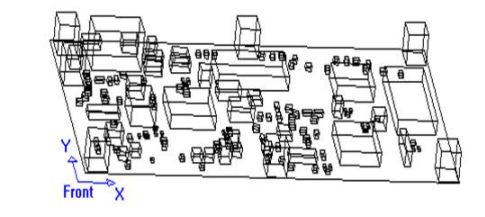
プリ解析の重要性については、改めて述べるまでもないと思いますが、What-if 解析は、プリ解析段階で行うのが効果的で、基板を作成すること無く様々なパターンを、仮想の中で試してみることができます。
例えば、解析ツール上で部品を移動してみたり、ヒートシンクを追加したり、ベタを追加したり、筐体側に取り付けるファンの性能を変更したりといったことです。これらの変更は、ツールの中だけで完結することができるので、実物を作成するよりも遙かに短い時間で確認することができ、なおかつ、お財布にも優しいという効果があります。
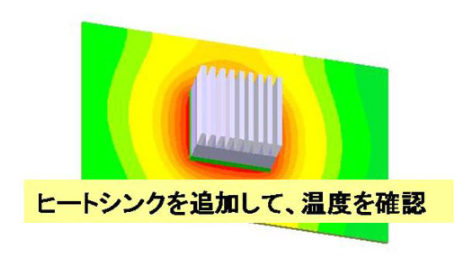
このように、What-if 解析により、実際にいろいろなパターンで基板を作成することなく、温度を予測することが可能となります。確認できるのは基板の温度だけではありません。部品単体で規格値の温度を超えていないかをチェックしたり、基板の歪みの原因となる大きな熱ストレスがないかなど、多岐にわたってチェックすることが可能です。
基板用の熱解析ツールはとても簡単に扱うことは可能ですが、熱解析は奥深くもあります。最近は、熱対策に関するセミナーなどがあちこちで開催されているようですので、今後必要になるだろうとお考えの方は、今のうちから、いろいろなところで、情報を仕入れておくことをお勧めします。
関連情報
セミナー/ワークショップ
▶ [オンラインセミナー] PCB 基板のノイズ解析セミナー 信号品質の基礎と伝送線路シミュレーション <無料>
信号が歪む基本的な原理・要因と一般的な対策方法、そして、100万円以下から購入可能な HyperLynx を使っての実デザインを使った検証例を解説いたします。SI や PI の対策が必要と感じている方はもちろん、高価な費用で SI/PI 解析を外部委託されている方もご参加をお勧めいたします。
▶ Siemens EDA 関連のイベント・セミナー
お問い合わせ
メーカー情報 Top へ
メーカー情報 Top ページへ戻りたい方は、以下をクリックください。
シーメンス(Siemens)が所有する商標や登録商標:こちら